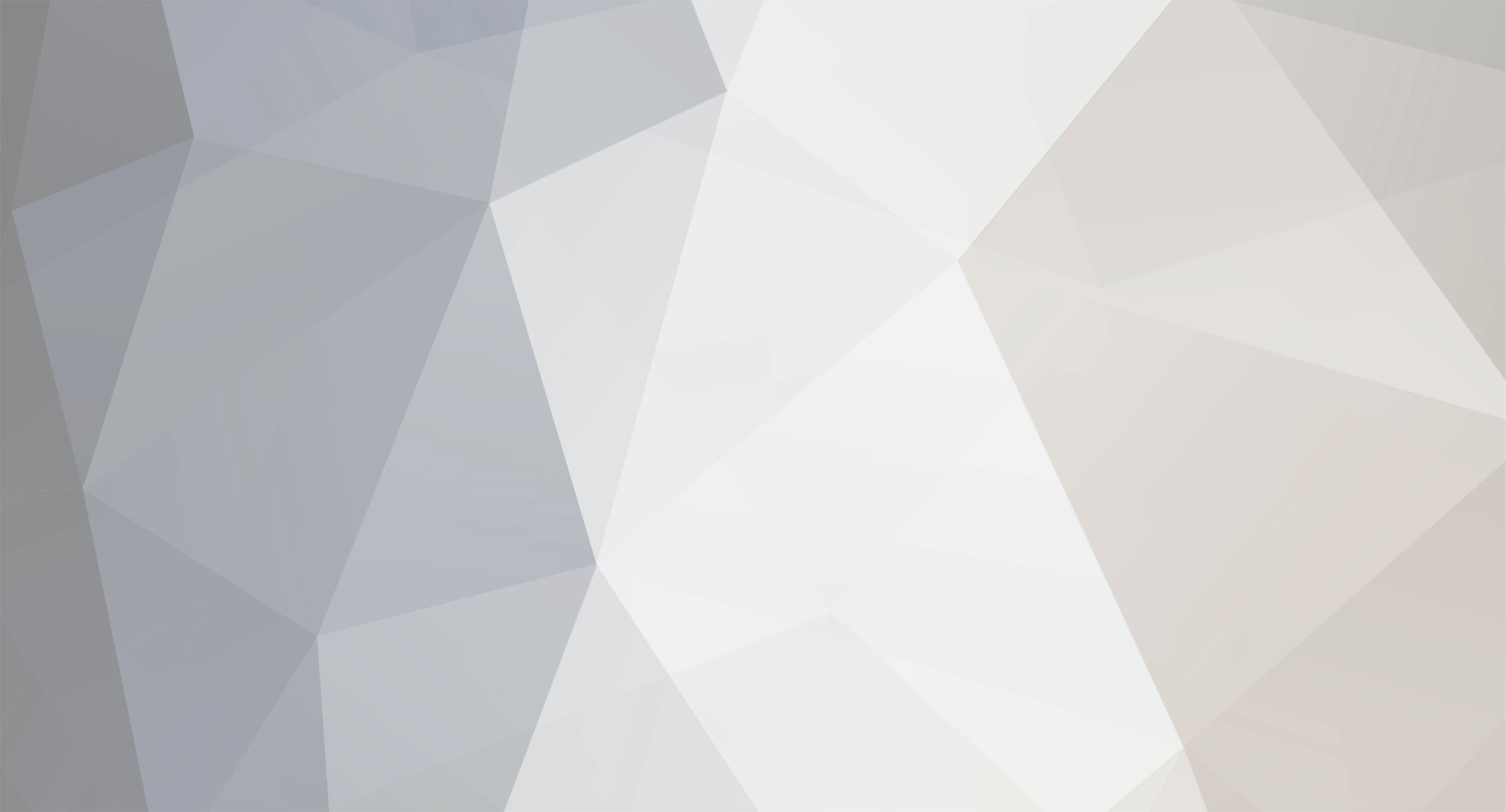
Andrew
Members-
Posts
198 -
Joined
-
Last visited
Everything posted by Andrew
-
I've just checked our cost spreadsheet and our TF was 22.9% of the overall build cost (total includes consultant fees and a bit of landscaping). That was for the TF itself, erection including a mostly cut on site complex roof structure but no felt and battening and supply & fitting of insulation on site to 0.11 w/m2k throughout the thermal envelope. So I don't think you are a million miles off with your assumption above. As an aside one thing that surprised me in terms of material cost and labour cost were the fascias, barge boards, soffits and any valley boards / roof noggins that may be required. If I were doing it again I would negotiate it into the TF company package - that way once the TF team are finished the build should be ready for the roofers to start straight away.
-
@Siggles I'm delighted that's solved the problem. I think there may be a batch of PCBs with a component issue (although no-one admitted this) so I guess not too surprising that we've had the same problem. I'm also pleased that anyone googling may find this thread as when I was looking there was very little information out there on the issue. Hopefully this will help others.
-
Actually turns out I already had a photo on my computer. The things I've circled in yellow are the relays on the boards - the black rectangles. I'm not sure exactly which one it is that controls the primary pump so I just gave them all a hard tap - like a flick with my nail. In my case this got the relay moving again. It is possible for the relay to have welded shut if there has been an arc across the contacts at some point. If that's the case I don't think you are going to be able to get it moving again and will need a new PCB or relay. Good Luck. Btw if you do need a new PCB then Freedom Heat Pumps are a UK distributor for these Samsung units and AFAIK also administer the warranty on behalf of Samsung. I still think you would be best going back to the people who installed it and asking them to help, but I believe Freedom told my electrician that a new PCB was about £180 if you need to buy a new one.
-
I've recently had the exact same problem on the same heat pump. E911 is the lack of flow error code - this is what you get if there isn't enough flow through the primary loop. E912 means the flow switch is detecting flow when it believes it shouldn't. I was seeing this error about 10 minutes after there was no call for heat. In my case a relay in the control board was stuck closed so the primary loop circulating pump was running even when the controller thought it wasn't. I could confirm this by turning off the power to the controller and turning back on - the primary loop circulation pump would start up immediately every time. You can also check by going into self-test mode (you'll need to hold down up and down arrows on the controller display, it asks for a code, input 0202). In that menu there is a self-test option which you can turn the circulating pump on and off manually. If the pump stays on when it has been turned off in the menu you'll know the relay is the problem. I was able to fix mine temporarily by powering off the controller, opening the box and giving the relay a tap which caused it to start working again. I got a new PCB under warranty from Freedom Heat Pumps who supplied the unit, which has hopefully permanently fixed the issue.
-
I've had to furnish 2 bathrooms, 2 en-suites and a downstairs toilet. We used a mixture of different brands and suppliers. Most of the things like vanity units and shower screens came from Victoria Plumb in the sale. They are crafty beggars and I needed to keep a fairly long-term view on the price of the things to get a true picture of when they are actually reduced. Stone resin shower trays were generic unbranded from a random bathroom supplies website - all have turned out fine. We decided to go for Grohe taps and shower mixers throughout as we wanted something decent quality (and to be honest it's the only logo you would really see) - these were from the cheapest website I could find that stocked them - again turned out fine and look good. For tiles I got all of our from the Johnson Tiles factory outlet in Stoke (https://www.johnson-tiles.com / https://outlet.johnson-tiles.com). It wasn't too much of a trek for us to go and have a look at what they had and then I called up and ordered what we wanted which they delivered on a pallet. They were well up for a deal too, I think I got about 15% - 20% off an order of £1500. I'd say the best thing to do would be to buy to your budget, you can spend mega money on bathrooms but also do it quite fugally but still have good looking results (I spent about £7.5k total on all the stuff for our 6 bathrooms including electric underfloor heating mats + towel radiators). The other thing to mention is alway open and check the stuff when it arrives. I didn't install one of the vanity units from Victoria Plumb until 13 months after it arrived, and of course that was the one with a broken handle. It was a real challenge to get them to replace it - had to leave a bad Trustpilot review threatening the small claims court before they "found a spare one in the warehouse" and sent it out to me.
-
The plumber came yesterday and we flushed everything out to ensure there is no air in the system but it's still not working as expected. What seems to be happening is that the manifold nearest to the plate heat exchanger is taking all of the flow, so when that thermostat is calling for heat the other manifold gets little flow. When the zone valve of the near manifold is closed the other manifold then seems to get decent flow. I've attached a very crappy diagram of how the system is set-up. Apologies I don't know the correct symbols for everything and I've left out the actual UFH loops. The branches to the manifolds are just teed off the pipework. I know little of fluid dynamics so I don't really know how the water would be expected to behave in this situation. Would beefing up the pump near the plate heat exchange improve things or could pumps be added to each of the runs to the manifolds (after the zone valves). If these were added would the pump near the plate heat exchanger still be needed?
-
Yes all the white values and flow gauges are all fully open. I'm starting to wonder if there may be an airlock on the flow side somewhere - I guess this could cause the issue if there is very little flow getting to the manifold. The flow and return pipe run does go from knee height in the plant room up to first floor joist level before coming back down to the manifold.
-
Arrow on the pump is pointing upwards, so seems correct. Yes, I'm sure the flow is on the correct, when I turn the TMV and restrict the flow then I can feel the elbow by the red isolation valve heat up which then is reflected in the temp gauge on the top rail. Problem is the flow meters are then at zero so no heat goes round the loops.
-
Thanks Dave. It's the Wunda premium pump set (as of about 24 months ago when I bought it). The instructions are here - https://cdn.wundatrade.co.uk/wp-content/uploads/2017/08/M06-Wunda-Pumpset-1.pdf I'm not sure if you can see from the photo but the red / blue dots are on the correct sides, so it looks to me like the plumber put it on the right way!
-
Having moved into our self-build in June, we are only just this weekend using the heating in anger for the first time. Unfortunately it isn't working very well. The system has two manifolds, an 8 port and a 4 port both fed from an ASHP. The manifolds are fed from a plate heat exchanger, there is pump on this side of the heat exchanger which runs when the ASHP is in heating mode. Each manifold is set-up as a single zone (i.e. no actuators on the manifolds) for simplicity, with a thermostat, pump on the manifold and a 2-way zone valve controlling each one. All of the control side seems to work fine with the thermostat calling for heat at the appropriate time, the ASHP is firing up, the pump near the PHE is running, the zone valve opening and the pump on the manifold running. The problem seems to be related to the TMV on the manifold - by twisting from 'Min' to 'Max' (this TMV does not show the temperature) I can either have full flow through the manifold but no heat (i.e. the water seems to just be circulating through the pump - the flow and return on the manifold are the same temperature) or by turning it to 'Max' I can have some of the incoming heat but it seems to throttle the flow completely (the flow meters show zero). Btw I have opened the flow meters and the white caps on the manifold fully so these are not constraining the flow at all. I have tried to find a 'sweet spot' on the TMV where the flow and temperature are balanced but it seems to be a knife edge, as soon as any heat gets through the TMV the flow just seems to disappear. I have tried a variety of supply temperatures from the ASHP, starting at 30 degrees and up to 40 degrees but it doesn't seem to make any difference. I should also note that both of the manifolds do the exact same thing so I don't think it's a faulty TMV. I've attached a photo of the manifold. I'm tearing my hair out as I can't get enough heat into the floor to raise the temperature, at the moment the ASHP is running constantly but there is very little of that heat reaching the house. Any ideas or help would be very gratefully received. Thanks.
-
I haven’t got the energy to write out my experiences so far getting connected with openreach (still not connected after 6 months) but it has been a kafkaesque nightmare.
-
Looks to me like a jolly good example of why we have the planning system and building regulations.
-
Have a look at the website linked further up by @Alfie if you want to see the mere essence of pretentiousness - https://www.huxshard.uk
-
The external appearance wasn't really to my taste but I did like some of the interior. £120k on a kitchen blows my mind - for me it didn't look 6 times better than a £20k kitchen despite all the fancy finishes and materials. I prefer to watch the Grand Designs where the owner puts in much of the work themselves and are hence much more invested in the building. On last night's episode the guy didn't seem interested in how it was built - his view was if there's a problem just throw some more money at it. Rightly or wrongly the vision definitely belonged solely to the architect.
-
Biggest problem with calling round is that the people you speak to (sales / customer service) don’t really have a clue about 3-ph smart meter availability. Some will promise the earth but then months later still can’t deliver (as was our experience with Octopus). I think it’s a bit of a gamble in reality. We ended up switchIng to SSE as they were able to quickly install a 3-ph meter albeit not a smart one. We needed this so the electrician could complete his testing and issue the documentation for sign-off. When I feel up to it I’ll switch again to someone who can install a 3-ph smart meter. Should be straightforward, just tell them you want a single phase meter installed on your 3-ph supply. I had a single phase smart meter installed initially on our 3-ph supply. However if you are planning to use the 3 phases later, I would start the process of getting a 3-phase meter now as you can always just use a single phase from the 3-phase meter.
-
Hot return circuit, how to control it.
Andrew replied to Russell griffiths's topic in General Plumbing
I’ve installed one of these smart pumps - https://product-selection.grundfos.com/uk/products/comfort?tab=products. It’s meant to learn usage patterns and modulate accordingly. We only moved in on Wednesday so can’t yet comment on effectiveness or energy usage. -
I had estimators online (other online estimating services exist) do a cost estimate from the building regs drawings, tweaked it a bit and submitted that. In practice it was just passed on to the valuing surveyor who came up with their own build cost estimate based on RICS tables and sq. footage. This was £225k more than my (slightly ambitious) cost estimate. Ecology didn't seem bothered by this higher build cost estimate as there was plenty of headroom on the LTV and affordability to increase the loan if necessary. I have found Ecology very flexible and pragmatic.
-
Same happened to me. I was in collecting 7 wastes and traps and they asked if I was a plumber. Told them no, but I was building a house and that was good enough. Quite enjoy going through the special door whilst there's a big queue of people at the main counter.
-
We originally had a single phase temp electrical supply to our build, but in December last year this temporary supply was moved into the garage and upgraded to a 3 phase supply. We have high electrical demand with 2 x electric car charging, 12kW ASHP, 2 x double ovens, etc and the electrician has done his planning and diversity calcs based on having a 3-phase supply into the garage + house. We are part way through the 2nd fix and a 3 phase consumer unit has been fitted. The problem is that we only have a single phase meter attached to the incoming supply and I'm tearing my hair out trying to get a 3-phase meter installed. Originally the temp supply was with British Gas then we switched to Ebico to take advantage of the zero standing charge, but ironically they were bought by British Gas and we ended up back with British Gas. I called BG early in January this year and enquired about having the meter swapped to 3-phase. They said during lock down they are not doing any meter swaps. So I contacted Octopus and asked them if they were installing 3-phase meters during lock down. 'Yes' came the reply, so we switched to Octopus going on supply at early Feb. Since then I seem to have been caught in a nightmarish loop of broken promises and declarations of 'it'll be a few weeks'. Latest excuse is that the 3-phase smart meters are stuck in the Suez canal - I kid you not. I've lodged a formal complaint today but I'm coming to the conclusion they they either can't or don't want to install a 3-phase meter for us. Btw I'd like it to be a smart meter but at this point I will take any 3-phase meter if it gets us connected, something I've told Octopus repeatedly. I don't think it will be possible to move into the house until the 3-ph meter is installed and our very busy electrician is using it as an excuse to stall 2nd fix. So I think I'm going to have to switch providers again to get the 3-phase meter installed. The question to the wisdom of BH is - does anyone have any experience of an energy supplier who will be able to quickly install a 3 phase meter for us? I really don't want to switch again and be no further forward. TIA.
-
I didn't bother in the end, mainly as budget is under stress and whilst the quote was only £1500, all these 'only' 1500 quid items add up. I have laid a duct from the plant room under the driveway to the boundary so if the ASHP turns out to be a disaster we can connect it without digging up the drive.
-
The valuer who valued our build, twice, was a complete bell-end (sorry I really can't find a more accurate term). He'd been everywhere and done everything, the self-build he did was bigger, more expensive, more complicated, blah de blah. He valued the completed build £75k less than my conservative estimate and £50k less than the recently sold new-build house across the road with 2 fewer bedrooms on a smaller plot which had been built to a lesser standard. He was based 30 miles away and had no clue about the local market. At the end of the day the valuation was enough to get us the borrowing we wanted so I just bit my tongue rather than start kicking up a fuss. The second time he came to value mid-build he just asked me what my rough guess was of the cost to complete and he just put in a current valuation of his original completed valuation minus my guesstimate of the cost to complete! The valuation bit took him 2 minutes but he was on site for over an hour telling me of his greatness.
-