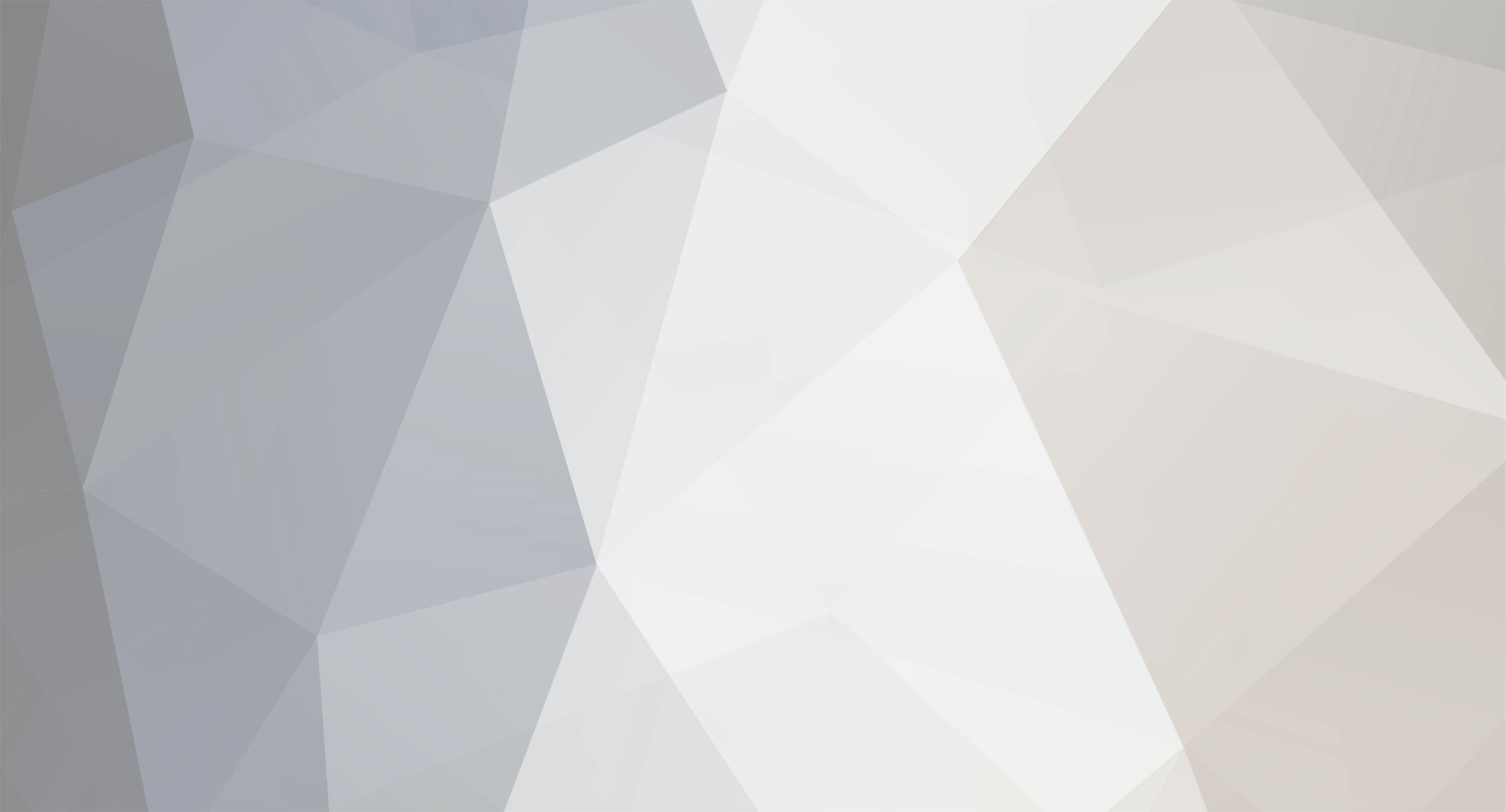
Mike
Members-
Posts
1268 -
Joined
-
Last visited
-
Days Won
7
Everything posted by Mike
-
Boiling water tap - Quooker alternatives
Mike replied to canalsiderenovation's topic in General Plumbing
It's recommended that there should be a supply of unsoftened water in the kitchen - either feeding the kitchen tap, or a separate one like @Nickfromwales provides. -
Help! How can we avoid trickle vents on a Jacobean cottage reno?
Mike replied to Amberella's topic in Windows & Glazing
Find a an installer who is a FENSA / CERTASS / Assure member who agrees that you don't need them because your cottage is drafty enough. However, adequate ventilation is necessary to maintain a healthy internal air quality and to avoid condensation & mold; the dMEV fans mentioned by @Iceverge would also be my choice if there is any doubt about that. It's also vital that any solid fuel fires / wood burners have proper dedicated ventilation or you risk carbon monoxide poisoning, or worse. -
I'd choose a flexible woodfibre batt such as SteicoFlex (or hemp batts, but I AFAIK they're not yet widely available in the UK). Apart from being pleasant to work with, they provides roughly double the 'decrement delay' compared to glassfibre or mineral wool (the length of time taken for heat to move through the insulation). That's very helpful in reducing indoor overheating in summer. Of course it also has good green credentials.
-
Advice as I start budgeting - can I afford to self build?
Mike replied to four_candles's topic in Costing & Estimating
There are a few things mixed up in there: The pore structure of lime mortar and plasters does transport moisture transfer though them better than through sand-cement & gypsum (and lime putty does so better than NHL), so lime plasters are useful in allowing moisture in a wall to escape - which is why it's often recommended in older buildings without DPCs. Gypsum plasters are better than clay and lime at absorbing moisture, but clay is better at short-term (daily) bi-directional moisture buffering, while lime buffers moisture the least. However if the wall material behind the plaster is good at buffering moisture, then lime (due the above mentioned moisture transporting behaviour) and clay can both be useful in moderating daily swings in indoor humidity. And that can increase comfort in circumstances where uncomfortably high or low humidity would otherwise occur. I don't recall seeing any any research on plaster types & VOCs, but since Fullers Earth has some useful properties, it wouldn't surprise me if clay plaster had some too. VOC levels are normally very high for around the first 3 years after construction, partly due to off-gassing from building materials, partly from the new carpets and furnishings that are often used. Reducing them is going to require good well controlled ventilation, as will keeping CO2 levels to acceptable limits in both the short long-term, irrespective of the other factors. -
New extension DPC Tray Flat / Sagging - What to do?
Mike replied to boxrick's topic in Brick & Block
If there's EWI, then indeed it's very unlikely to be a problem. -
If you can find a bung (68mm » 40 reducer +40mm bung?), then you could have a capped-off 'stub' downpipe just long enough to fit a rainwater diverter. The connect that to a black hosepipe and run that along the top of the wall. Or even under the coping stones?
-
Tipped off a few days ago by @Nick Laslett's mention of the free Opaque software package (decrement delay calculator etc.), I experimented with another free package from the same site: Climate Consultant. Climate Consultant indicates the potential effectiveness of different design strategies that could be adopted at a particular location, based on its typical local climate. Being based in France, I found it interesting to compare different geographic locations, but was thinking that it would be good if it were possible to use it to compare current and future climates in the same location. I spent a day or longer trying to pull together a similar comparison for a client some years ago Today, I came across a website from the University of Bath - COLBE (https://colbe.bath.ac.uk/) - that provides separate future climate files for every 5 km square in the UK (and every 25 km for India), based on current projections. They're provided free and are in the same .epw format that Climate Consultant uses, so it's now easy to use it to compare climate design suggestions for a regular year or a heatwave year during 1961-1990, 2010-2039, and 2070-2099. All suggestions are generic, not tailored to a particular building, but it's worth a look if you are into your building / climate science. The cut in the need for winter heating and the increased desirability of shading windows both stand out and, of course, the climate projections are scary.
-
- 3
-
-
New extension DPC Tray Flat / Sagging - What to do?
Mike replied to boxrick's topic in Brick & Block
Or non-harmlessly though to the inner leaf. One or the other. -
New extension DPC Tray Flat / Sagging - What to do?
Mike replied to boxrick's topic in Brick & Block
If it's not rendered, then with hard rain in an exposed location it can be a continuous flow, especially if the brickies haven't fully filled all the joints. Unless I had a rendered wall, I'd definitely be wanting to correct it. You'd need to cut out short sections of brick, cut the insulation and insert 'retrofit cavity trays' designed for the purpose, reinstating the insulation above and below, then the add back new bricks, making sure that the joints are well filled, but adding preformed weep holes. Then leave it several days before do the next section. You can have different sections on the go at once, as long as they're well away from each other to maintain the structural integrity of the wall. I've done similar (as a manager) retrofitting trays above lintels that the original builders 'forgot'. -
Chimney to increase subfloor venting? Liquid radon sealant application?
Mike replied to YodhrinForge's topic in Ventilation
There are Radon measuring services available, if you want to be sure. But if not, then assuming that there is a problem is wise. There are published recommendations for Radon barriers & sumps and I'd stick to one of those to avoid potential problems with home-rolled solutions when you eventually come to sell it. -
Sliding along runners works well, but at 180KG it could go dangerously wrong for the people beneath. I've slid heafty gluelam beams to roof level before, using a pulley on the scaffold to avoid anyone beneath. I think I'd probably do similar by building a scaffold tower (metal or timber) the full width of the landing at the head of the stairs, to get the pulley up near ceiling level. That would enable you to pull the bath up the stair sliders and up onto its end, then move the pulley and lower it down onto its side again.
-
Out of curiosity, I've just been checking the requirements in France. A quick look suggests that there may be no requirements for individual & semi-detached homes, which isn't going to help much. For terraced housing & larger buildings the solution seems to be to use a 15mm fire-resistant plywood cladding to the outside face of the stud (rated B-s3 d0), followed by the external membrane & cladding (to which you could add cavity barriers - not required in France, it seems). Of course, that means keeping the insulation within the studs, with supplementary insulation on the inside face of the studs, not the outside.
-
MVHR plan questions
Mike replied to oliviaaa999's topic in Mechanical Ventilation with Heat Recovery (MVHR)
It looks like there may be 2 on the drawing already - if that's what the large dots are. The 'Single duct supply valve' symbols are in strange locations, so I think they're only intended to show you which type go in which room. Could be clearer... Just spotted that the duct runs in the attic go to some inappropriate locations too - you don't want the standard vents they've specified that close to the walls. I can't think of any good reason why they've shown it the way they have. You'd be better using the 'big dot' locations as the starting point, then consider how that fits in with your light fittings / showers / other features & come back to us for feedback. -
MVHR plan questions
Mike replied to oliviaaa999's topic in Mechanical Ventilation with Heat Recovery (MVHR)
Like MVHR units, it's easy to stick a fan in a box and call it a cooker hood, but that doesn't make it effective. Choose one with a high European 'Grease Filtering Effectiveness' classification - see https://forum.buildhub.org.uk/topic/42370-cooker-hood-with-its-own-mvhr/. It's still a good idea though to have a filter on the kitchen extract, but it can be a concealed 'sock' type behind a regular extract (a good idea on every extract). The only reason I know to use the 'visible' type in your spec, is that it jogs people's memory to change the filter when they see it's ugliness. It looks like there may be 2 on the drawing already - if that's what the large dots are. The 'Single duct supply valve' symbols are in strange locations, so I think they're only intended to show you which type go in which room. Could be clearer... There are a few special circumstances where it's possible (that you're not going to encounter if you're following a good design & specification), but no risk at all if you use a ceiling vent that uses the Coanda Effect (Zehnder Luna, if you're sticking to that brand). Keep them underneath the loft insulation. As already recommended, find somewhere within the heated house envelope. In a larger house you might have a plant room, but a utility room or kitchen would be OK if you can spare the wall space. If not, then there are some models that hang horizontally from a solidly constructed ceiling. For example the Zehnder EVO range, if it's available in the UK and you want to stick with Zehnder. -
Are there any modern basin wastes and traps that are reliable?
Mike replied to SimonD's topic in Waste & Sewerage
Another style with a clear flow (apart from the stopper) is the flip top type, where the stopper remains permanently in place but rotates from vertical to horizontal. Though it may also put your earrings at risk. -
A good tip. I did the same.
-
Another topic to add your to-do list is to learn the VAT rules and budget accordingly. If you're mostly DIYing then you'll be paying VAT on your materials and, while you can eventually reclaim the VAT on most items (not all), you'll have to fund them until you put in your VAT reclaim, so don't let it become a cashflow issue. And, where you do have contractors, make sure they only charge you VAT on the items that they should; if you pay it on other items you can't reclaim it. There are other threads that go into this. Returning to the design, because plasterboard, plywood, OSB and other sheet materials come in 1200mm widths, it will help to reduce waste if you can plan as many dimensions as possible on multiples of 300mm. It won't save a fortune, but will make a difference if cash is tight. For some 'relaxation', track down the BBC series 'The House That £100k Built'; it may give you some cost-cutting ideas, though bear in mind that inflation means you'll now have significantly less to play with than they did.
-
They've some concerts in Europe this year: https://kraftwerk.com/concerts/index-concerts.html
-
Yes, if they're wired in, then no problems on a balcony or anywhere else, in most cases. However the article posted by @saveasteading (and the use of Balkonkraftwerke, AFAIK) refers to balcony plug-in solar.
-
Looks like they changed the law in 2019 to allow it (subject to rules & registration): https://www.canarymedia.com/articles/solar/how-germany-outfitted-half-a-million-balconies-with-solar-panels
-
Not legally, but that may change (though not in a rush); there was a report just a few of weeks ago: Currently, UK regulations do not allow plug-in solar to be used in the UK, but the government is working to explore its potential. Action 2: Government will conduct a safety study this year with the aim of unlocking opportunities for plug-in solar over the next few years. https://www.gov.uk/government/publications/solar-roadmap/solar-roadmap-united-kingdom-powered-by-solar-accessible-webpage
-
Self build house - is MVHR worth cost?
Mike replied to Wadrian's topic in Mechanical Ventilation with Heat Recovery (MVHR)
I spent >€4K on my apartment (+VAT), but that includes following my own advice and installing a PassivHaus certified Zehnder unit (with per-heater due to cold winter temperatures) and hiring some guys to abseil down the side of the building to core-drill through 400mm of stone for the air intake and exhaust. Apart from them screwing the external vents in place, it's self-installed. If you're wondering, I can vacuum the vents from the windows. The new electrical installation is incomplete so It's not yet operational, but it's installed for several reasons. The apartment will be pretty airtight so it provides the necessary ventilation; I'm in an urban setting so using it to filter the air and avoid noise via trickle vents / open windows is a very big plus; it's essential to reduce humidity due to having a tricky unventilated insulated ceiling; adding an evaporative cooler to it (another €1K) is the only way I could provide some summer cooling; it also provides heat recovery during the heating season. -
Mansards with no soffit ovehangs
Mike replied to jackcowdrey's topic in Lofts, Dormers & Loft Conversions
At a guess they're not ventilated as they probably have very minimal insulation in the ceiling - there's not enough depth. As for drainage, the roofs would likely slope backwards, so the rain would run back and down the mansard (unless driven by the rain). -
How best to cable for Washer and Dryer ?
Mike replied to Spinny's topic in Electrics - Kitchen & Bathroom
This. Also, when you push the machine back in, you don't have a cable looping on the floor and getting in the way of the wheels - you can pull it through from under the sink. -
How best to cable for Washer and Dryer ?
Mike replied to Spinny's topic in Electrics - Kitchen & Bathroom
I'd put the sockets in your 'sink cupboard', so you need no additional depth behind the machines. It's what I'm doing and I only have a 350mm width unit below my sink to squeeze everything you have into (plus the waste & overflow from a water conditioner). If the appliance cables aren't long enough - they probably will be - then replace them (or get your sparky to).