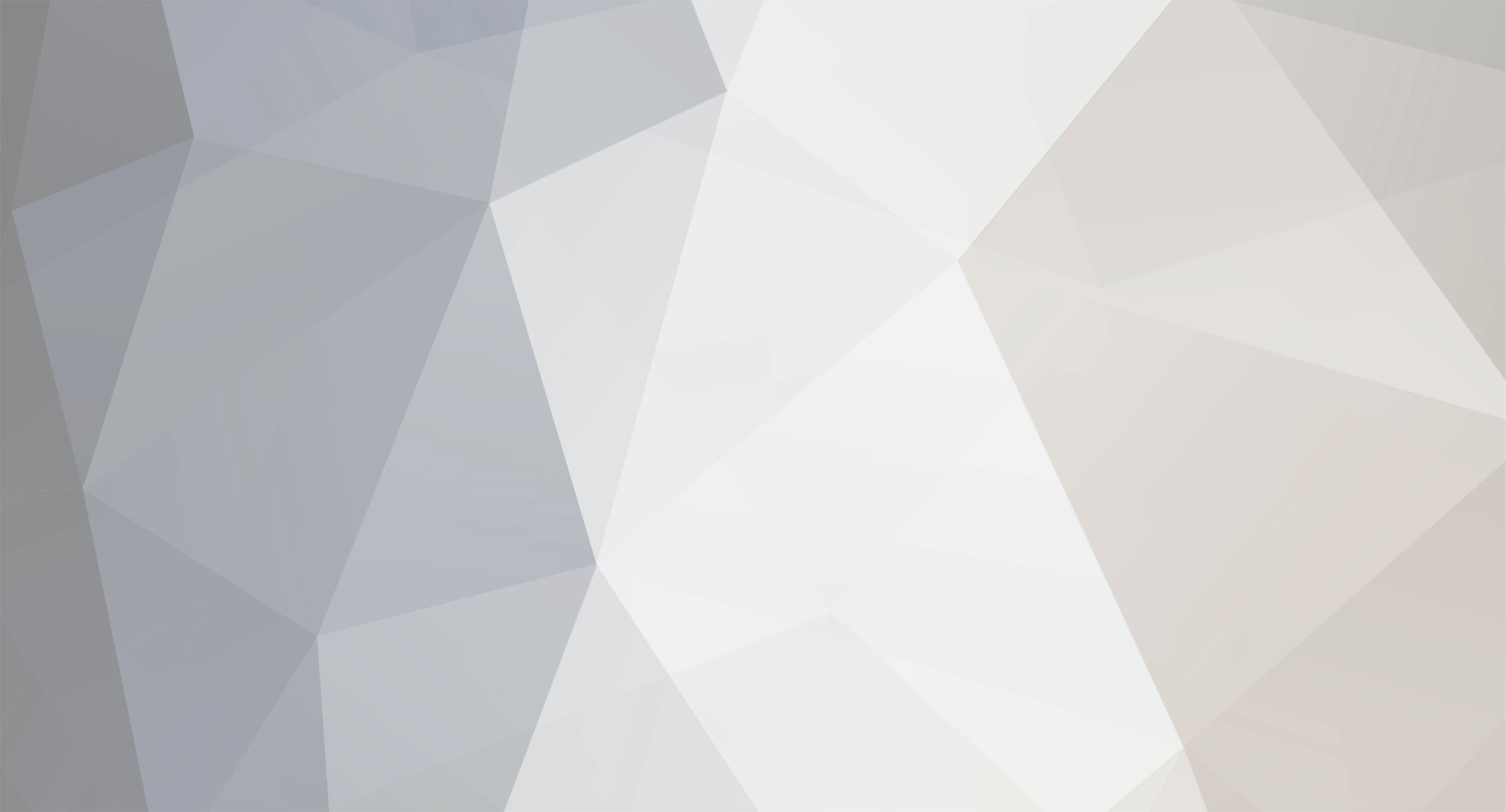
MortarThePoint
Members-
Posts
2050 -
Joined
-
Last visited
Everything posted by MortarThePoint
-
I used the same compression coupler in the other bathroom and it leaked at first so I'm keen to rule that out
-
I've got too many branches etc to do an air test I think. What I'd like to do is block the 40mm with something and do a water test as that would test the trap too. Is there something I can use to block the 40mm having been inserted through the tee?
-
I've got a bit of 40mm waste before the stack that includes a straight coupler (compression), tee, elbow and shower trap. I want to test all of this is ok, but not sure how to. I could easily check similar in another bathroom where the stack wasn't installed fully and I used a stop end in the partial stack. Here the stack is installed all the way to underground. The pressure will be too much to block of the stack at the bottom. Is there a sensible way to test it just in the 40mm pipework? Photo attached
-
Posi joist - This install feels rubbish, thoughts?
MortarThePoint replied to boxrick's topic in Roofing, Tiling & Slating
I don't know what the correct method for bearing a sloped beam on a pad stone is. I can imagine welding or bolting a steel 'wedge' under the end of the beam, but would be interested to know what the answer is. Has the SE now provided a detail drawing? -
Posi joist - This install feels rubbish, thoughts?
MortarThePoint replied to boxrick's topic in Roofing, Tiling & Slating
I know very little about renovating, but careful since if you replace the wall the U-Value may need to improve which couldn't be achieved in just the cavity. I guess you'd need insulated plasterboard. BCO may not be fussed though since the wall area is so small, but may be worth getting a verbal confirmation first -
Carrying wood on top of van roof.
MortarThePoint replied to gavztheouch's topic in Building Materials
I'm surprised this would be worth your effort cost. If there are dual carriageways/ motorways involved there is logically a closer option. It'll cost you about £30 of fuel I'd have thought. Easy to get that timber <= £0.85/m. You'd need to be getting about 500m of it for free to make it worth it (Inc time cost). That would weigh about 500kg which is way over that the roof capacity is likely to be. Roof capacity might be up to 250kg so 250m, even that feels pushing it. Assuming £20/hour and £30 fuel you'd be paying about £0.52/m just for collection. -
Posi joist - This install feels rubbish, thoughts?
MortarThePoint replied to boxrick's topic in Roofing, Tiling & Slating
I've always defined Stress as Pressure without Control. Well done, you've taken control and soon this will be behind you. Sort everything now as it wears on you otherwise, but it looks like that's your plan. Cut corners compound, so you're right to be taking things back. In the first picture from last night (unreturned wall), the lintel over the exterior door looks to have less than 150mm bearing. You're probably already on it, but do check. It would be another example in your catalogue of evidence if needed. Strange collection of block types in that wall too. Good to hear you're taking it down. -
T&G chipboard flooring fixing over ply diaphragm
MortarThePoint replied to Rick734's topic in Floor Structures
I'm pondering what force the nail from the nail gun would clamp the plywood to the joist with in that first gluing operation. I'm much more familiar with screws, but I expect the nails should make for a tight joint which is what you need to avoid an excessively thick glue layer. The Chippy will definitely want to use his nail gun for this bit so I wouldn't be suggesting screws unless someone more knowledgeable than me has concerns. -
T&G chipboard flooring fixing over ply diaphragm
MortarThePoint replied to Rick734's topic in Floor Structures
Gluing and nailing the plywood feels OK, but I'd glue and screw the T&G to the plywood at the joists. Then the screw is clamping both the plywood and the T&G to the joist. So yes it's gluing the T&G to the plywood, but only at the joists. I'd also glue at the T&G short edges if not at joists, already gluing if at joists. That would add strength and may avoid need for noggins. -
T&G chipboard flooring fixing over ply diaphragm
MortarThePoint replied to Rick734's topic in Floor Structures
Curious as to why the SE has specified the plywood at all. Squeaks come from rubbing and if both the plywood and the T&G are glued at the joists there shouldn't be any scope for rubbing -
Self build laziness
MortarThePoint replied to Pocster's topic in General Self Build & DIY Discussion
I've wasted many hours going round merchants to get the odd thing here and there. I think my appetite for not getting in the car extends to about £6. How much is the the Toolstation rapid delivery? -
Air tightness advice required for masonry build
MortarThePoint replied to ruggers's topic in Ventilation
Key areas as we wet plastered the walls. If we'd gone for and dab I'd have fully covered. We have a membrane on top of precast concrete GF subfloor so I painted from that up about a block's height (225mm). The FF is hollow core (HCF) so painted about a block's worth down from that to encompass the ceiling void. Focused on joints between HCF at walls, perhaps should have sealed along whole joint. On FF painted up from HCF about a block's worth and down from top of wall plate about 150mm. Also painted up floor to ceiling all wall corners. I used Intelligent Membranes tape on windows followed by Passive Purple and then their Pink Grip. +1 for Adam being a top bloke. We don't have MVHR and am not aiming at PH standard, but did want to do a reasonable job of air tightness. -
Air tightness advice required for masonry build
MortarThePoint replied to ruggers's topic in Ventilation
I've used Passive Purple quite a lot Aero barrier looks interesting, but I'd worry about my windows getting covered in gloop -
It looks like a great approach for lightweight buildings like garden offices. I'd want the load spread a bit more than they appear to though. Looks like tops 200mm diameter hole every 1.2m which makes for a pressure of (1.2m*1.2m*1.5kN/M2) / (3.14*0.1m*0.1m) = 69kPa Which I expect would high to bear in the alluvium
-
You can get a funny looking spread base for Sonotubes as well: Metal music not mandatory
-
I've started another thread about a different approach that doesn't suit your desire for a more substantial foundation, but is interesting:
-
Another thread (link below) made me wonder about simple garden room foundations. This led me to discover the Rod System which looks interesting. Does anyone have any experience of the long term stability. The rods are concreted into the ground and don't go very deep so that makes me wonder. The loading won't be high, but would be interesting to know. Could be made adjustable for later correcting any movement but that doesn't appear to be done. In the US, you often see people using Sonotubes which are e.g. 12" cardboard tubes put into an augered hole and filled with concrete. These can go much deeper, but could still have a rod system at the top, though that's not how the US guys seem to do it. They have the tube/concrete stick out above grade and then bracket or bolt the timber directly to the concrete. It's cheap to hire an auger machine in the US due to how common this approach is (e.g. for decks). Flexible approach: Example of fitting timber base onto rods: Close up of parts: Another example: Sonotubes:
-
Consider a raft Foundation: https://forum.buildhub.org.uk/topic/12840-outbuilding-foundations-raft/ What you've dug already could be a large ring beam
-
Edmundson are good and can normally work on the price for you. The key is volume. Making fewer bigger orders. There are also some good online only options. Careful though, you'll pay a lot of attention to cable prices which are normally well matched, but it's all the other bits where they claw back margin. I've paid an eye watering price for SWA glands before with a shrug from the guy at the counter.
-
Opinions on best way to drop a ceiling
MortarThePoint replied to Thorfun's topic in General Construction Issues
I've seen the Casoline system one the website before and it's what the architect suggested. If I recall it has a larger minimum void. Gyplyner worked well. I used brackets like GL9 under concrete which worked well with concrete screws and packers to tweak (default 3mm then fine tuned later as needed). I don't know requirements of flats -
Associated costs of self-build mortgage.
MortarThePoint replied to flanagaj's topic in Self Build Mortgages
Mixture I think. I've been happy with my independent one. Strict but very helpful -
Associated costs of self-build mortgage.
MortarThePoint replied to flanagaj's topic in Self Build Mortgages
Building control can be carried out by private companies too which has injected a bit of 'customer service' into both the private and LABC -
Oh dear, I've made a mistake here then. Painter is in and busy painting and I am a while away from having doors on site let alone hung. I guess that leaves me these options: Fit the door stops where I hope they should be and let the painter at them Have the door linings painted along with the architrave and skirting, then fit painted door stops later and hope the joint can then be tidily painted over to make the join disappear Somehow not paint the door lining face (i.e. the bit shown red below)