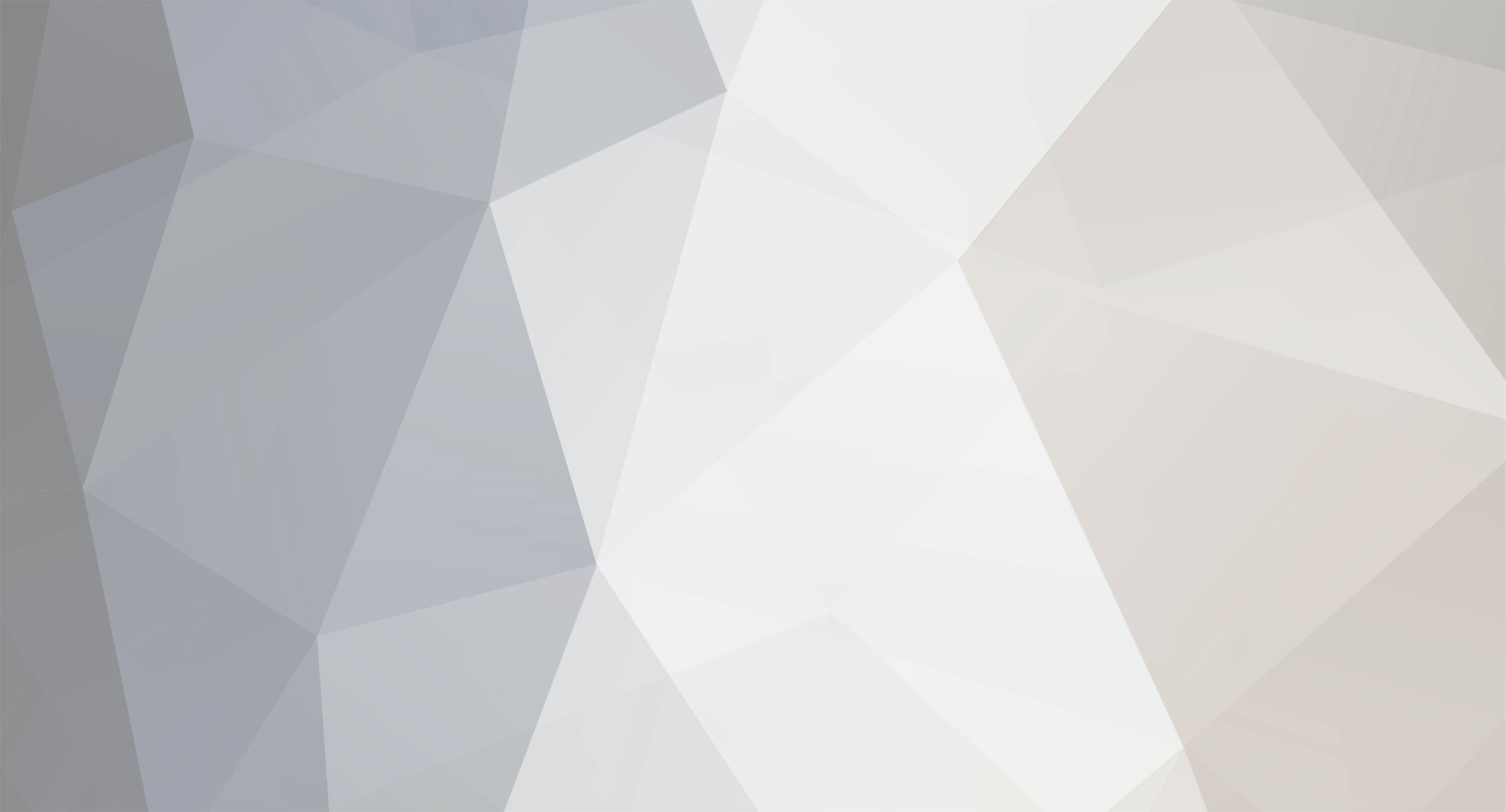
cwr
Members-
Posts
329 -
Joined
-
Last visited
Recent Profile Visitors
The recent visitors block is disabled and is not being shown to other users.
cwr's Achievements

Regular Member (4/5)
44
Reputation
-
Wasn't until I did this that I realised just green it had got in only 3 years!
-
Just report back, I looked for algon but our local place had patio magic so trued that. Did a test area and was very impressed with the results. 5l diluted as per the instructions applied with a weed sprayer did the whole house. The photo shows the test area after 3 days.
-
Hi folks I've couple of garden walls built from concrete block to render, and would like them to match the house. The house (also concrete block) I believe was done with the following, and appears to be a good job. Weberend aid Weberend MPR Weber PR310 Webersil TF There is a good bit of Weberend MPR left over, but I am wondering if the Weberend aid and PR310 are really necessary for an 800mm high garden wall? I guess a lot of folks would just sand/cement render and paint, but I have the MPR and want to match the house. Thanks
-
Thanks for the replies and suggestions. I had tried diluted bleach but it had no effect, it may have been too weak a mix though.
-
Hi folks Any recommendations for something to spray on render to get rid of green algae? It's a white thin coat Weber render. Plenty of trees near by so guess I'll be doing this every couple of years... Thanks
-
I'd guess that water sitting behind the wall is not great. Some info on this page may be useful if you've not already seen it. Scroll down a good bit to get to retaining walls. https://www.pavingexpert.com/featur03
-
I think I would go 'A', as I think it would suit the room shapes and also be continuous between rooms with no joins. But that's just my take, others may prefer other approaches. We had herringbone continuous through several rooms, aligned it centrally in the biggest room, and the rest were dictated by that. More than happy with it. Why don't you get a few boxes and lay some and play about with it?
-
Yes, but at cost. (I'm really watching the pennies now...) On the last stairs I did I bought lengths of planed whitewood and cut to length as I needed over 900mm, and then bought 900mm spindles for the landing. Wre v similar cost. The 'proper' spindles had a much better surface finish, edges better and less knots.
-
Hi folks, Could anyone suggest somewhere to get 41mm plain square stair spindles in northern ireland, that are 1100mm long? Primed or unprimed. Anywhere local I've tried only do 900mm long, and can't find any mainland GB suppliers that would send over to NI. Thanks
-
vent-axia sentinel wired remote
cwr replied to Ajm's topic in Mechanical Ventilation with Heat Recovery (MVHR)
I have had exactly the same issue. We have 2 vent axia's. On one the display was not great but worked, the other did not show anything. By swapping the controls over i was able to show the control was not the issue. I went back to the supplier who sent me a new main control pcb, having it swapped has helped. Its still the case though that neither are particularly impressive. Mine do not appear to have back lights, which would have been helpful. -
Practicalities of Static on site
cwr replied to Post and beam's topic in General Self Build & DIY Discussion
If you can get or build a small shelter or shed for the washing machine you'll likely be glad of it. It would take up valuable space and produce noise in a caravan. I can't think of a reason that 100ft would be a problem for water or electric, assuming the wires/pipes are suitable spec'd and installed. We were about 80m away, which was good. Wouldn't want to be really close, but depends on the site etc. Big lorries, diggers, things falling off scaffolding need to be considered. And if you have kids, that's another factor. -
Thinking about this again, and looking at the 'panels, battery, inverter, AC heating element' option. If I get four panels around 400w each, would this inverter be suitable? https://www.cityplumbing.co.uk/p/solax-power-x-1-1-0-7kw-single-phase-inverter-1-x-mppt-inc-dc-switch-x-1-0-7/p/628024 And what size of battery would be recommended? Bearing in mind the battery is only to smooth out, not be used as a storage device.
-
Ended up pretty much as per the drawing above, except with 100mm pir, and osb instead of ply. We also went for Rationel aluclad frames instead of pvc. Standard concrete cills, though might have been better with ones with a narrower part for the window to sit on.
-
Beefy ridge beam check and plan to reduce size
cwr replied to NandM's topic in RSJs, Lintels & Steelwork
Out of curiosity I asked my SE why he'd spec'd a UC for a horizontal beam and not a deeper lighter UB. He said due to torsional buckling. Slightly different situation as was supporting a wall, but no doubt you SE will have a justification for the choice. -
Getting house signed off - Northern Ireland
cwr replied to DG77's topic in General Self Build & DIY Discussion
+1 to what Declan and other responders have said. I got sign off a year ago (also in NI). About a week before we needed sign off I asked our BCO to come out and we walked around together, there were a few minor points which we then got sorted. Always found BC to be very helpful and willing to chat and give advice over the phone or to do a site visit. After all, their objective is to ensure a good quailty construction which is exactly the same as us self builders.