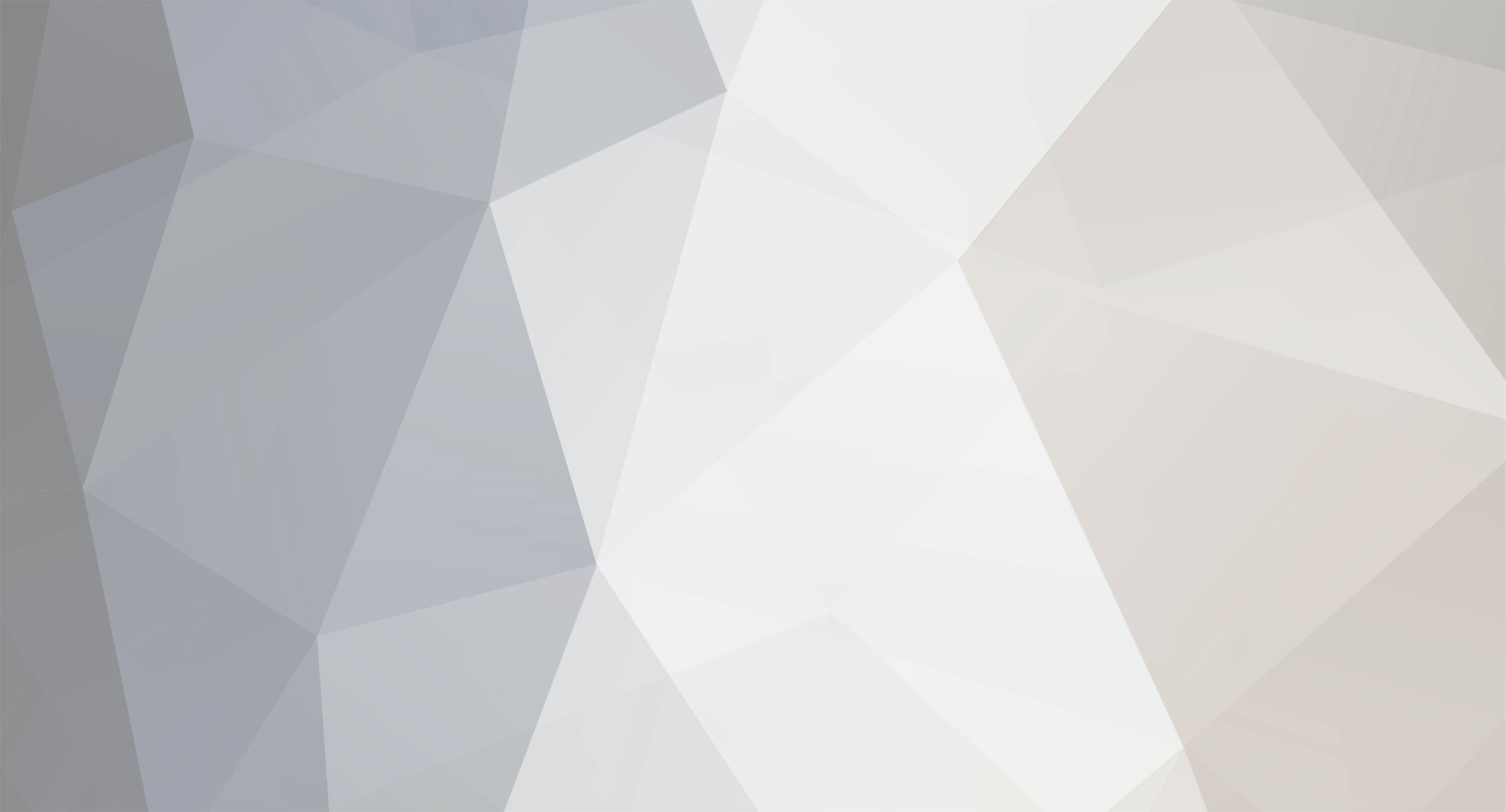
djcdan
Members-
Posts
139 -
Joined
-
Last visited
Recent Profile Visitors
The recent visitors block is disabled and is not being shown to other users.
djcdan's Achievements

Regular Member (4/5)
11
Reputation
-
My reason for insulating would be that the stone cladding - which would be applied just below the BBQ base on the face of the block - is adhered to the block using mortar. Would mortar cope with the potential heat transfer?
-
I am currently in the midst of an outdoor kitchen project, but am receiving conflicting information on the net about materials to use in the fabric of the BBQ/fire pit planned. We'll be having an open grill with direct heat on the base of the BBQ area just beneath the grill. I would like to line the bottom, sides and backsplash in a black coloured natural stone - I'd been looking at granite offcuts from our local supplier. However, there is conflicting information whether granite can take the temperatures generated by wood/charcoal embers. I would be black firebricks as a backup option but in 220x110 blocks it would look overly fussy and would prefer a single slab of something purely for aesthetics. Beneath the slab/firebricks which will be taking the direct heat, I feel as though I need an insulation layer as a barrier to below (which is blocked and stone cladded). I have come across Ceramic Fibre Insulation board, however the only viable supplier of this charges an absolute fortune to deliver just the one sheet needed on a pallet to my location! At the same time, the information on the net isn't conclusive that this is the right material to insulate and have also read the material has been linked to health and cancer risks. Therefore my question is two part: i) Do you think it would be suitable to use a natural stone directly against the heat, if so which. If not, what alternative would you suggest? ii) What material should I be using beneath as an insulation barrier? TIA
-
We have a window in our bedroom on the gable with the top of the window following the angle of the barge board therefore meaning the top of the window is angled. It looked great on the plans, but in practice it is a nightmare to dress with a suitable blind at a suitable price. It would need to be blackout. What have others sourced in this situation? Any suggestions or links to products/companies would be greatly received. TIA
-
Hi. I am needing to purchase ducting for our AEG combohob to complete a recirculation setup. I know these pieces are purchased from AEG directly. Problem is, I cannot find a piece shown in the manual on AEG's marketplace. I am hoping that someone here has also installed the AEG combohob with recirculation and can point me in the right direction. The part I need to find is the item coloured in light grey in image 9a.1. I am aware that the dark grey is the carbon filter but I do not know, and cannot find what the piece is that connects between the hob and carbon filter. Does anyone have any ideas. AEG themselves were not too helpful...
-
I would presume since it is on the Scotland Homesafe website, that this meets Scottish Building Regs? It has a display as required but is a little more inconspicuous than the other options.
-
I'll need to look for an alternative that doesn't look like a 20 year old hospital monitor? My bedroom will end up looking like a GP's office 😄 But on a more serious note, the wiring is done, boarded and plastered. There is no back box with wiring for a wall mounted monitor. Is it an absolute requirement that this needs to have an integrated display and wall mounted with its own main power supply? Is battery power out of the question? Is there any scope to omit this requirement now in your opinion? We also have MVHR.
-
Ah, ok. Thanks. So perhaps Aico's enviromental sensor would be appropriate? https://www.cef.co.uk/catalogue/products/5052860-temperature-humidity-and-co2-environmental-sensor?gclid=Cj0KCQjwjN-SBhCkARIsACsrBz5kb3egrkVB4o1nqsl6x22rocvOr89GhsoF50ehfLp4Tu8_lOClOq8aAhEUEALw_wcB&gclsrc=aw.ds Right now, there is a loop of cable coming down from the ceiling for mains installation. If it isn't to be mains installed/linked, I presume pushing the cable back above the plasterboard and installing the environmental sensor (powered by battery) in it's place would be sufficient here.
-
-
Specified on our house plans are: x2 heat alarms x6 optical alarms x2 ionisation alarms x1 carbon dioxide alarm Alarms would need to meet the new Scottish regs since we're north of the border. All the wires are in for mains powered. Aico seems the generally accepted brand here. However, am I being daft? It doesn't seem that Aico sells a carbon dioxide alarm or am I looking at the wrong thing? There are several listings found on Google that claim to be a CO2 sensor, but the packaging shows Carbon monoxide sensor in the image on the product listing. Aico also launched an environmental sensor, which does include CO2 sensor, but it seems a little OTT and doesn't appear to interlink with the rest of the alarms.
-
I have slate tiles going in to an ensuite. The thickness of the slates are 12mm. There are many 12.5mm trim options available (it further limits options it because I want matt black finish and metal), but I'm aware that the trim should be a little deeper than the tile, so had been looking for 15mm. My question is, will I get away with a 12.5mm trim for 12mm tile or should I get the idea out of my head?
-
How to achieve sound proofing/noise insulation in the house
djcdan replied to Indy's topic in General Construction Issues
My father-in-law was an acoustician and insisted we install resiliant bars as a cheap and easy solution for decreasing sound transfer from one room to another. As well as this, we did a lot of double boarding and all internal walls and ceilings had a sufficient layer of acoustic insulation and the results are a nice surprise. My parents built a very similar construction to ours, but didn't take sound transfer in to consideration and can hear others using the bathroom elsewhere in the house. We can barely hear a relatively loud radio from one room to another. I'd definitely recommend resiliant bars: https://www.floorscan.co.uk/product/db-resilient-bar/ was my supplier. Cost me about £650 inc VAT for the entire house (downstairs ceilings and all partitions where sound transfer wasn't desired). -
Cheers everyone. I'm still a little lost about which of these are trowel size and which are bed depths. Is the top quote bed depth and bottom quote trowel size? And so you wouldn't worry about adjusting bed depth to tile size or whether it be on the floor or wall? From what I understood, you're recommending matching bed depth to tile depth, so a 9mm tile would use an 15-18mm trowel to get a 9mm bed depth with bb and a 12mm tile would need a 20mm trowel to get a 12mm bed depth with bb? Wouldn't be so much of a problem if the closest Topps (or any other tile retailers) weren't 3 hrs away 🙂. And the local BM's take the piss on materials like this, quite comfortably 50-75% higher than online trade supplies, which results in me shipping a lot of mats in myself.
-
First time tiler tying to work out the materials needed. Currently calculating how much adhesive I need and answers on the net are surprisingly inconsistent. Hoping some of the experienced folk here can help. My understanding right now is that you generally use a trowel size a little smaller than the tile thickness itself. So 8mm for 9mm tile or 10mm for 12mm tile etc. On the floor, you'd maybe add a mm or two extra? For large format tiles applied to walls, also add a mm or two? The floors I have to tile: 2.5sqm 12mm natural stone on backer board 5sqm of 9mm porcelain on backer board All on top of electric UFH, but I don't believe that makes a difference to the adhesive thickness, just to make sure it's flexi enough. The walls I have to tile: 13sqm of 12mm natural stone - half 200*random (on backer) and the other half 600*300 (on moisture board) 22sqm of large format tiles - 1200*400 (on moisture board) 1.5sqm of feature mosaic (mb) 7.5sqm of 9mm porcelain - 100*400 (mb) Based what I calculated needing for the beds and the coverage rate of adhesive (20kg bag covers 4.5sqm at 3mm bed), I calculated that I'd need around 370kg of adhesive. However, I then thought I would double check on one of these online calculators, which said I'd need only 160kg. I'd rather not be left with ten bags of adhesive at the end of the job, so what is the more accurate answer? TIA
-
I am looking for local quarries anywhere in West Scotland or South West Scotland who cut their own stone used for floor tiling. Is anyone aware of options? Using a natural, local product bought direct from the quarry appeals. I'd be looking for either granite or slate. I am aware of a few in the Lake District through my father in law's recommendations who also have a scrap pile with discounted rates for left overs/scraps (ideal for me with relatively small quantities). If anyone is also aware of quarries who do this, that's a bonus! TIA
-
Floor is to be carpeted.