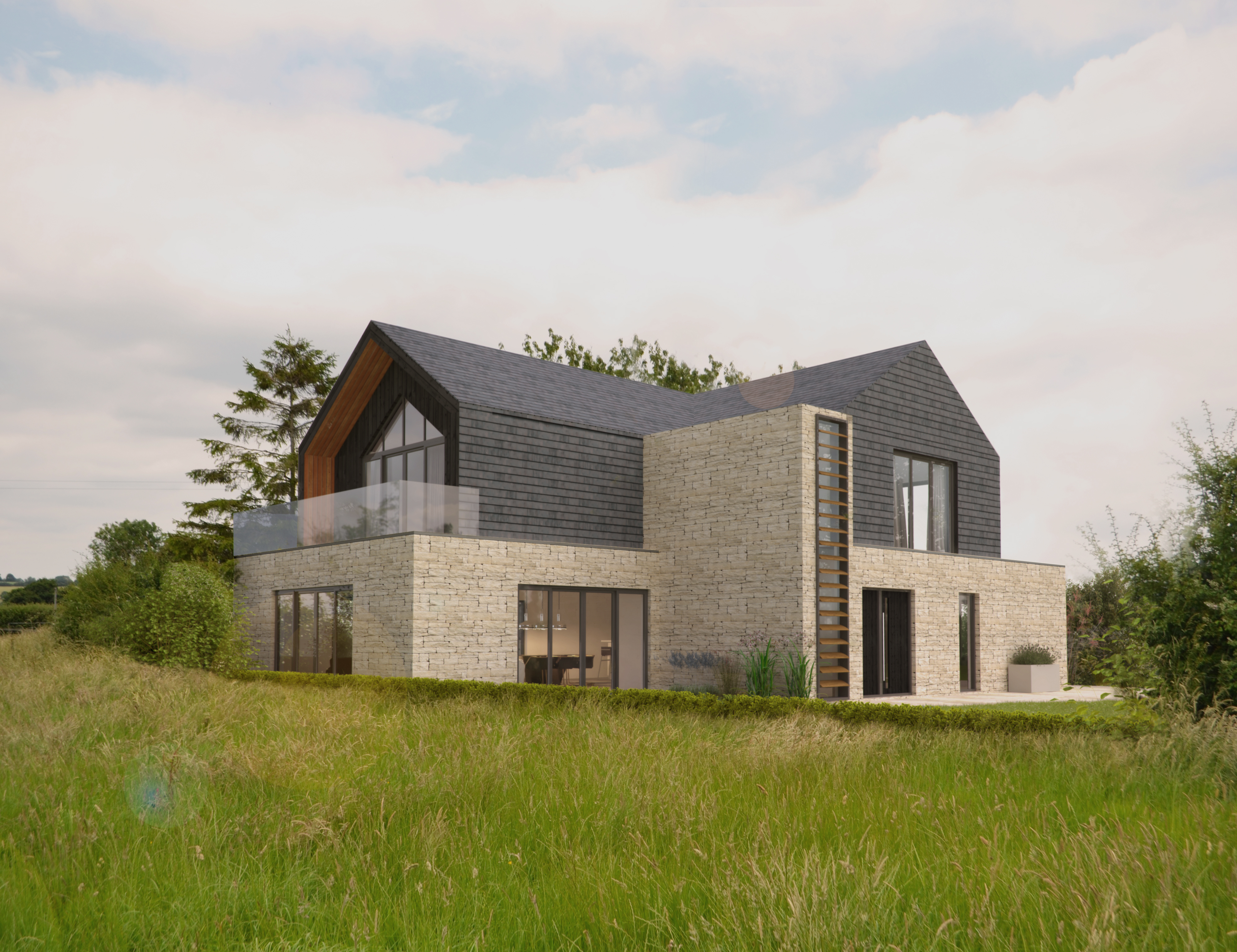
-
entries
53 -
comments
404 -
views
16612
About this blog
Vivienz's blog on a contemporary new build in north Dorset. Hopefully.
Entries in this blog
12
Vivienz's blog on a contemporary new build in north Dorset. Hopefully.