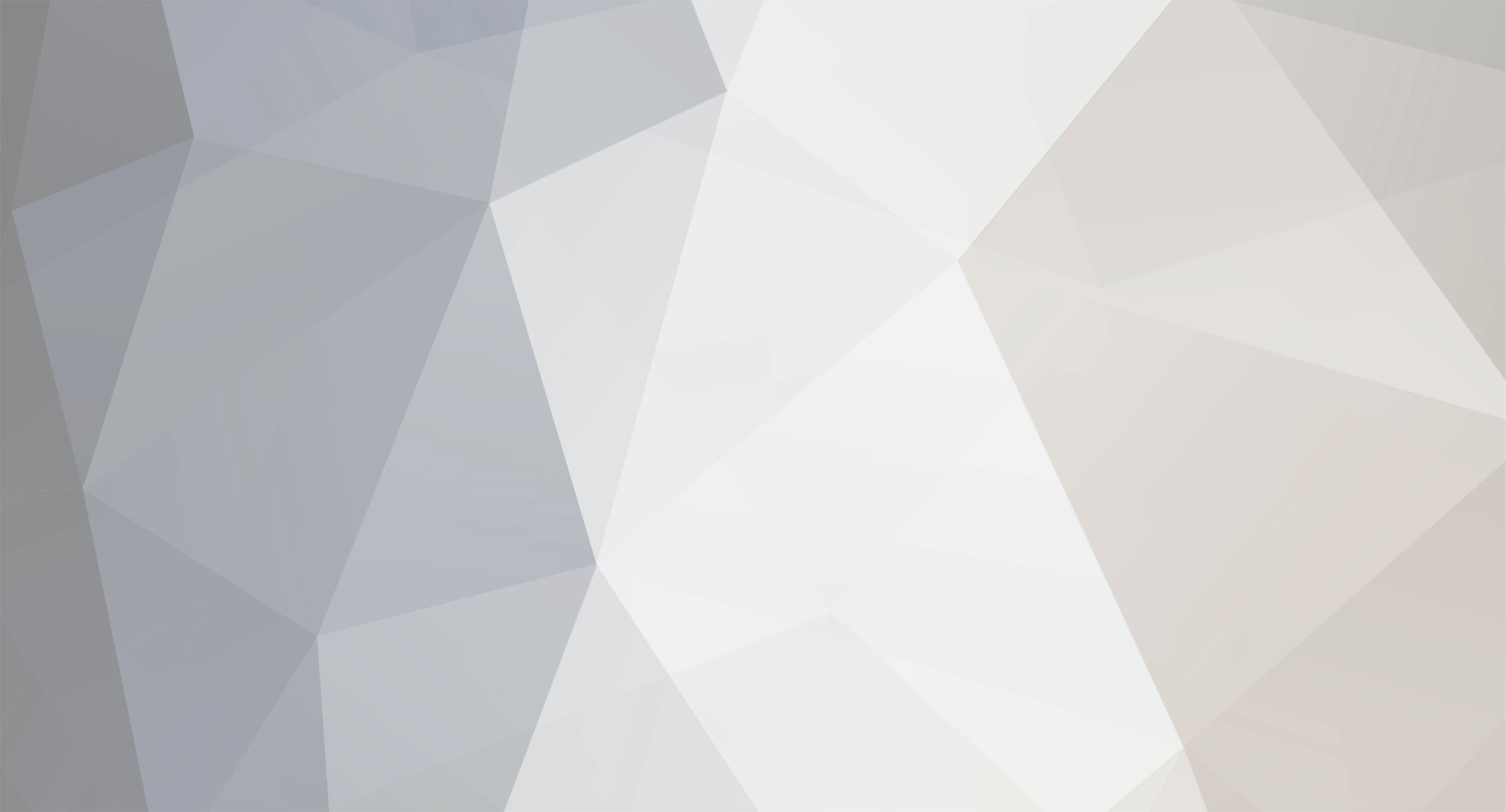
Carrerahill
Members-
Posts
2122 -
Joined
-
Last visited
-
Days Won
10
Everything posted by Carrerahill
-
Risk is still there, when doing a lightning protection system risk assessment, you review 500m either side of a buried LV cable - further away from the sub-station the bigger the risk as the collection area grows, 1000m x 1m for every meter your cable travels, so 1000m² per m travelled, a ground strike within 500m either way will probably affect the cable, worse if they are old metal cables as the strike can send a surge flying up the earth nicely too.
-
Remote DNO Kiosk, need cable to consumer unit indoors
Carrerahill replied to Post and beam's topic in Power Circuits
25mm² XLPE SWA -
You could take the 10mm² into a junction box, use high quality connectors, then continue on 6mm² onto the EV charger. If you need to feed a socket, you could, take another cable out the connection blocks and into the fused connection unit, do it within 3m, then you can use a smaller cable cross section here so you can get it into your FCU (under BS7671 434.2.1) and drop it into a fused connection unit, de-rate to 13A and feed your socket from that. There are other ways too, including a small din-rail module and some MCB's locally, but it depends on your situation, space etc. What run is your 10mm² cable and what size MCB is protecting it? I'd be making sure it is a 40A for the 6mm² cable.
-
Welcome, not far from you.
-
Sharing Fee Proposal with other Architect
Carrerahill replied to flanagaj's topic in Surveyors & Architects
Don't ask us, read the fee proposal, ours states: "This document is for the exclusive use of XXX and should not be used in whole or in part by any third parties without the express written permission of XXX" In other words, this fee is private, between you and I. I would need to really sit down with one of the 7k quotes and the 15k quote and understand to what stage are they designing, is there a site stage, have they allowed meetings, Teams and Site, what is included, what is excluded, does the 15k include EPC's, statutory application costs, with Mr 15K do variations and hold your hand, will Mr. 7K bill you another 10K in variations and fees? Does Mr 15K perhaps include M&E consultancy, other consultants? -
I tried to do something like this last year when I did our PV install, in the end I pretty much just found the highest output panels from good manufacturers I wanted to use and within a price range that kept the £/W ratio reasonable and made a little table - I came up with about 6 panels I actually wanted to use. There were, at the time, some panels about 575W but being new to the market, means costs were £££/W and they were bigger, much bigger, which meant I could actually fit less peak power on my roof as the sizes were awkward to tie in around the Velux's. What I learned as well, was that you can plan and plan and plan, but when it comes to it, you more or less have an area you can utilise, stick with decent power density and you will more or less get the same same power be it using 10 500W panels or 11 450W panels but the 450W panels are probably a bit smaller and might suit your roof better. If you have a huge area, lots of space, no obstructions then just get as many high power density panels onto your roof as you can.
-
Urgent assistance: Constructing Flat roof stuck with a problem
Carrerahill replied to Hemant's topic in Flat Roofs
My thoughts are: 1. Replace the window above with a smaller one and brick up to new sill height. or 2. Redesign the roof so the insulation is within the depth of the steel and board out just above steels for roof deck. Even at that, flashing detail won't be 100% but can work because you can use the sill in your favour to get a good seal to the flashing. You are meant to have 150mm upstand then dressed into brick, but in fairness, I have 75mm flashing upstand which I dressed in under windowsills. Who made this mistake?- 8 replies
-
- 1
-
-
- flat roof
- roof design
-
(and 1 more)
Tagged with:
-
We have this, just bought the bits and installed it, roofer helped with the PV panel bit, although I actually installed the rails and panels, I wired it all, installed it all, commissioned it all. I didn't need or want the system MCS certified and as I was 100% self consuming I was not interested in any pay in. I just fired off a G98 to the DNO, I think. A friend who happens to be an electrician came and helped as he wanted to learn how to do it (I had already done PV on the shed and garage) - so I taught him how to do it all, from how to design the system to crimp up MC4 connectors etc. and he wrote up a minor works certificate. Brilliant isn't it! (facepalm!).
-
What model is this oil pump - have a guess
Carrerahill replied to cwr's topic in Boilers & Hot Water Tanks
Why do you need to replace it, what part of it has failed? I only ask as I repaired a drive shaft/gear spline/key on one of these not long ago, it was pulsing the oil pressure and it turned out to be the gear slipping on the drive shaft. -
Simply, it is not ideal. The issue you have is your ASHP will pull from say L1, however your PV will generate on L1/L2/L3 - any benefit of self consumption of L2/L3 generated power will be lost where house load is low as you will push that to grid, i.e. export getting pathetic SEG payment rather than benefit of use which, financially, far outweighs SEG payment. Also, phase balancing is all very well in theory, in that your electrician may load L2 and L3 with more house load than L1, in practise if your house loads are low, all electric loads more or less off and ASHP going full pelt you now have a nice imbalance, not really your issue, more the DNO/local transformer, but not ideal - can cause neutral issues.
-
Electric towel warmers, how to control?
Carrerahill replied to crispy_wafer's topic in Electrics - Other
Run a dedicated towel rail circuit to the pair of them and put them on a timer, immersion heater timers work well, or something a little more fancy, and just set a schedule, that is the simplest. Or you might want to split the circuit, i.e. if one is in a infrequently used bathroom you might not want it on at all unless you have guests? In which cause schedule the main bathroom towel rail to suit your typical daily schedule and put the guest bathroom on a simple on/off switch which can be switched on while they visit etc. I've also seen them linked to PIR sensors in the bedroom/hallway - the idea being that if people are about then the chances are they will use the bathroom at some point, that then automatically adjusts for when you are away for the weekend etc. -
I assume he has water, just not a large enough supply to support a fire hydrant so he needs upstream network reinforcements, at his cost!
-
No idea, almost certainly not (something my mechanical colleagues would deal with) but that is the rate we used to calc the tank size, in other words we based the tank on having an infill rate so low it didn't really count and it makes the tank essentially a standalone water source for suppression. The structural engineer wasn't too pleased we added 21 tons to the structure!
-
5692m² The tank size was calculated based on a minimal infill water of 0.7l/s (nothing), that tank also includes the un-useable volume.
-
Design it, build it, put it to use and don't worry about the DNO, just don't take the p***. Especially if you won't allow any export of your battery power. I have said it once and I will say it again, there is no DNO police.
-
Is this purely for fire extinguishing in your build? Without knowing more details I may be going off on a tangent, however, if for fire suppression in your own home, then sprinkler tank? We are currently building a care home in a village, the water authority has said they cannot give us the flow rate for sprinkler tank makeup, so we are specifying a 21,000 litre tank, which meets the needs of the sprinkler system within a large 2 storey care home. Do you see where I am going with this? I will also say that as the water authority cannot give a decent enough supply to continually fill the tank during use, it clearly would not be able to support a hydrant, so if a care home full of elderly, potentially immobile residents can be served by tanked water, then why can't your house?
-
Nearby Piling, advice needed!
Carrerahill replied to Residential build's topic in General Structural Issues
I think I would find a friendly local structural engineer to pop out and see you, agree a cost for visit and a cost to record findings, but not necessarily present, at this stage. If anything happens you have the ability to have a before and after report detailing any structural, or other related damage. I would inform the main contractor immediately of the steps you have taken. You may also check your legal cover on your house insurance - they may help here because if your house falls down they won't be best pleased at having to cover the repairs! Photograph your home - have a means of proving things such as show a plumb line hanging adjacent to walls to prove plumb etc. (don't use a spirit level, the accuracy can be argued against easily). Submit these photos on the date taken to your SE and someone else, ideally a consultant or your insurance company or something (find someone who will agree just to receive them and file them so you can prove dates taken. -
When I exposed land drain on my build it was a flat tile with a U shaped tile laid over the top. Loads of infiltration possibilities!
-
Depends on the board, wet, install it tight, dried out, a nail width. Most of it is bloody soaking!
-
I would go sarking, make sure it is decent stuff, I have had some crappy circa 15mm stuff delivered and it was very knotty and scary to walk on! Finally got a delivery of decent 22x150mm.
-
If you do this, get a hybrid inverter with a AC input, this can be grid, or, as I plan, a generator for the worst winter days. I know of a chap not far from Glasgow who bought a plot with no power, SPEN wanted silly money, he went off-grid, he has PV, storage and a generator, he reckons he uses about 50litres of diesel a year max and it only kicks in during the worst winter days - as PV pane efficiency increases he expects to come off the generator once he renews one of his arrays in 5-6 years.
-
They are not really for this purpose but will do a grand job of this, get some intumescent putty pads and fit them to the backboxes. That will seal them up and fire rate your sockets!
-
Would some 160mm soil pipe be about the right size? I would keep it at least the same size or bigger and just sleeve a bit over, I think I would use your big rocks and some hardcore bound up with cement to make a sort of no fines concrete around the whole lot and reinforce the bank, as you are doing, around it.
-
If it was me, I would hire a diamond floor saw and cut a decent channel, dig out, lay conduits, waste pipes etc... plumb it all up, test it, replace concrete. I'd go for continuous runs of plastic pipe (although I hate it and won't use it) laid in conduit in such a way you can pull through new lengths if needed in the future. Allow spare conduits too. I'd put in some 63mm smooth bore twin-wall ducting for water pipe and power: https://skyplastics.co.uk/63-50mm-black-twinwall-electric-duct-x-50-metre.html