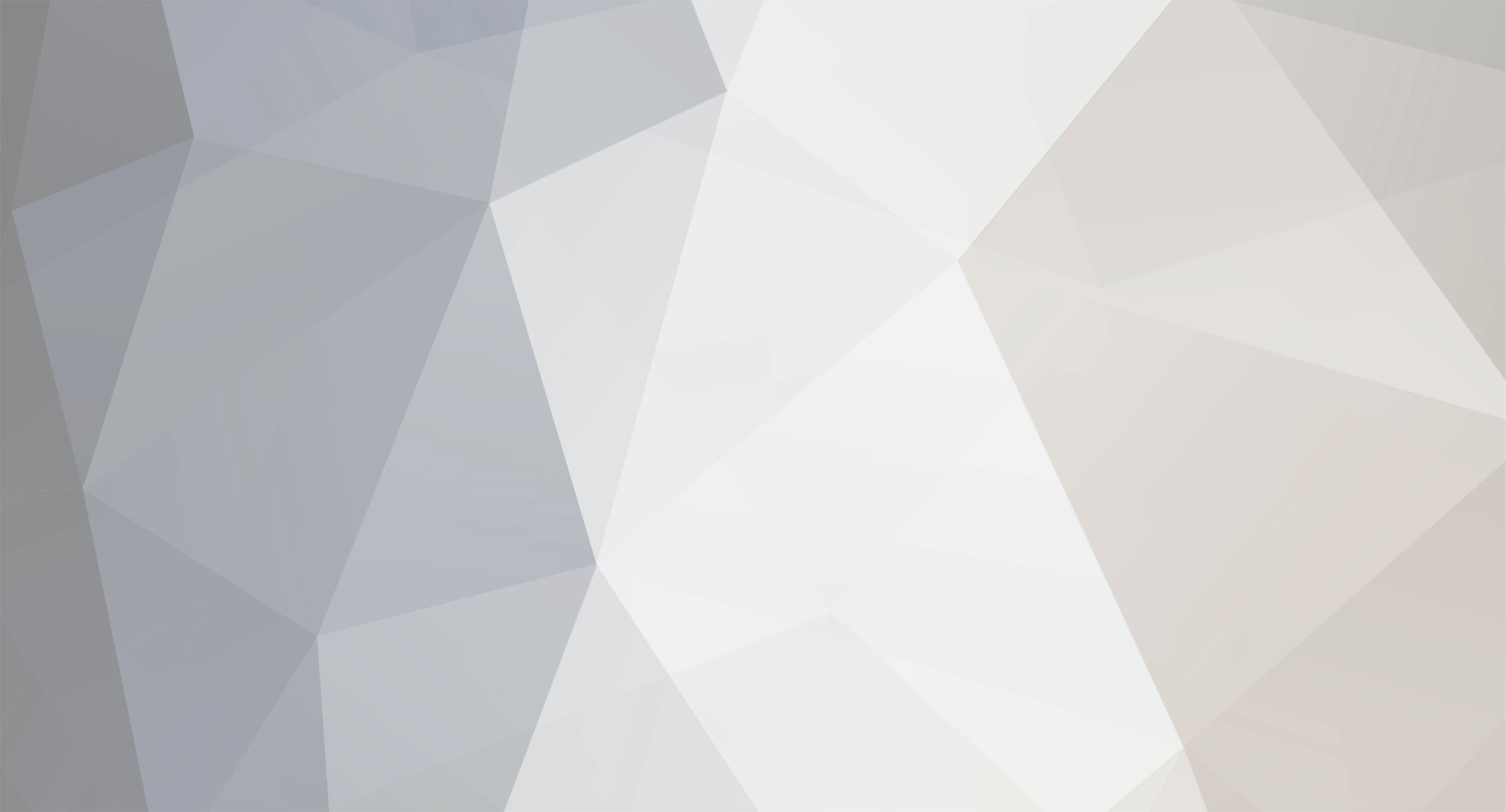
Ian
Members-
Posts
751 -
Joined
-
Last visited
-
Days Won
3
Everything posted by Ian
-
Just make sure your tiler is going to use a good quality decoupling mat under the tiles. Schluter's ''Ditra 25'' is very good and that's what I specified on my own self-build as well as on any of our commercial projects. https://www.schluter.co.uk/media/schlueter_db_6_1_ditra_uk.pdf
-
Cost per square metre for single story vs 2 story dwelling
Ian replied to smart51's topic in Costing & Estimating
That's correct. -
Cost per square metre for single story vs 2 story dwelling
Ian replied to smart51's topic in Costing & Estimating
@smart51 rule of thumb is that it costs approx 15% more per square/m to build a bungalow compared to a normal 2 storey house -
The old fashioned way- natural ventilation via windows that open. Also you’re supposed to have trickle vents on the windows.
-
Extra Note: in Exposure Zone 4 (see page 35 of Part C) the minimum residual cavity is 75mm if you’re building a masonry cavity wall using facing bricks.
-
Probably too late for the OP (I’m not here very often these days as it’s now 5 years since I finished my own build) but for the benefit of anyone else contemplating a masonry cavity wall, the Approved Docs for England (not sure about Scotland) expressly require a minimum cavity width of 50mm. The alternative is full-fill insulation. The relevant bit of the regs is Part A, Page 14, Sections 2C8. It’s also in Part C, Page 32, Section 5.15 together with diagrams showing the options.
-
No, the Osmo Poly-x has been great - no issues at all with it in the 5 years since we did the work.
- 21 replies
-
- doors
- spraying doors
-
(and 2 more)
Tagged with:
-
As @Conor says the main issue is that all the loft insulation needs to be in the same place and, with your roof, it would be best to add it to the insulation that you’ve already got across the floor of the loft. Adding extra insulation to loft spaces can sometimes lead to condensation problems in the roof void - the degree of risk depends on how well ventilated your loft space is and the type (if any) of the roofing felt that’s under the tiles.
-
@Marvin you could try Gorilla tape. I’ve used it for an external repair and it’s lasted 3 or 4 years so far without failing. https://www.amazon.co.uk/Gorilla-Glue-3044401-Duct-Black/dp/B001E5ZWT4/ref=asc_df_B001E5ZWT4/?tag=googshopuk-21&linkCode=df0&hvadid=223237768057&hvpos=&hvnetw=g&hvrand=4834807999352096810&hvpone=&hvptwo=&hvqmt=&hvdev=m&hvdvcmdl=&hvlocint=&hvlocphy=9046437&hvtargid=pla-312217067516&psc=1&th=1&psc=1
-
Sewage treatment plant - air blower electricity costs
Ian replied to David Essex's topic in Waste & Sewerage
We use ours as a holiday home so it’s only used 2 or 3 days max a week. We have a Bio Pure 1 which has been running now for 5 years with no issues. When I completed the build I rang the manufacturer for advice about the best way to operate the air pump due to the intermittent loading and I was told to put it on a timer set to operate 2 hours on and 2 hours off. It’s been completely problem free with no smells. The added benefit of the timer is that it halves the running cost. -
Sewage treatment plant - air blower electricity costs
Ian replied to David Essex's topic in Waste & Sewerage
Our Bio Pure 1 came with a Secoh JDK-S-60 air pump which only uses 40 W. -
How well does vermiculite insulate compared to fibreglass, PIR, etc?
Ian replied to Oxbow16's topic in Heat Insulation
It has a thermal conductivity of 0.063 W/mK. article about its insulation value & cost compared to loft roll insulation here: https://www.thegreenage.co.uk/micafil-loose-fill-loft-insulation/ -
We’re coming up for 5 years with our 3G windows. The only condensation we get is on the outside. They are bog-standard Rehau upvc frames but fitted with 44mm glazing units
- 131 replies
-
- 1
-
-
- triple glazing
- condensation
-
(and 3 more)
Tagged with:
-
Paranoid about spontaneous failure of large skylight
Ian replied to hendriQ's topic in Skylights & Roof Windows
Yes, you're correct. Commercial projects almost always carry higher risks than domestic so it will depend on your attitude to risk whether or not you wish to exceed the minimum requirements of the Building Regs. The relevant guidance is in BS 5516-2 and it takes a risk based approach. Below are some extracts relevant to your build:- 49 replies
-
- skylight
- heat soak testing
-
(and 1 more)
Tagged with:
-
Paranoid about spontaneous failure of large skylight
Ian replied to hendriQ's topic in Skylights & Roof Windows
@hendriQ the glass spec that would be used on a typical commercial project with overhead glazing or for balustrading would be for the lower pane of glass to be toughened laminated (IE: 2 panes of toughened glass laminated together). The upper pane would be typically be toughened. (All toughened glass to be heat-soaked) with toughened laminated glass, if one of the 2 panes breaks the plastic interlayer and the other intact pane holds everything in place.- 49 replies
-
- skylight
- heat soak testing
-
(and 1 more)
Tagged with:
-
I got all my ABS Avocet anti-snap Eurolock barrels & keys from JC Plastics on Amazon: https://www.amazon.co.uk/dp/B015YCZVJS/ref=pe_3187911_189395841_TE_dp_1 Edit: unlike the Yale anti-snap barrels these Avocet ones need no adaptation to the door and are a straightforward fit.
-
Marks on Larch cladding when using stainless steel nails
Ian replied to David R's topic in General Joinery
A4 stainless steel would be better than A2 in locations anywhere near the coast or industrial areas. A4 vs A2: https://www.bolts.co.uk/guides-and-tips/heads-threads-and-finishes/difference-between-a2-and-a4-stainless-steel/ -
You’re best option is to use a liquid DPM on top of your screed which will allow you to lay the engineered wood on top.
-
@Clemenza you need to use a F2S2 grade of brick in this situation: https://www.brick.org.uk/admin/resources/g-brickwork-durability.pdf
-
@Moggaman the insulation layer is there for acoustic reasons - it’s there to prevent impact noise like footsteps transmitting directly through to the rooms below.
-
There’s nothing in either the British Standard or in the Building Regs that stipulate a maximum gradient so you’ll be okay when the inspector visits.
- 24 replies
-
- 1
-
-
Good link here to a Scottish Gov publication: https://www.gov.scot/publications/timber-cladding-scotland/pages/13/
-
We’ve got a house which is surrounded by mature oak and sycamore trees. I first tried the flat type grids and the wet leafs just sat on top and blocked the whole thing off. I then switched to hedgehogs and they’re much better.
-
I got one prepared by a local solicitor when we were preparing our own planning application. It didn’t cost much. We also got some friendly neighbours to write letters of support which included statements about the existence of a previous structure on the site.