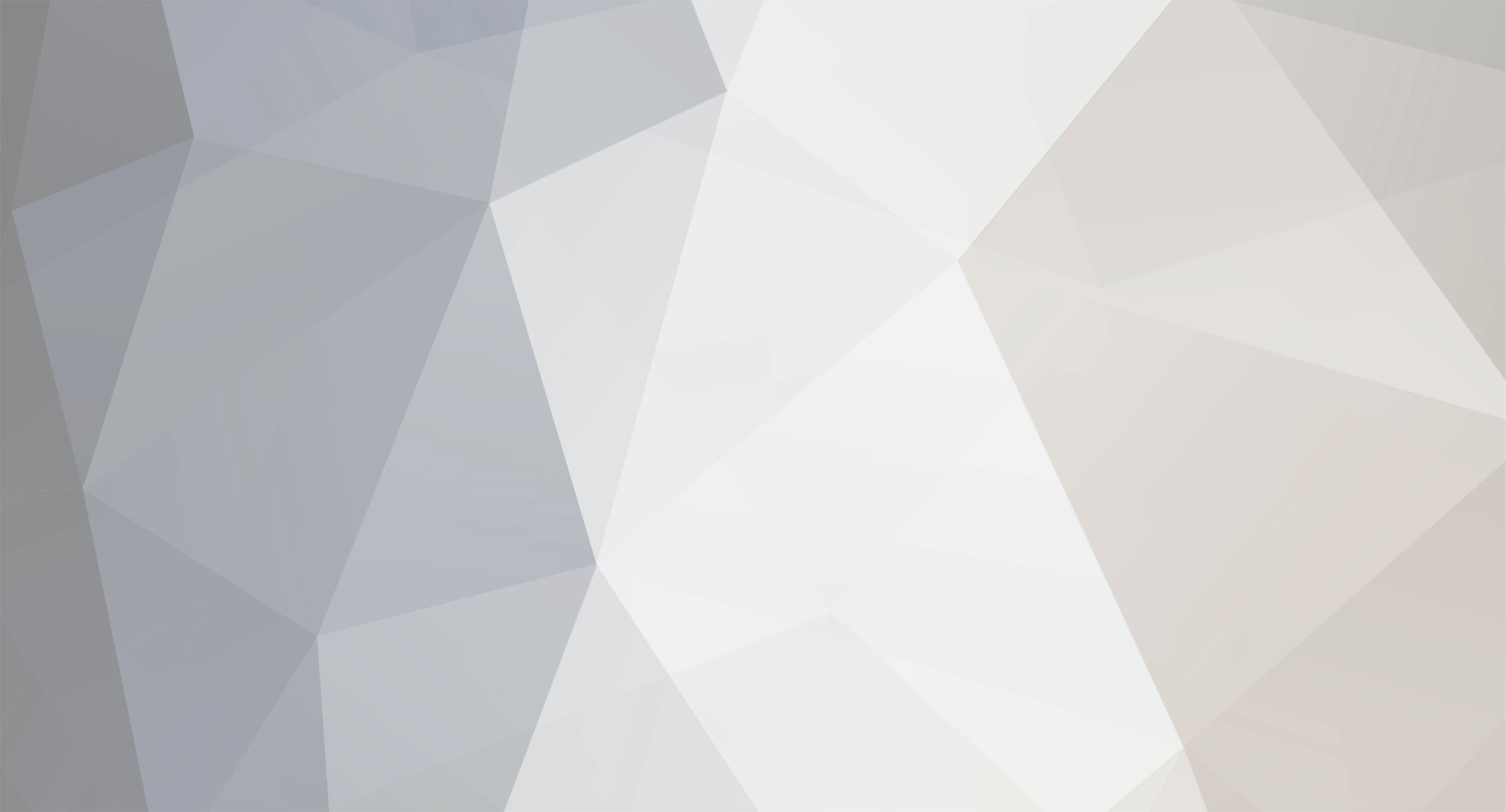
jfb
Members-
Posts
616 -
Joined
-
Last visited
jfb's Achievements

Regular Member (4/5)
120
Reputation
-
extension Construction Method in Old Stone Property Extension + Renovation
jfb replied to Lears's topic in Brick & Block
I just used lime.- 10 replies
-
- blockwork
- timberframe
-
(and 2 more)
Tagged with:
-
extension Construction Method in Old Stone Property Extension + Renovation
jfb replied to Lears's topic in Brick & Block
Really? I mean it depends on the house. And also on how much you value the aesthetic value of the old construction - a new version is going to be different and not always in a good way.- 10 replies
-
- blockwork
- timberframe
-
(and 2 more)
Tagged with:
-
extension Construction Method in Old Stone Property Extension + Renovation
jfb replied to Lears's topic in Brick & Block
I just used sand and hydraulic lime for the wall levelling layer(s). I recall diathonite is quite pricey and not sure worth it if you are using wood fibre IWI anyway. The amount of effort to get your walls flat depends on if they are back to stone, how level they are anyway, etc. I got my walls flat enough so that I didn't use any lime mix on the back of the wood fibre which makes its lot simpler to install. Even if it isn't flat the plastic fixings do a good job of pulling the boards in (not if 100mm thick though). I just used the cheapest wood fibre boards I could get (steico something) that were square edged (not tongue and groove). I think I might have used some expanding foam in a couple of places where there would be an obvious gap behind a board, but you could use some sand/lime as well there. Pretty sure it was full fill mineral fibre batts. No membrane on the internal - just lime render no mesh. Airtight and breathable. Put wooden flooring in - on battens set on the limecrete. But we have a pretty high water table in winter so that can't help dampness generally!- 10 replies
-
- blockwork
- timberframe
-
(and 2 more)
Tagged with:
-
extension Construction Method in Old Stone Property Extension + Renovation
jfb replied to Lears's topic in Brick & Block
I did very similar. Lime render to flatten walls, 60-80mm IWI wood fibre, lime render and mesh to finish. Has worked well. Good for air tightness if dealing with junctions well. Reckon it also performs much better than u values of materials might suggest. For extension i went for stone external wall, 200mm cavity with cavity batts for insulation, blocks for internal wall and lime render finish. For floor I went for 100mm compacted sub base, 200mm eps and Ufh pipes in 100mm concrete slab. I tried a limecrete and expanded glass floor in a small barn and had more problems with that regarding damp than the main house. But it does lie a bit lower. if you are hands on and want more details on IWI installation ask away- 10 replies
-
- blockwork
- timberframe
-
(and 2 more)
Tagged with:
-
Have the regs for copper tails from a boiler changed recently for brand new installs changed? friend thought it is now 1.5m not 1m
-
I thought it was but not sure
-
Probably not if you keep gas for cooking.
-
Welcome Lyn. definitely a lot of good advice to be found on here!
-
Brink Flair 400. Language setting?
jfb replied to Post and beam's topic in Mechanical Ventilation with Heat Recovery (MVHR)
How much setting does it actually need? I have a brink where the manual is in multiple languages so you could easily (?) cross reference the instructions to get the desired result. mayne best to check the manual is in English as well. -
Wood Fibre to prevent Thermal Bridging - How to handle joins
jfb replied to Lears's topic in Heat Insulation
What you have drawn does a decent job of mitigating thermal bridging I would say. Belt and braces would be to go round the internal section and join the IWI up. Can be done with curved corners to soften the edges if you want a less modern feel or else you’d have to use a plastic corner bead. It wouldn’t take much effort given what you are doing already.- 2 replies
-
- woodfibre
- thermal bridge
-
(and 3 more)
Tagged with:
-
Did they glue the osb down with expanding PU glue? squeaking could be because they didn’t use any and so might still squeak regardless what you put on top
-
Looking to put in place a board for easy/secure fixing of a CU. It’s a stone wall so much easier to have a wooden backing board. are you allowed these days to use a wooden board?