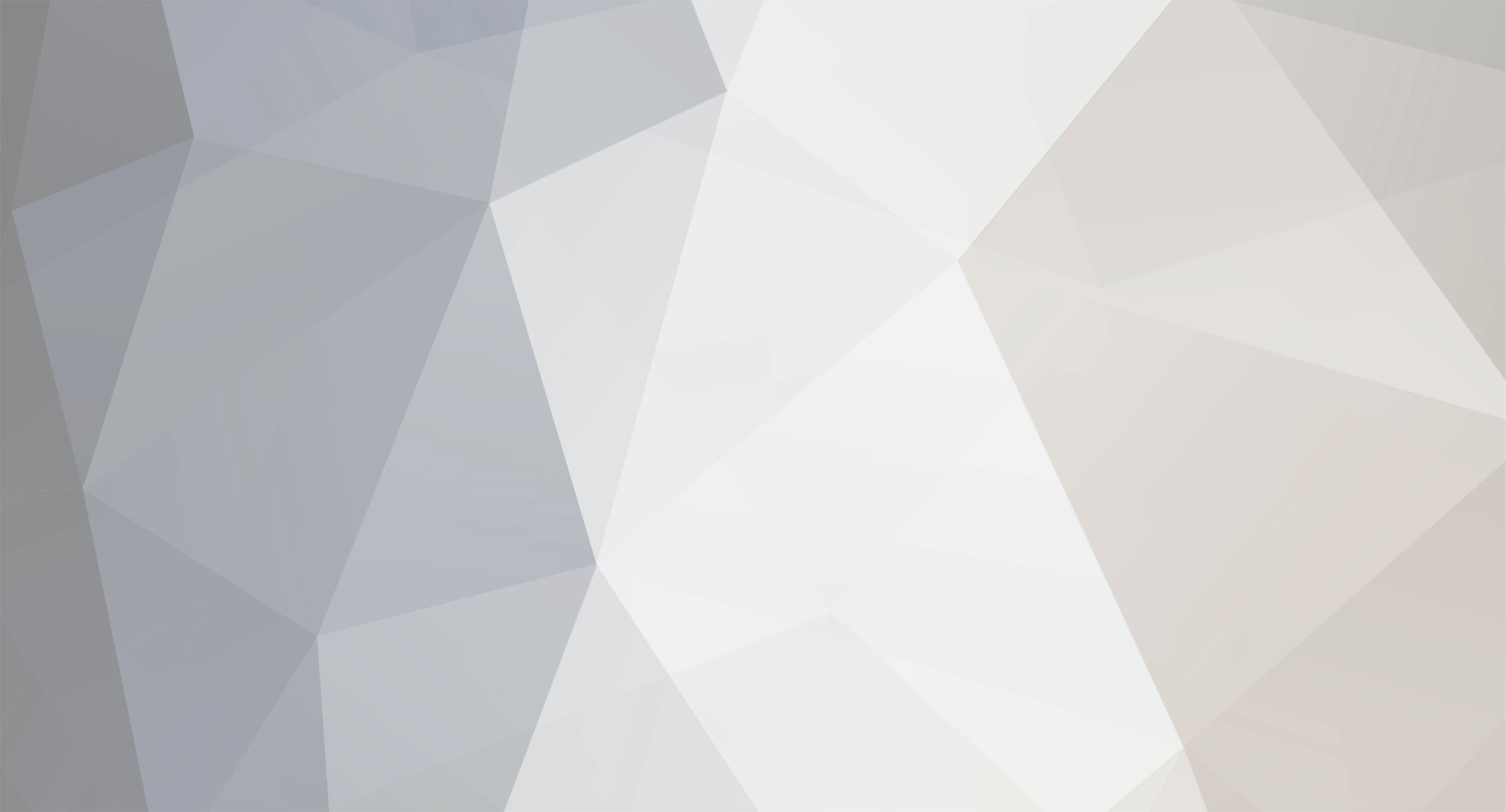
MortarThePoint
Members-
Posts
2023 -
Joined
-
Last visited
MortarThePoint's Achievements

Advanced Member (5/5)
216
Reputation
-
Recommendations for internal doors?
MortarThePoint replied to markharro's topic in Doors & Door Frames
Did you have any success finding formaldehyde free doors or indeed any that have any sort of certification (M1, A+, Carb2, etc)? -
A handy specification that may go unnoticed is 'punctual conformability'. Nothing to do with ability to be on time, but the ability to cope with small defects. No idea what the 'resistance to large ball' specification means. Parador appear to call this "Compensation for punctual unevenness" and their 500 product (2.6mm thick) has a figure of 1.15mm. I'm going with TimberTech Elite Plus 3mm, also 0.1tog but more available, which is 3mm thick and has 1.5m of 'punctual conformability' Sorry @Nickfromwales, good advice about UFH but we're going to pop insulation over it in some rooms. Laminate and underlay should total 1tog or less which is a R-value of about 0.1 m2.K/W which in my mind I compare to the Rsi value that is likely around the same. Many have questioned my putting UFH upstairs and I think this is an example of where it's going to give me options. Compromises, compromises.
-
It could go up an if not liked or goes bad get taken down easily
-
Does look good I wonder about peel & stick being a good compromise
-
We've got to the stage of proceedings where 'client management' is a significant challenge. In that I mean trying to keep my wife happy. I need drawings, dimensions, products and decisions whilst she lives in mood boards and options. This isn't a picture of my wife but, I am getting used to this expression and worse: She is keen on having wall paper in a couple of places: Hallway, above shaker panelling Downstairs loo, above v-groove cladding I am sold on the panelling / v-groove but not the concept of wallpaper. A painted wall with pictures on looks much nicer to me and feels a better way to have the 'interest' that wallpaper adds since the pictures can be changed and don't damage the wall. It's very easy for wallpaper to end up kitsch. Also, I don't think I have ever seen wallpaper that hasn't started to lift at the joins. Am I rightly concerned about wallpaper or should I get back in my box.
-
He's seems really good. He's knocking back any imperfections in the plaster. His method is light sand, primer/mist, proper sand, spot prime/mist and then the finish coats (which we haven't got to yet). The first sand mainly gets rid of plaster splashes and dust etc as it's got extract. The uniformity of the white primer coat allows him to pick up imperfections with his low angle light. The spot priming is adding back primer to any significant patches that have been sanded off.
-
Good point and in one room that gets me thinking. I had intended to lay the laminate (10mm Egger EHL175) in the direction of the long axis of the study which also leads to the predominant light source. That does however leave it perpendicular to the direction of room entry. The red zigzag is the direction of the herringbone in the hallway. I have a similar situation in the sitting room, but there is a bay window at the end and it will also run through into the dining room with patio doors at the end so I think it only makes sense to have it going parallel to the long axis in there. That's likely to be 14 or 15mm engineered oak flooring so a different consideration to the laminate. Upstairs, we are having Herringbone 8 laminate (8mm) in the main bedroom and also I expect in the dressing room, though that may end up carpet to better cope with the possibility of wet feet. Ground floor is Thermabeam insulated precast concrete planks over 300mm void and first floor is 150mm HCF planks. I particularly liked the idea of the Thermabeam as it keeps the concrete inside the insulated envelope unlike standard beam and block. HCF was good for speed of installation and again thermal mass inside the insulated envelope. I'd be concerned if either had any mid-span settling. They've been down for 5 years and covered in screed (50 - 60mm Cemfloor cement-based liquid screed) for almost 4 years. We've only had one screed crack in a position I partly expected it on a long narrow run where I proposed a break anyway. The screed is extremely flat, with the odd bubble crater or piece of aggregate sticking up about 1mm. I think I'm over thinking it and a 3mm underlay would be fine, though I'll still hunt down and grind any pimples with a brick as @saveasteading suggests and a grinder if anything more significant, but I'd be surprised if I needed that.
-
I have already been including AAVs at the end of all my significant branches (before any vertical sections of 110mm pipe so that should satisfy any negative pressure requirement (i.e. stop traps from being sucked out). I understand that septic tanks need a low level inlet and high level outlet so as to create a flow though of fresh air, but a STP has a pump so any outlet I would expect to be OK surely. Maybe not one of the BioRock type or spinning disc ones though, but I'm not considering those. I am considering Graf One2Clean and Marsh Ensign systems. The Graf looks to have significantly cleaner effluent, easier to have granular backfill rather than concrete and also has a non-continuous pump which saves energy. They do talk about having a 'chimney effect' though which I assume is to prevent smells coming out of the low level pipe.
-
I may end up plumbing the detached garage just for this reason. Will probably be grateful of having a sink in there too
-
Looking at Part H I see a conflicting pieces of information: So which is it, 32mm, 50mm or 75mm? I understand the need for a large diameter if it is to allow air into the stack and there is no AAV as it has to provide a reasonable flow of air as the waste water rushes through the lower pipes. Even so, air moves much more easily through a pipe than water does. I was planning to just have an Durgo/AAV, but think I need an SVP to allow positive pressure from my sewage treatment plant (STP) to vent. Any such venting from the STP would have low flow rates and could therefore go though a narrow pipe (to a roof tile vent). Even 20mm pipe would be plenty big enough I don't fancy a 75mm pipe going up the bathroom wall and a 32mm one would be much more acceptable. Can I plead the case if I have a Durgo/AAV for the high flow inlet requirement?
-
Oh, are you suggesting I have no underlay and use something that can be glued straight to the screed (or feathered) surface? If it's to be believed, 0.1 tog is the difference between 8mm and 10mm laminate, so wouldn't rob much heat. Anything that could be bonded is likely to be thicker. As an example, 14mm engineered oak is 1.13tog. that's the same as 10mm laminate plus 0.3tog underlay. Or are you suggesting something like glue down LVT would be a better choice?