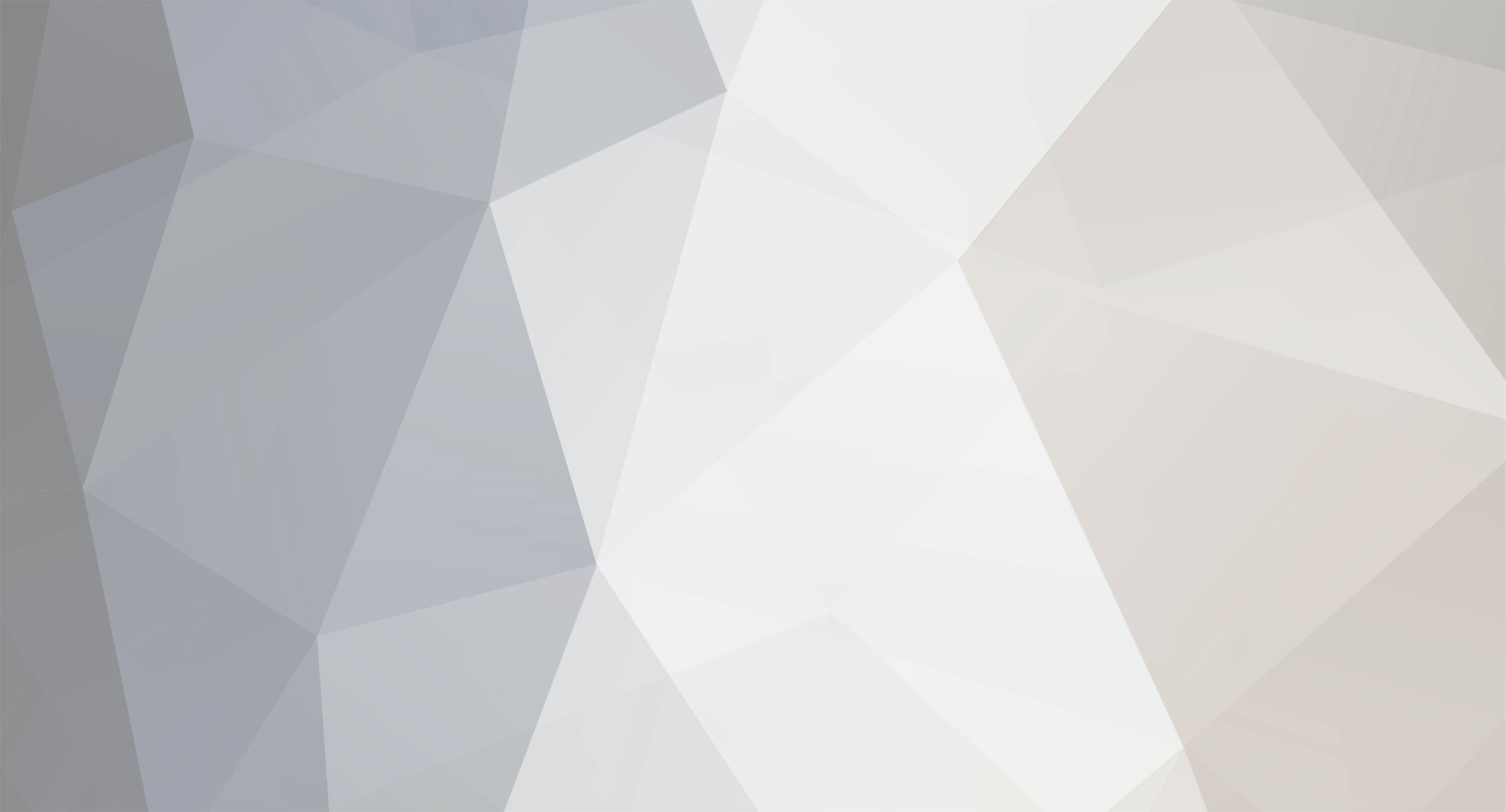
MarkyP
Members-
Posts
151 -
Joined
-
Last visited
Personal Information
-
Location
Kent coast
Recent Profile Visitors
2144 profile views
MarkyP's Achievements

Regular Member (4/5)
88
Reputation
-
I bought a 2.5t Takeuchi TB025 for my project, I've had it 4 years now. It is very old and tatty but starts every time and is still a strong machine. Old used machines are risky, if something major goes wrong with the hydraulics, like the pump or a track motor, then it can be a bill of 0,000s to fix. Fortunately, I've only had a replace a few pins and bushes, had it serviced, replaced the coolant and changed a few track adjuster seals. I am running out things to do with it and my wife is enthusiastic about me finally selling it on now (me less so!). Postives for your own machine are using it whenever you want, with hired in you need to have a job to do with it and get on with it and get the machine off hire promptly so it can put you under pressure, particularly if you are oding DIY. If using your own machine means you can break up jobs over days or weeks, no pressure. Other trades will find it handy having a machine on site, mine can lift bulk bags and living on a big plot that has saved a lot of labour. We've done all sorts with it, lifting steels, lifting large windows onto scaffold, demolising old outbuildings. I've also done a lot of ground clearance of bramble scrub in overgrown areas with it (the grading bucket can skim undergrowth off the surface once you get the knack). I wouldn't fancy a backhoe for house ground works, a digger can get in and out of tight spaces, is very easy to adjust position, it can cross over dug footing trenches, can straddle trenches as you dig them, and is generally very versatile, I reckon a backhoe is a farm machine really, better than noting but a bit of a compromise on house build site, I'd get a digger every time. I think most people who have bought their own machines have found them well worth the investment.
-
Water main replacement, fittings and weeping joints
MarkyP replied to MarkyP's topic in General Plumbing
unfortunately the old fitting went the way of the skip and is long gone, I only noticed the weep some time later. I think I can only try to sure up the BSP thread join with more PTFE and braver extra 1/4 turn. I might buy another fitting first in case it all goes wrong and I overtighten it. I noticed MDPE fittings are a bit leak prone, as you say, if the pipe isnt dead straight into the fitting and I've had them leak with scored pipe where the o-ring cant make a perfect seal. I wonder if many homes have small leaks between meter and the house for these reasons and just arent aware of it -
Water main replacement, fittings and weeping joints
MarkyP replied to MarkyP's topic in General Plumbing
thanks, yeah it's the male threaded end rather than the 25mm MDPE pipe into the o-ring fitting. I've had leaks on those as well, but seem to be if the pipe is scratched and the o-ring doesnt make a clean seal. -
Hi all, I have been landscaping my drive and found that a long section of water main was metal pipe which was very corroded and brittle. I decided that while I was digging it all up and would replace with 25mm MDPE. The main supply stop cock is near the boundary, it is a metal stop tap with a metal female BSP socket on the domestic side. I purchased a male BSP to 25mm MDPE plastic coupling which fits fine but keeps weeping. I think the weep is at the MDPE male to metal female joint rather than the 25mm MDPE pipe/fitting joint. I did apply some PTFE and I made it tight but stopped going too hard as was worried that the plastic male would crack or deform if overtightened into a metal female socket. I wonder if I should try to pinch it a bit tighter or should I try a thicker wrap of PTFE? thanks. the fitting is one of these:
-
HI all, I'm finally cladding my kitchen extension (5 years after I built it, I quite liked the blockwork but my wife was wondering if I was ever going to clad it!). I decided ofcourse to wait until timber prices had at least doubled before deciding it was time to proceed. So, I have some iroko hardwood cladding boards coming. It is going to be horizontally fixed with an interlocking T&G type profile. I cant decide whether to face fix with two screws or to fix through the tongue and secret fix them. Is there any consideration other than aesthetics? Also, does any consideration need to be made for movement of the boards or are they butted up tight with the T&G. I dont really mind the idea of visble screws but wonder if it will be much faster doing a screw into the tongue method as I can see it being slow work for face fix with putting in 2 screws and keeping neat lines and perps for each batten run. I'll be using stainless screws of the type for cladding fixing. thanks
-
Hi all, I'm after a bit of plumbing advice. I am re-routing some pipework which was installed hastily and in the wrong place some years ago. By re-routing the pipes I can dramatically shorten the flow and return runs for a UFH circuit d get them out of the way of some other work I am doing. I have a oil fired system which heats a radiator circuit, a UFH circuit and a water cylinder circuit, flow to each circuit is teed off and controlled with its own motorised valve. The returns join up variously onto a main return to the boiler. I am trying to decide where to link up the UFH return. I have two options, drop down into a cupboard where the cylinder is located and join up with the return from the cylinder which routes to the main return near the boiler. Or run a return leg to nearer the boiler (means hole through a steel beam) and join to the main return nearer the boiler. Does it matter where a circuit links up with the return? I was told it would be fine and just not to link up another circuit with the return before the last radiator (which I am not doing) thanks
-
does anyone know the rules on glass type and thickness for a juliette balcony? I've been getting some conflicting advice from suppliers. The balcony is face fixed to the frame of the french doors with a frame system, there is no top or bottom rail, the glass spans the opening fixed either side. The glass will be 1100mm high for the protection from falling regs but in terms of glass thickness and type I've been told 10mm toughened is sufficient and another saying 17.5mm toughened and laminated is required. The width of the opening is 1750mm. thanks
-
Fixing things to EPS EWI and render
MarkyP replied to canalsiderenovation's topic in Insulated Concrete Formwork (ICF)
I'm probably strating the obivous but use stainless screws otherwise you'll get a rust streak down your render face. -
Fixing things to EPS EWI and render
MarkyP replied to canalsiderenovation's topic in Insulated Concrete Formwork (ICF)
you can get some fat EPS plugs but I treid them and didnt get on very well with them, they made a bit of a mess of the render and pull out resistance wouldnt be very high. https://www.fastco.co.uk/fischer-fid-50-insulation-fixing-art-no-48213-pack-of-50.html?kw=pla-59448214701+c&fl=1000&ci=144812953870&network=pla&gclid=Cj0KCQjw6NmHBhD2ARIsAI3hrM1TU-dVJiD8hMpChoejXGQjU8m9s8xEtg47TpU_4l6u9GTLvhqfn78aAiEHEALw_wcB my EWI is quite thick so came up with a way to avoid going all the way through, for things like lights I used long rawl plugs, drill a hole in render and EPS about 70mm deep, air spray to clear the hole, fill hole with squirty foam PU glue (mask face of wall first!), insert long rawl type plug watching for PU being splurged out, leave to set, then screw in with a relatively thin screw that only just bites the plug so as not to put too much rotational pressure on it. Worked well and the plug held without spinning and took a pretty strong fix but dont ask too much of the render. otherwise fix right through to solid substrate, with a plastic rawl plug the thermal bridge won't be too bad, barely worth worrying about. watch for point loads on the render face and dont overtighten -
it is the total thickness of the screed so, yes, measure insulation to top of screed regardless of pipework. If sand and cement screed then 75mm is about standard. Liquid pour is thinner. I used liquid at about 60mm, personally I find it a bit bouncy on the insulation and it doesnt have a completely solid feel, the kids thumping around can be felt through it. If I had my time again I would have gone with my 150mm concrete slab over the insulation and had the concrete laid to a decent standard of flatness/level and done away with the screed entirely. I havent done sums but reckon the higher spec slab finish is more than covered in the screed savings. Then I would have put finish floor over, or run a smoothing compound if it was a bit rough, then finished. Slab would possibly need some structural movement joints depending on what you want to put over the top of it.
-
I used lightweight aggregate blocks, avoid aerated. Aerated is one reason why the volume builders dot and dab - to hide the cracks. Can you not widen the cavity to improve the uvalue if needed and add more insulation? Wet plaster best for air tightness and a nice solid finish, good to fix to. My brickie said he really doesn't like aerated, very high suction and mortar can dry before it's cured in summer. Cracking seems to be brittle nature of the blocks, they have standard compressive strength 3.6n 7n, etc, but weak flexural strength.
-
Excessive cracks and shrinkage in plasterboard ceiling
MarkyP replied to GaryM's topic in General Construction Issues
I have vm zinc standing seam on my loft dormers, each dormer is clad in exterior grade ply with a membrane and standing seam over. Under the ply is a ventilated batten space, then insulation between and under the rafters. the fluffy stuff referred to earlier might have been OK if they'd used a 0.032 high density mineral wool like frametherm or rafter roll but if just standard loft insulation fluff at 0.044 then not ideal. Personally here I would prefer a combo of dense wool 200mm between and perhaps 50mm phenolic under rafter to get both a pretty decent u-value and a good decrement delay and sound insulation of the dense wool layer. But agree with others that ventilation under the metal would have been a standard detail unless very conciously designed otherwise. Some consideration of wind tightness of the mineral wool would also be a factor if a ventilated void was introduced. there are examples of fully filled build ups with no ventilation under either sarking or even a "non-breathable" metal roof but I think these are often with meticulous attention to airtightness detail and backed by warranted condensation risk analysis. Not sure the architect described here is in that bracket though. I have a hybrid roof - after much deliberation I have the south and south west roof pitches insulated with fully filled 150mm dense flex wood fibre with 75mm PIR under rafter, this is under OSB sarking and fully filled, no ventilated void under the sarking but ventilated counter batten space above the sarking under the roof slates, so there is lots of outward drying potential for any moisture that does enter the insulation layer, boosted by the solar gain on the slates which heat up in the sun. The roof pitches which don't get full sun are different, 100mm phenolic between rafter with ventilated void (eaves and ridge) under sarking and 75mm PIR under rafter. My BC inspector did take a few mins to understand my logic but couldnt see any issue with it, but he did say he'd never come across a roof with two different insulation strategies in opposite pitches before but he got used to my strange ideas during the project! This was a large loft conversion so I was limited in insulation depth by existing rafters. My trade off on the south facing pitches was a small drop in u-value for a large improvement in decrement delay to reduce risk of summr overheating. Those roof pitches without full sun I went for the best u-value I could achieve within the depth available to me without compromising room space too much so used phenolic and PIR. -
Render, EWI and DPC - Advice needed
MarkyP replied to canalsiderenovation's topic in Plastering & Rendering
good to hear the below DPC is in the plan, this is a detail which seems to be more standard now, a few years' ago it wasnt. the builder will likely use a starter track or plinth at the DPC line. This is based on the idea that the DPC needs to continue through the EWI (I'm doubtful it is needed, EPS doesnt wick water to any extent but your builder will likely want it). Lots of discussion on this point on green building forum. But if you do have a plinth/starter track you might find a bead that will create a slight lip and still allow 50mm below DPC as well. Or you could consider wehther you need to mark the DPC at all and run 50mm all the way down, but I appreciate this might seem bold and your builder might not like it and sounds like you havent got much time to research it. I did use a bead at DPC but only becuase I needed to get the EWI done and planned to do below DPC later when I had the time to dig out down to the top of the footings so the starter track gave me a level base to work from. I'm actually planning my below DPC EWI this summer, 4 years on. if you need to backfill to bring the ground back to level (the plinth EWI should really good down to the footing) consider a strip of leca (clay pellets) - it's quite an insulative material and will create a further benefit in addition to the below DPC EWI and will help keep the area around the plinth EWI well drained and dry. Again check out GBF and search for "EWI & leca" there's an architect who posts with some really good ideas and experience with EWI. hope the admins dont mind the GBF plugs, EWI has been discussed there in great technical depth so is really worth a read.- 7 replies
-
- ewi
- insulation
-
(and 2 more)
Tagged with:
-
Render, EWI and DPC - Advice needed
MarkyP replied to canalsiderenovation's topic in Plastering & Rendering
hmm, your window extension sills may not be big enough, this may be an issue. Mine were clip in and came in various sizes. Looking at the pictures (which may be deceiving), they look barely big enough for 50mm EWI, check that you can accomodate 50mm insulation plus 10mm adhesive plus 10mm (or more) render plus ideally 30mm projection for a drip. And ss above, 50mm really isnt enough insulation for regs unless you have existing, and in any case you really ought to do as much as poss while you are at it but the sills may be a constraint now. also ideally take out the soffit and run the insulation up the face of the wall to the underside of the roof (be midnful of ventilation though), between rafters/joists such that it can meet the loft insulation. If not you get a cold spot at the top of the wall and window heads where there is no insulation. it will mean running new soffit or refitting cut back original sofft but again an important detail most installers wont bother with as too much trouble. if the below DPC EWI seems too much to contemplate at the moment, the builder will run PVC starter track along DPC in all liklihood anyway so you could do the below DPC EWI later when you can face digging it out to the top of footings and installing. if the renderer is good get his number and see if he fancies a little side job to come back and do it later. If you end up with 50mm EWI then think about a drip or bellcast bead as you will not want less than 50mm below DPC and will need a drip detail of some kind to create a small overhang at the join.- 7 replies
-
- ewi
- insulation
-
(and 2 more)
Tagged with:
-
Render, EWI and DPC - Advice needed
MarkyP replied to canalsiderenovation's topic in Plastering & Rendering
I've done EWI to my bungalow renovation and a few things to consider. In my view the best insulation choice is graphite enhanced EPS. However, unless you have existing insulation in those walls, 50mm isn't anywhere near enough to meet regs which you should aim to better in any case. If your builder proposed Jablite then I think this will be EPS which is a start however the spec sheet doesnt say what type - you need to check they are using an EWI grade EPS sheet, this will be grey coloured (graphite enhanced) and more insulative than the white stuff. It should also be from aged blocks which are dimensionally stable, again EWI grade will be such. Even if you do have insulation in the walls, go for as much EPS as you can accommodate with your eaves/verge overhangs. The thicker the better. 50mm isnt very much at all and adding thickness isnt the main cost driver here, EPS is pretty cheap. I'd go for at least 120mm or more. check out green building forum, search for "DIY EWI installation thread" to read all about my install. i did it myself and spent more time than I care to admit researching it! things to watch out for - - make sure the installer foams the joints in the boards. If they pug them with adheisve this is creating thermal bridges and is bad practice (but very common practice!) - ensure they use branded, EWI grade EPS (I used kaycel) - ideally they should use thermally broken fixings and adhesive, the fixings are recessed and have a insulation cap, really neat (see my thread on GBF) - avoid an aluminium tray at the DPC if you can, plastic is better and doesnt create a cold bridge. - you dont need to break the insulation at the DPC contrary to building folklore it really wont matter or create issues but your installer might not agree. You could run run the insulaton right down to the top of the footing. Alternative is to break with a plastic plinth bead at DPC and run a course of EWI under the DPC level to the top of the footing. The aesthetic of the different DPC levels will be a fiddle but how you detail the below DPC insulation will be a factor. - through colour render isnt my favourite, I prefer thin coat with mineral silicate finish. I used Baumit star contact white basecoat and nanopor fine finish. - think about where you might need to mount rainwater downpipes. You cant fix into EWI, you can put timber grounds behind the insulation to screw into, or fix right through into the underlying wall - frameseal beads for windows are really neat, check if they use these if not sugges tthey do, rendering up tthe window frames is scruffy and will need to be siliconed to create a weather seal - EWI is a great solution - will make the house much warmer and the insulation is inherently wind tight once installed and rendered (unlike brickwork and cavity fill)- 7 replies
-
- ewi
- insulation
-
(and 2 more)
Tagged with: