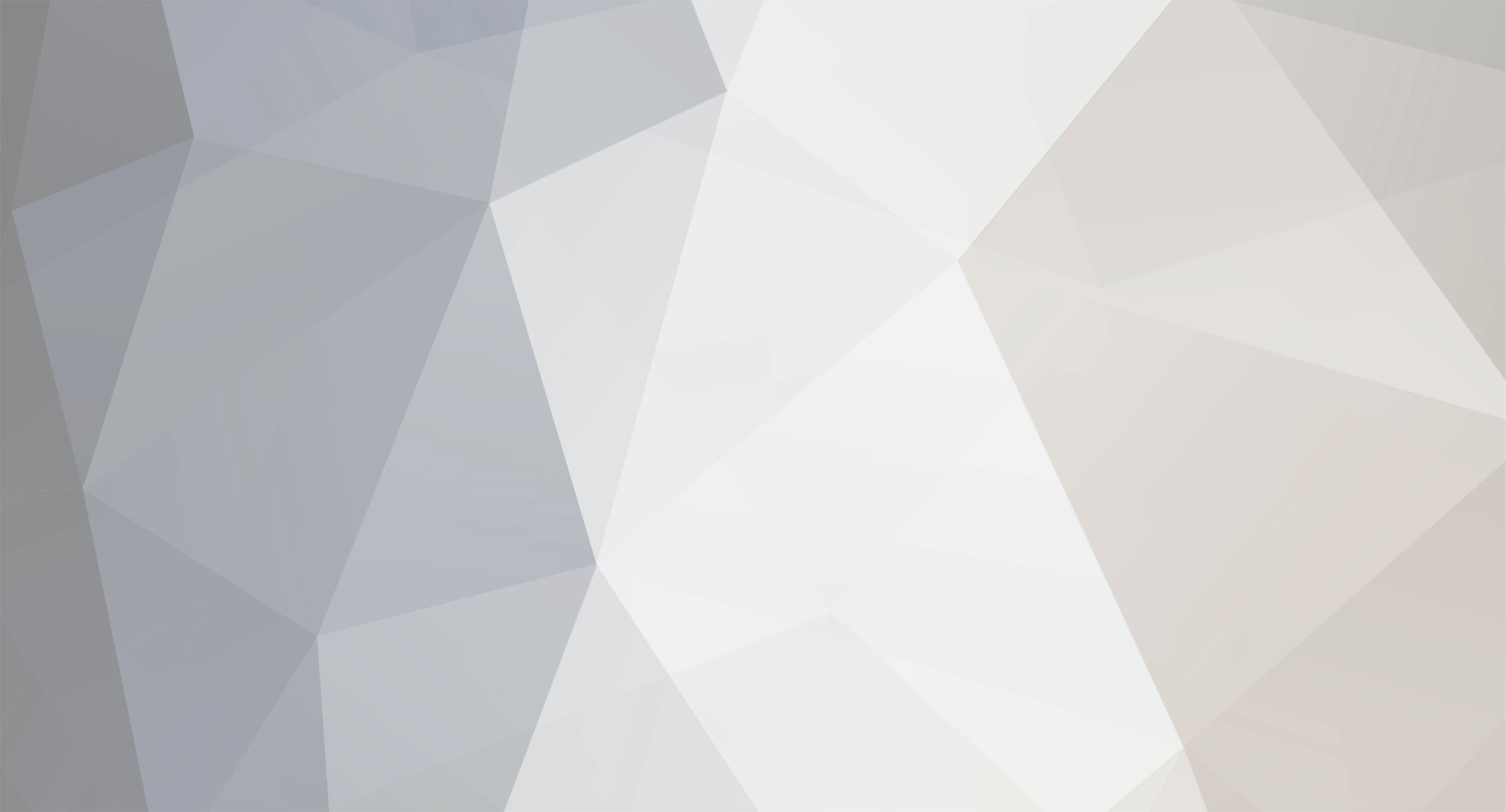
HaloThree
Members-
Posts
13 -
Joined
-
Last visited
Recent Profile Visitors
The recent visitors block is disabled and is not being shown to other users.
HaloThree's Achievements

Member (3/5)
1
Reputation
-
In the process of having my UFH installed by a gas safe contractor. The end state will be 4 multi-zone manifolds with actuators on each loop and no radiators. The manifolds have a wiring centre which allow for control of the pump, actuators and can send the signal to call for heat depending on the zone thermostats. The gas engineer has pushed for no zone valves to separate each manifold or each floor. He’s has pressed ahead and starting installing the first floor accordingly. I wanted to get your input on this approach please.
-
Thanks for the replies. I've got the UFH design/install guide that Wunda recommended which has the BS EN 1264-2 tables for the various subfloors and finishes. Striking the balance between required heat output and the maximum floor surface temperatures (room temp + 9deg) across the different floor build-ups is the challenge here. Without having different flow temps for the different floors build-ups I'm unable to get the required heat output within an acceptable max floor surface temp. That's how I landed at 45deg (@200 centres) for the joisted space & 35deg (@100 centres) in the solid screeded area.
-
Hi all, I'm looking for some advice on options where different loops (on the same floor) require different mean water temperature to meet the required heat output. In this case some of the loops will be pug mix between-joist (at 45 deg) and some of it solid screed (at 35 deg). Wunda have suggested that I would need a separate manifold for the different temps. I think I came across a thread a while back suggesting this might be possible using actuators? Keen to hear thoughts on what's possible at a 10deg difference - and if a 5deg difference would make this approach more viable? If it's not possible then I'll stick to two manifolds - but thought I would check-in first and see what you guys think. Thanks
-
I've gone ahead and put up some metal C studs to bring the existing walls in line with the extension (new cavity walls). One side I've used 50mm C studs and the other 70mm as there was more room (both sizes at 600mm centres). The height of the studs are just under 3m, I had to splice extension on to the 50mm ones (with 600mm overlap) as I could only get my hands on 2.7m lengths of 50mm. The 50mm studs are close the existing wall at the bottom but are about 50mm out at the top because the existing wall has moved over time. The 70mm studs are about 200mm away from the wall, as they have been set to go flush with a steel beam rather than the cavity wall. I've been able to secure the top/bottom tracks to the concrete subfloor and the ceiling joists above. The end studs are quite tricky to secure to the existing building, but I've secured them to the tracks using suitable fixing. The 70mm side will be boarded with 12mm ply and then plasterboard (as it will be holding kitchen units), the 50mm side will have some 12mm ply where the TV will be hung, but the rest plasterboard and then a layer of plasterboard over all of that (so that the ply is covered). I've seen a post where @nod has suggested supporting studs by fixing pieces of track to the wall and to the C stud. I wanted to confirm if that was the best option in this case, and what centres to put these supports for the 50mm & 70mm studs please?
- 1 reply
-
- 1
-
-
Removing old plaster from this solid brick wall with an SDS has left it looking a little worse for wear. We're going to build a stud wall/battens in-front of this wall to bring it flush with the new extension cavity wall - I was wonder if it's worth mixing up some mortar or similar to give the bricks a bit more strength.. some are wobbly. Thoughts?
-
Hi folks, We're moving the downstairs toilet, kitchen and utility to the opposite side of the house. This is up against the party wall side of the house and further away from the existing drain. Looking for a sanity check before I engage the BCO on the matter, I've taken a look at the Part H document and tried to make sense of it. See attached my proposed drainage plan - I would really value some input before I put it in front of the BCO. Regards,
-
Air-to-water & Air-to-Air from the same unit?
HaloThree replied to HaloThree's topic in Air Source Heat Pumps (ASHP)
Thanks Joth - I'll search the forums for fan-coil unit/fan-assisted radiator. In the meantime if anyone coming across this thread has any recommendations of these please do share! -
I'm exploring the idea of installing an air con unit in our upcoming open plan kitchen/living space to keep it cool in the summer. With full height sliding doors I've heard it can get quite hot! I'm also in the process of designing a renewed central heating/DHW system for the whole house (current plan is UFH, system boiler and indirect DHW cylinder) . Which got me thinking, if I'm going to go down the route of getting an air con unit (which I believe is an air-to-air pump), is there mileage in getting an ASHP that can do air-to-water for the underfloor heating in the colder months and then do air-to-air in the summer for air conditioning? I did a cursory Google and couldn't find anything of the sort.. Thoughts?
-
Approach to Temporary Works for Steel Beam Installation
HaloThree replied to HaloThree's topic in RSJs, Lintels & Steelwork
FYI - I spoke to the SE and he has advised that he can design a 'splice' such that the long span can be split into 3/4 and 1/4 if needed. -
My whole house UFH heating requirements have been calculated at approx 15KW, I've read many times that the rule of thumb is add 3KW to your central heating requirements for hot water (system boiler for indirect unvented water cylinder). I've spoke to the manufacturer of the cylinder I'm looking at (Telford Tempest 300L Indirect), and they've told me that the coil is rated at 15KW - exact wording was "The cylinder will require roughly 15KW". Am I right in understanding that I would have to have a 30KW Boiler (15KW for central heating + 15KW hot water) in order to reheat the cylinder in the quickest time from empty whilst the heating is on full. I'm keen to ensure that if the tank is emptied it can get back up to full asap. Thoughts?
-
Approach to Temporary Works for Steel Beam Installation
HaloThree replied to HaloThree's topic in RSJs, Lintels & Steelwork
Thanks all for your feedback, I'll explore introducing a pillar and see how we get on. Cheers. -
Approach to Temporary Works for Steel Beam Installation
HaloThree replied to HaloThree's topic in RSJs, Lintels & Steelwork
Hi @bassanclan - I've added the proposed floor plan to the bottom of the post. Thanks. -
I've approached a structural engineer with a view to hiring him to produce the structural calcs and designs for an open-plan rear single storey extension. I have attached a sketch which illustrates the proposed steel works. Before progressing I'm keen to get some feedback on the feasibility of installation, specifically the beam that spans the width of the property. Most of the installers I've spoken to want calcs and designs before engaging in conversation. My question is around the feasibility of opening up the wall marked in blue (see link to animation below) to allow for the beam to be located into place. The house is a 2 storey solid-brick 1910 semi. All examples of temporary works that utilise needle beams appear to be spaced ~1m apart which would seem problematic to manoeuvre the beam in place. Their are neighbouring properties either side of the site. Does anyone see a feasible way to do this or do I need to work to alter the design? Thanks, HT Link to beam installation animation: https://gfycat.com/lastdarlingicelandgull