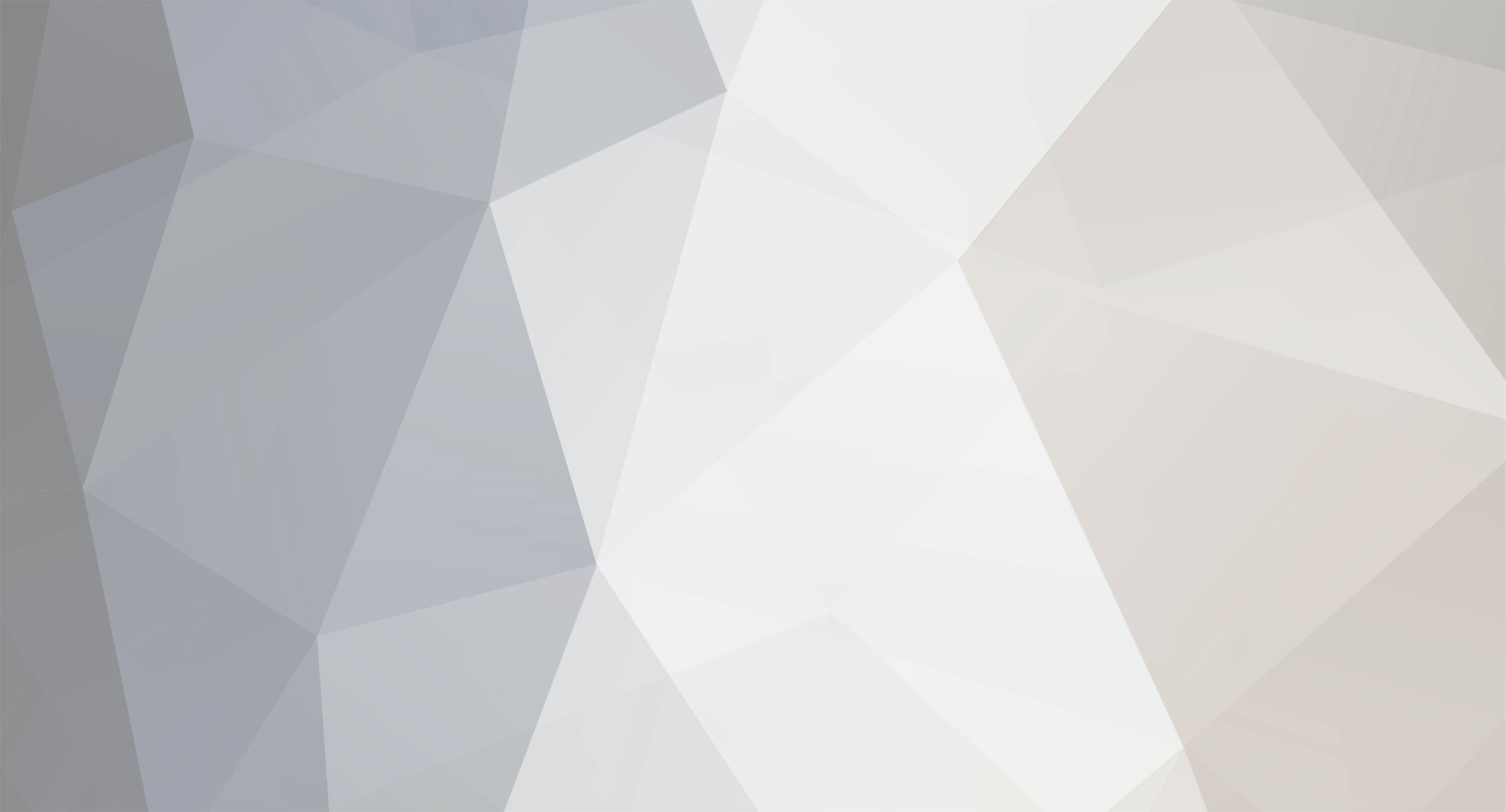
Andrew
Members-
Posts
198 -
Joined
-
Last visited
Andrew's Achievements

Regular Member (4/5)
75
Reputation
-
I've just checked our cost spreadsheet and our TF was 22.9% of the overall build cost (total includes consultant fees and a bit of landscaping). That was for the TF itself, erection including a mostly cut on site complex roof structure but no felt and battening and supply & fitting of insulation on site to 0.11 w/m2k throughout the thermal envelope. So I don't think you are a million miles off with your assumption above. As an aside one thing that surprised me in terms of material cost and labour cost were the fascias, barge boards, soffits and any valley boards / roof noggins that may be required. If I were doing it again I would negotiate it into the TF company package - that way once the TF team are finished the build should be ready for the roofers to start straight away.
-
@Siggles I'm delighted that's solved the problem. I think there may be a batch of PCBs with a component issue (although no-one admitted this) so I guess not too surprising that we've had the same problem. I'm also pleased that anyone googling may find this thread as when I was looking there was very little information out there on the issue. Hopefully this will help others.
-
Actually turns out I already had a photo on my computer. The things I've circled in yellow are the relays on the boards - the black rectangles. I'm not sure exactly which one it is that controls the primary pump so I just gave them all a hard tap - like a flick with my nail. In my case this got the relay moving again. It is possible for the relay to have welded shut if there has been an arc across the contacts at some point. If that's the case I don't think you are going to be able to get it moving again and will need a new PCB or relay. Good Luck. Btw if you do need a new PCB then Freedom Heat Pumps are a UK distributor for these Samsung units and AFAIK also administer the warranty on behalf of Samsung. I still think you would be best going back to the people who installed it and asking them to help, but I believe Freedom told my electrician that a new PCB was about £180 if you need to buy a new one.
-
I've recently had the exact same problem on the same heat pump. E911 is the lack of flow error code - this is what you get if there isn't enough flow through the primary loop. E912 means the flow switch is detecting flow when it believes it shouldn't. I was seeing this error about 10 minutes after there was no call for heat. In my case a relay in the control board was stuck closed so the primary loop circulating pump was running even when the controller thought it wasn't. I could confirm this by turning off the power to the controller and turning back on - the primary loop circulation pump would start up immediately every time. You can also check by going into self-test mode (you'll need to hold down up and down arrows on the controller display, it asks for a code, input 0202). In that menu there is a self-test option which you can turn the circulating pump on and off manually. If the pump stays on when it has been turned off in the menu you'll know the relay is the problem. I was able to fix mine temporarily by powering off the controller, opening the box and giving the relay a tap which caused it to start working again. I got a new PCB under warranty from Freedom Heat Pumps who supplied the unit, which has hopefully permanently fixed the issue.
-
I've had to furnish 2 bathrooms, 2 en-suites and a downstairs toilet. We used a mixture of different brands and suppliers. Most of the things like vanity units and shower screens came from Victoria Plumb in the sale. They are crafty beggars and I needed to keep a fairly long-term view on the price of the things to get a true picture of when they are actually reduced. Stone resin shower trays were generic unbranded from a random bathroom supplies website - all have turned out fine. We decided to go for Grohe taps and shower mixers throughout as we wanted something decent quality (and to be honest it's the only logo you would really see) - these were from the cheapest website I could find that stocked them - again turned out fine and look good. For tiles I got all of our from the Johnson Tiles factory outlet in Stoke (https://www.johnson-tiles.com / https://outlet.johnson-tiles.com). It wasn't too much of a trek for us to go and have a look at what they had and then I called up and ordered what we wanted which they delivered on a pallet. They were well up for a deal too, I think I got about 15% - 20% off an order of £1500. I'd say the best thing to do would be to buy to your budget, you can spend mega money on bathrooms but also do it quite fugally but still have good looking results (I spent about £7.5k total on all the stuff for our 6 bathrooms including electric underfloor heating mats + towel radiators). The other thing to mention is alway open and check the stuff when it arrives. I didn't install one of the vanity units from Victoria Plumb until 13 months after it arrived, and of course that was the one with a broken handle. It was a real challenge to get them to replace it - had to leave a bad Trustpilot review threatening the small claims court before they "found a spare one in the warehouse" and sent it out to me.
-
The plumber came yesterday and we flushed everything out to ensure there is no air in the system but it's still not working as expected. What seems to be happening is that the manifold nearest to the plate heat exchanger is taking all of the flow, so when that thermostat is calling for heat the other manifold gets little flow. When the zone valve of the near manifold is closed the other manifold then seems to get decent flow. I've attached a very crappy diagram of how the system is set-up. Apologies I don't know the correct symbols for everything and I've left out the actual UFH loops. The branches to the manifolds are just teed off the pipework. I know little of fluid dynamics so I don't really know how the water would be expected to behave in this situation. Would beefing up the pump near the plate heat exchange improve things or could pumps be added to each of the runs to the manifolds (after the zone valves). If these were added would the pump near the plate heat exchanger still be needed?
-
Yes all the white values and flow gauges are all fully open. I'm starting to wonder if there may be an airlock on the flow side somewhere - I guess this could cause the issue if there is very little flow getting to the manifold. The flow and return pipe run does go from knee height in the plant room up to first floor joist level before coming back down to the manifold.
-
Arrow on the pump is pointing upwards, so seems correct. Yes, I'm sure the flow is on the correct, when I turn the TMV and restrict the flow then I can feel the elbow by the red isolation valve heat up which then is reflected in the temp gauge on the top rail. Problem is the flow meters are then at zero so no heat goes round the loops.
-
Thanks Dave. It's the Wunda premium pump set (as of about 24 months ago when I bought it). The instructions are here - https://cdn.wundatrade.co.uk/wp-content/uploads/2017/08/M06-Wunda-Pumpset-1.pdf I'm not sure if you can see from the photo but the red / blue dots are on the correct sides, so it looks to me like the plumber put it on the right way!
-
Having moved into our self-build in June, we are only just this weekend using the heating in anger for the first time. Unfortunately it isn't working very well. The system has two manifolds, an 8 port and a 4 port both fed from an ASHP. The manifolds are fed from a plate heat exchanger, there is pump on this side of the heat exchanger which runs when the ASHP is in heating mode. Each manifold is set-up as a single zone (i.e. no actuators on the manifolds) for simplicity, with a thermostat, pump on the manifold and a 2-way zone valve controlling each one. All of the control side seems to work fine with the thermostat calling for heat at the appropriate time, the ASHP is firing up, the pump near the PHE is running, the zone valve opening and the pump on the manifold running. The problem seems to be related to the TMV on the manifold - by twisting from 'Min' to 'Max' (this TMV does not show the temperature) I can either have full flow through the manifold but no heat (i.e. the water seems to just be circulating through the pump - the flow and return on the manifold are the same temperature) or by turning it to 'Max' I can have some of the incoming heat but it seems to throttle the flow completely (the flow meters show zero). Btw I have opened the flow meters and the white caps on the manifold fully so these are not constraining the flow at all. I have tried to find a 'sweet spot' on the TMV where the flow and temperature are balanced but it seems to be a knife edge, as soon as any heat gets through the TMV the flow just seems to disappear. I have tried a variety of supply temperatures from the ASHP, starting at 30 degrees and up to 40 degrees but it doesn't seem to make any difference. I should also note that both of the manifolds do the exact same thing so I don't think it's a faulty TMV. I've attached a photo of the manifold. I'm tearing my hair out as I can't get enough heat into the floor to raise the temperature, at the moment the ASHP is running constantly but there is very little of that heat reaching the house. Any ideas or help would be very gratefully received. Thanks.
-
I haven’t got the energy to write out my experiences so far getting connected with openreach (still not connected after 6 months) but it has been a kafkaesque nightmare.
-
Looks to me like a jolly good example of why we have the planning system and building regulations.