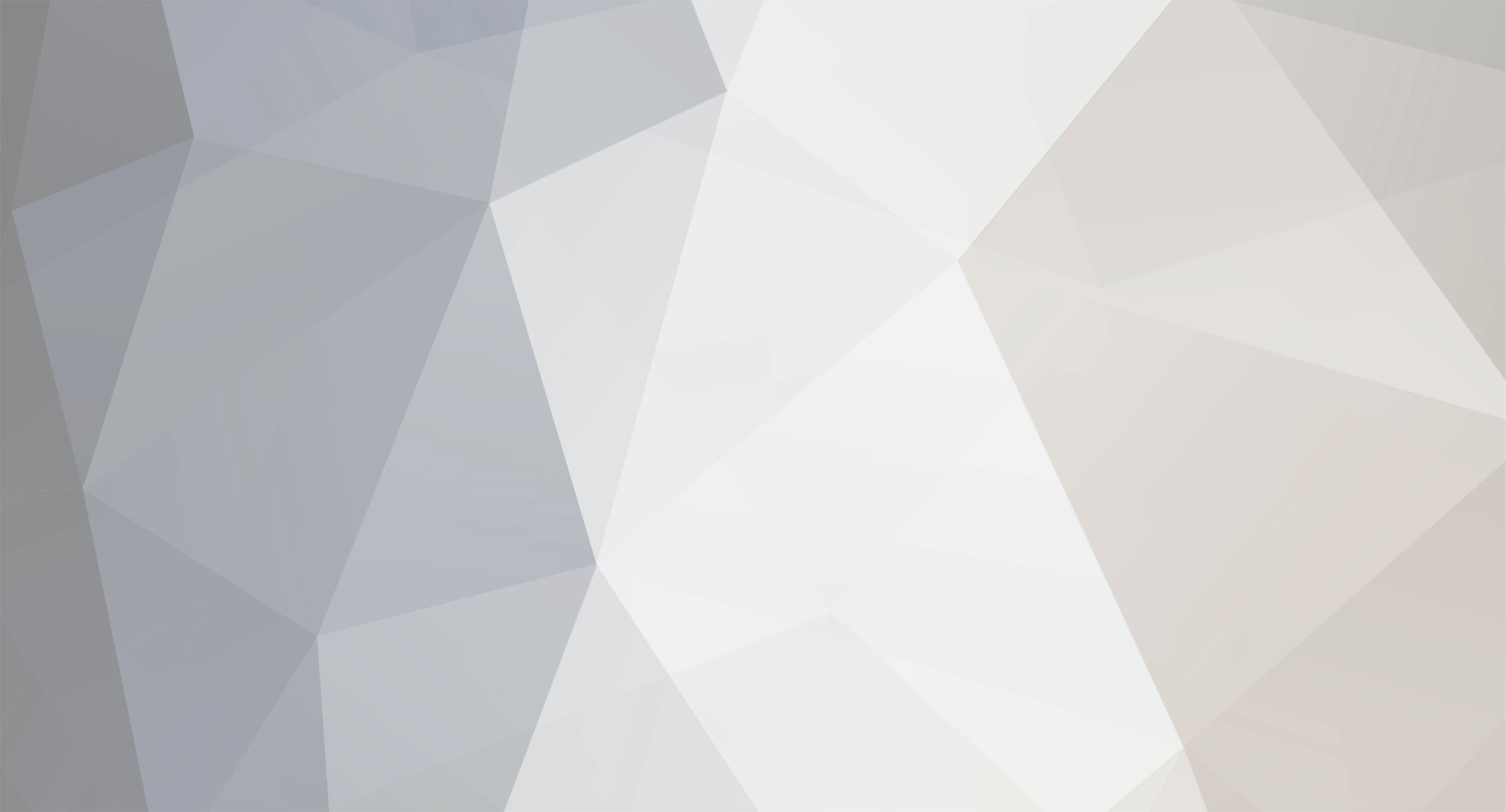
Gus Potter
Members-
Posts
1846 -
Joined
-
Last visited
-
Days Won
20
Everything posted by Gus Potter
-
This New York skyscraper had a 1-in-16 chance of collapse.
Gus Potter replied to Alan Ambrose's topic in Research Resources
It looks like what you are intending to do is to create a horizontally spanning wall, hence your placement of the rebar on the outside face as the load is from the inside outwards. I have my doubts as to whether your framework is strong enough for it to work this way. Your column to rafter connection looks iffy and the timber bolted joint between the bracing and rafter will likely not pass a design check. For economic wall design for grain or cattle we often run a cee channel along the top of the wall and this way we convert into a two way spanning wall. But for all that to work we need a decent steel frame and we need to be careful around openings as these interrupt the spanning assumptions. My feeling is that your steel frame is too slender and flexible thus you maybe just want to see if it can resist the wind load and snow load alone and then design the grain / cattle wall to be free standing. If you are willing to install a good thickness of floor slab then you can use that to restrain the vertical cantilever wall.. with a good amount of rebar. -
This New York skyscraper had a 1-in-16 chance of collapse.
Gus Potter replied to Alan Ambrose's topic in Research Resources
Ok it's a shed, call it agricultural. I used to do the SE calcs that underpinned the software that was used to design these sorts of things. So technically I've had a hand in, as an SE, in thousands of these types of frame, all over the world and not just in the UK. So I know a bit more than many SE's about this. But let's be pragmatic and look at the risk if it falls down. First thing is we don't wan't anyone to get hurt. To reduce the risk we want make sure that folk are not near it or in it when it snows a lot or it is windy. In agricultural design codes we call this the duration an occupancy rating. If it was a chicken shed then you would only be in it say 2 hours a day and there maybe only two folk at the most at any time. Now the other thing we look at is how close to the boundary your shed is. If the roof flies of your shed and hits a house or a car driving along the road that is not good. In the agricutural design codes there is a bit that deals with how close to the road it is. So once we have dealt with the risk you may or may not want to get some insurance. Up to you but some places like yours are next to care homes and schools.. catch my drift. Now once we have satisfied ourselves that we have not done something that is downright dangerous we maybe want to look as how the building moves about. Is is going to move differentially at roof level so much that within a few years the roof cladding fixing start to oval and leak.. then we have wasted out money or if it is just for that we can we live with a bit of a leaky roof? Don't do this unless you design them to be free standing.. it's bloody dangerous other wise. Or you can get an SE to sort this out for you properly. -
From my pheasant rearing days a Fenn trap is a satisfying solution. No nonsense, but you must protect it to stop other wildlife from detriment.
-
Ha ha..this is a hot topic on my books at the moment! story for another day. The secret is in the detailing. Let's go back to traditional leadwork. In any place where you get regular dripping of water then we would go for code 5 lead as a minimum . Your first port of call is to look at the exposure condition, is it sheltered or near the coast with salt in the air. Next is to refer to say Kingspan cladding techincal data for steel coated panels, similar to Greencoat... your cill is just the same. To give you a direct answer in ideal conditions say as a roofing panel away from the sea.. 50 years.. but as a cill maybe not unless it is under shetlered eaves. But will your window last that long?
-
This is a good conversation as it lets new folk on BH see what can crop up and how you might go about dealing with things. There is I think at least four or more BH members chipping in on this topic, including yourself who do this as a day job. OK. In the round let's take these welds as a case in point. I pointed out why I would not pass them and uploaded a guide to weld inspection so that folk on BH can get a feel for what might be a good or a bad weld. Temp pitches up, no mucking about and says they are crap. I responded by saying let's not panic .. can we be pragmatic and find enough good weld that will do the job. "So far I've not met an SE who didn't concur that my 'bespoke' solutions wouldn't pass with flying colours." And that is an interesting statement. I work from time to time as a checking SE. In a post earlier about William Le Messurier, the wind thingy on tall buildings off the back of what @SteamyTea was saying. One of Wiliams errors was that he was arrogant and self appointed not least, he would broke no dissent as a person and that primarily lead to his downfall. The point here is that SE's especially in this day and age make mistakes. I make mistakes occasionally when I do calcs. But I have a process that picks these artithmetecial errors up nearly all the time. Nine times out of ten these get spotted in house when doing or looking at the drawings as your eperience tells you.. that does not look right! Nine times out of ten when I check other SE's calcs I'll find mistakes. Some are benign, some are dangerous. I had one recently where the wrong axis of notation had been used by a well know UK SE company. The design was dangerous by a long way. But the main thing was that we caught it early, it was dealt with an no one fell out. On this project we are all experienced Engineers and designers and recognised that we caught it in time. And that is why you probably want Nick to do your job! It's rare these days to find a builder / commercial designer / project manager that has this commitment. "welcome being dumb and well rested, trust me!!" and then you would die of boardom Nick! Keep doing what you are doing.
-
No, but that is the great thing about the building trade.. oh I've admitted this on BH before. When I was a building Contractor in my last life I did a telephone exchange conversion for Mr Boom the Man on the Moon. He went off to AU and left some of his stuff under a hap, it was big pile and in there was his tractor, never lifted the hap as it was his stuff. He came back and said "where is my tractor?" I said what tractor! He said the one under the hap. So now the tractor is boxed inside the conversion and won't get through the narrowed door openings Luckily a couple of lads who worked for me were Farmers, they took it apart and reassembled outside.
-
What's the case for not getting an ASHP?
Gus Potter replied to kentar's topic in Air Source Heat Pumps (ASHP)
My thoughts as a philistine are. By all means look to install an ASHP and let it tick over most of the day and night, It makes sense, less wear and tear on the switching and moving valves. Think maintainence and cost of that, this is key to long term performance., often overlooked on BH. You can have as many fancy controls as you like, but these will all break down at some point and you may want to sell on the house so you might want to make sure your ASHP is an asset rather than a liability. Let's say you can square that circle, size you tanks and so on. If I was you I would certainly look at ASHP as a solution. But here is what I would do first. "The loft has been insulated up to standard 10 years ago." This is your low hanging fruit in terms of improving the existing insulation. In Scotland we look for a U value of 0.12 W/m^2K. To give you a flavour for this 400mm of glass wool will get you over the line. But you must make sure the roof void is properly ventilated, loft haches are sealed and you are not pocketing up bathroom down lighters that let moisture into the attic. You can't go flooring the loft unless you ventilate that properly also. Look at the type of roof you have and see how you can ventilate it. "My property is early 1900's solid wall construction." There is a good chance you will have a timber suspended floor? Now you are going to spend a pile of cash so you want to make sure your floor does not rot. Make sure you get that ventilated properly. Now it may be that you are going to do some work that will let you get extra insulation into parts of the floor. So you trade that off, you have now plenty ventilation under the floor so you need to get the skirtings and so on air tight. Your solid walls are probably more insulating than you realise! But it's the apertures (windows and door) that will let you down. Spend time getting this detail right. In summary I think it's doable but unless you are going to live in the place for a very long time then it will take you a long time to get your investment money back. Some folk are happy with the techy stuff as it becomes a hobby and are happy to take the financial risk and potential right down when they sell they house. In terms of ASHP cost and sizing. There are a few on BH that say.. ok lets design for 11.5 months of the year and if it gets a bit chilly then we will plug in a couple of fan heaters. This make much sense! -
I was trying to be diplomatic. That said as an SE I come across this quite often where folk have done remedial stick welding, not ground down the surfaces and so on. Yes, I could be anal about this but what I do on site is often to get everyone together and say what is the problem and how much load does the connection need to carry. Are we doing something that might chuck load in unwanted places? We then look for any part that might be a good weld and say ok.. can we count that and then check.
-
This New York skyscraper had a 1-in-16 chance of collapse.
Gus Potter replied to Alan Ambrose's topic in Research Resources
Well that is my good turn for the day, make folk laugh! Glad to see you used the backhoe as much safer than trying to yank it with a telehandler? To be serious, looks like you have done the job getting that to 5.0mm per m, well done! What's going on with the top of your column to rafters connections? I don't know where you shop for your clothes but these look a bit like a "summer blouse". Are you going to leave one side open. Any ideas on wind bracing as yet? -
This New York skyscraper had a 1-in-16 chance of collapse.
Gus Potter replied to Alan Ambrose's topic in Research Resources
Yes I think I mentioned this a few years back. It was the quatering wind that blew the gaff. It was from memory a student at uni that was looking for a dissertation project and that is where the "discovery" started. There are a few on BH that are involved or have been in education. One great example here is Jeremy Harris. He wrote some design codes, has a huge wealth of knowledge. From time to time I discuss with other Engineers / designers what we call loss of grand father experience / loss of tacit knowledge. You get to call yourself a designer when you have enough experience to appreciate that what you do is an art underpinned by your theoretical knowledge. One theme that crops up a lot is that the latest generation, given the information over load that young folk experience means that they just don't have time to look back two generations and learn from some of the horrific mistakes. Tacoma narrows brige is a good video! The other big problem is that young Architect's, SE's and other construction professionals are under a lot of commercial pressure which leads them in to more specialist areas of design.. they just don't have time to learn more about the general design craft and that leads to mistakes. In summary you only need to be a self builder trying to get your TF manufacturer to talk to say your Achitect or SE to see the results of this. -
Fair enough. Sometimes though we need to be careful when doing remedial work on site. As SE's we often deliberately design connections to be flexible. If we make them overly stiff they attract more load and that load can go somewhere we don't want it to. A good example is say you have a two storey house and converting the attic. Often you find that someone has knocked a hole in the central spine wall to create a more open plan space on the ground floor and chucked in a beam. You do all the right things, sistering the attic joists and so on. But when you first look at the attic floor joists you see they are lapped over the spine wall by max two feet (600mm), so the joists are simply supported and mainly act as ties to stop the roof spreading. But sistering often means you are making the attic floor joists into a continuous member and that stiffening attracts a lot more load onto the spine wall which can then end up on the ground floor beam.. and then trouble can arise as it was never designed for that. So before you go welding stuff to death stop and think.. are there going to be knock on consequences?
-
This New York skyscraper had a 1-in-16 chance of collapse.
Gus Potter replied to Alan Ambrose's topic in Research Resources
It depends.. but for all self builders out there. Often in my sometime lengthy submission to BH (this is kind of one of them) I refer to the Bristish Standards as they are often easier to understand and still applicable particularly to self building. But in this case to get a handle on things we are better to look to the Euro codes as they expose more of this factor of safety malarky cf some of the Bristish standards which work on permissible stress, not that many mind, but enough.. all the safety factors get lumped together. Let's take a steel portal frame first. This could be an agricultural barn conversion. Most design codes recognise that many are put up out of plumb, the steels are not straight due to the hot rolling process. If you have seen steel erectors work, they have a sledge hammer in the van, they use drift pins, crow bars, the tele handler (when no one is looking) and straps to pull things into place to get the connection holes to line up for example. When it comes to levelling base plates, you maybe need to go and have a tea break if you are a Client / Engineer. To help us get round this we assume that the frame is erected out of plumb by 5.0 mm for every meter height. 5.0mm / 1000mm is 0.5% gradient. This means that on a 6.0m high steel portal the roof could be sitting off centre from the base plate by 6.0 x 5.0 = 30mm. We then calculate this eccentric load and apply as SE's in our design, this is what we call a notional horizontal load, which is basically a saftey factor on workmanship and manufacturing. You'll also find this figure in the British Constructional Steel Association guide to Steel erection which describes an acceptable level of workmanship that can be reasonably expected on site. Ok turning now to timber design. Typical thing you see on BH is folk using joist hangers and angle brackets. If you take say a Simpson Strong ABR 9020 bracket. Here they declare the Charachteristic strength which then gets divided by a material factor of commonly 1.3 to give the design strength, sometimes shown as the design load. Don't mix this up with a safe working load as the loads also need to be factored UP first. There is no workmanship safety factor here. The workmanship is controlled by other bits of the design codes where we make sure the nails have adequate edge / end distances and so on. If the chippie / joiner does not follow the drawings or has not been properly trained there is no fall back position. Masonry.. bricks and blocks. Here again we rely on, as does many other aspects of the build porcess, on the British Standard 8000 series which relate to workmanship and tolerances. But qualitively we could look at the BS 5628 part 1 for a bit of ball park guidance. Below is a screenshot of the masonry table. Normally you see SE's using the bottom right saftey factor of 3.5 as the factor by which we reduce the strength by. So say you are using a 7.0 N dense concrete block in an class (iii) M4 mortar. Characteristic strength is 6.4 N/mm sq. Take the 6.4 / 3.5 = 1.83 N/mm^2 or 6.4 / 2.8 (bottom left figure) = 2.29 N/mm^2. So in terms of construction control you get 2.29 / 1.83 = about a 25 increase in performance. But on a self build you just won't spec this as the reality is that the self builder will never be able to execute this, and to find a brickie that can is whishful thinking, then you have the additional labour cost. In the round then we need to establish a reasonable quality of workmanship. Here we may look to the NHBC guidelines and standards for tolerances on the masonry. In summary your workmanship needs to be to the design codes or manufacturer's recommendations. The manufacturer's need to sell stuff and it's fair for them to assume you can do the work to a reasonable recognised standard. -
On the face of it Nick I would say the welds are concave and not standard. I'm entitled to do this based on the photos, to make reasonable enquiry without being a tosser as best you can. NIck, I'm just saying as an SE that welds look concave and if this was standard SE stuff then it's fair for me to ask as part of my due dilligence to ask is that ok? are the welds heavily loaded? Welds can be pretty strong after all if not subject to bending forces. Now if the loads are low then you can reduce the throat width and the ones you show may be just fine. So yes of course I don't understand the overall context.. but what I'm trying to do in my posts on BH is to give self builders tools and reference documents that they can use to get the best out of things and to provide informationto help them say to a builder.. that looks no good and here is why I think this way. But I'm not going to back off from this. If the weld you show in your picture has been designed on a 6.0. mm leg length which gives you an effective throat width of 4.2 mm and I can clearly see that the weld is concave then it just looks off! Now it may be just fine as the loads will be low, but I'm trying to alert folk on BH about how SE's design normally, to support them when their gut feeling is telling them... that does @Ay8452 not look right to me. The whole connection and what is round about is looks seriously iffy to me as an SE. @Ay8452 banter hat off .. get your SE to check this as built on site for your own safety. You have thermailite or similar block in there be safe and ask questions. Ok banter on BH keeps the ball rolling. So in that spirit.. If we all got on all the time it would be totally boring. In Scotland we say.. "come on ya yadge" I think in Wales you break into song.. xxx
-
Ok I have attached a guide I use as an SE for Weld inspection. For all on BH it's a great document for getting a handle on what might or not be dodgly welding. If you are a self builder then it's a good document that you can refer to if you have worries about welding on or off site. Ask, raise your question with BC if they think the weld is compatible with my attachment. It is highly unlikely that they will know about this stuff and if they have any sense they will say .. I don't know.. if they say it's ok ask.. are you insured to put this in writing.. they won't be! As an SE, Client's ask me some questions that I don't know the answer to. I say I don't know but I'll go and find out! This is the mark of a professional but as a self builder you can read up also and be well able to make sure you are getting value for money out of folk like me that do this as a day job. What I can say is that if it is supposed to be a structural weld then it ain't going to pass. I'm telling you this as me! In fact if you look at the document I've attached you'll find that the welding is so shite it does not qualify as a weld at all! Now if you have a builder that is taking the piss what you have here is on site is welding that I bet will be non compliant with the staturtory HSE law on CE compliance for structural steel, that is you CE compliance (for structural steelwork see internet and the law) So at the end of the day if you builder is taking the piss they can go to jail! You probably hold a lot more cards that you realise at the moment so keep you head up! Don't accept this until you know more. Indeed Nick.. but as as SE the standard throat with is 4.2mm.. for a 6.0 mm weld leg length. The weld you show `looks of good quality.. but I would scrutinise this to make sure is actually has enought beef.. pretty it may be but.. to be blunt the weld in your picture is concave.. it should be convex so straight away I say.. it might look good in the pic but the throat width is not enough on apearance .. unless it is a partial penetration weld. So @Nickfromwales I won't be passing the welds you have shown either based on your photos! Guide to Weld Inspection of Structural Steelwork BCSA Book 54-12.pdf
-
Wall for floating staircase?
Gus Potter replied to flanagaj's topic in General Self Build & DIY Discussion
It's remarkably simple once you understand where the loads go and how the the treads twist (torsion) on these "flying stairs". The secret is in the detailing of the stairs, the SE stuff is straight forward! Often the stair does not need to cost a lot more.. but the time is in the devil of the detail.. making sure that the surrounding structure is designed and built so the thing works. Most folk on BH split stuff up into packages, seek the lowest cost.. so it does not work logistically.. but then you can't afford your "flying staircase" as everyone else has cut off your options.. and you end up with some crap version that probably costs you more anyway. One way is lets say I go and buy a motor bike off the shelf. Then I shop about and but the parts of ebay will cost me more. This is an affliction particular to self builders, but an unavoidable one. You need to know if you can afford to sefl build.. and if you have not done it before then your only way is to go the route of building a bike like by buying parts like a motor bike. This used to work ok as there was plenty money to be made in self building.. but now things are much tighter financially. Look at it this way.. these flying stairs have been built for hundreds of years.. do you think these old builders did this out of charity? For hundreds of years they know how they stay up.. in the last hundred years and a bit we have proved how they do their thing mathematically. The thing is look at how these old builders made their money! and then ask can I make the same savings! If you have a look on the internet and search for flying stairs in torsion you'll see how they work. Technically you can do this with a good thickness of oak tread with some modification and with a good stringer bolted to the masonry wall it will work also. Lastly you can also utilize the ballusters and handrail.. it's a traditional way but if you are enthusiastic then in the round it's massivley elegant as you use every part of the stair both architechturally and structurally. And if you put all that together then you are on you way to having a work of art! It does not need to cost the earth! -
Public liability insurance - nothing else (yet)
Gus Potter replied to Drellingore's topic in Self Build Insurance
Hiya. The film management should be used to sorting this out and I suspect that they will be a deviant (commercially of course) bunch. Look at it this way.. they could be surveyors that are coming to "measure up" and just taking some video with some commentary. If they are not used to building sites.. they are a liability. Now here you may come under more scutiny, do you have a principle designer, are you fully complying with the CDM regs and so on. Make sure you are fully HSE complaint, who is your PD etc? If one of the film crew get hurt (twist their ankle) you will be the first to go under the bus! That said I am rooting for you and looking forward to seeing you on the Telly! -
This New York skyscraper had a 1-in-16 chance of collapse.
Gus Potter replied to Alan Ambrose's topic in Research Resources
It is. When I was at uni I had a lecturer that was about ten years older than my self, I went to uni at 40 he was about 50 and had a long an varied experience first as a Civil Engineer (like @saveasteading) and then got into structures. He used this as a teaching example about how you need as an Engineer to "sense check things". A good Engineer uses a computer, maybe complex analysis (say FE) to refine the design, seek economy.. but we always use the model as a tool. We never take computer output and sign off unless we have sense checked it. That is dangerous. Another example is the Hyatt Hotel collapse. This came about because of; a simple steel detailing error, if the detailer/ engineer had put a big red note on the drawing.. don't (expletive deleted) about! , the contractor did not change things on site ( explain the buildability) all coupled with a loss of engineering oversight and site inspection. https://en.wikipedia.org/wiki/Hyatt_Regency_walkway_collapse Now in terms of self building.. always think before you let your contractor go off and do their own thing! Don't let them sway you.. we have always done it this way and we know best! The modern self build is becoming a lean design animal.. to make it worth while (you make some money) designers are pushing the boundaries and with that comes a need for builders to get with the programme! -
Oh dear, that didn't go well.
Gus Potter replied to Alan Ambrose's topic in General Self Build & DIY Discussion
There will be two sides to this! There are a few folk on BH that have built houses worth more than £3.0M if you include the land value. -
Wall for floating staircase?
Gus Potter replied to flanagaj's topic in General Self Build & DIY Discussion
What a lovely proposal. This floats my boat as an SE. I imagine you have seen a "floating" stair in say a tenement (Scotland) or a traditonal town house in Bath. I'll try and explain how these roughly work. Each tread is not a cantllever. It is supported by what can be a thin wall at the inner edge.` Simplisticaly the way we design these is to let the outer side of the tread rest on the one below and to make it work this has to continue all the way down. The treads are actualy, in torsion so where they are built into the wall the wall has to be designed to resist the tread torsion, so you need a good weight of wall above. By default the treads need to have torsional resistance. A traditional stone stair tread has enough beef to satisfy. You find more detail on the theory on the internet. It's not a design job for the faint hearted but most SEs can handle it.. but you'll need a good height of blockwork above (to provide ballast weight) and maybe some engineering brick round about the tread end where they run into the wall to take the local torsional stress. -
Public liability insurance - nothing else (yet)
Gus Potter replied to Drellingore's topic in Self Build Insurance
Ah.. that will change the game a lot! You'll need some new threads, a hair cut and so on if you are going to be on the telly! -
Good question. There is a lot of good technical comment from previous posters. MVHR is well proven technology if you design it right, build in a bit of spare capacity so you can sell the house on without copmpromising the value and live in a certain way. So in that context I'll paint you a diferent picture. Now I am a past self builder, site was in the country, like waaay out in the sticks. But round about me were other young couples that were also that were doing the same. Most wanted a house that was large enough to fill with kids. Most of us were in our 30's or a bit younger (but there was also a cohort of retiring folk who really got behind the ethos and they also wanted chickens and plenty fresh air.. like open windows and doors) and wanted to send their kids to the good local school, get chickens! And sure enough it all happend. Good teachers moved to the local school and it thrived. But it did not stop at chickens! Then there were sheep, goats, more kids, the dads got involved in the local scouts, the local pheasant shoot, (they learnt to shoot as the foxes were eating their chickens) their houses became a hive of activity.. the doors were open and shut from morning to night, the new kids got sick at first when they moved to the country so windows were open / shut .. Take a step back @Wadrian and review again! What function you want your house to perform. You are starting, it seems, to think about a bit of technical design..you'll get loads of info on BH so always review, it's Ok to change your mind as you go and learn more. If it just a house for say two of you that are in eh "later years like balding me" or a mental family with a country feel, you get to smell / topuch what is happening in the outside environment, If mental then MVHR is maybe not the best option in the first place! Personally as a designer, SE, ex building contractor with 40 years experience my personal horror is to live in a sealed box! It looks great on paper but few years down the road it makes no commercial sense to me in the self build market ( it will break down so if you can avoid installing it in the first place? ) and is probably bad for your kids.
-
Mansards with no soffit ovehangs
Gus Potter replied to jackcowdrey's topic in Lofts, Dormers & Loft Conversions
Great comment and input from jackcowdry and Mike. Old roofs were so draughty with traditional sarking / battens that the last thing on the builders mind was to introduce more ventilation. Looking at these more modern photos I'm at a loss how they have ventilated it as the large format slates won't be helping as they are so tight. You could use traditional timber sarking with a 5.0mm gap between the boards and a breathable membrane (Tyvec Supro or similar) but again these modern slates are so tight you need to be careful. Potentially you could get eaves ventilation (50mm air gap up the roof with minimum 25mm width soffit ventilation) up behind the gutter but there is no ventilation at the ridge.. unless it's all hidden on the back side? The potential for damp at the Juliet balcony looks high. A bit spoilt by the plastic soil vent pipe. A nice bit of cast iron pipe would compliment.. if the budget stretched to that. As a rough guess it could work with a smaller slate size, a bit uneven with plenty air gaps between the slates.. but I can't promise at the moment! Food for thought though eh! -
Have a quick chat with your SE. It's often missed at the Architectural design stage.. you get hung up on the thermal bridging, water penetration and so on. But masonry cavity walls can be designed as vertically or two way spanning so they resist the wind load and stay stable (not buckle sideways) when you also load up say the inner leaf with floor joists or the roof which often sits on the inner leaf that load the wall off its centroid. If you put in DPC's wily nilly you can break the vertical spanning capability of the wall which in this case it look like you might have done. You have no wall ties at lower level so that looks a bit off so this is related to the above as you have a quasi rocker bearing in the wall. I've not spent long thinking about this but I would first look at, and then test my arguement: 1/ Delete the cavity tray that runs from the bottom of the cassette vent back up into the inner leaf. What is it doing when you have vulnerable insulation below it anyway? So now we have done something good structurally too! 2/ The DPC on the inner leaf is shown at top of screed level. I would look to drop that to bottom of screed (think buildability) level and then turn it down behind the insulation against the inner leaf and stop it 20mm short of the cavity lean mix fill to stop any potential wicking effect. 3/ Get another wall tie in below the lowest one you have shown to improve the vertical spanning capability of the wall. 4/ Your cassette vents are too high so the lower insulation and cavity are not getting air. Drop them and the outer DPC so they are just over 150mm above finished ground level. Draw that out, think about the structural side and mull it over. That is what I would do in the day job and then think does what I've drawn make sense! For the sense check, yes I've talked about the SE side but let's have a look at buildability and cost. Are we making things more expensive or are there any Architectural details that prohibit say the height of the cassette vents?
-
Public liability insurance - nothing else (yet)
Gus Potter replied to Drellingore's topic in Self Build Insurance
Interesting. I've been working and advising a Client that has been wading their way through the ProteK procedures, their fine print, how they are looking to offset their risk to produce, I assume, a competetive 10 year warranty quote. In the last couple of days this seems to be resolved and a deal has been done. I can say it's been a journey and I feel for the Client but they are now able to move on. I can't expand much more on the detail as much is confidential. From my experience so far with ProteK it may be worth letting the public liability slide for now. My reasoning is as follows: As an SE / Architectural designer my Professional indemnity insurance premium is quite a lot. There are two primary reasons for this. First is that if I cock up as an SE injury or worse could occur and that would result in a high level of claim. If you want to be an SE then a high premium comes with the terratory and we maintain that cover normally for 3 to 5 years unless otherwise agreed. Second. with my Architectural hat on if I miss something like daylight requirement, breach the building regs there will be a potential claim. ProteK, as you'll find out may or may not ask you for a plans check / the insurance the Architect or you carry if have drawn the plans yourself carry against a breach of the building regs. Again cover is for 3 to 5 years unless agreed otherwise. ProteK have "now" got the jist of the above. Now the above coupled with your (Contractor's site insurance) adds up to a fair sum, but all of the above cover most aspects of risk and what you are left with is the public liability (PL) insurance which is cheep in comparison. I think ProteK bundle everything up and that is why they don't want the hassle of separating out the PL as it's a small element. There are "commisions" and so on. To provide a bit of context my PL cover is less than 5% of my PI cover. This is where the premium could vary a lot, concentrate on this bigger ticket item rather than the PL. Check your fine print for contaminated land clauses and the statement of facts you made. They may have updated their documentation but note, SE's need to be insured, but by omission in their statement of fact questions an Architect or Architectural Technician maybe does not require insurance and thus this could infer that you can do your own drawings for BC as a self builder. Have a look at their PD (CDM) requirements and with that comes the need for a health and safety file at the end of the build. I'm sure you'll get it sorted out but you probably need to get a hold of a senior person at ProteK. ProteK as I understand (having sat down with one of their inspectors) sub contract (sort of) out their site inspections to independent surveyors. The inspector that came to meet me in my office was highly competent and appeared a dilligent individual which was reassuring I felt. In the round I got the feeling that ProteK are doing a good job, have quality surveyors, yes they might be strict but that is what you want surely.. to get your house right? Where I think they may fall down is on admin and the computer says no!