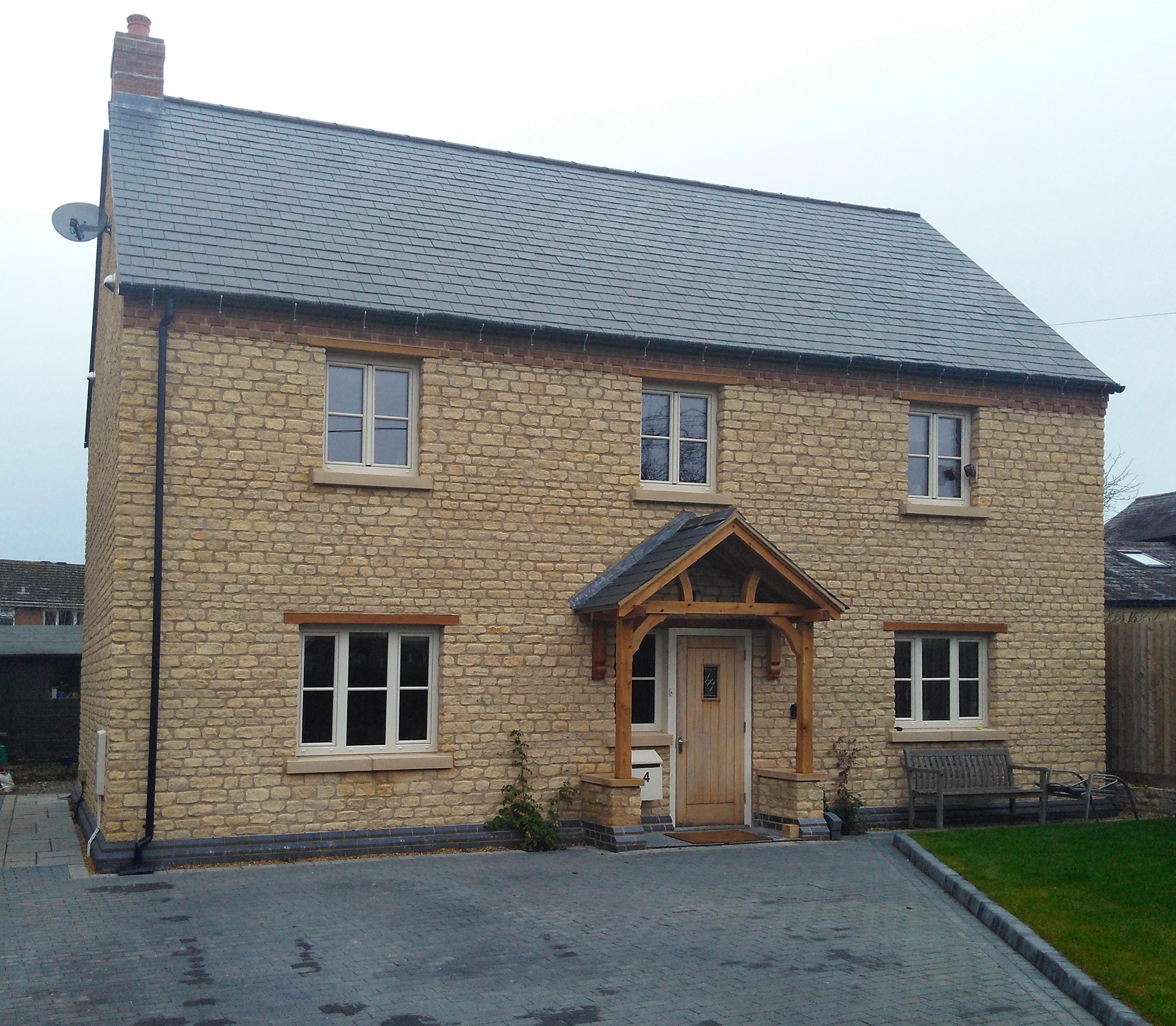
TerryE
Members-
Posts
3745 -
Joined
-
Last visited
-
Days Won
27
TerryE's Achievements

Advanced Member (5/5)
1.3k
Reputation
-
I understand the SAP / EPC issue, but in our case this also very flawed. We now use a double immersion heated 250 ltr OSO and our W/M and DW are in-appliance heated cold-fill and we almost always use ECO wash cycles time-shifted for cheapest Octopus Agile tariff rates. The OSO has under 1 kWh / day parasitic heat-loss and we (3 adults) use maybe 50 ltr at 50°C from our hot taps except on the occasional bath day. And again our OSO is heated at the cheapest Agile slots. The bottom line is that our DHW typically costs less than £1 / day, so it is really hard to come up with a cost benefit justification for the complexity of using alternative means of heating the HW. We don't currently have a ASHP but if we did I'd install a 5kW UHF only unit at a max O/P temp of 30°C direct into slab UFH at an SCoP of around 5.5.
-
As @ProDave says they are probably OK, but I personally would (i) check immediately under the joins for any evidence of dripping / water damage, and if so bite the bullet and replace them. (ii) don't disturb them unless you are going to fix them properly. The last time I got burnt by a joint this bad was about 40 years ago (I am not a professional plumber but only have done the plumbing on my own houses). In this case I left it but the joint then failed after I replaced the CH pump. I couldn't resolder because it was at a low point and I couldn't drain it down. I ended up cutting out a section and managed to put in a small insert with two new end-feeds. When I got the failed bit out and looked I found that the plumber had never actually soldered one side: the flux and gunk were all that was sealing the joint! Nick is the expert on this. He is my Sensei. 👍
-
My vote as well . I believe it to act as a keying surface for the mortar bed; a smooth surface is more likely to shear, and the slabs to loosen. 🙂
-
Our LPA were a bit arsey on this. Our old farmhouse next door and the listed cottage across the street were made of the locally quarried stone. The PA told that they would turn down flat reconstituted stone or machine cut stone because it wasn't character. We need a 1×1 m sample stone panel plus sample slate, and bricks used for the chimney and eve detailing. We used the sample to make up when we put up the porch plinth. 🤣
-
Is it worth having a gas connection for self build house?
TerryE replied to Wadrian's topic in Central Heating (Radiators)
We have an all-electric house. This was a design decision for our build, and one we've never regretted. -
Advantage of an induction hob.
TerryE replied to SteamyTea's topic in Kitchen & Household Appliances
We installed a 4 ring induction hob and a 2 ring propane backup for power cuts when we built the house ~8 years ago. I think we used the gas rings once in anger just to see if they worked. All cooking means have their foibles, but IMO I'd never go back to gas or conventional electric. -
I did maths and operations research as my degree, and then spent over 5 years doing physics based modelling in a management consultancy before moving into systems / IT, so this type of approach is "in my DNA": I trust an evidence based engineering approach. That's not the case for Jan who came up a different educational route. The key is finding a common evidenced basis to informed agreement in your partnership. Take an example Jan wanted a fire in LR, and I knew from the modelling that this would a disaster, but the argument that swayed Jan was my point that she really looked forward to spring, when we could clean out the hearth and decommission the fire over summer; the new house would be at this temperature all year round inside, so when would we ever want a fire? The final nail was a tale from someone who was talking about his passive house, and they'd put in a fire. They decided to light it one Christmas when the extended family was visiting. An hour later, everyone was standing in the garden with the doors and windows open waiting for the fire to out and the house cool off because the open plan downstairs was about 35°C. That was the one and only time they used the fire. 🤣 How many houses of the class that plan to build have you both visited and talked to the owners about the strengths, weaknesses and realities of living in their house? We must have visited ½doz or so. You expressing your views and research is one thing, but listening to others talk of their personal experience can be more compelling. Maybe your architect can link you up with other clients? If you are willing to share you post code area or nearest town, then you might be able to hook up with other members on the forum who would host a visit.
-
Surely you need an evidence-based conversation and come to a joint decision. Jan's comment was "it's going to cost a fortune to get the heating and cooling right: you've got to take the long view." You need to do the heat loss and solar gain calcs and make sure you both understand the implications. 2G panels have about 8-10× the U value of your walls and introduce lots of opportunity for air leeks. Do the sums; share them; own them and their consequences.
-
We have a passive class TF build with external stone cladding 2 storeys with 2 rooms and en-suite in warm loft, so really 3 floors. We have UFH on the ground floor in the poured slab and nothing on the two upper floors. Not having to stick rads on any walls is a real boon for laying out your rooms and planning built-in cupboards and furniture. BTW, all of our wardrobe space is in built-ins / walk-ins, so no VAT, and again keeps living space uncluttered. What we saved on CH costs easily paid for our (self-installed) MVHR. IMO, air-tightness isn't really a major cost as long as you've factored into your design and build rules. It's attention to detail and making sure everyone understands the rules and follows them. When you say "I'm building" this can mean a spectrum from "I am really paying a builder to build it for me" to "I am building it all myself". Where are you on this scale? In our case, we used a specialist sub for the slab and TF, another for the fenestration, and a good local builder for all of the ground-works and stone skin. We also used a couple of his regular and recommended tradesmen for electrics, tiling, slate roof and plaster boarding. I also got a local architect technician to do the plans for the planning application for a few £K. Other than that we did the overall design, project management, procurement, quality assurance, and various trades like plumbing, woodwork, MVHR, CH, so pretty much all internal second fit; also planning and BCont docs and sign off. TBH neither Jan or I realised just how much work this would really entail, and we were exhausted by the time we moved in. Still 8 years later, and we live in a pretty maintenance free house with pretty much no post move in problems or things needing fixing. We have a high quality house and saved a lot on our build costs by doing a lot of the attention-to-detail stuff ourselves. One Q I would ask: Why so much glass? It costs a lot more than TF/blockwork and dumps heat like crazy. I know that it can occasionally help you connect to a stunning view, but if you are overlooking the street or neighbours, then do you really want to connect to them or have them looking into you private space? There's a 1970s/80s estate close to us where the architects loved having full 2-storey wall to ceiling window panels. Maybe 95% of the houses have since bricked in / insulated clad the bottom halves and fitted conventional 2G/3G windows instead. Architects might love it, but IMO occupants usually end up hating it.
-
Just to support what @torre says, we split our garden and did our new build on the bottom half of our garden. We were chatting to the estate agent who was handling the sale of our old farmhouse and he was quite interested in what we were doing, and gave us this piece of advice: "If you are ever thinking about doing a loft conversion, then the best time to do it is when you build the house: this works out far cheaper in the end and involves less disruption." That one aside was just so valuable: we raised the pitch of the roof from 40° to 45° and put in a warm loft during the build. This increased the effective size of our house by maybe 35% for very little extra build costs. My son has his bedsit on the loft floor now. We have an MBC (passive class) TF, but the builder (who did all of the ground works and stone skin) showed us around a couple of his own self-builds. In one case on the Planning Application it was "two storey", but he had a huge walk-in cupboard on the landing which had a loft ladder to a huge warm loft that was already built with roof lights and to code for conversion to living space. His reasoning was that since his application was for a two storey house, then he would get it signed off as that. This also avoided all of the costs of second-fit to the loft and hoisting the sales price. His intended buyer was going to wait a few years and then put in a planning application to convert the loft to living space. The Regs for conversion are slightly more relaxed than new build, but the way the house was laid out it was already fully compliant: it was just a matter of installing the 2nd flight of stairs instead of the cupboard and doing the 2nd-fit in the loft. You could consider either of these options to future proof your build so you could add the extra living space if and when you need it.
-
@Sparrowhawk, I'll add you as soon as I've those creds, ditto you @MikeSharp01 We do have an issue about where we store all of our secret stuff like creds than is excluded from our public repos. Maybe it's worth rolling it all up into an encrypted 7z file and putting this on our cloud server. That way we only need to share one password.
-
I think that I've worked out what is going on. The GSE property was set up years ago when HTTP was our default and /ipb/ was in the URL. I've just added https://forum.buildhub.org.uk/ to my GSE account. If you WhatApp me your Google creds, then I'll add you in Users and Permissions for this site.
-
@Sparrowhawk, methinks this is your forte rather than mine. Care to take a look and analyse the Google Search Console. Thanks It might be still worth adding rule to remove the gash /ipb from the URL. IIRC in the very early days the DocRoot didn't include the ipb directory so the rewrites added it, but on some VPS move we just made the DocumentRoot /var/www/ipb (see service/apache2/conf/extra/ssl.conf). This predates the move to Docker since the change isn't in the git logs.
-
I have made the ACP change and sitemap.php seems to be giving the correct URLs now. So let's see if Google picks this up. The change that I added to robots.txt was to add the sitemap directive. Before that google was just indexing from the homepage.
-
I've found it. The sitemap.php module is adding an extra /ipb in the forum uri's which gets snotted up in our URIs, e.g. https://forum.buildhub.org.uk//ipb/sitemap.php?file=sitemap_content_forums_Topic_21 instead of: https://forum.buildhub.org.uk/sitemap.php?file=sitemap_content_forums_Topic_21 Rather than change the sitemap module, it's probably easier just to add a rewrite rule to remove the extraneous /ipb. That way I don't need to mode the ICsuite code There's an ACP option one the SEO tab to fix this. 🙂 @Liam Jones thanks again for the heads up.