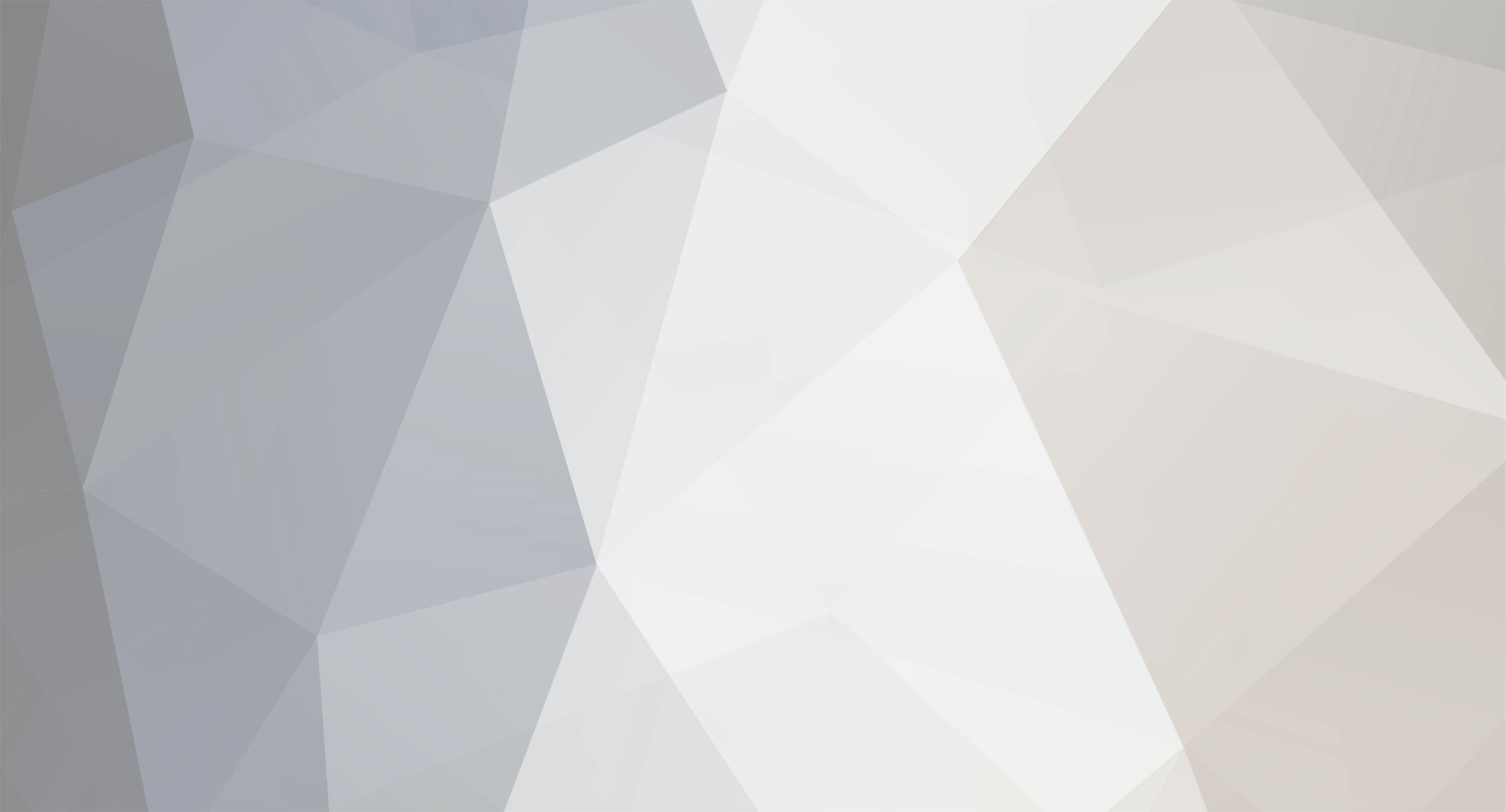
SimonD
Members-
Posts
1485 -
Joined
-
Last visited
-
Days Won
8
SimonD last won the day on March 12 2024
SimonD had the most liked content!
Recent Profile Visitors
The recent visitors block is disabled and is not being shown to other users.
SimonD's Achievements

Advanced Member (5/5)
717
Reputation
-
Intelligent go smarlty controls ev charging 24 hours a day but gives you a window of cheap rate leccy every night to use at your own pleasure - the window is actually slightly longer at night than with the dumb version go.
-
Yes, absolutely. And this will change a bit now with the r290 heatpumps working 'fairly' well up to 75C, so on an Octupus intelligent go rate, it becomes cheap as chips to batch charge on a reduced cop and then top up a few degrees with immersion. I think the cylinders should have a low level pocket for a thermostat so the call for heat to the heatpump is optimised according the stored temp around the coil. I've currently got a 200l thermal store knocking around and wondering how I can keep this in parallel to a heatpump unvented, potentially using the thermal store as a heat bank for the heatpump as we don't have a massive slab. But like with all these things, just got to get the calculator out and crunch the figures! + 1 I've been ordering from here for the past few months for all my installation jobs.
-
Viessmann 100-W Boiler, Wet UFH, 2 Port Valve and Opentherm
SimonD replied to Antec123's topic in Central Heating (Radiators)
Yes -
Yup, been there seen it and done it. I've lost a lot of hair in the process. I had a customer's house where the neostats would repeatedly pair fine up until the 10th stat and the last ones would refuse to pair, or would pair and then not work correctly. This was after replacing the wireless hub. I doubt it's the UH8, but more a tendency of the neoair stats. Why they can be problematic, I don't know. When you reset everything, did you proceed to repair from the closest stat to the furthest stat and do this methodically? It's worth calling Heatmiser tech support as they will help you through the process while to try to repair and get everything up and running again.
-
Viessmann 100-W Boiler, Wet UFH, 2 Port Valve and Opentherm
SimonD replied to Antec123's topic in Central Heating (Radiators)
Heatmiser sell an opentherm mini hub that will control 2 zones with 240v relay to zone valve. The opentherm is done by output from the mini hub to boiler. So you could buy another neoair to replace the t6r and then wire up the minihub. The other alternative is to use EPH CP4 combination if you're not using a heatmiser wiring centre - with the cp4 you just have 2 stats with receivers with one receiver set up at the hub unit which is is wired to the boiler with opentherm. Oh, and especially if you're running a low temperature heating system (i.e. 55C or below), make sure the installer has actually installed the UFH with hydraulic separation, otherwise you'll probably end up with balancing problems between the radiator system and ufh. HTH -
I've got a retired electrical engineer doing the 2nd fix electrics with me but passed me on to another guy to install an ev charger in our remote garage. Unfortunately, this one has disappeared into one of those trades black holes and just doesn't get back to me. I have a problem because I've got open trenches partly used for national grid to install my permanent supply, but also to take the cabling down to the garage. So, my plan is to just install this with the retired electrical engineer and then get it covered with the part p inspection. question is, what stuff do I need to install the infrastructure now and for the future? I'm putting in 25mm cable and the sparky who was supposed to do the job mentioned its useful to have a control cable, but I don't know what this is? Can someone here list everything I need from my meter tails to the ev charger, so I can get these trenches filled in and stop getting hassled by my wife about getting a proper charger instead of the wall plug? Thanks!
-
No connection on boiler to receive wiring centre - what to do?
SimonD replied to sb1202's topic in Underfloor Heating
Yup, this drives me mental. I did an instal (natural gas) a while back where the owner was doing a deep refurbishment. I put in the boiler with modulating controls etc. and said she should call me when it's time for the ufh. However, the guy doing the floors, ripping them out and properly insulating them etc. never called me and did it himself with some other plumbing/heating muppet. Then winter came and the customer called me to say house wouldn't get hot. its a tiny cottage and they'd zoned it all up, then thrown away the brand new modulating controls for cheap shite relay ones and the system constantly short cycled. The circle completed with me tearing all their crap out and putting back modulation. Hey presto no short cycling. Makes my blood boil... -
No connection on boiler to receive wiring centre - what to do?
SimonD replied to sb1202's topic in Underfloor Heating
TBH the installers could have made their life easier by just using a heatmiser UH-8 as that can also control rad ch and dhw, and then no need for the abovementioned Navien wiring centre which I assume is just like the widely used Honeywell and Drayton standard wiring centres. It would also be a lot tidier I think. -
No connection on boiler to receive wiring centre - what to do?
SimonD replied to sb1202's topic in Underfloor Heating
Yes this. I'm really confused. The installation manual clearly shows switched live from wiring centre to boiler terminal 4 on CONM4. This is connected to the two orange switched lives that come from dhw and ch 2-ports, which is standard in the wiring centre. So to add ufh, there will be a switched live from the ufh 8 zone wiring Centre, which is sometimes volt free and just needs a bridge to com on the wiring Centre itself, and Bob's your uncle. Given the thread, this seems too simple. Or am I missing something? Some electricians too 😉 A customer of mine had new ufh installed while I was away last summer and then emailed me when i got back to say that neither the heating engineer nor his very competent electrician could get the ufh calling for heat to the boiler. It took 10 minutes 😁 I was tempted to say it was a very complicated and expensive call out but went easy on the electrician, who was there when I sorted it 😀 -
It could just be the fan. When you switch on ufh fan speed increases slightly to compensate for addition load.
-
Yes. Like the figures I posted earlier, this provides the best output. Radiator manufacturer figures are usually based on Top and Bottom Same End. But remember that rad output depends on the air temperature differential too. So for example with a flow temp of 70 with return of 50 you have a mean water temp (mwt) of 60. Mean water - air temp differential is then mwt - air temp so output differences between 21 degrees and 16 degrees are as follows: 60-21 = 39 60-16 = 44 To get the actual radiator output you then divide this by the manufactures delta, usually 50 so: 39/50=0.78 44/50=0.88 This means that with a room temp of 21 the radiator output is 78% of catalogue and with 16 degrees it's 88% Which clearly shows that even just 5 degrees has a big impact on output. You then take these results and multiply by the connector emissions factor which for TBOE is 1.05 or 0.96 for BOE Plus there are other factors used for the whole calculation.
-
Boiler short cycling with low flow temperatures
SimonD replied to seanblee's topic in Central Heating (Radiators)
Yes, but is it useful to believe its all down to delta T, even for general public and enthusiasts without also understanding the implications this has on heat output and mass flow rate and how this impacts the function of the system as a whole? By definition a lower delta T distributes less heat and therefore requires higher flow rates for the same output, some of which are impractical. And then with radiators heat transfer is based on Mean Water Temp to Air Temp differential as shown by the spreadsheet above so many radiator systems just won't work at low flow temperatures. Yep, maybe it's a sheesh post......😉 -
Boiler short cycling with low flow temperatures
SimonD replied to seanblee's topic in Central Heating (Radiators)
yes, they must be, but like most Heatgeek blogs, the nuance of all factors required to get a heating system working are missing, giving what I think is a misleadingly simplistic account, even if the principles are fairly simple. A lot of the figures above simply won't work very well with radiator systems without impractical modifications. -
Sounds like the system needs purging which could also account for poor flow through some of the loops. Then a need to balance the loops. If this is a new/ish system is there a technical manual showing the theoretical flow rate through each loop? Setting them to this would be a great start.
-
Doesn't instill much confidence, does it? But yes, Opentherm is supported with the 050-W and 100-W which are plusbus, weather comp or opentherm, or relay. With the 200-W it's plusbus or canbus and you'd probably go weather comp. You can even add opentherm to many older 100-W with an X21 wiring harness for less than £10.