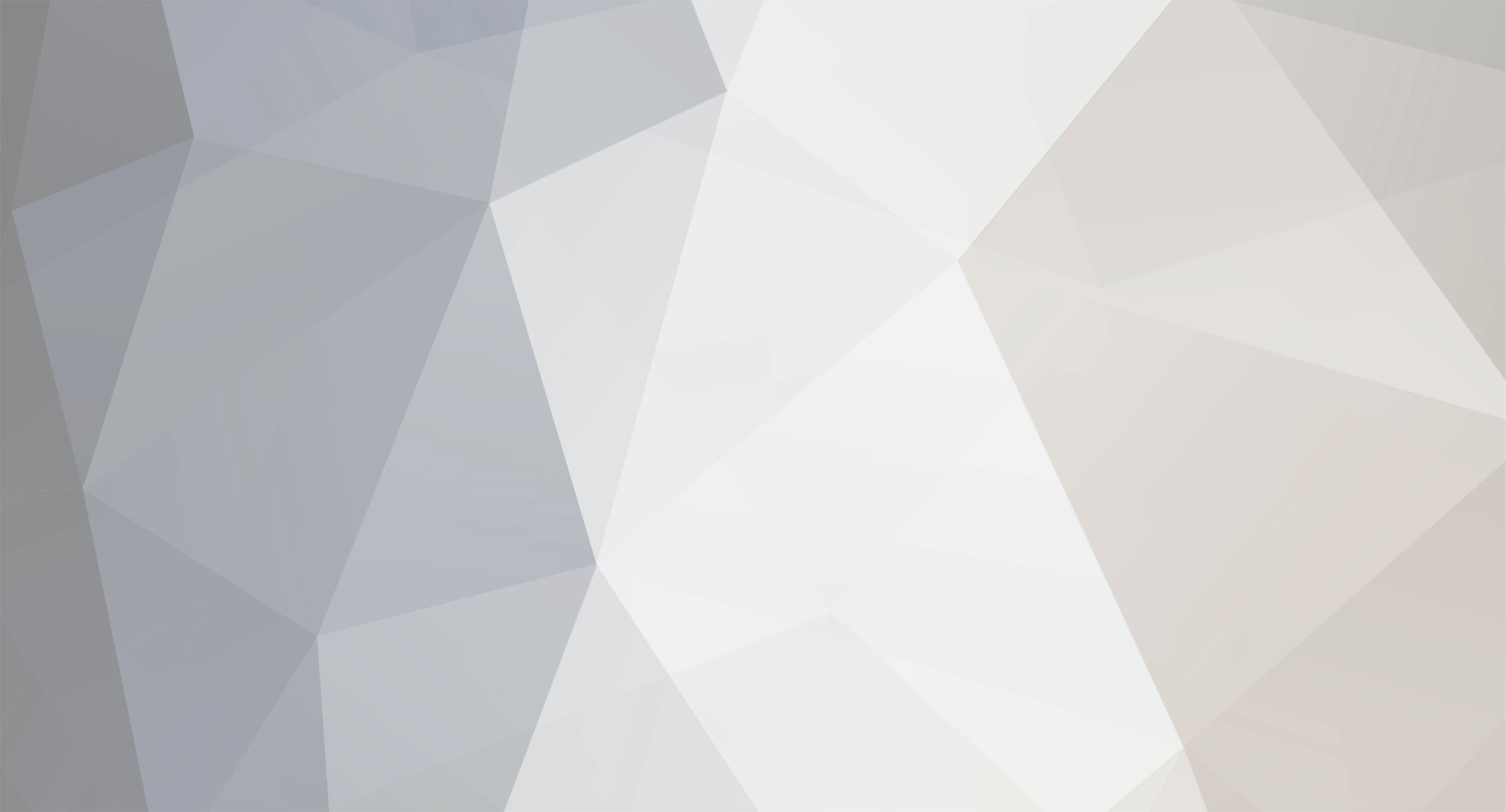
Gorlando
Members-
Posts
19 -
Joined
-
Last visited
About Gorlando
- Birthday 12/09/1984
Personal Information
-
About Me
Planning a self build 4 bed + roof space with attatched annexe in stoke. Plant breakdown engineer, sparky by trade. Father of two.What I know I will share, but I don't know much!
-
Location
Stoke on Trent
Recent Profile Visitors
The recent visitors block is disabled and is not being shown to other users.
Gorlando's Achievements

Member (3/5)
1
Reputation
-
That's it I don't. The insulation quotes above are just for 'a' sq meter @ 155mm cavity. I have no actual floor plans or elevations to work a total off. To use the initial design put forward would be a waste of time as we have changed it so much. Plastering. I know I will still get expansion cracks whatever. I'm bearing an open mind still towards thermalite and it's good to know about your positive results. I do know to just soak the bejesus out of em, first lesson in plastering from me old man! Suppose it just comes down to costs and like @PeterW says whether the difference is actually costs effective. Hopefully have some better plans by the end of the week Cheers
- 21 replies
-
When you say light-weight, do you mean thermalite or med dense/light-weight concrete such as fibolight? Preferance is for fibolight, which is the block spec'd in the valies above, or similar. I want to avoid thermalight etc for the many snagging issues they can bring on further down the line. But in answer to you question, no. I can't price anything up, as such yet, as we are still agreeing the final design. The initial design put forward was a non starter from our point of view so we threw it out. Now waiting for a more suitable initial floor plan to work off.
- 21 replies
-
No sorry that's a 200mm cavity; .18 with a 155mm cavity. FYI Energystoreltd have come back to me this morning also, their product has only a slightly worse r-value and are stating approximate per sq meter costs as £6-8 for 155mm cavity. A 155mm cavity with the above spec is rounded up to .19 with ESltd as oppose to .18 with thermabead's CS. Hope that helps?
- 21 replies
-
@Oz07 @JSHarris Calculations for the u-value of .14 were done with fibolite, another bonus!
- 21 replies
-
@JSHarris it is an interesting point you make surrounding the buffer it provides. To be completely honest we have always sought to try and achieve a value equal to or less than .15. A 200mm cavity for example, using the above stated wall construction would achieve .14. I got talked out of it by my designers viewpoint initially, but providing the budget can handle the extra wall tie costs and cavity closings then I may well settle on 200mm. I think it's time I became more assertive! The build won't be starting for a good while also so I have plenty of time to shop around. @Oz07I will report back no problem, but like I said above we won't be building until this time next year at the earliest. Also, we never intend on selling, with the intention being to pass it onto the kids. Prob more reason to spend that bit extra money on the fabric. I think a more dense block will require an even bigger cavity to acheieve .14 for example, may be wrong. My preference is medium dense, but all card are on the table at present. Can I ask your reasons for not wanting to aircrete/thermalite next time around? @PeterW that would be the 325mm for me then, With a quick look last night I found them at approx 2.30 per wall tie, for a branded kind. I'm sure with a little shopping around we could shave a bit of that, and a bulk buy of course. I read somewhere that there is a company in Ireland who do cheaper alternate basalt composite ones, but I can't find where I read it now. Any idea how many is used per sqm of wall? @Declan52 all valid points that I have logged for discussion and costings, thank you. Lets just hope the ground doesn't hold any nasty surprises to boot! @bassanclanOn the face of it, (£7.78pm/sq) that's pretty cheap. That is my main reason to have it blown in, to avoid the errors. @ADLIan points noted, but surely as your building from scratch than the opportunity to engineer out said voids is present? I can see how clumping and variations will be harder to overcome, or builders bodging/hiding installation defects whilst I'm not there when employing the use of batts/eps boards. Ultimately for me, its choosing the lesser of the two evils. I'd be interested to read any articles you may have surrounding the issues you have highlighted. @JSHarrisThe roof...never even considered at this stage that we could get it blown in there also as we are looking at warm roofs (house and annex) more volume should hopefully mean better price and more saved time and money for the initial super structure build. And a useful first hand insight, thanks. @Ian plot is in Stoke-on-Trent, about 16 miles north of Stafford. From my understanding of the document, and please correct me if I'm wrong. We should be okay with tooled flat joints @+150mm. This joint will give us the farmhouse look of the local area also. @ADLIan I'll check the BBA certs for the one we settle on when the time comes. In your opinion then, is there a top performer?. My research so far is highlighting the Thermabead Carbon saver as the best performer, but I haven't had the chance to research a great number. thanks to all for some really interesting points, I'm sure this thread will help many others too. Giuseppe
- 21 replies
-
Depending on the number crunching, I seem to be settling on a 155mm full fill cavity with eps beads for a number of reasons, fast install, builder free installation etc to name a few. With Thermabead's Carbon Saver for example brick outer, 155mm full fill, med dense block inner and plaster finish gives back a u-value of .18. To cost out Thermabead have said to work on the basis of £10pm/sq for a 155mm fill. I was just wondering if anybody had there insulation costs to hand to easily try and draw some comparisons to other methods (I realise this may difficult so cost per meter squ would be easiest) If anybody can suggest other eps bead providers also. Finally, would like to hear people's options on the figures achieved above. I like it as it appears a respectable value for a modest cavity size. Climabead doesn't seem to perform as well (185mm needed to achieve the same), waiting to hear back from Poly-pearl and energystore (all taken from the national bead blowers association website) thanks in advance
- 21 replies
-
much appreciated, thank you
- 29 replies
-
- u value
- insulation
-
(and 1 more)
Tagged with:
-
yes liking the looks of Thermabead for example, brick outer, medium density inner, plaster finish gives a value of .18
- 29 replies
-
- 1
-
-
- u value
- insulation
-
(and 1 more)
Tagged with:
-
Just thinking back to your previous posts, your build sounds similar to mine in principle. What beads did you use, cavity thickness and u value if you don't mind me asking? Also, did you manage to find a resource calculator any where on tinterweb to calculate the wall make up u-value with beads? cheers
- 29 replies
-
- u value
- insulation
-
(and 1 more)
Tagged with:
-
good job I checked with the knowledge base as in fact I have missed this point it appears. thanks again.
- 29 replies
-
- u value
- insulation
-
(and 1 more)
Tagged with:
-
So we had our first meeting with the designer last week and when I asked about the u-value for the walls he said he had calculated it to .22 with a 125mm thick full fill mineral wool, block inner and outer, render finish, plastered inner walls. I stated I wanted it to be lower and asked about the advantages of using a foil faced eps. He then said if we used a foil faced then we need to leave a gap i.e. not full full?? Is this right? For example, using the Concrete Block Association Website u-value calculator a medium density block inner, plaster finish, brick outer with 150mm foil faced full fill cavity gives a figure of .15 which is more like the figure I was hoping for. Just found his comment about the gap was a little strange as it contradicts all my research, but he has me thinking I've missed something now? I was just curios to anyone's thoughts on the point to see if they had heard similar?
- 29 replies
-
- u value
- insulation
-
(and 1 more)
Tagged with:
-
I can expect mine to be very similar in size and demand I feel. We are a family of 4 plus the mother in law in the newly built annexe.
- 30 replies
-
- u values
- insulation
-
(and 1 more)
Tagged with:
-
Some very interesting lines for me to investigate. The EPS bead fill is appealing to me as it's another fail safe in that I don't have to be watching and worrying about the quality of the wall insulation intallation. This will help also, in regards to my shift pattern, as I will be away from site for 4 consecutive days out of 8 so will not be there to oversee the superstructure build at times. Like I said I do trust my builderbut the less risk attatched to sloppiness the better. In terms of worker control post shell. At present i'm only planning on hiring a plasterer and subies for speacilist commisioning (RHI eqip, MVHR) As said previous, i'm a spark and dad and brother are Gas CH Engineers. Although there's no gas service to the site, they can still do the majority of the pipe work. Anything else I feel pretty confident we can get it done together. Apart from using a block and brick building method, nothing else is set in stone. Whatever gets me the values I need at the right price is very much on the table. And to summarise what you all seem to agree on is that passive house standards can be achieved for the same or only slightly more thay a building regs house. Correct me if i'm wrong! Once again thanks for all the replies. Really is proving to be a great community. Hopefully this thread will help others who are on a similar thought trail as I was....
- 30 replies
-
- u values
- insulation
-
(and 1 more)
Tagged with:
-
Thanks for all the replies. I see the point of what you are all saying. I definitely need to have a play around with the u value calculator and then cost a few things out etc. A main contractor will be completing foundations, slab and erect the weather tight shell. I will insulate it and then finish the rest/organise subs where needed so I can control a lot of the installation. Our intended builder/contractor is a good guy I know who will take pride in it I feel. I'm set on brick and block that's final, timber frame just isn't for me.
- 30 replies
-
- u values
- insulation
-
(and 1 more)
Tagged with:
-
As the title suggests I'm trying to work out where the happy medium in relation to the target u value/s and air tightness for my new build. We're about to have our initial design meet with our designer and I want to have some u values in mind to specify. I very much want to adopt a fabric first approach using block and brick and have already had thoughts around specifying thin joint aircrete for the inner skin and a tetris insulated floor. My question is, at what u values for the different elements (walls, floor, roof, windows etc) do you get the most bang for your buck? I know this could be quite subjective and is dependant on my house size and budget, but I want to target that sweet spot before costs get silly for minimal improvement over and above that spot. Cost effective is key. Further details on request. Thanks in advance
- 30 replies
-
- u values
- insulation
-
(and 1 more)
Tagged with: