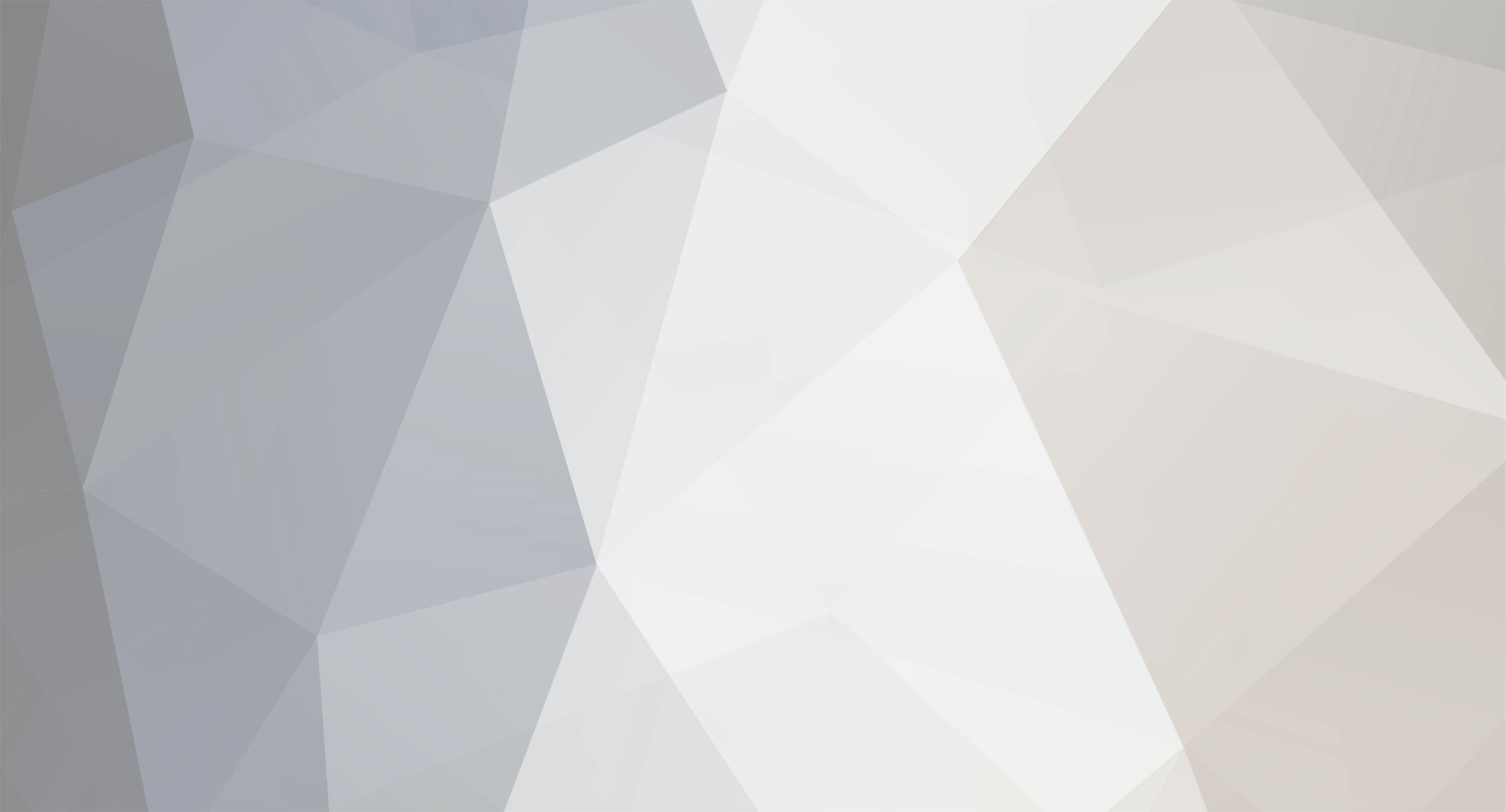
ruggers
Members-
Posts
283 -
Joined
-
Last visited
Personal Information
-
Location
NW England
Recent Profile Visitors
The recent visitors block is disabled and is not being shown to other users.
ruggers's Achievements

Regular Member (4/5)
17
Reputation
-
The builder has said the house to garage fire door has to be installed on the garage side of the cavity wall, is this correct? My current home has it on the inside but this was built 15 years ago and building control were a bit lax. Do i need a special fire rated casing?
-
I need some weeps for my grey facing brick perps to go above the trays. Theres the taller thin cassette type, roughly 10mm x 60mm Or the peep weeps. What are most commonly used? Looking at muck drop off from the builder I'd imagine a much higher chance of a peep weep getting blocked. The grey ones are the exact same colour as the brick.
-
I've found in my current home with same integral garage, that having the outside walls also insulated slows doen the release of the heat lost from the house and the temperature in the garage is never less than 11 degrees on the coldest day. Issue is needing a fire door between utility and garage loses a lot of heat. I trued to find an insulated airtight fd30 to no avail.
-
Would my original sketch not be a better set out so the dpc is external to the building. There will be 100mm insulation in the garage walls too and 50mm insulated sectional door on the garage. No side doors to outside, only an internal door to utility room.
-
Thanks Nick. I suppose the foams for minor insulation and in this case not required, so just keep the gap to a fingers width, bed the 100mm dpc under the lintel on the inner leaf and then run a bead of adhesive on the wall and stick the dpc to the cavity side of the inner leaf. Then let the mesh bridge the gap & K rend TC 15 over both. Could always add some low expansion gun foam between the dpc and returning block to help support the mesh bridging the gap if needed.
-
Thanks guys. I just wanted to check while im at the setting out stage for inner leaf dpc course. I understand the princliples of heat loss for the thermal envelope and setting windows back, fully insulating reveals etc, but wanted to make sure the garage was being done the best way to prevent the cracking you refer to. Builder wanted to leave open and upvc over it but i said its a bit ugly. Ive had them hairline cracks on my current garage reveals. So having never used the vertical dpc foam insert, can you tell me how its installed and is it just one thickness of foam bonded to dpc? Is it a compression fit installed when the lintel goes in with the top being bedded in under the lintel?
-
I need advice of the best way to close off my garage door reveal for finishing plaster. I'm building a house with an integrated garage which sits under a first floor bedroom. The build is partial fill cavity 100 block, 100 pir, 50 air gap, 100 face brick. I'm aware of thermal bridging using the returned block method, and wont be doing this on the rest of the house, but would it be the best option for my garage door reveals to provide a solid backing for rendered reveal, or what other options do i have? Upvc i think will get scuffed over the years in anthracite. Adding plastic cavity closers could be flimsy and would likely require a lot of mesh? Rendered reveals would be sand and cement, or k rend tc15.
-
Below DPC level detail advice needed for new build.
ruggers replied to ruggers's topic in Foundations
I'm following on doing the insulation so i get the opportunity to do my best with it. The house is started so I can't change the cavity size and no one uses blown bead where we live. It's not suitable for facebrick outer skin in wind driven rain areas, only with render on. I've not seen driterhm before. Everyone local uses PIR partial fill or timber frame. -
Below DPC level detail advice needed for new build.
ruggers replied to ruggers's topic in Foundations
Thinking back to this. How tight is the tongue and groove fit, is it too snug to pass DPC roll between the joint to bed onto the inner skin and then step down to outside DPC level? Cutting the tongue off flush effectively making one side a square edged board to allow DPC to pass between may be an option. -
Below DPC level detail advice needed for new build.
ruggers replied to ruggers's topic in Foundations
@Brickie So it is recommended that I include this stepped DPC around the house perimeter from the outer leaf DPC level (on top of telescopic vent) which is 150mm above ground level, to 225mm above inside finished floor level? The same as figure 26 NHBC image I attached on an earlier post? But rather than slice through the PIR at an angle, just pass it between the PIR joint. This would produce a steeper angle on the DPC roll than splicing through the PIR, but still direct wind driven rain back out through the weeps and prevent pooling in the bottom of the cavity? -
Below DPC level detail advice needed for new build.
ruggers replied to ruggers's topic in Foundations
I wouldn't like to fit it as a builder daily. On this occasion I'm following on from the brickie to install this so they don't have to worry about the hassle and I can be fussy with cuts, corners and chamfers over lintels. -
Below DPC level detail advice needed for new build.
ruggers replied to ruggers's topic in Foundations
When you say come out across the top of a PIR sheet, do you mean a DPC roll as a Z shape so it's bedded into the inner and outer cavity walls and spans as far as you roll it out? I agree, trying to split PIR at obscure angles would be terrible. I'm also using T&G PIR and taping joints so thought the plastic Type E or type G might be a way to divert any rain water back out if they have a profile thats the width of a facing brick then the back lip can angle up and rest on the outer face of the PIR. I wasn't sure if trays are ever used at DPC level but doesn't seem as if they are, but how else can water escape out below FGL? Only other thing I can think of if the trays are a bad idea, is to lay a land drain up against the outside wall for the full house perimeter, set to the same height as the lean infill and direct water away to garden or drains. Maybe drill some holes between the bottom of the perps level with the lean infill too. -
Below DPC level detail advice needed for new build.
ruggers replied to ruggers's topic in Foundations
A stepped DPC in the cavity directing any water back out through weep vents won't work because it would divide the PIR insulation. I'm aware that angled cavity trays need positioned over the telescopic vents. Would it be advisable to fit Type E horizontal cavity trays at outside DPC level right around except under window openings, some like the image? I calculate 40 required at 900mm, £280. Might seem like over thinking but where else can the water go. It doesn't move on site summer or winter. -
Detached house build - I'm wanting to check, how wind driven rain will leave the cavity once it comes in through the facing bricks if outside finished ground level is 300mm higher than the bottom of the cavity. If the cavity fills by 75mm, it will breach the DPC under the beams. Ground is all clay soil and poor drainage until land drains are completed. Render doesn't let water in but bricks can be quite a lot. I have my beam and block floor in and next stage is to complete the partial fill cavity walls up to DPC level. It's ready for outer leaf block & 3 course of Staffordshire blues, then I can get the outside to finished ground level, some drains in, stoned up clean ready for builder and scaffold. My plans were very generic for the DPC area, a few versions had been sent and none were suitable for B&B. I've attached a sketch of the buildup I decided to go with.
-
Theres too many figures and a bit too confusing for me to calculate. MVHR ACH, Heat loss survey ACH which very depending on the room use from 0.5, 1, 1.5 ACH. The lower the number the more it reduces the heat loss for the room. then theres the air permeability score too. Are you saying 2m³/m² @ 50 Pa is much higher than a natural windy day? If so, why are they testing at such a rate? The MVHR I'll be installing, but it will be designed by ADM and commissioned by them. They calculate it all to comply with English regs and satisfy B.C MVHR isn't to be considered in any heat loss calculation I've been told by a lot of heat engineers and read it online. Reasoning being, the building has to be be sized to heat from cold when theres no heat to recover. Including MVHR in the calculations would result in smaller heat emitters and it would take much longer to reach desired temperature from cold. It's 5.1Kw without exposed area, I can't see it being lower than this. You have massive amounts of insulation compared to what I'm putting in. Mine will be: 100mm T&G PIR in the cavity, taped and self installed. 0.17 W/m2k 400mm loft insulation 0.11 W/m2k 170mm PIR floor 0.12 W/m2k And intermediate floors and stud walls too which I've added, but it makes no difference when all rooms are sized the same for 21C at -4.4C with a MWT of 37.5C A friends family had an identical house size & layout, built in 2006, it never had MVHR, will have had 50mm PIR vs my 100mm, and probably poor air tightness, they always had the heating on, but said it cost a fortune to run.
- 19 replies