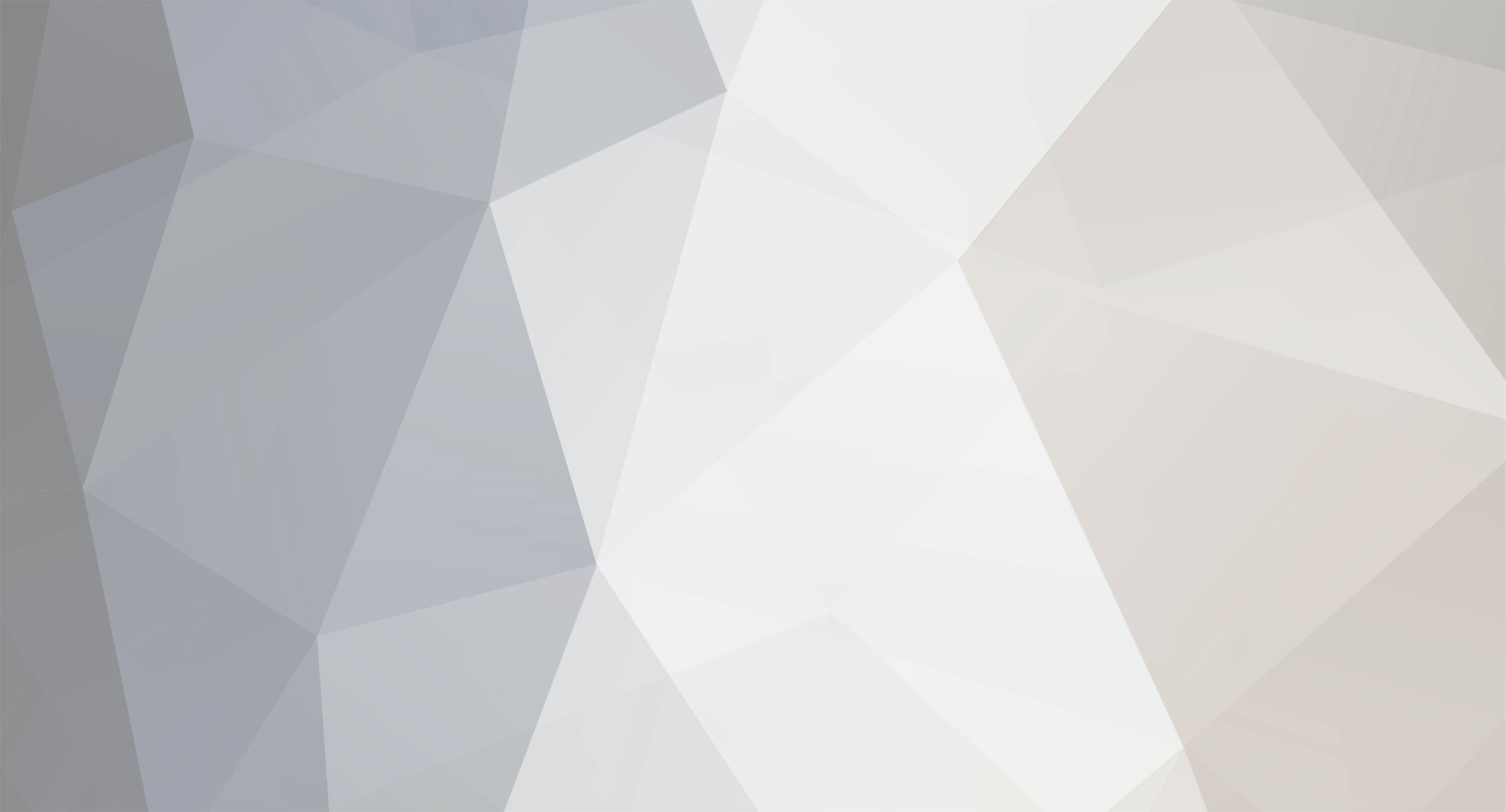
Ian
Members-
Posts
751 -
Joined
-
Last visited
-
Days Won
3
Ian last won the day on July 15 2020
Ian had the most liked content!
Personal Information
-
About Me
RIBA Chartered Architect
Recent Profile Visitors
8629 profile views
Ian's Achievements

Regular Member (4/5)
292
Reputation
-
Just make sure your tiler is going to use a good quality decoupling mat under the tiles. Schluter's ''Ditra 25'' is very good and that's what I specified on my own self-build as well as on any of our commercial projects. https://www.schluter.co.uk/media/schlueter_db_6_1_ditra_uk.pdf
-
Cost per square metre for single story vs 2 story dwelling
Ian replied to smart51's topic in Costing & Estimating
That's correct. -
Cost per square metre for single story vs 2 story dwelling
Ian replied to smart51's topic in Costing & Estimating
@smart51 rule of thumb is that it costs approx 15% more per square/m to build a bungalow compared to a normal 2 storey house -
The old fashioned way- natural ventilation via windows that open. Also you’re supposed to have trickle vents on the windows.
-
Extra Note: in Exposure Zone 4 (see page 35 of Part C) the minimum residual cavity is 75mm if you’re building a masonry cavity wall using facing bricks.
-
Probably too late for the OP (I’m not here very often these days as it’s now 5 years since I finished my own build) but for the benefit of anyone else contemplating a masonry cavity wall, the Approved Docs for England (not sure about Scotland) expressly require a minimum cavity width of 50mm. The alternative is full-fill insulation. The relevant bit of the regs is Part A, Page 14, Sections 2C8. It’s also in Part C, Page 32, Section 5.15 together with diagrams showing the options.
-
No, the Osmo Poly-x has been great - no issues at all with it in the 5 years since we did the work.
- 21 replies
-
- doors
- spraying doors
-
(and 2 more)
Tagged with:
-
As @Conor says the main issue is that all the loft insulation needs to be in the same place and, with your roof, it would be best to add it to the insulation that you’ve already got across the floor of the loft. Adding extra insulation to loft spaces can sometimes lead to condensation problems in the roof void - the degree of risk depends on how well ventilated your loft space is and the type (if any) of the roofing felt that’s under the tiles.
-
@Marvin you could try Gorilla tape. I’ve used it for an external repair and it’s lasted 3 or 4 years so far without failing. https://www.amazon.co.uk/Gorilla-Glue-3044401-Duct-Black/dp/B001E5ZWT4/ref=asc_df_B001E5ZWT4/?tag=googshopuk-21&linkCode=df0&hvadid=223237768057&hvpos=&hvnetw=g&hvrand=4834807999352096810&hvpone=&hvptwo=&hvqmt=&hvdev=m&hvdvcmdl=&hvlocint=&hvlocphy=9046437&hvtargid=pla-312217067516&psc=1&th=1&psc=1
-
Sewage treatment plant - air blower electricity costs
Ian replied to David Essex's topic in Waste & Sewerage
We use ours as a holiday home so it’s only used 2 or 3 days max a week. We have a Bio Pure 1 which has been running now for 5 years with no issues. When I completed the build I rang the manufacturer for advice about the best way to operate the air pump due to the intermittent loading and I was told to put it on a timer set to operate 2 hours on and 2 hours off. It’s been completely problem free with no smells. The added benefit of the timer is that it halves the running cost. -
Sewage treatment plant - air blower electricity costs
Ian replied to David Essex's topic in Waste & Sewerage
Our Bio Pure 1 came with a Secoh JDK-S-60 air pump which only uses 40 W. -
How well does vermiculite insulate compared to fibreglass, PIR, etc?
Ian replied to Oxbow16's topic in Heat Insulation
It has a thermal conductivity of 0.063 W/mK. article about its insulation value & cost compared to loft roll insulation here: https://www.thegreenage.co.uk/micafil-loose-fill-loft-insulation/ -
We’re coming up for 5 years with our 3G windows. The only condensation we get is on the outside. They are bog-standard Rehau upvc frames but fitted with 44mm glazing units
- 131 replies
-
- 1
-
-
- triple glazing
- condensation
-
(and 3 more)
Tagged with:
-
Paranoid about spontaneous failure of large skylight
Ian replied to hendriQ's topic in Skylights & Roof Windows
Yes, you're correct. Commercial projects almost always carry higher risks than domestic so it will depend on your attitude to risk whether or not you wish to exceed the minimum requirements of the Building Regs. The relevant guidance is in BS 5516-2 and it takes a risk based approach. Below are some extracts relevant to your build:- 49 replies
-
- skylight
- heat soak testing
-
(and 1 more)
Tagged with: