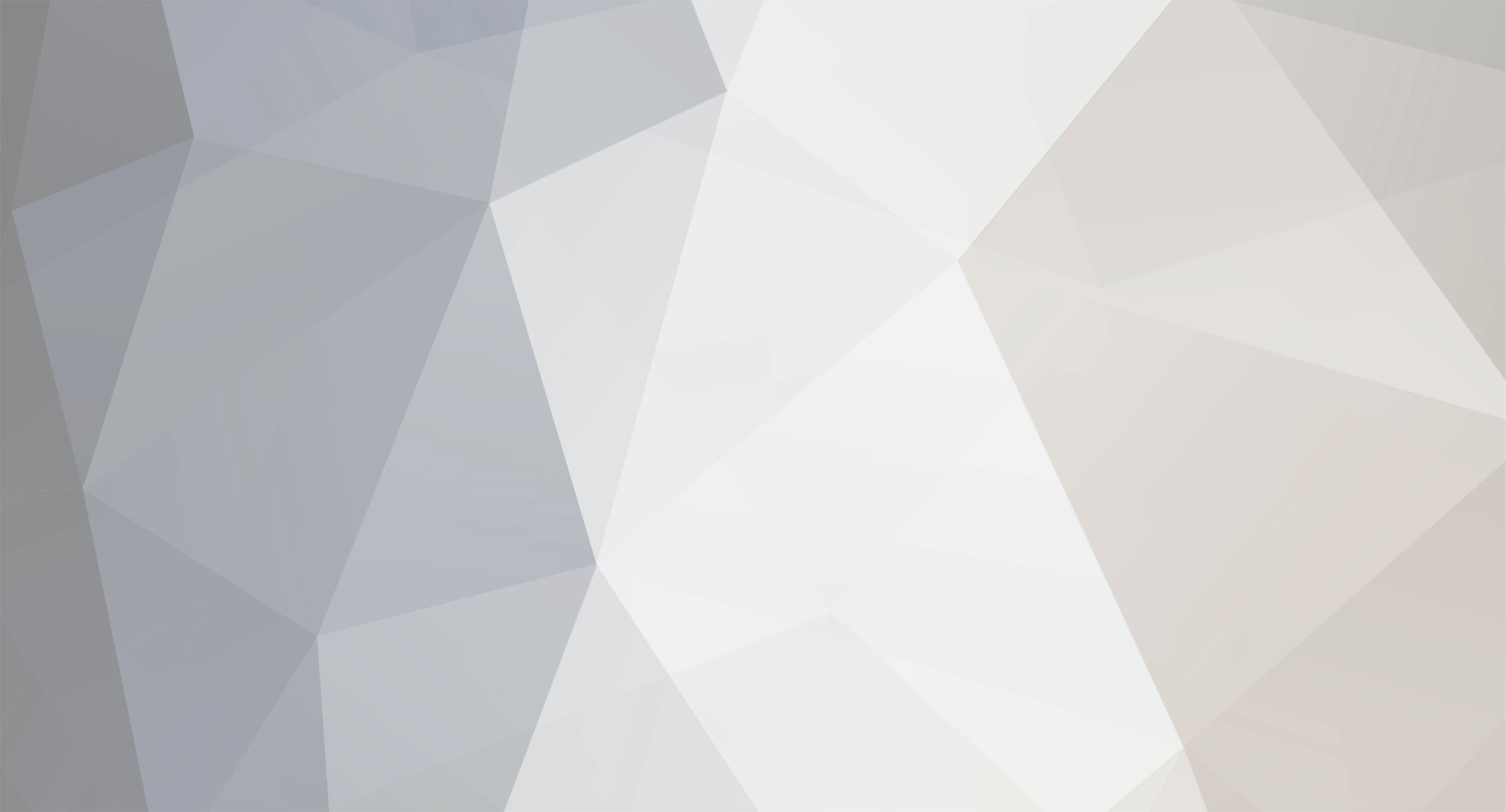
Rich123
Members-
Posts
42 -
Joined
-
Last visited
Everything posted by Rich123
-
Are you talking the pressure relief valve drain. Sizing is required as building regulations . It should discharge in a safe location , visible. If you wanted to drain it via a tank or similar , you would need to fit an alarm with a visual display I would say. Installation of unvented cylinders is defined in the building regulations in detail under the domestic heating and hot water guide which you can download . also it needs a certified installer to sign it off.
-
Hi the movement is a theory , the weather exposure is a south corner so lots of sun. But the cracking is along the length of the render bead. Could be damp board or something else
-
Connecting radiators to UFH Manifold?
Rich123 replied to valmiki's topic in Central Heating (Radiators)
Hi , I think ideally you would connect to the primary pipe supplying the manifold , assuming that it’s supplied from a boiler , as the temperature will be higher . if you connect the radiator to the underfloor you would need to increase the size to compensate for the lower temperature, but it can be done . Approximately double the size radiator if off ufloor. -
The actuators are for each zone , therefore each room is a zone and requires a separate zone controller via a room thermostat. This is required under the building regulations domestic heating installation guide. you don’t need to zone the manifold supply as the individual actuators achieve room discrimination. the only reason to do this would be if you want to run the system as variable volume, which could cause issues with the heat source and I think would probably be overkill for this application.
-
Ufh manifold, blending valve with ASHP.
Rich123 replied to Russell griffiths's topic in Underfloor Heating
Hi Russel , it depends on the application. The ASHP should have a weather compensation on it , therefore the flow temp will be determined by the ASHP. Having a blending valve installed won’t reall change anything as long as you keep it set to the maximum temperature of the ASHP. If you have an ufloor design it may be based on a flow temp of 45 degrees for example . It could be useful as a high limit so I’d install it regardless, it won’t do anything if the temperature from ASHP is lower as it will operate fully open. -
I’ve had my extension rendered for around 2 years. One corner on the front has badly cracked around the corner bead and the render has lifted off by about 4 mm over an are around 200 mm . The render is applied on to a render board which is a magply external BBA board. The thin coat is the Johnson high silicone 1.5 . First issue , Johnson’s advise that the magply isn’t an approved base and therefore thats why the render has lifted, but it’s ok everywhere else . They approve the knauf external board , which is a similar product , cement based board. Second issue , when the board was installed the corner was not battened due to the detail at the corner with a post , therefore the board over sales the batten by about 200 mm , which seemed solid at the time. I’m thinking this may be the issue causing differentIal movement at the joint ? 3. So I can remove the corner panel and replace it with the approved knauf board in that location. I will then batten the corner and reinforce it to stabilise it, but the render will need to be repaired and re sprayed leaving a joint line . Luckily it’s beside a door opening so only about 800 mm either side of the corner, but I’m concerned at cracking between the new and existing render as I will need a joint vertically above the door head about 400 mm. Any thoughts on the above would be appreciated
-
Depends on your attitude, ideally weekly but the risk is actually pretty low according to tests I’ve seen. But compliance with anti legionella advice would be more often. I can’t open the report but I would suspect it is .
-
Hi actually it can vary 10 is max nominally around 7 but it varies with the underfloor design. Usually this is a specialist supplier so it may vary depending who is selected. 25 seems low however if it works that’s great , you must have a well insulated house. The problem as a designer is that the output can be radically affected by the occupier, so furniture, carpets , rugs etc need to be considered. I see here that most people are self build so you know what the end game is and it’s very interesting and informative.
-
If this is a new slab then it will take weeks to dry and therefore the return temp will be low As far as flow rates are concerned unless you have the indicators on the manifold then it’s pretty difficult unless you have an ultra sonic flow measuring device. I have recently installed under floor in an anhydride screed and it has taken 4 weeks to stabilise with a flow of 55 C . As you say increasing the flow made the heat pump work hard it suggests that the system is under excessive load which is an indication of the load on the slab evaporating moisture. It’s pretty normal on a new system .
-
Yes possibly there is an issue but I wouldn’t position a manifold that far away that it’s an issue. A local bathroom manifold seems the sensible answer served from a suitably sized main.
-
I’m amazed it’s working at all at the low temp settings you have if it’s a slab. The recommended max floor temperature is 28 C , so I’d up the temperature to get to that on the surface Also the warm up depends on differential temperature between the pipe and the slab, so the heat transfer rate is a lot less at reduced temperature. This is known as exergy https://en.wikipedia.org/wiki/Exergy
-
The altherma set up is a bit tricky and requires a number of dip switches to be set . You should have a commissioning report as this https://www.daikin.co.uk/content/dam/dauk/document-library/Warranty/Daikin UK Commissioning Report.pdf ive had numerous issues with these not being set up correctly, so that’s the first thing I’d check. Thats the first thing , as there are priority settings that can effect the operation. I assume it has an electric boost in the cylinder as 48 C should be boosted say once a week for anti legionella. SAP is not a designers tool , it’s an energy assessment and I would not rely on the figures as it looks a heat balance not heat loss. ie it includes gains from lighting , cylinder heat loss, pump heat emissions etc. Many houses will use double the energy in the assessment !
-
Seems to be a big discussion about flow rates and pipe sizes here. The whole system should be calculated and the pressure drop assessed. Sizing on velocity can be risky in some circumstances ie low pressure. I don’t really understand why you would pipe in 10 mm , it’s not any cost saving . just run 15 mm and reduce at the outlet . I would add that if you are using flexible connections the bore on some is reduced substantially. These can delaminate over time so better to flex 15 and reduce after the flex in my opinion. I also note some of the flow rates and wonder how you are complying with the requirement of Part G of the building regulations . I am not up to speed on this as I’ve only used the Code for Sustainable homes in the past.
-
OK I assume this was traditional connection. I’m not sizing the system agree I would normally allow 25 max on domestic houses. interesting about the showers , anything over 10 l/ sec is seen as low efficiency , in commercial, i would only use 6 l/ sec, and I have that at home also and the shower is fine .
-
Yep,I did think that also but if it was working before then something has changed either with the system or the room. micro bubbles can be an issue but it’s not something I have encountered on under floor heating.
-
Hi it’s interesting about the heat pumps, provided that yours is fully inverter controlled,then over sizing is actually probably more efficient as the heat transfer through the exchanger is more efficient. A COP of near 3 is good for ASHP. I’d be interested to know what the annual COP is if that’s a winter figure.
-
Integrating an MVHR to our build
Rich123 replied to djcdan's topic in Mechanical Ventilation with Heat Recovery (MVHR)
Thanks , I was a registered SAP assessor for 10 years so I understand . -
The shower flow rates will be lower than 14 l/ sec, I would suggest 8 l/ sec . High shower flow rates are not very energy efficient for one reason. And the flow rate is split Hot Cold with about 65% Hot so the cold flow is quite low. 32 MDPE will be fine for the supply to the house. I would supply 15 mm to all outlets. It is normal practice to allow diversity to all of the outlets and generally a 22 main to a bathroom Is more than adequate. The mains incoming pressure will vary, but you can ask the local water authority to check the pressure if you can’t do it . It’s unlikely it is less than about 1.5 bar so you should get 1 bar at the shower heads which is adequate for a mixer shower. I would also add a pressure control valve on the inlet. A decent shower valve and don’t forget it is a requirement for a thermostatic mixer on the baths , I would use a TMV3 standard valve for safety. Re hot water , a combi of minimum 35 kw to get 2 showers.
-
Hi I think I would blow the pipes through with water , that will deal with any air locks and possibly any sludge build up. possibly the thermal actuators are leaking , they rely on expansion of the fluid so it’s possible that there is a slight loss , try removing them to see if the system operates better.
-
The standard design temperature drop of underfloor heating is 10 degrees, so a supply of 32 c would mean a return of 22 c. If it’s a new system in a new floor then it also depends on the type of floor and any moisture which will add a load to the system. My thought is that a supply temperature of 32 C is low and I would raise that to 40 C at least . if you have flow balancing indicators , then ensure that these are correctly balanced. Also check that the pump is set up correctly with proportional flow selected .
-
That’s great and it’s good that they have been honest and are rectifying it , 14 kW will be fine I’m sure . Also ask them to commission it and let you have a certificate with all of the settings on .
-
Yep agree , I had to do CPD and actually I was attending at least One a week , with suppliers etc and then training at CIBSE and online . And then additional research etc so you need to stay on top. I retired 2 years ago and I am starting to get out of date with some of the new stuff already so I’ll need to check up on that . I hope i can assist in some way .
-
Integrating an MVHR to our build
Rich123 replied to djcdan's topic in Mechanical Ventilation with Heat Recovery (MVHR)
I it won’t effect the SAP as it’s based on the system not individual room heating . Most SAP assessors won’t be designers. If you add electric heating points then that will effect the SAP so if you are going to I’d keep that quiet. -
Integrating an MVHR to our build
Rich123 replied to djcdan's topic in Mechanical Ventilation with Heat Recovery (MVHR)
Yes air tightness is the issue , and with testing that’s a huge improvement over the past few years. Also Insulation , but also cold bridging which is important ( also a requirement of SAP). And I accept that there are issues with specifications of heating and real life values . Also there is a requirement for intermittent operation and that is also a big issue. I had an issue with some holiday homes and ASHP , they took forever to heat up , and I had advised a remote system to allow systems to be turned on in advance but it was removed to save money. Hence I’m a little safe when it comes to design. -
Thanks Joe , hopefully I can help a few people as well as get some advice myself.