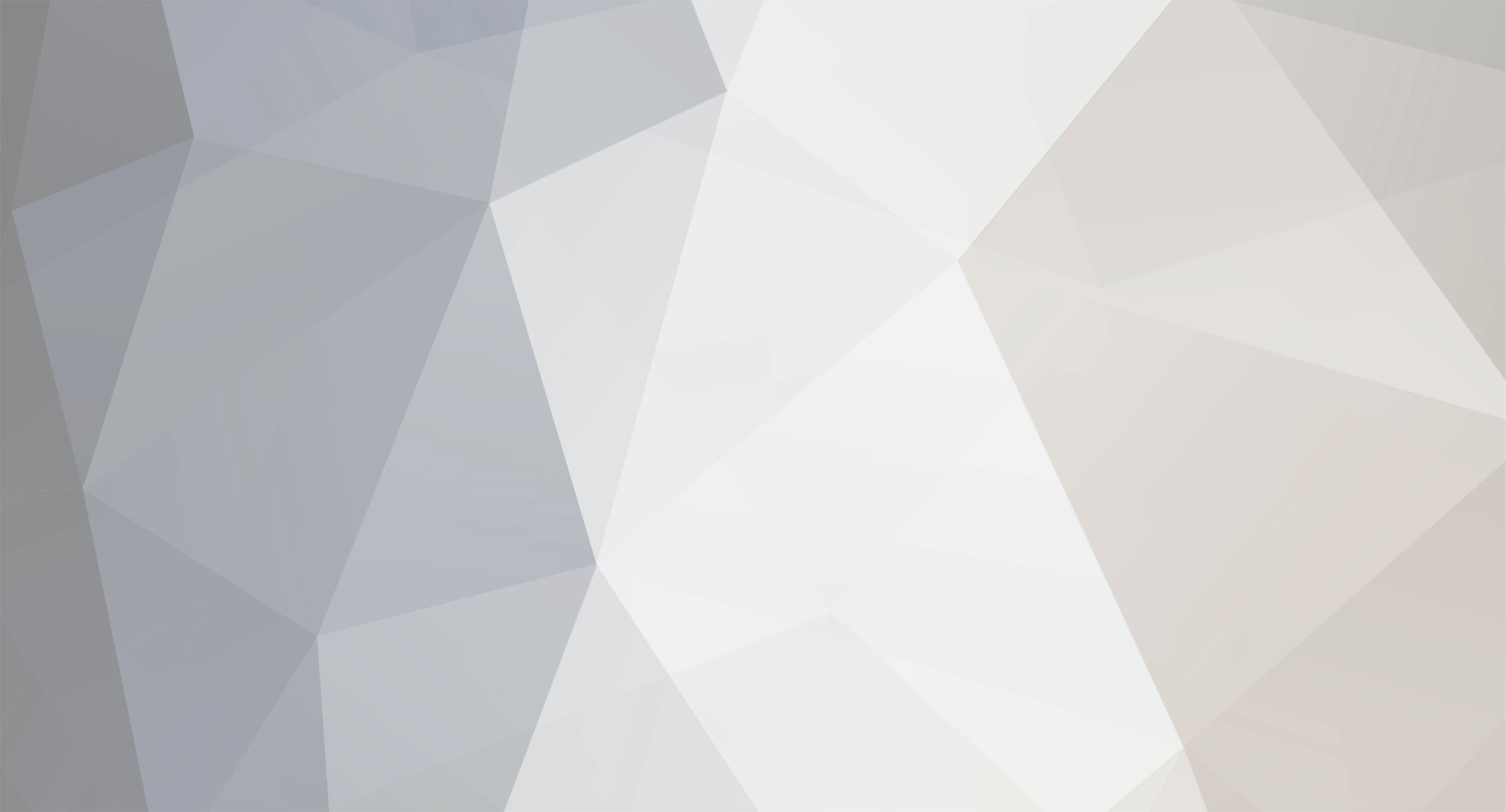
Tetrarch
Members-
Posts
144 -
Joined
-
Last visited
Personal Information
-
Location
Hartley
Recent Profile Visitors
The recent visitors block is disabled and is not being shown to other users.
Tetrarch's Achievements

Regular Member (4/5)
32
Reputation
-
Removing soil through the house - do you have a direct line through the house, navigating through and around door ways will be the real challenge. In my experience, wheelbarrows are difficult to control consistently when loaded, I found a four-wheeled pull trolley easier to manage although a soil conveyor would be optimal - hence the first question......... Regards Tet
-
Thank you for the link. It looks as though I should have spent longer on the FH Brundle website.......there is a specific pre-made (but MUCH more expensive) panneled version called zenturo available: https://www.fhbrundle.co.uk/fencing-and-security/super-gabion-fencing https://www.wireland.gr/en/products/steel-wire/rockfall-mesh/item/toixos-apo-sirmatokivotia-zenturo The sizing on this is bigger mesh than mine but it comes up in maximum two metre panels Regards Tet
-
I intend to use a drainpipe to insert stones slowly rather than dropping from a height It's just a stone wall, (plus design proof of concept for a more substantial curved retaining wall planned for the drive). I started with the idea of a wall that was 9" at one end and 6" at the other. It's only when offering up the mesh that I realised that this would be costly Agree with both these. I have plenty of hooks. As it's decorative rather than structural then the thinner it is the less it will bulge. I have some 1" box-section aluminium that I could use as guide bars to give the structure some support Do you guys think that a 4" thickness would be suitable - ultimately if it doesn't quite work then I can always make it thicker Regards Tet
-
I've created a space that I want to fill with a gabion wall. I've chosen 1" x 1" x 10g galvanised wire mesh sheets and they are fixed at the ends and to the bottom. I have a number of gabion ties (double-ended hooks) to hold the walls together before filling. The "filling" itself will be ~30mm pebbles of some sort. The overall size is approximately 3.1m x 1.7m. The post at the right hand end is 6" across and I have a 9" brick wall at the other My question is how thick should I make the wall? The thicker it is the heavier it will be, the more the pebbles will cost and the more likely it will to bow the gabion itself The thinner it is the less stable it will be Any advice welcome, pics below Regards Tet
-
With the right kind of standoffs you secure the standoffs to the beam and then fit the glass to the standoffs in an entirely separate process. I found this on youtube to give you an idea: Just to note I have NOT installed these, but just came across this when doing my reseaach Regards Tet
-
You don't need these. For a standoff in a glulam (is there a better screw substrate?) you could use a regular coach screws - the biggest that you can safely insert Regards Tet
-
Things masively depend on the glulam beam construction and what's behind it but it looks like you have two options: Either some HD through bolts like these: https://www.fixingswarehouse.co.uk/products/toggler-snaptoggle-heavy-duty-toggle-bolts-bm10-25pk Or some M10/12 screws straight into the glulam - are there any load recommendations Regards Tet
-
I can't recommend FH Brundle highly enough. From order to delivery their people are absolutely top-notch, the prices are extremely keen and they keep you very well informed I wanted the standouts but didn't have enough vertical space on the return to make it work as you need (IIRC) 100mm below the low standout in the glass. Getting it exactly straight was a process but using their inserts and four post-it notes (a new construction unit) made it perfectly vertical Regards Tet
-
Aluminium box gutter in non standard ral colour
Tetrarch replied to G and J's topic in Building Materials
I looked at Aluflow. I'm going to make a recommendation but with one HUGE caveat www.clearamber.com aluflow deepflow gutterring is superb. Really strong and looks fantastic. Using the deepflow means that I haven't had to introduce any fall and they have no problem shifting water in the heaviest rain. I would unreservedly recommend if it wasn't for one detail...... The corners and fittings are cast and the main pipes must be extruded. I have found that the cast parts finish has gone matt over time. To their credit clearamber have offered to replace the faulty parts but 60% are already in-situ and I am loathe to change them out as they are screwed and siliconed. I may keep the roof-line ones as-are and just change the first floor, but I am still weighing my options Regards Tet -
But he'd lose his floor space..... I was wondering whether you could take the walls in at the "shoulders", where the wall creases but then feather it so the floor remains unchanged Regards Tet
-
This instruction from the council will oblige you to sacrifice your loft room as one of your lettable spaces How much extra PIR do you actually need? Its a sloping roof - can you not just add thin PIR on the sides and then a thicker portion right at the apex to achieve what you need? Regards Tet
-
Welcome - from a fellow Kent dweller (Kentish Man in my case) This place is an incredible resource, invaluable advice and opinion - I have learnt so much, and continue to do so Much of your plans will depend on your local authority - if it's Sevenoaks then buckle-in it's going to be painful All things are possible if you have adequate budget, patience and a hide of leather Very best of luck Regards Tet
-
Flat Roof with Parapet detail - correct fall
Tetrarch replied to Ay8452's topic in Roofing, Tiling & Slating
If you're cricketing then you might need behind your rooflight to divert the pooling that will inevitably occur there Regards Tet