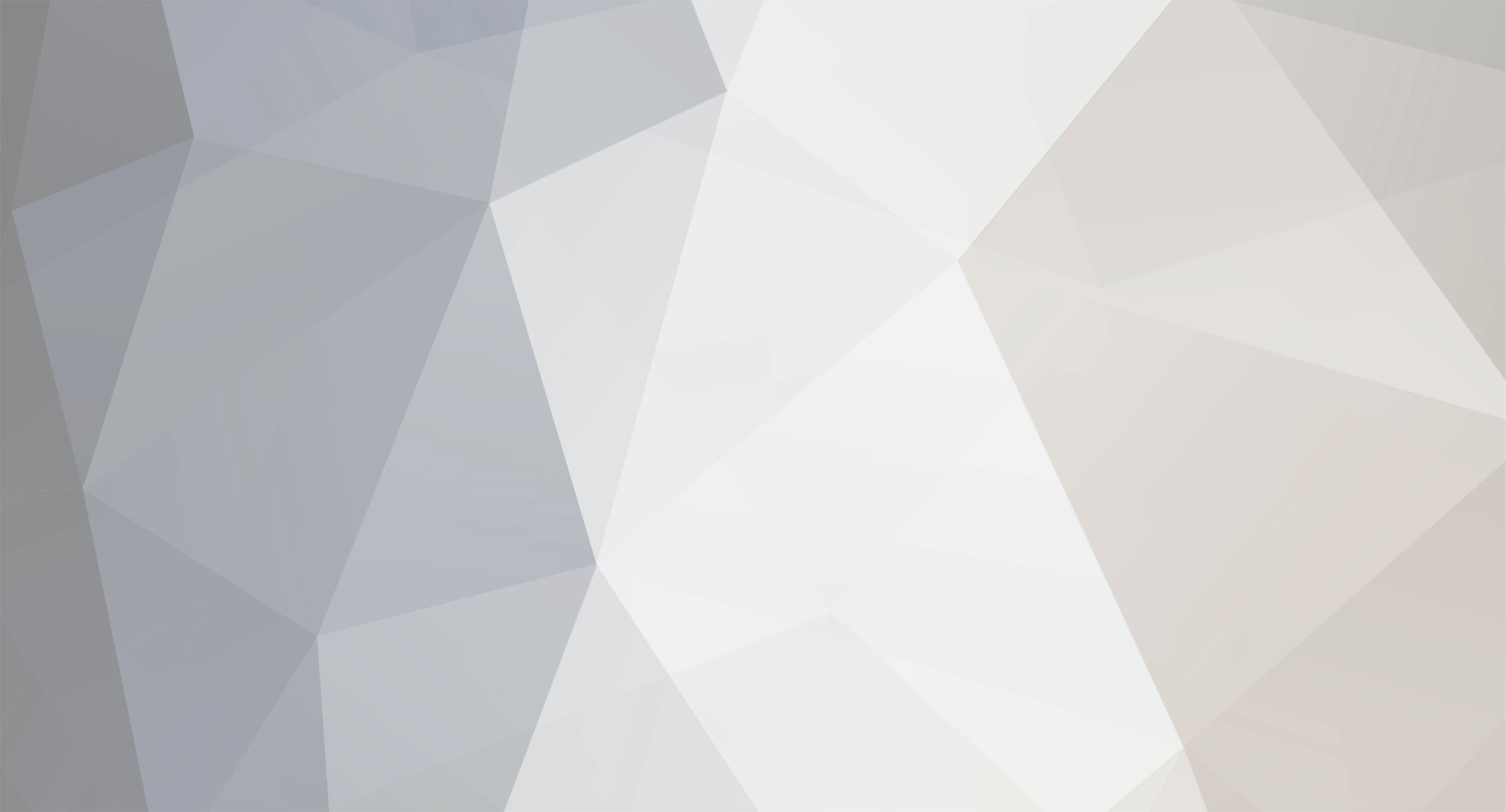
Jimbo37
Members-
Posts
165 -
Joined
-
Last visited
Everything posted by Jimbo37
-
Asbestos disposal VAT
Jimbo37 replied to Jimbo37's topic in Self Build VAT, Community Infrastructure Levy (CIL), S106 & Tax
Thanks @Conor -
Hi To my knowledge, things like overalls and masks etc are not VAT DIY reclaimable, in the regular circumstance - can these things be claimed, if they are single use, eg disposable overalls for asbestos removal? Also, can you claim for stuff you did before the PP was granted - e.g. securing the site outlays, fence etc? TIA
-
Thanks @joe90
- 3 replies
-
- settlement cracks
- paint
-
(and 1 more)
Tagged with:
-
Anyone, please?
- 3 replies
-
- settlement cracks
- paint
-
(and 1 more)
Tagged with:
-
Hi all, a bit of a steer, please I had a block cavity house built by a contractor who did everything up to, plastering (ie excluding kitchen, painting and other latter jobs) and I'm in since June. Generally all is good, thankfully, but I do have a lot of minor cracks that mainly appear around windows and doors, strecting out to floor or ceiling. I have it on good advice that there are minor, basically drying out and settlement cracks - so I am not worried - and to drop back after 12/18 months to fill and paint them. My question - is that up to me to do, the builder or the painter (thats me anyhow)? Thanks, James
- 3 replies
-
- settlement cracks
- paint
-
(and 1 more)
Tagged with:
-
Hi BuildHub'rs I'm in the latter stages of a 2 story build with a joist and osb first floor. I have installed hushpanel 28 floating soundproof on top of osb, which seems very good. Problem is, my flue comes up internally from main living space through corner of master bedroom through 400x400mm hole with heat ventillation grill, bypassing the soundproof. All is not lost, as I can box in flue in upper floor. What product/ board should I use for good acoustic performance, please?
-
- 4 replies
-
- window cills
- window sills
-
(and 1 more)
Tagged with:
-
Thanks @Mr Punter - should I have expected the DPC to have prevented my inner cills getting, before the mastic was increased?
- 4 replies
-
- window cills
- window sills
-
(and 1 more)
Tagged with:
-
Hi Self Builders I need a steer, please I have a new built masonry house, with a cavity and standard DPC window details. I had wet patches low down on the internal reveal - a wet quadrant from junction of window cill and window frame. The builder resolved it with additional mastic around the frame on the outside, and it seems dry now. My questions are - shouldn't the DPC have directed the wet out, before it got to inner leaf? - is mastic in this case a robust solution, or will it need replaced, maybe every 5 years?
- 4 replies
-
- window cills
- window sills
-
(and 1 more)
Tagged with:
-
@ADLIan Just passed this to my architect, as I was concerned that my insulated upstands were not insulated at the top. She didnt understand the reasoning (this edge of the insulation is facing up/cold) - do you have any references or further comment you can give. TIA
-
Oh dear! Can the flue squeeze in here?
Jimbo37 replied to Jimbo37's topic in Stoves, Fires & Fireplaces
Mmh, the flue guy installed this using lead flashing and loosely packed insulation wool, but there is condensation falling from bottom of lead. Anyone got a good understanding of how the detail should be (warm roof, insulated box) - I'm guessing solid insulation with vapour control, maybe? Also, that collar is siliconed - is that OK? Im a tiny bit nervous that the lead does not stretch down far enough. Ooh, I have to stop looking!!- 25 replies
-
@Andehh see pics above, and this one which was taken for unrelated issue (unprotected timbers) but shows head stepped dpc
-
Ive spent a bit of time studying these today 1 - I noticed that there are weep hole covers missing, could that be the source? 2 - I see cills run under frame from outside to inside, could water be getting blown back through? 3 - Mastic is good, but not perfect everywhere (could this be the cause, or is this really essential to weather proofing)
-
I'll look for pics, but it looked right. Step dpc in head, and strip of dpc from inner leaf down outer leg of frames Edit: see 1 pic up. Unfortunately I don't have much better pic
-
There is a 50mm runoff on patio, does that deal with issue soakaway would deal with? No render stop. The patch you see is a problem with paint, as it rained before it dried
-
Oh dear, Im worried - please put my mind at ease I have a 'regular' block and s&c render house, with a flat roof in the final stages of build. I finally had the windows sealed (rubber between frame and glass and the mastic between the s&c and frame) a few days ago. Todays rain has shown a problem on 14 of the 18 door/window openings - a wet patch at the bottom of the inner reveal (always on one side, just) - see pic. (There is S&C behind the cladding). I have noticed this previously, but the builder felt it was because the rubber on the windows was missing - obvs, Ill speak with him in the morning. What is most likely to be going on?
-
This is what I had - after comments, advice and suggestions hare and a chat with my architect, I have allowed it to pass - and keeping a close eye on it for (no) cracks etc. Thanks @all
-
Agreed @saveasteading, but I'm unsure if I'll follow this through as my main concern is the quality of what I have and the general consensus is that its fine. To go for cost rebate, I'd have to be 100% sure of depths in middle of floor, which presumably would call for a couple of drill holes, which is a taking from quality and would rankle the builder if I'm wrong - on balance, I think it's best to move on.
-
Looks very good
-
LVT, click vinyl or lino. A tad faffy on that 😳
-
Calcium sulphate
-
@JohnMo im nervous, as there is ufh
-
Hi all. The architect spec'd to install 50mm of screed. Thing is, I think only 40mm was actually put in. I think this coz I marked the walls before the screed went in, and all suggest 40mm. In addition, 40mm is apparent around doors etc. I'm mindful that the centre of the floor could be deeper - any way of checking? 🤔
-
Chipboard or Ply, 18mm or 22mm for Bathroom LVT
Jimbo37 replied to Tetrarch's topic in Floor Structures
My glued/interlocked chipboard has 8mm soundproofing mat underneath, that will compress to about 4mm as you walk on it. Room sizes are about 3m to 4m. I want to lay LVT, glued or click, but wonder if that that is risky with the 4mm compression - any thoughts?