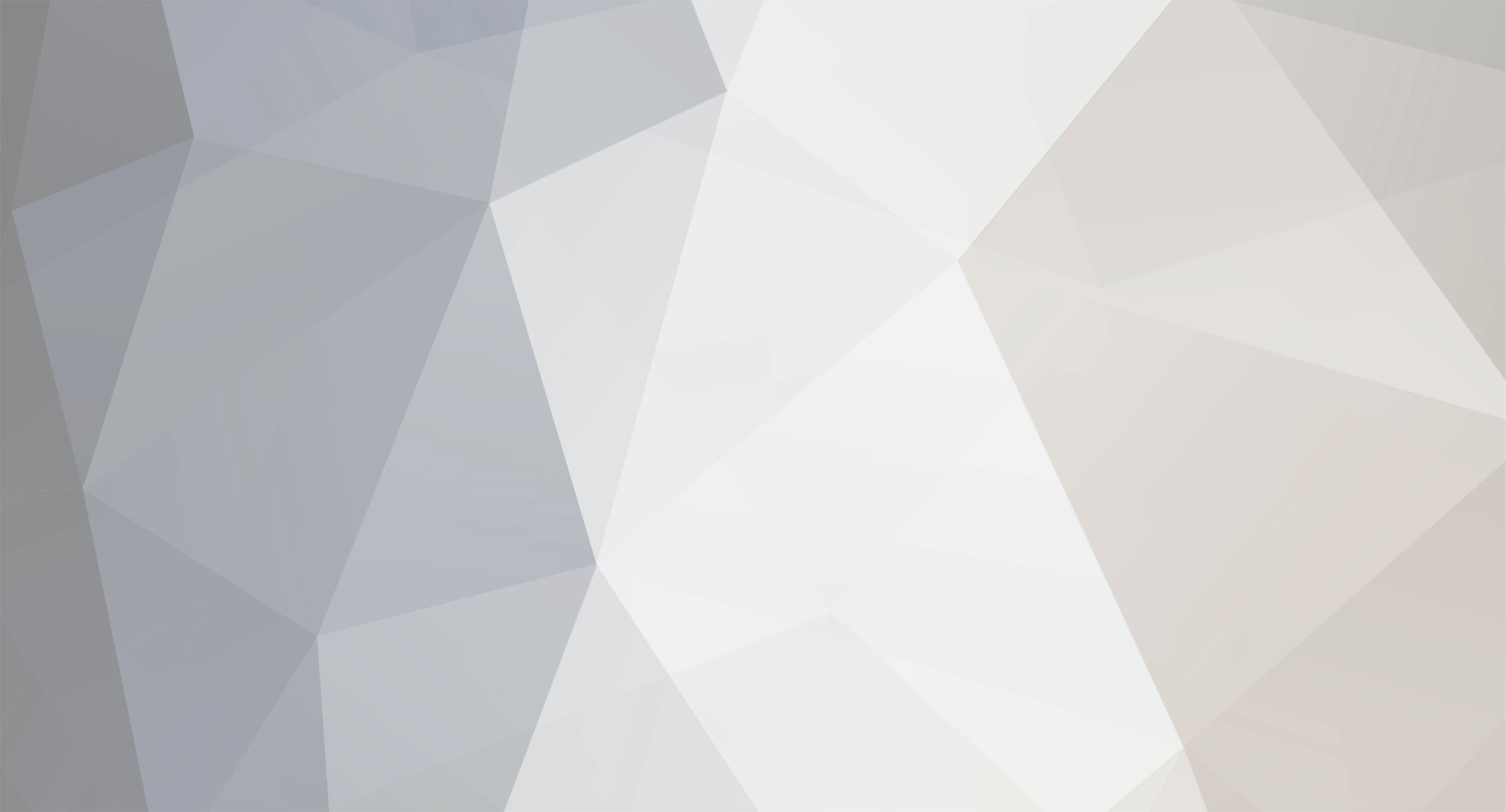
sean1933
Members-
Posts
88 -
Joined
-
Last visited
Everything posted by sean1933
-
I'm speaking to sparky tomorrow re locations as it somewhat slipped my mind. I did just plan AICO's interlinked with a central test/reset button (high ceilings). But im now worrying about the Large Dwellinghouse criteria (380sqm house, ground is 230sqm) that makes me think I need a special ie expensive grade A system. Anyone else get caught out by this?!? "Grade A Category LD3 fire detection and alarm system"
-
Discount Offers of the Week
sean1933 replied to Ferdinand's topic in General Self Build & DIY Discussion
I couldn't agree more - but when the wife has ruled out any other 'fob' option its the only way for smart control. First world problems aye. -
Discount Offers of the Week
sean1933 replied to Ferdinand's topic in General Self Build & DIY Discussion
Anyone looking for a standalone Ekey finger print reader - I've just bought one on Amazon for £271! Normally retail at nearly £800. After purchase yesterday price jumped back up to £795 but looked again this morning and now showing £294 with 2 left in stock. Not sure what's going on its the black glass version too. 😄 https://www.amazon.co.uk/dp/B0BRJPQ6HY?psc=1&smid=A3P5ROKL5A1OLE&ref_=chk_typ_imgToDp -
Thanks for your responses both. To confirm - its bottom fix channel only, and yes I meant coach screws sorry. Coach bolts would be simple but look awful from below as obviously visible from the underside. Russell sadly you appear to confirm my secondary worry in that without testing the pull out strength is unknown, not to mention my (probably overthinking mind) worry about splitting / weakening the beam with so many big holes in close succession. The need for a structural engineer would probably negate the cost of the already tested method, especially as I'd need to find a new one as mine has retired and emigrated. This is the alternative that I was trying to avoid purely due to cost - expensive but tested and avoids the need for deep holes. https://pure-vista.com/product/timber-fixing-plate/ I've managed to get a bit of discount due to quantity but still eye watering for what it is.
-
Evening all. Short story is our balcony frames on the gables is made of 250 x 225 oak. The intention being to fit frameless glass balustrades (21.5mm lam/tough) in the associated channel. I have the glass and Posiglaze channels on site but when revisiting my building regulations i note the following condition 'Provide full balcony guarding details i.e. glazing and support posts and fixing 'details. 0.74 KN/m at 1100mm height not 1m.' I'm yet to speak with building control as I don't want to set hares running just yet, but all the fixing details/deflection test data I can find are into solid concrete or steel. Speaking to the manufacturer they agree 200mm M12 coach bolts at 200c (as per concrete detail) will be fine, but obviously don't have certificates to back this up. They do however now have certificates for their timber fixing plates which can be used on much smaller 100x150 timbers... but at £12.50+vat each at 200mm centres I'll need something like 116 so its going to cost a small fortune. I'm interested in others experience of such fixing scenarios - do I get into it with building control and hope they agree the coach bolt concrete fixing spec is fine, or just suck-up the extra £1500 and move on with my life?
-
Hi Mark, sorry for the slow reply I didn't see the notification. In short - this is still on the jobs list (for various reasons I had to take some time away from the build) but I wont be going for the EzyJamb product as the price is ridiculous. I planned to trial a custom setup with some plaster in QIC trims - I'm double boarding everywhere so with some ply behind to tie in the door frame to studwork I'd like to think it can be made rigid enough to not crack out - I think this is the principle NOD talked about above but I've struggled to picture his exact proposed setup.
-
Blinds that are compatible with Loxone
sean1933 replied to Dunny1234's topic in Networks, AV, Security & Automation
Interesting insight thanks. I have loads of wired velux and the sparky insisted on each one having a fused spur... thankfully happy for them to be in service locations rather than on show but still a bit of a pain. Upstairs UFH is wet so no issue there but will certainly expect a fused spur to be required for the electric towel warmers. Really helpful input. I assume you're running each location 3+e back to the loxone cabinet rather than a ring just for permanent live...? I've been hesitating on what I should install here as it seems to be a bit of a minefield of blind motor options... are there any standalone motors you'd recommend? I had seen others fitting 5 core flex but most dumb blind setups only required 4 core so was a tad confused why the extra core was required. what core thickness are you using for 3+e? Cheers Dan - blind motors do appear to be very low draw from what I've read so hopefully 0.75mm will do the job... then again there also seems to be 24v options which I expect would need thicker cable... decisions decisions but I dont want to waste money unnecessarily. -
Blinds that are compatible with Loxone
sean1933 replied to Dunny1234's topic in Networks, AV, Security & Automation
More googling led me to the following which makes me think I dont need local isolation... albeit its another forum and an 8yr old post so obviously interested in a more up to date opinion! https://www.electriciansforums.net/threads/electric-blinds-mechanical-maintenance-isolators-bsen-60204.101954/ Also - what size core flex did you go with @Dan F ? Would 0.75mm2 suffice or should I go with 1mm2? It gets expensive quickly! -
Blinds that are compatible with Loxone
sean1933 replied to Dunny1234's topic in Networks, AV, Security & Automation
I'm in exactly this situation now and looking to consider how I control lots of blinds throughout the house... but it's throwing up a few sill questions I can't answer. I have pretty much settled on just running 5 core cable back to the loxone cabinet for 240v control and sorting motor choice further down the road.... although cheap aliexpress Zemismart motors are looking tempting. https://a.aliexpress.com/_mLS5OTe However I'm getting confused re what the requirements are for local isolation for blinds... if required surely this is a major downside to 240v motors as they are a pain to locate especially with 4 blinds in close proximity. The next question is how do I isolated a 5 core cable as the usual fused spur isn't going to do the job!? @Dan F @joth what did you do? -
Morning @nod. I don't suppose you ever found any photos of this setup? I'm struggling to visualise the setup and am currently at this stage of my build. We have flush pocket doors and stupidly suggested we do the same on normal doors to match, rather than shadowgaps. I've found a ready-made profile (EzyJamb SRC) but at £500 a pop ( I need 10!l it's rather expensive! Any help much appreciated.
-
@SimonD Really great to see someone using this product - are you a tradesman with experience of such products/plasting or is this a first attempt? If the latter, recon its DIY friendly on a floor (and to a high standard) or does this fall within the realms of plastering, ie leave it to the pro's unless its behind some furniture! We've committed to microcement on our floors for the entire downstairs of our house (240m2). Originally planned on giving topcret a go myself in the garage but now seems they only sell with installation and the prices are eye watering. Do you have any experience of the Cemher floor product?
-
Fan Coil Units for use with a (cooling) ASHP
sean1933 replied to ProDave's topic in Air Source Heat Pumps (ASHP)
Did you ever proceed with this source Joth and if so what was your experience? I'm planning a similar setup to yours (inc Loxone control eventually). I have the same ASHP (although 14kw) and after researching air flow issues have written off the MVHR cooling solution. Will use UFH cooling downstairs but plan to at least plumb for FCU's upstairs. I'm in 2 minds whether to buy units now or see how the summer goes as the budget is shot and we may not need cooling (very likely though!) . We wont finish until end of the year I imagine, so time to fit in autumn before final decorating. Out of interest what size feed pipes did you use to the FCU's from plant room? We have 4 bedrooms in total upstairs, 2 on either side of the house that could theoretically share 2x ducted units if sized appropriately, or alternatively an FCU per bedroom. I'm not sure what sort of water flow these FCU's need. If I run vapour sealed(insulated) 22mm Hep2O to each side of the house will that suffice, or do I need larger if each feed may run 2 FCU's? Thanks in advance! -
Fan Coil Units for use with a (cooling) ASHP
sean1933 replied to ProDave's topic in Air Source Heat Pumps (ASHP)
Waterless trap straight into the soil stack should do the job. -
Thanks Nick. I think what differentiates Joth's suggestion is that the detection and shutting of the valve is triggered by the smart home leak sensors located throughout the property. Rather than an integrated alarm/detection unit that you are tied to their protocols/cloud controls etc. https://www.solenoid-valve.world/connexion/1-electrically-actuated-ball-valve-9-24vacdc-or-110-240vac-abvm08s This unit can have a manual control added to bypass in case of a fault. Have you seen any units like this ever installed? I did wonder if a standard 2 zone actuator could do the same job but decided not to go down that rabbit hole as not its designed purpose (or pressure I imagine).
-
Ufh manifold, blending valve with ASHP.
sean1933 replied to Russell griffiths's topic in Underfloor Heating
Thanks Gents, insightful as always. I've fed this back into the design guys and he's going to move some things around. Particularly the duct cooler also coming off the LLH/buffer. He didnt appreciate previously that I will want it running at the same time as UFH - assumed it was for cooling only and that I wouldn't cool through some of my UFH (he's not a fan). Will also be ditching some of the pumps as unnecessary so close to the ground floor manifolds. -
Did you go for this in the end Joth? Just come across the same product and seems like a sensible idea for backup flood prevention in the plant room. I'm inclined to go with fail open as wont want to lose water as well as power in the event of an outage! I also considered the option with leak detection alarm but unsure if its the right model to work with Loxone....
-
Ufh manifold, blending valve with ASHP.
sean1933 replied to Russell griffiths's topic in Underfloor Heating
Seems to be a running theme here despite the age of this thread. I have Wunda manifolds installed which are already in situ with the standard mixing valves (and Wilo pumps) - my fault as since install we've ditched gas and gone to ASHP (various reasons). Our ASHP (Mitsi Ecodan 14kw with FTC-6 controller) install is starting on the 20th Feb. Installer prev said we dont need the mixers, but at the time I didnt dive into why and he was relaxed about leaving them in if I wanted. I note Pete and Nick, you both say with ASHP we need the lower temp mixers. It might be because I'm tired but I'm struggling to get my head around all the reasons. I trust the advice just dont understand! Aside from the protecting overheating issue for the floor type (surely 35deg is safe enough - we have UFH downstairs in slab and upstairs overboarded, NO RADS), if the ASHP was running in weather compensation mode why do we need mixers that can get to 20deg?) I am minded that I only have a short window to buy different mixers if they are a must, but at the same time I have 4 manifolds (400sqm house) so not a small cost! (ESBE T4's @ £132 is a bit cheaper than the IVAR's thankfully - assuming they are up to the job and will work with the Wilo pumps from Wunda). https://underfloorparts.co.uk/product/esbe-t4-water-underfloor-heating-blending-valve/ Appreciate I'm going off topic slightly but due to size of the house/number of zones our ASHP installer has specced for a low loss header. Not something I've seen many others mention so interested on if its contentious or should I just trust its justified? With a low loss header do we need additional pumps to push water from the LLH to the post manifold/TRV pumps (required due to TRV's I believe)? I ask because they are showing on the schematic... meaning in total 7 pumps - 1 when ASHP hot runs into the house, 2 after LLH (per floor (2 x 2 manifolds) then the 4x post TRV's @ manifolds. Seems an awful lot to me! Diagram attached, note it doesnt include any of the UFH manifolds as thats outside their contract and 'my problem', and the HWSR shown has been deleted as we're going for a short run manifold setup. Having typed all this out I have now read the entire post and seen Joth's comments, I wonder if I've come full circle and am further confused! Bearing in mind we're using the same ASHP, FTC6 controller (albeit bigger/more loops/LLH etc) and eventually loxone too, would this do away with the needfor mixers entirely? If so, does this also do away with the need for pumps at the manifolds entirely as the post LLH pumps will suffice? HELP! Really appreciate the technical help as always! -
Stud thickness for horizontal 110mm soil pipe
sean1933 replied to sean1933's topic in Waste & Sewerage
Thanks both. I really like Punter's idea as it would help keep the wall slenderness down to a minimum which will keep her in doors happy, and I'm pretty sure I have some of that size timber lying around already. I did consider back to back studs but a +275mm finished wall buildup made me wince somewhat! -
Hi all. I've come to put up the last stud wall in our house (vaulted ceiling @ 3.8m, not load bearing) and my wife in all her wisdom is now adamant on a new bathroom layout, which moves the toilet to the opposite corner from the soil pipe. I am mindful that the 110mm soil pipe now has to travel horizontally 2.5m within this wall before it can turn 90deg and go under the floor (there is a steel within the mid span of the room that prevents me from going straight into the pozi joist floor at this point). The room sizes are already getting smaller than ideal so anything I can do to mitigate would be ideal. I had planned for 145 studs to hide vertical soil stack but now its going horizontal I appreciate after 125mm central hole is cut the remaining 10mm either side is clearly insufficient. Should I beef them up to 195 studs / line with ply (both sides I assume) ? I think someone had previously mentioned a similar issue being avoided with a raised sole plate but for the life of me I cannot find it by searching. I also found some sort of stud shoe but these didnt appear to be appropriate for 4inch pipes. Or is there an alternative easy solution? thanks in advance!
-
How did you get over this conundrum in the end, did you do something yourself or have to go to a specialist? ... we are just starting this delightful staircase journey now, and our budget has been well and truly destroyed already. When I started this journey over 3 years ago I thought 10-15k would be fine for a nice floating step design....... apparently that's the starting from prices these days!
-
Plant room wall covering - will ply suffice?
sean1933 replied to sean1933's topic in General Construction Issues
Only just seen this - thanks very much it covers the problem perfectly, I'll have to plasterboard some of the walls annoyingly but heyho! 😄 -
Following a slight move around to accommodate a larger downstairs WC (dont ask) we now sort of have 2 separate plant rooms - a HVAC/wet room, and an electric/loxone cupboard. House is block/brick cavity walls with a mix of block and stud internal walls. When I fitted the UFH manifold I stuck a full sheet of 12mm ply to the block wall to ease fitting. The top half will be used for supply Hot/Cold water manifolds. The plant room and cupboard are both mainly timber stud. As they are 'service rooms' my intention was to just fit ply straight to the studs and leave it at that. Ceiling would probably be plasterboarded but I haven't given it much thought - given the amount of HVAC ducting (2 units) I'd even considered not fitting any. We are due to have the internal 3 phase consumer unit installed on Friday and the cupboard is currently just ply'd floor to ceiling. I thought this was fine but having read a few other threads I'm confused if this is acceptable or does it need covering with plasterboard/skim to give some fire protection (or paint with expensive intumescent paint). If I need to cover it, will there also be an issue with the ply stuck to the block wall? I must say something that appears so trivial is causing me a headache. thanks in advance.
-
Much appreciated all - in that case I think I'll be going with the cheapest option.
-
I'm just going through this delightful decision at the moment. I have 220mm rafters and was aiming for a u value of 0.12 (rafters at avg.600 centres). Having previously looked at pricing 2yrs ago I had planned to use 230mm Frametherm40 + 70mm PIR below. Now I have come to ordering and I'm looking at pricing again. One thing for me is I hate noise so have started looking at density in comparison to stay Rockwool RTA45 (kg/m3). From what I have found the Frametherm 40 is only 13 kg/m3, 35 is 25kg/m3 and 32 is 32kg/m3. Does anyone have any experience of these densities in a pitched roof (I have 11mm OSB above rafters, planned for 38mm service battens and 15mm or double 12.5mm plasterboard below)? Should I just bite the bullet and go for the 35? Nobody appears to mention the Frametherm40... which is substantially cheaper than 35 or 32. Is there a reason for this and has anyone used this? Here is my quotes just to highlight the differences (over £3k between 40 and 35)! Unit price M2 per unit m2 price TOTAL for 400m2 100mm PIR £32.95 2.88 £11.44 £4,576.39 70mm " £26.75 2.88 £9.29 £3,715.28 50mm " £18.50 2.88 £6.42 £2,569.44 25mm " £12.50 2.88 £4.34 £1,736.11 140mm Knauf FrameTherm Roll 40 £28.59 9.14 £3.13 £1,251.20 90mm Knauf FrameTherm Roll 40 £30.50 14.25 £2.14 £856.14 140mm Knauf FrameTherm Roll 35 £35.00 4.45 £7.87 £3,146.07 90mm Knauf FrameTherm Roll 35 £38.50 6.84 £5.63 £2,251.46 140mm Knauf FrameTherm Roll 32 £40.50 3.19 £12.70 £5,078.37 90mm Knauf FrameTherm Roll 32 £44.50 5.13 £8.67 £3,469.79 If I had my own way I'd go pumped cellulose but sadly on the south coast the only installer I have found wants horrendous money so a no go.
-
Chimney stack flue choice, help! Liner or twin wall...
sean1933 replied to sean1933's topic in Stoves, Fires & Fireplaces