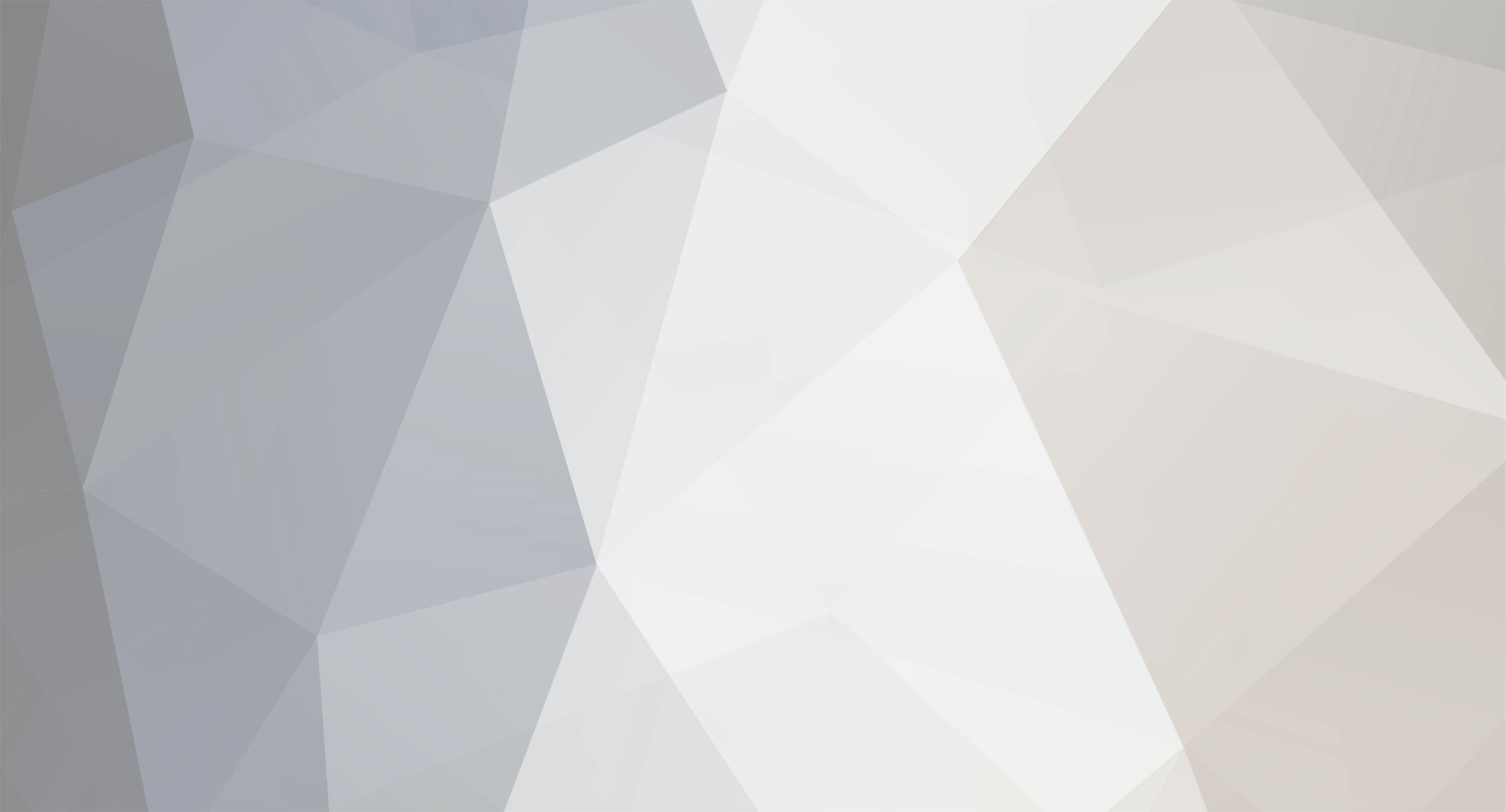
George
Members-
Posts
699 -
Joined
-
Last visited
-
Days Won
1
Everything posted by George
-
If the walls are in-plane vertical then I'd be inclined to reapply sealant, repoint the crack and put a crack monitor on to see if it's seasonal or worsening. Most of the movement has been taken in the MJ and if it were just that it really wouldn't be much of an issue. But for some reason it stops two courses above ground level.
-
Just buy what document I need, when I need to buy it. Subscriptions only make sense for large organisations.
-
I'd keep things as they are until you can do the thing properly. Removing half may destabilise it.
-
Is chimney flashing usually like this? Just wondering.
George replied to Gone West's topic in Demolition
Not typically historically where it's essentially just a stack of bricks with an internal parge coat. But modern chimney construction do have trays at the roof line and at the top of the chimney. Wouldn't worry about it. They just went belt and braces to make it watertight. -
Padstones aren't usually necessary for lintels because the spans are shorter (so the reaction loads are less). Looking at that photo, the bricks appear to be solid and not on a perpend joint so shouldn't be an issue.
-
Usually bedded into mortar with slate to level if needed.
-
New opening steel beam and pitched roof snagging
George replied to Alistair Shaw's topic in RSJs, Lintels & Steelwork
It really needs a structural engineer to do an inspection rather than a builder. Sometimes joists hangers are needed, sometimes skew nailing is acceptable. Similarly for the ledger plate connection (although the single lone fixing definitely looks a bit weedy) and padstone questions. If there's a steel presumably there are structural calculations available so it's not starting from scratch. -
Anything is possible with enough cash.
-
Yes but the use of agricultural land to avoid inheritance tax seems to be a more recent trend. A cap or stronger limits that the owner is actually farming would help.
-
Agricultural sector doesn't have the cash to pay 40% of the estate every 20 years or so. And the subsequent devaluation of land may make paying an inheritance tax impossible anyway. Realistically you'd probably find that land is owned by large corporations which then becomes landlords for tenant farmers. Essentially the corporations will become the Lords of the modern world. But experience around the world shows that owner occupiers make more efficient use of agricultural land. Actual profit margin is around £200/hectare, depending on many factors. So more like a century or two.
-
Ehhh brickwork cracks. I'd suspect leaking or broken drains being the most probable cause. Check them, repoint, maybe crack stitching and crack monitoring should be enough. You'll never be able to eliminate the worse case causes from visual inspection alone but they are unlikely.
-
It'd cause glorious chaos in food production if that were introduced. Mind you, the likes of Dyson and others shoving their money into farmland does make things harder for actual farmers. Value of land Vs income from food production bears little relationship these days.
-
House retrofit, knee wall/roof structure
George replied to HugoR's topic in General Structural Issues
Are they wobbly? -
What fixings may I need to stop leaks?
George replied to David001's topic in Roofing, Tiling & Slating
Thanks - didn't know about the lap screw. Corrugated fibre cement is still a popular choice for ag buildings. -
What fixings may I need to stop leaks?
George replied to David001's topic in Roofing, Tiling & Slating
Can I just check my understanding... for square sections you don't put fixings through the crown, only tight into the flat sections. For corrugated roofs it's the other way around and the fixings only go through the crowns. -
Balcony leading to flat roof....does it need fall protection?
George replied to Thorfun's topic in Flat Roofs
Oh it just sounded like there was more you could say but I wasn't expecting a name and shame exposé on BuildHub. -
Thanks It'd depend on where the internal walls are. If there aren't enough internal walls (allowing full roof trusses to span across and support the dormer) then you likely need steels to provide a ridge beam and dormer support. So it might depend on the internal layout and your neighbours might have something different that does allow it to work.
-
Piled foundations and private drain question
George replied to JackOfNoTrades's topic in Foundations
Ideal would be to excavate around and provide shuttering over the drain and backfill when the concrete has cured. This is to prevent the wet concrete damaging the drain and you know the surcharge hasn't damaged it during construction. -
I think it is unlikely the piers would pull out (although would have to run the calculation to be sure), but there is a lack of bracing in the walls and roof, and no holding down / restraint straps in the superstructure (roof, walls) down to the foundation. For 100mph gusts on a lightweight roof every rafter will want some sort of strap.
-
Balcony leading to flat roof....does it need fall protection?
George replied to Thorfun's topic in Flat Roofs
Ooh tell us more. There is CROSS for anonymous safety reporting as well. -
They can block around and lintel over. I've be tempted to get the brickies to build a closed cavity (build blocks across the end of the cavity) where the drainage pipes are, to act as the formwork for the cavity fill.
-
Balcony leading to flat roof....does it need fall protection?
George replied to Thorfun's topic in Flat Roofs
I think if it was steel structure, say forming a u shape back to the sides then it's a straightforward design job. The devil will be in the details. Usually edge protection is not designed to that detail by the SE - essentially the supplier would do it using whatever standard system they sell and the SE checks the forces on the main structure. -
Balcony leading to flat roof....does it need fall protection?
George replied to Thorfun's topic in Flat Roofs
The Building Regulations can't cover every eventuality but it'd be Part K. I would say that because there is no fall risk along that edge then you do not need the full edge protection. It would essentially be a 'demarcation' barrier. However, I would make the demarcation barrier suitable for p3.3 in Part K - that is, it can't be climbed over/defeated by children. So it'd basically have to be full edge protection except for the full restraint forces... so in reality, probably just the same as along the other two edges. Note that the flat roof area does need to comply with p3.4 as green roofs do need occasional maintenance, so be prepared to justify the lack of guarding on that section of roof. -
Class Q permitted development post May 24 changes.
George replied to Leroy's topic in Planning Permission
Do a walk round with a structural engineer, they might have a few suggestions on repairs to carry out.