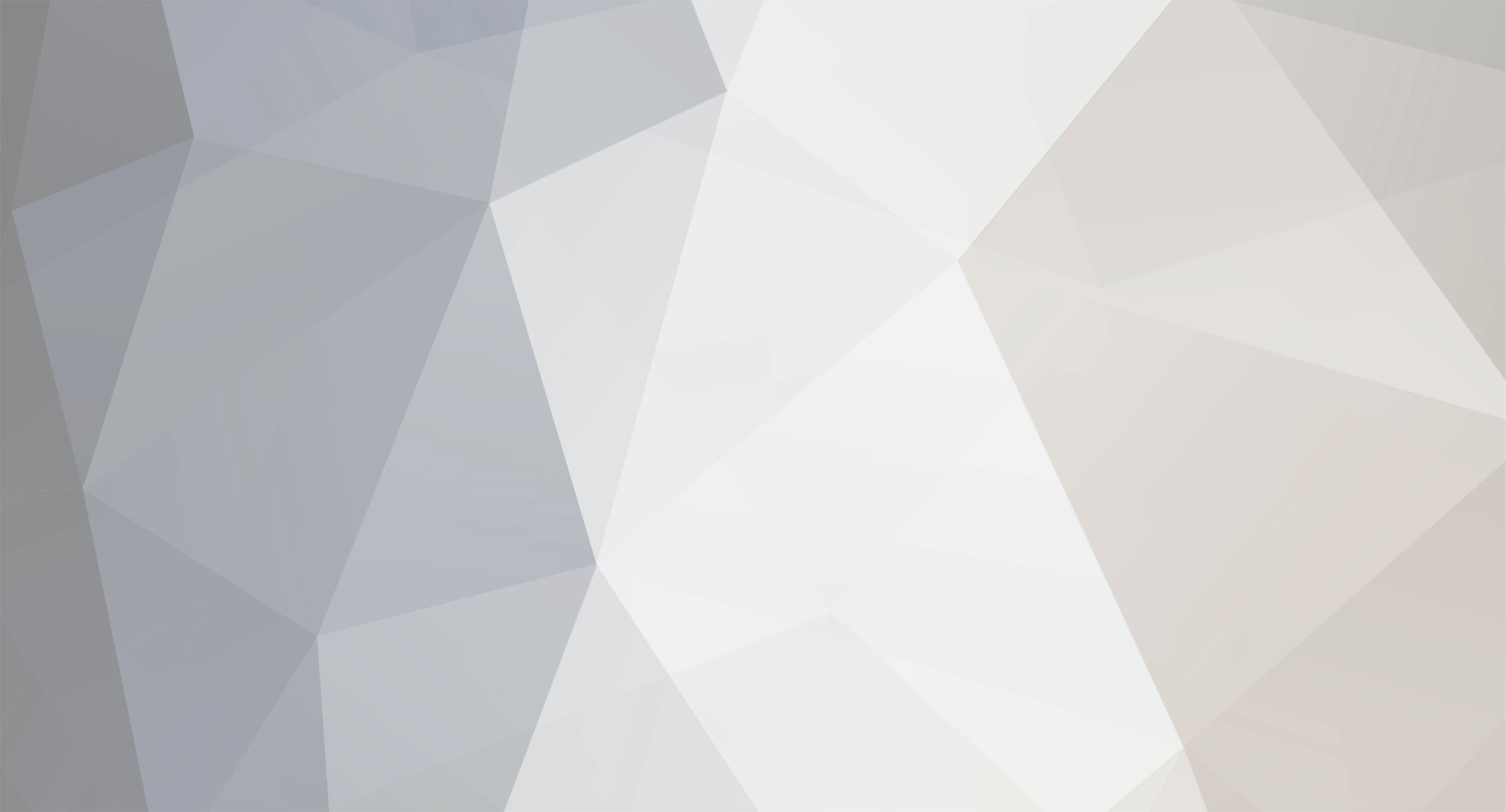
infaddict
Members-
Posts
13 -
Joined
-
Last visited
infaddict's Achievements

Member (3/5)
0
Reputation
-
Running new pipes from loft into kitchen behind plasterboard
infaddict replied to infaddict's topic in General Plumbing
Thanks Mark. How do you usually repair? Do you use dot and dab technique or something else. Guess it's important to ensure edges and joins don't have any give which could lead to cracking later. Cheers. -
Planning a kitchen renovation and all appliances and sink are moving to different places. I live in a bungalow and all hot/cold pipes go upwards into loft for easy access, and its all plastic push fit style. All the pipes are sat on top of blockwork which then has dot/dab plasterboard over the top. I need help on best way to run new pipes to the new locations. Is it possible to use a flexible rod kind of kit to find a way down between the dabs, or it that impossible and best to cut out sections of plasterboard and repair later. I plan to get the whole room re-skimmed anyway. I think for fire safety, dot and dab is solid all around board edge anyway which makes it hard to feed new things down. So what is best approach? And whatever the best approach, any advice/tips of repairing the damage to the plaster board, inspection holes or sections cut away where I will run new facilities. Thanks in advance!
-
New drainage required through/under concrete floor
infaddict replied to infaddict's topic in Floor Structures
Interesting. So option 1 is a diagonal run of about 1.7m to a gully that is used for the current kitchen sink. Option 2 is a 4.5m straight run to an existing private sewer where I would install a new IC to take this new connection. Clearly option 2 is a much longer run, but at least it is straight. But I don't know if its straight in line with the beams or perpendicular to the beams! The final option is ditching the sink on the island and just running power (for a hob or socket to charge phones) which requires much less depth (level conduit only). The Mrs wouldn't be happy and means we'd have to find another home for the sink and redesign our proposals. I wonder if its possible to get a wired inspection camera through the air vent and around the periscope to see whats going on under there. Or I could drill a pilot hole anywhere on the kitchen floor to do the same, but risk hitting a beam and that will of course puncture the DPC which would need repairing. Am I right to say the block and beam would normally have some rigid insulation on top, then a screed of concrete? If so any usual depths for both the insulation and the screed? Thanks for all the help. -
New drainage required through/under concrete floor
infaddict replied to infaddict's topic in Floor Structures
I will ask specifically about the floor but when I previously asked building control about their inspection of sewers/drains, they said an external company/partner was used for my site and they do not have the records. I could ask them who would have the records as surely they should be kept! -
New drainage required through/under concrete floor
infaddict replied to infaddict's topic in Floor Structures
Yep there are several air vents on all 4 external wall aspects. The DPC appears to sit on top of them. I wonder if these are ducted as they appear to be slightly above floor level. Does the presence of air vents mean its beam and block then? -
Hi, I live in an 11 year old detached bungalow that has a concrete floor throughout, with all services (except drainage) going upwards into loft. We are remodelling the kitchen and my wife wants an island so investigating options for drainage from the sink on the island to an existing gully or sewer just outside the existing walls. The challenge I have is, I am unsure of exact construction method for the floor. It could be block and beam with a screen on top (if so, depth of screed is unknown) or it could be a deeper concrete slab. I have contacted the original housing company to ask for any plans or technical information they have on the floor structure, but as its 11 years ago I don't hold out much hope. Any ideas on how to confirm the structure? Could I drill a test hole and use an inspection camera to try and find out if there is a cavity under block and beam? If I do that, I will have likely broken the DPM so not sure thats a good idea (unless I come in from side of house under the DPM perhaps). If it ends up being block and beam, my guess is its a very bad idea to cut the blocks and beams in any way as it will damage the structural integrity of the floor. What other options for new drainage do I have? If its not block and beam and is a deeper slab, then that might work as I don't need much fall and its a fairly short run. As always, any comments, thoughts, tips much appreciated and thanks in advance.
-
Been looking at floor cutters and more than willing to hire one for the job. Unsure if 165mm depth of cut is enough, as I don't know how deep my pad is. Maybe I could drill a test hole or something. And perhaps 165mm is enough even if concrete is a bit deeper, as likely an impact breaker might do the rest. Wondering if its possible to dig a decent channel, but not damage the DPC too much allowing me to repair it fairly easily. Thanks for advice on conduit, I definitely need to use it to future proof, including some spare mousing lines etc.
-
I have no idea what depth of concrete pad I have either. House was built 10 years ago. The deepest hand held saw cuts around 120mm, the deepest floor saw cuts around 165mm, but found the one below which cuts much deeper (400mm) if required. I quite like the idea of nibbling little bits away at a time but unsure if it would be more efficient in the long term. https://www.husqvarna.com/uk/power-cutters/k760-cut-n-break/
-
Thanks Conor. Local building control did suggest 110mm as first choice, but also seem happy with narrower than that depending on the distances involved. But advised protecting it with PVC protection tape. But I like to do a "proper job" so if it needs to be 110mm I'd rather bite the bullet and get it done. The 110mm option clearly means a deeper trench to run the pipe with required fall, which will certainly mean breaking the DPC. Again building control seem fine as long as thats repaired properly, either using liquid DPC or patch and seal. In terms of making it rod-able, any recommendations please? I would likely convert from 110mm down to smaller white under sink size immediately so unsure where to put a rodding point.
-
Thanks Peter, makes sense. I need to work out my exact distances to see if ventilation becomes an issue and have to use certain pipe size. Option 1 is a short 1.7m run to an existing gully but I might end up too low (as I need the required fall) and can't remove that gully or replace it without damaging a lovely new patio laid only last year. Option 2 is a much longer run (approx 4m) to side of house where my private foul sewer runs with several inspection chamber (and not patio to worry about). But longer run means more fall required and potentially bigger diameter pipe and/or syphon proof trap etc. With this option I will likely end up below the DPC and therefore have to be careful to repair that as necessary.
-
So glad I found this amazing forum! I'm remodelling a kitchen in a 10yr old bungalow which has a conrete slab floor. I want to create a new island with a sink so need hot, cold and drainage fed to the middle of the concrete slab. All hot and cold pipes run through the loft and down the dot-and-dab walls, so new pipes can easily be fed off in the loft, down a nearby wall and then along a gully cut in the concrete slab to the island. For the hot and cold, a few places I need help/guidance/confirmation: 1) I was planning to use a conduit (like a wider waste pipe or simiar) to run each of the hot and cold pipes. 2 conduits to keep hot and cold separate (this might be overkill but thought hot would need insulating but not cold and don't want hot heating cold). Does this sound ok or unnecessary? 2) How deep into the slab do I need to bury the conduits/pipes and do I need to protect plastic conduit from the cement? Then for the waste situation, I have a private foul sewer that runs under unused (soil) last to the side of this kitchen, so was hoping to route a waste pipe in a new gully in the slab, to that side of the kitchen. With suitable fall built in of course. Over the weekend, I will open the inspection chamber to see how deep that sewer is and if there are any spare connection points I could use. For the waste, again some things I'm wondering about: 1) Can I use standard 42mm white plastic waste pipe to bury in the new gulley I've cut, or is that a bad idea and there's another way (conduit, different kind of pipe, wider etc)? 2) How deep into the slab should I bury any waste pipe? 3) What is best practice to connect to the private foul sewer buried outside my wall? Does this have to be done underground, meaning I have to drill/cut/dig very deep and potentially hit foundations, DPC, ironwork etc. Or can it come out at ground level and go down into this sewer. Sorry for all the questions and thanks in advance.