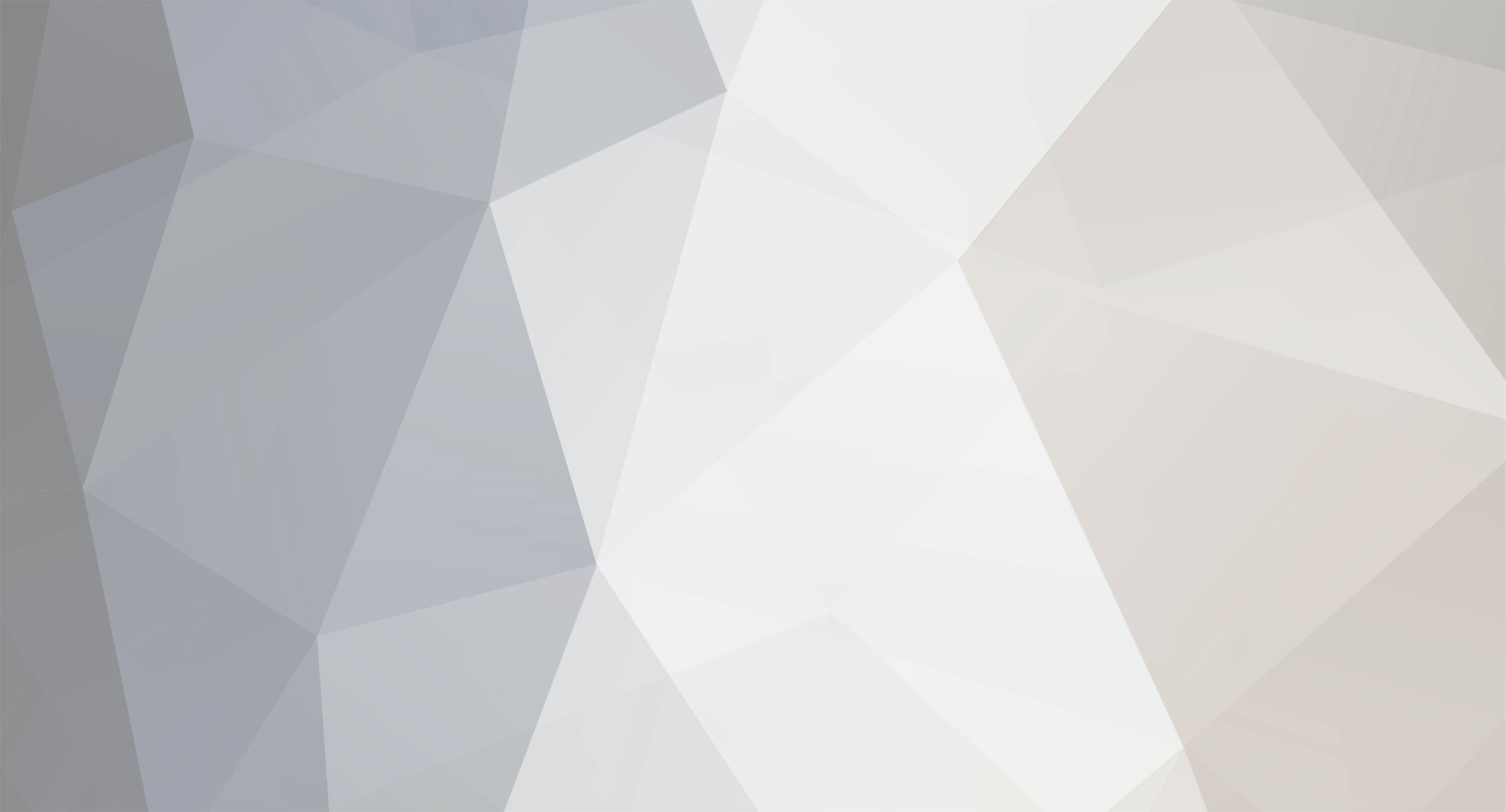
jamieled
Members-
Posts
639 -
Joined
-
Last visited
-
Days Won
1
Everything posted by jamieled
-
Our tf was built from JJI's. Get a copy of the James Jones technical guide. It details the connections. Where reinforcement was needed they were packed with osb and then nailed together. At right angles, such as window openings they were nailed like normal timber.
- 26 replies
-
- timberframe
- i-beam
-
(and 2 more)
Tagged with:
-
As above. Scottish Water have two accredited labs - one in Inverness and one in Edinburgh. Contact them here: Logistics Services - Scottish Water As them to give you a quote for sample analysis for potable water. If you're either not clear on how/what to test for, then there are companies who will sample, get it tested (probably by SW) and then interpret it for you.
-
It might depend if they are truly penalty clauses or whether they are liquidated damages (sometimes the terms are used interchangeably despite the difference). While there has been a tightening up of the enforceability of penalty clauses, there is still a strong presumption that if both parties are properly advised and of a similar standing, they are best placed to agree on what a reasonable penalty amounts to. It can be challenged if the penalty amount is out of all proportion to the losses incurred, but these losses can include some less obvious aspects such as reputational damage.
-
Private BC / Habitation forcing final sign off
jamieled replied to ellieh89's topic in Building Regulations
Can you buy the materials for the outstanding works soon? That way they can be included in your VAT reclaim even if not fully built? -
Solar - Where to start?
jamieled replied to DazRave's topic in Energy Efficient & Sustainable Design Concepts
Our insurers were not at all bothered - I ticked a box that noted we had solar panels, but they didn't ask about MCS. Haven't sold it, so I can't comment on any problems related to that. But there is no legal requirement to have an MCS install and there are a lot of people without such certification, so it's difficult to believe it could ever stop a house sale. -
All Water Companies (and SW are no exception) tend to be pretty careful about the specification and checking of new connections to ensure their network is not affected. If your connection and plumbing is to their standard then hopefully just a little paperwork? In the worst case they may disconnect the entire connection until any remedial work is done, to prevent any impact on their operations or customers and then take enforcement action.
-
I was under the impression that perimeter, french drains are a standard detail for all insulated raft type foundations, partly to reduce the risk that the angular gravel that the foundation sits on doesn't become waterlogged.
-
The way you describe the problem suggests the quantity of water must be quite significant - you could only get 'sloshing' noises if there's some movement/flow, and a reasonable volume of water. While there may be some defects, I'd struggle to believe the problem is with the areas you highlight in the photo. A higher water table might explain it, so the idea to dig a small investigation trench seems a good one. Have you checked to make sure it's not related to a problem with the downpipes - either a poor joint or misdirected gully?
-
Floating sludge increase in treatment plant
jamieled replied to Crunchynut's topic in Waste & Sewerage
I have a vortex 6 and yes, have similar observations to the OP. Had more severe sludge problems starting around this time in the last two years but never really able to figure out why. -
House is Too Airtight
jamieled replied to Newlands Ian's topic in General Self Build & DIY Discussion
An airtight test is meant to test uncontrolled leakage, hence why vents are taped for tests. -
Yeah I don't think anything AICO produce looks like it fits the bill. To the OP this may also be of use: Building standards - Carbon dioxide monitors standard 3.14: letter to local authority verifiers - 22 January 2018 - gov.scot (www.gov.scot)
-
It's not so much a detector (as with Carbon Monoxide) as just a sensor with some kind of visual indicator of the CO2 level. I'm pretty sure they can't be ceiling mounted, because the occupants need to be able to look at them and see what they're telling you (not that you probably will in practice, but hey ho). Second the comments above. Ours is a Deta.
-
Quite a few modern stoves are 'convection' type stoves, so, as mentioned above they can be sited closer to walls. Ours is, and irrespective of safety distances you can put your hand pretty close to the stove metal - they don't radiate much heat out the sides/back. More traditional stoves that radiate heat probably can't do this. We have ours around 150mm from fire resistant plasterboard (the pink stuff) with no obvious signs of it popping.
-
using cement board as external cladding
jamieled replied to Tom's topic in General Self Build & DIY Discussion
We have an EPS passive raft type of foundation from AFT. It comes with a cement board type product bonded to the EPS, it looks a bit like block work when installed. -
Virtual machine to overcome Loopcad trial period.
jamieled replied to Post and beam's topic in Boffin's Corner
I remember having a similar problem. Can you not just download the .iso directly to the VM? Pretty sure that's how I did it. -
I'm probably not well placed to answer - I chose not to use any form of contract for our self build (with the exception of some T&C's for materials supply and one or two specialist contractors for specific jobs like insulation). I was happy with this at the time but I can easily see how it would not always be appropriate. JCT seems the most common option for self build from what I've read. In some ways NEC fits the bill for a contract that 'communicates expectations' - it was designed (and is used) as much as a project management tool as well as a contract (this is based on my experience of its use outside of self-build situations - commercial engineering). It's downsides are that it requires quite a a bit of time to 'manage' the contract which is probably where it varies from a lot of self build contracts that are written and then only ever used if there's a problem requiring the contract as a reference for what to do. This works OK on large-ish jobs where the contract management fee is proportionately small compared to the job. The second aspect is that both parties to the contract need a really good understanding of it and someone on each side who can administer it. If you're chosen contractor/builder has this skillset then it might be a goer, but as it's not a common form of self-build contract then this might be a struggle? That's probably not much help though, hopefully some more contractually-experienced self-builders will be along soon!
-
Where is your PV inverter? Reluctant to put them in house...
jamieled replied to Carrerahill's topic in Photovoltaics (PV)
We have panels mounted on a timber frame. Inverter mounted to the back of that. Crude wee wood canopy over the top so it's mostly open but protected from the prevailing weather. Has worked fine. -
We have a slightly similar setup and play about a bit with trying to maximise our PV use. We have a 210l oso tank with two 3kw immersions and an eddi connected to 3.6kw of PV. Family of 4. We rarely run out of hot water. In the middle of winter we tend to assume the PV does nothing and just use the immersion (using the eddi boost timer to programme on/off). At this time of year we'll have it set to boost for a couple of hours later on after the sun goes down. Soon we'll switch off the boost altogether and just let the PV diversion do its work. On the odd occasion of prolonged grey weather in summer it might need a manual boost, but I think it's a small price to pay for the saving.
-
I replaced one of the threshold seals and one of the door frame seals. In both cases I took the whole thing out and replaced it (even though only a wee bit was damaged).
-
I had this a few weeks back. I think nearly all the threshold seals will pull out, but they do need a bit of elbow grease, try getting a screwdriver underneath them or something. Once it's out, you know what the profile is, as it can be hard to tell before then. I used the website linked to above to get a replacement. Pushing the new seal back in is just as tricky!
-
The science behind sewage treatment plants
jamieled replied to Crunchynut's topic in Waste & Sewerage
I have it set to run for about 5 minutes every hour. Could you describe what your SSR looks like when it's working well (accepting what works well for you may not necessarily work for me)? Is there a lot of overspill? -
Fitting insect mesh with board on board cladding
jamieled replied to eandg's topic in General Joinery
I can tell you how we did it, though I'm not going to claim it's the best way. We cut small strips of mesh equal to the width of the gap. Staple one end to the underneath board, then bend the other end round so it forms a sort of roll or cylinder. When the top board gets placed over this it compressed it a bit to fill the gap. Pretty faffy, but we couldn't think of an alternative. It seems to work so far. -
MVHR is Largely Bogus
jamieled replied to DavidHughes's topic in Mechanical Ventilation with Heat Recovery (MVHR)
Indeed. Ours was lumped in with our other electrical costs, but I believe there were very few on the market at the time and given they were mandated there might have been a bit of price creep! They seem very sensitive. Ideally I would like one with a logging function, otherwise unless you hold your breath while looking at it, the values spike. -
@eandg in general yes, because we had a 'typical' overlap, it was generally possible to avoid the situation you describe. However, I reckon there are probably a few areas where we reduced the board spacing which resulted in nailing through the underboards - if you don't then the surface nails need to be really close together which risks cupping the outer board.