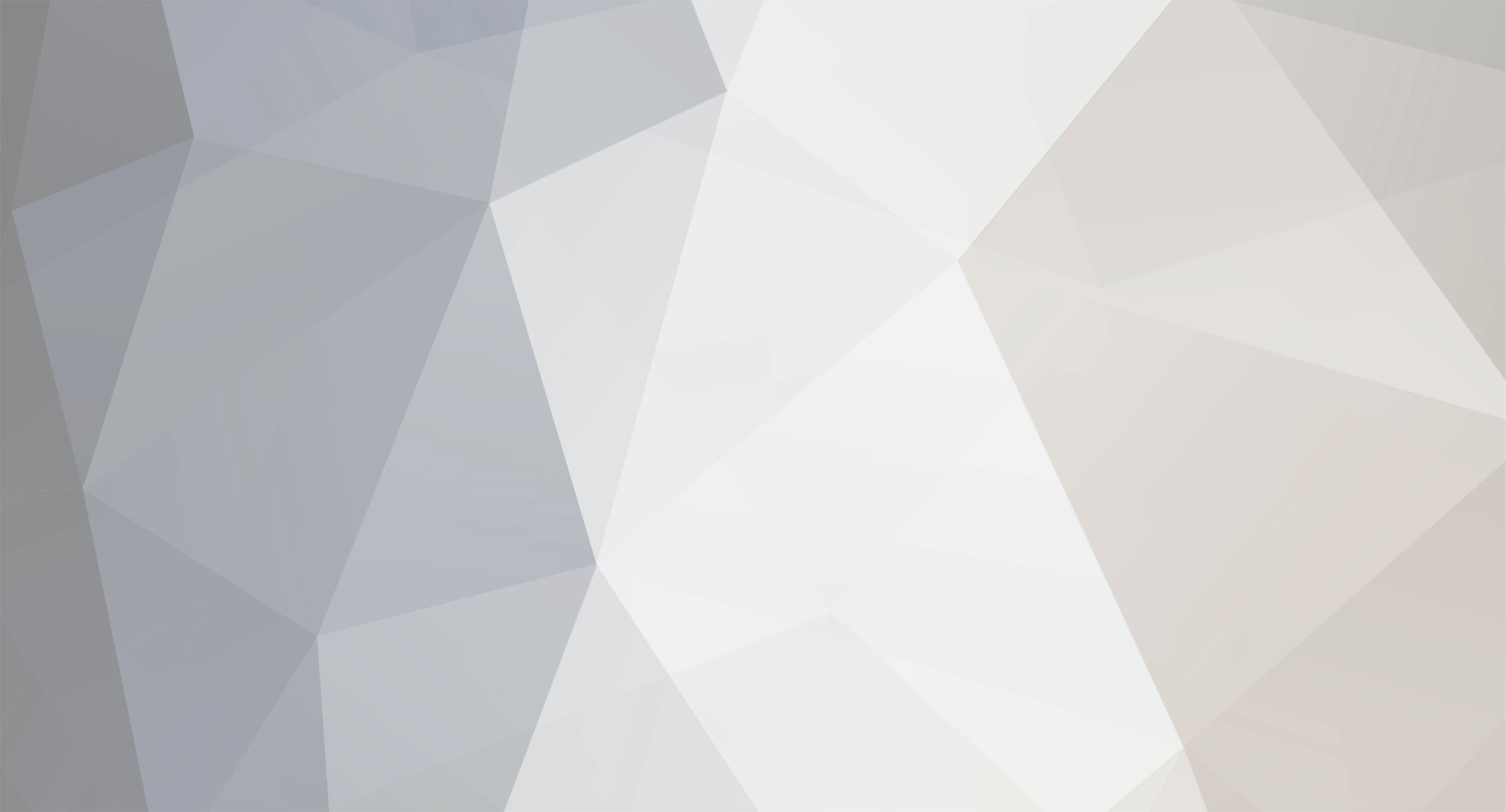
Nick1c
Members-
Posts
267 -
Joined
-
Last visited
Recent Profile Visitors
The recent visitors block is disabled and is not being shown to other users.
Nick1c's Achievements

Regular Member (4/5)
46
Reputation
-
Hi, We built a house near lands end, overlooking the sea. It’s a great place to be, but has its challenges - salt, wind & humidity being chief amongst them. Anything that can corrode will, & at a frightening rate, so it is worth ensuring everything (including window & door hinges/ furniture) is warranted for a marine environment. Airtightness is key, it will minimise heat loss from wind wash & make it easier to control the internal environment via managing the ventilation. This extends to the window/ door seals, in our first week in the house we had 70+mph winds straight off the sea onto the house, this forced some water through the seals, but thankfully it drained out through weep holes. Heating is underfloor via an ASHP, we have only one zone per floor and it works well. Good luck!
-
Habito, Fermacell, OSB & Plasterboard, Ply & Plasterboard, or…..
Nick1c replied to G and J's topic in Building Materials
We had them fitted. Where the sheets butt up is great, it’s the cut edges I am referring to. We have no architrave or skirting which obviously massively exacerbates the problem. As far as I could see if you use beads to clean up the edges you would then have to use a conventional skim rather than the FST. -
Habito, Fermacell, OSB & Plasterboard, Ply & Plasterboard, or…..
Nick1c replied to G and J's topic in Building Materials
We went for fermacell walls & PB ceilings due to both the weight of fermacell & the lack of requirement for impact resistance. The insulated timber frame was supplied by PYC & used smartply on the inner face. It feels really solid, is great to hang things off & adds to the racking….but the edges aren’t as clean as I had hoped. I am not sure how to make them super sharp, maybe FST on all the edges would work. The house is remarkably quiet, the combination of warmcell, a CLT first floor & (possibly)the fermacell) really works. -
It’s worth bearing in mind that it is common for push fit insulation to be fitted less than perfectly, this can result in a dramatic reduction in performance. Blown insulation is less likely to suffer from this. We went for cellulose partly for this reason, partly for the noise attenuation (which is fantastic) & partly for decrement decay.
-
Doesn’t covering the blockwork with a cement slurry do the job?
-
We went for Fakro as their 3G unvented units were cheaper than the equivalent Velux, 2 are motorised to allow for cross-ventilation. The motor in them is slooow relative to the Velux ones we had in a previous house, but the rain sensors work well. One of the motors stopped working a year after we moved in, but slightly over the 2 year warranty period since they were bought. It had been used less than 20 times in that period. Fakro’s technicians were great over the phone trying to find the fault, but once it was determined to be FUBAR they came back with a quote for replacing the motor of £600 - £300 each for parts & labour!! I pushed quite hard to get this reduced, the only ‘concession’ I managed to get was that someone would talk me through fitting the motor myself as it is apparently a simple operation. On the basis of my experience with their product support I would not recommend them.
-
I doubt that your project would be of sufficient scale for you to be treated as a wholesaler by manufacturers. In the event that you persuade them as a small unknown buyer you will be offered their worst terms (price & payment), even if you are buying by the artic-load. Transport costs have skyrocketed (along with demand for building products), managing logistics & customs would be challenging. As a self- manager of the project organising labour will be like herding cats. A job requiring a week’s labour from each of three trades could easily take over two months….. once you have found people to do it, which itself could involve several months wait. I have almost finished a self-managed build, it has taken well over twice as long as it could have if it moved seamlessly forward & has cost considerably over £2k/m2 (all costs, inc. fees & demolition, exc. plot). Access wasn’t ideal, the ground was good. The design could have been more cost-efficient (but we like it), the spec is pretty good, but not extravagant. There is a fine margin between confidence/optimism & delusion, misjudging it could be very costly.
-
My understanding is that houses with a high volume of air per occupant are likely to become relatively dry with ‘standard’ MVHR , particularly in winter when the RH of the incoming air drops as it is warmed up & the moisture generated by the occupants can’t bring it back up enough. An enthalpy exchanger in some way recycles the moisture recovered from the stale air keeping things more comfortable (as a result no condensate drain is needed). We had one put in our Zehnder Q 350 as there are only 2 of us in the house for the vast majority of the time & if done at the time of ordering the additional cost was negligible. We live on the coast & our local weather station rarely shows the RH below 80%, the house sits around 60%. It may be a waste of time, but I get eczema which is worse when it is particularly dry so didn’t want to risk it.
-
When we lived in Sussex I tried to get some reclaimed flooring kiln dried to speed things up. No one would do it as they were making full use of their kilns for themselves. I suspect they would need a large quantity to even consider it & then jack the price up, particularly given the demand for materials atm.
-
Bathroom Furniture/Suite Supplier Recommendations
Nick1c replied to Matt60's topic in Bathrooms, Ensuites & Wetrooms
Pre-Brexit I bought all the sanitary & brassware for a complete house renovation (2 bathrooms & a cloakroom) & an en-suite extension, both from Reuter Bad in Germany. It has an enormous range, the prices were competitive, the communication great, the delivery faultless….. Post-Brexit they now don’t deliver the the UK. Our new home was due to be started around the time we left the EU so I planned to do the same before our glorious leaders closed the stable door & put it in storage. As I was about to push buy the January sales started so I checked with CP Hart the costs of the sanitary ware as I thought transport costs from Germany might outweigh any savings for these items. Much to my surprise they price-matched the Germans! If I was buying now I would check products & prices on Reuter & Megabad & use them as benchmarks for the UK. Our local showroom also price-matched some on-line shops so don’t ignore them. -
We had something similar after a storm, it turned out that it was due to damp getting into an outside socket on the same circuit. No idea how it was checked / sorted out.
-
Getting hold of Bt
Nick1c replied to Russell griffiths's topic in General Self Build & DIY Discussion
You could try the bt forum, I got contacted by someone who moved things along when I posted there. IIRC you also get given an individual contact (& their email/phone no.) so get some consistency. -
Our main room is open plan & the original intention was to have engineered boards in the living area & tiles in the kitchen. We were told by the retailer (waxed floors) that he had customers with his flooring in kitchens for over 10 years. 2 1/2 months in & ours is still looking good, I’ll give you a definitive opinion in 9 1/2 years! Ours was factory sealed, laid & then I put another 2 coats of osmo on it.
-
I put a solar powered fan in the roof of my van. Obviously no good at night, but helps keep moisture levels down. Are you sure you have no leaks?