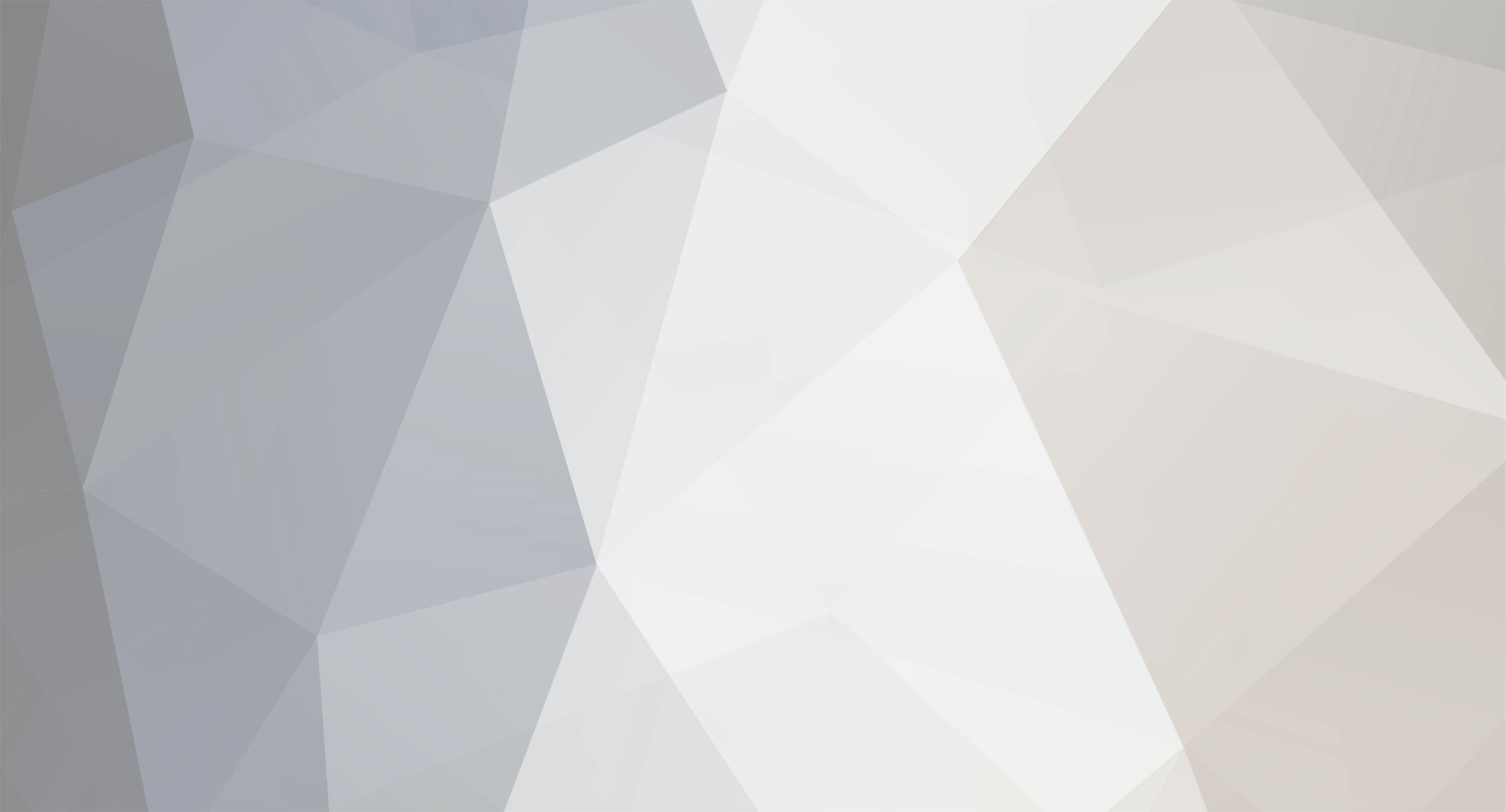
MrP
Members-
Posts
33 -
Joined
-
Last visited
-
Days Won
1
Everything posted by MrP
-
I would always recommend use of non corrosive fixings for external applications. Even though they are unlikely to get 'wet' there is always going to be risk of some moisture penetrating over long periods. Stainless steel nails are freely available for nail guns, a little more expensive but definately worth the extra in this case.
-
Just a heads up on the green pb, British Gypsum actually advise not to skim the board when tiling an area. From memory the rating almost doubles in regard to how much weight of tile the board can carry when it is not plastered as you get better adhesion of the tile adhesive direct to the board, particularly useful if you are using a stone tile or large format porcelain. Plus you save on money not plastering the area also .
-
I can absolutely assure you that is not the case, there is no guidance that allows for spot inspections and there are pretty strict guidelines BCO's and all inspection records have to be made available on request. The only thing this may apply to is air tightness testing which can be done on spot check regime. I can't say this does not happen at all as there is always going to be rogue inspectors, the same as poor builders and every other profession. You would be amazed at the level of monitoring and auditing as a BCO.
-
Private building inspection services is the key and i include the LA in this. All Approved Inspector bodies have a commercial pressure and this is always going to affect the impartiality of the inspection service. I am not a fan of nationalisation but I do think in this case commercial decisions need to be removed from building inspection services. The danger here as I am sure many are aware is how this then is run. We all know how many government departments are run and managed. I don't see a particularly improved situation with this either. Consumer protection has to be the key driver - it needs to start hitting the builders in the pocket before anything will start to change.
-
Any mineral or rock wool, including the sausages wrapped in polythene, under suitable compression (crucial) will provide fire protection and is what is widely used along with a 2x2 solid timber for closing cavity. Be generally warned of any so called 'fire rated' b1 & b2 type expanding foams - these are not fire rated. I did a bit of research on this stuff for a previous company and they are only tested for surface spread of flame and for use as a gap filler in conjunction with an intumescent mastic. Bit naughty of them really to have fire ratings plastered all over the fron of the cans.
-
Thats the thing about water, it is both canny and incredibly patient - it will find its way in eventually!
-
I have been looking in to this exact detail myself with vertical cladding. You can buy pre-treated cant rails @ 47x75 off the shelf. A bit over-engineered but designed for fencing and i cant find anything smaller. 25mm cavity should be fine provided sufficient ventilation grilles/gaps left at openings and top and bottom of cladding.
-
Stop Press!! I know many of you were disillusioned with the UK house building industry but fear no longer as TW are breaking the mould and pushing the boundaries for sustainable green house building. They are now even offering double glazing!!! Not only this but 'quality insulation'!!! (What they mean by this is actually 100mm cavities). Made me smile on my rounds - good old house builders. The sad thing is they have waiting lists as long as my arm of unsuspecting buyers clamouring to buy a bog standard box about the size of a shoe box for obscene amounts of money.
-
Traditional construction can be built to very high even passivhaus standards with a little care, the right spec and not too much additional expense. Google the Denby Dale or Golcar passivhaus and most of the construction details, thermal values and costs are online.
- 30 replies
-
- 1
-
-
- u values
- insulation
-
(and 1 more)
Tagged with:
-
This really depends on the relationship you have with the current landowner and also the price of the land (i.e. Worst case can you afford the risk of owning an undevelopable plot if pp can not be obtained). You could end up spending thousands on design and planning fees for the landowner to then cash in on your work and outlay to sell to highest bidder unless you can fully trust them to stick to original agreed price (very unlikely unless it is owned by family member). I think the best way would be to have a pre-planning discussion with the local planning authority (sometimes free, sometimes a small fee), they will generally give you a good idea if anything and if so what type of build will be accepted on the plot. If that is a positive meeting then i would negotiate with the landowner a price or have a survey to agree value and fair price. I would then approach a solicitor to draw up an option contract, this is a binding agreement but you will have to pay a deposit upfront that will secure the land at the agreed price if and when planning permission can be obtained. Beware the deposit can be lost however if pp can not be obtained - there is always some upfront risk and capital when buying land without planning.
-
Assessing the quality of a laid tile floor
MrP replied to Fallingditch's topic in Floor Tiles & Tiling
That does look pretty amateur, difficulty is if you have supplied the tiles then your only recourse would be to withold payment for laying. Not good, some pretty poor tradesmen around at the moment!! -
Assessing the quality of a laid tile floor
MrP replied to Fallingditch's topic in Floor Tiles & Tiling
Have a look through this, it gives a max tolerance of +/- 3mm over a 2m straight edge. Not really much excuse for flatness as with a decent adhesive bed you should always be able to even it out. Joint thickness is difficult as it depends on tolerance of the tile but i agree with earlier comments that you would like to think he would have stopped and spoken to you once he realised there was a problem. filedownload,15912,en.pdf -
From my experience you are right and the types indicated are low risk and will come under non-licensed work so you can remove yourself or you can ask your demo contractor to do it for you. if you go on the HSE website there are some standard method statements for quite a few situations which you can print and use.
-
Regarding the asbestos, the only way you can be sure is by having the materials sampled by a lab, generally whoever did your survey can provide the service. Regarding the demolition, you need to submit a section 80 notice form, the council have 6 weeks either to either issue a section 81 or if no reply it is deemed accepted.
-
Even with the tree removed you will still need a suspended floor but you will be able to reduce the foundation depths by approx 30%. Ive had a play around with the figures but cant quite get to the 2.1m though that you have been advised. If you can tell me what the tree type is and where about on the south coast you are i can calc the depths your BCO will ask for. The only other thing is your soil type - clay soils are either classified as low, medium or high volume change potential (basically it is how much it will shrink or heave due to the clay content). If you do not have this information from a soil report then the BCO has no option but to calculate based on the worst case scenario - im not sure whether you would have had a soil report done?
-
As Peter says, do not remove the tree, it is now known about and removing it will not alter heave/depth requirements and a crafty move like that would not bode well for your relationship going forward. Don't forget google earth images which can now be backdated are a regularly used source for site investigations by approved inspectors. The BCO will not issue a foundation design however, we do not hold the relevant qualifications or insurances to issue designs. You need to get your SE to issue a design taking the tree in to account using NHBC standard guidance which he should be well versed in. If i was you i would hold fire on pouring concrete until you have a suitably agreed design, trust me its a lot more expensive to put right than to put off. However having done the cost excersise for my build i didnt find block and beam to be particularly more expensive if you use a product like cellecta tetris to negate the need for the concrete blocks.
-
Getting large bits of glass up onto a roof
MrP replied to thomas's topic in Skylights & Roof Windows
You can also rent a glass hoist, like a panel hoist but with suckers attached. Just type 'glass hoist' in to google and loads of pictures will come up. Certainly cheaper than a crane! -
Depends on the screed but most cementitious products tend to achieve between 50-75% of strength after 7 days so should be good for a decent fix after a week. Just do a couple of test fires somewhere out of the way and see how you get on. Just remember a dpc under the sole plate to protect from damp
-
Try these felt lap vents, they work wonders and is a cheap and easily installed solution. Spread them out evenly across the roof and at different levels to maximise cross flow. http://www.manthorpe.co.uk/Building/Products/Roof-Ventilation/Felt-Lap-Vent.html
-
There are loads of online retailers offering all sorts of designs and sizes, just stick primed mdf skirting in to google. Alternatively if you want a pretty simple profile then it may be worth having a chat with your carpenter. When i did my first renovation and money was really short i just bought the 18mm mdf sheets from wickes, worked out the most economical way of getting as many skirting and architrave lengths out of a sheet and got them to cut it down and rout out the profile. IIRC i paid them about £100 and once they got set up it only took them a couple of hours. The only issue is then having to sand and prime it all, but it saved me a lot of money at the time and i got to choose exactly how i wanted it.
-
Wow, 22k! You must have built up a good line of credit over the years. To be honest i think that is going to be my only option, a mix of loans, cards and general begging. What really gets me is a contractor i used to work for went to 60 day payments on all suppliers, and they had shed loads of cash sitting in the bank! That's the way of the world though i guess.
-
So.....due to some unfathomably complex legal issues (restrictive covenant related) on the plot of land we are looking to purchase, the only mortgage lender who is willing to even start thinking about possibly considering us happens to be an arrears stage lender - not good when i only have 15% deposit for the land/build. The issue here is basically a cash flow one. I am going to need about £55K to get groundworks complete and timber frame up. I can pay for the groundworks with the cash left out the deposit but the timber frame and windows are the big ones at £40K and £15K respectively. Seemingly as soon as any contractor or supplier gets any whiff of the work self build its seems that payment terms become in full at time of placing order. Munster joinery is a particular example who supposedly apply a 10% discount to their prices which is removed if anything but full payment in advance is offered (basically it seems to be a 10% self build tax). But this seems to be across the board and puts me in a bit of a pickle. So what i guess i am asking in a roundabout manner is how have people fared in their various dealings with contractors and suppliers - Has anyone been in this situation? Have you been able to negotiate for example 30 day payment terms using a contract? How have you been able to creatively make money magically appear to pay suppliers in advance? Is this just a case of juggling credit cards and loans to get me through to timber frame completion (the good lady her indoors will not be pleased!)? Thoughts and ideas gladly welcomed....
-
Telescopic vents in a garage slab???
MrP replied to Vijay's topic in General Self Build & DIY Discussion
Which is exactly where it should be but because the floor is ground bearing and has no sub floor void then you need to create one in the form of a sump which can then be vented to avoid a dangerous build up of gas in the floor below. To me the drawing looks absolutely correct however as mentioned before you just need to check exactly how and out of what the sump is to be formed. -
Telescopic vents in a garage slab???
MrP replied to Vijay's topic in General Self Build & DIY Discussion
I would check that as a radon barrier is indicated on this drawing and the one on the other thread with your ICF to foundation detail. Sometimes radon can be extremely localised, i have developments of 100+ houses where perhaps only 1 or 2 require radon protection. Requirement for this will normally be confirmed in your site investigation/soil sampling report. -
Telescopic vents in a garage slab???
MrP replied to Vijay's topic in General Self Build & DIY Discussion
I think that is a radon sump and will definately need venting. You need to check what will form the void (i would assume a large diameter granular material) as the slab is ground bearing. Is the garage attached to the house or detached?