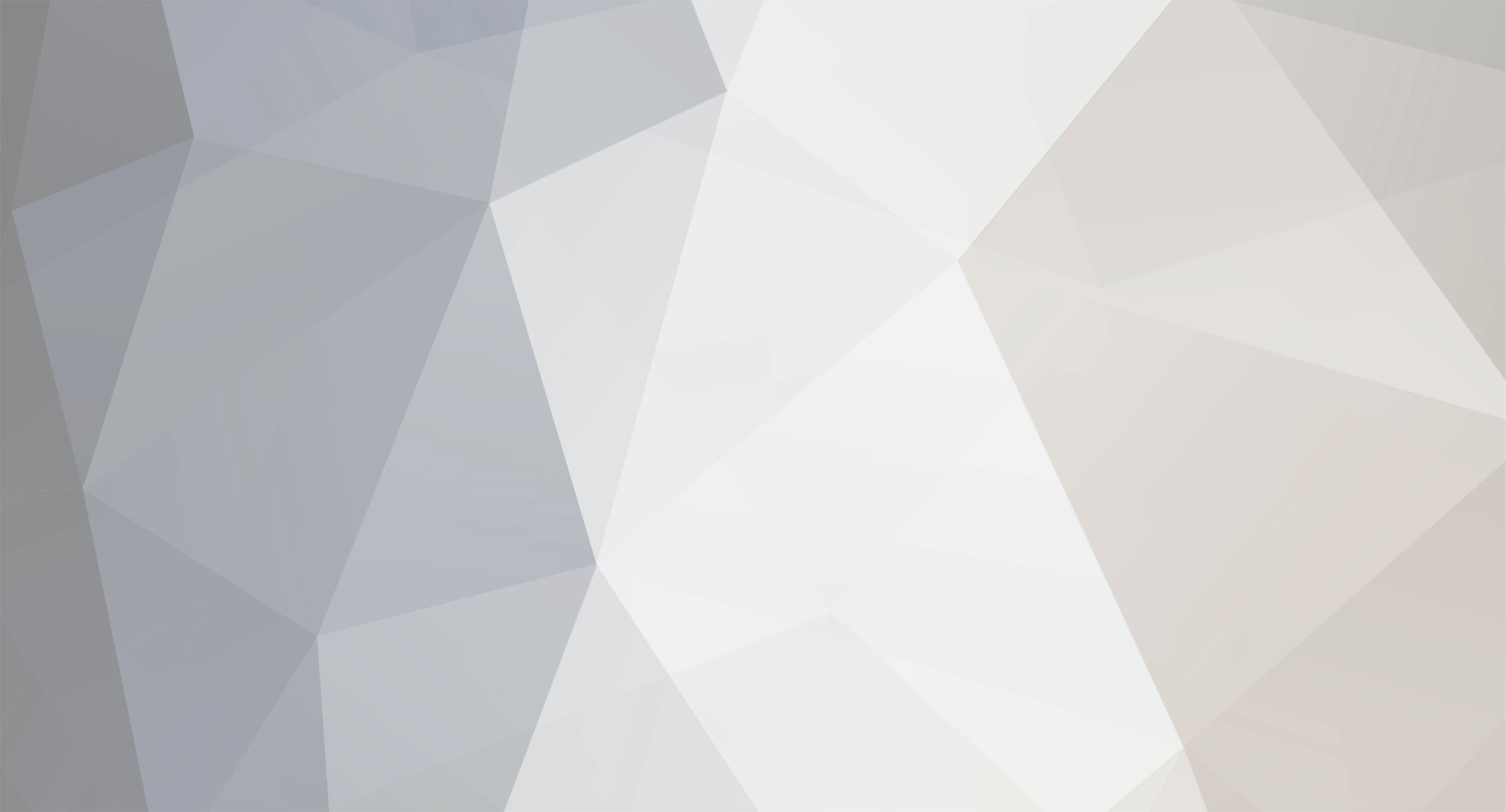
Olf
Members-
Posts
315 -
Joined
-
Last visited
Everything posted by Olf
-
It is probably 100mm, but that does not change you situation a lot: you need to dig up enough for the new structure to finish at existing floor level. over 100-150mm slab over 50mm blinding over 100-150mm compacted hardcore. This much digging is necessary. By the way, using PIR is typically the most cost effective way, as offets cost of digging and disposing against more expensive insulation. However, there are cases (soil easy to work with, can be used locally eg to level the outside) where using EPS (even though 250-300mm needed) is better choice. Unlikely here, but do your maths. Over the blinding layer (under insulation), binded to the existing DPC. That is likely some bitumen stuff, so Synthaprufe/Black Jack type of liquid membrane to link old and new together. Also another layer (not DPM as such, can be thinner, but also can use leftovers of DPM if enough left) over the insulation so screed does not flow through any missed gaps and reduces to 0 risk of any chemical reaction with aluminium film.
-
Questions on underfloor heating in a flat and insulation required
Olf replied to Honza's topic in Underfloor Heating
That would then leave you with This is to hold the pipes only Also, version with bonded aluminium layer acting as heat spreader will have higher emission (what you showed makes floor warm over the pipes only). And very likely will need some screed on top, so make it 3cm from current floor level. UFH retrofit does not marry well with finished floors. Back to basics, why are you so fixated on it? You have radiators in place, you could just do nothing. Depending on the layout, you could try skirting heaters though there doesn't seem to be experience with them on the Forum and they look like poor value for money for output tbh. -
Questions on underfloor heating in a flat and insulation required
Olf replied to Honza's topic in Underfloor Heating
You should be able, just look at your energy bills for last few months: pick the worst month, divide by 20 (30 would give average day, take the coldest day needed 50% extra) and you'll have your target. What about draughts? I had double glazed windows and behind mastic there were finger gaps around them: filling with foam did not take long and the difference is massive. You'll find many holes through the wall bringing frosty air in when you need it the least. Unlikely, and depends on many factors, some beyond control, so claiming '10% maximum' is an outright lie. Heat transfer through the floor = U (heat transfer coefficient [W/(m2K)]) x area [m2]x (floor surface temperature - what is under temperature) Well insulated (current BR) ground floor have U=0.13, let's say your flat have U=0.5. Let's assume your floor temperature (with UFH) would be 30°C and your downstairs neighbour at the ceiling it is at 20°C. 0.5x80x(30-20) = 400W, times 24h makes daily total of 9.6 kWh, @ 10p/kWh it would costs you £1 a day to heat your neighbour. When you get figures for heating energy needed, it should be easier to get percentage for your case. -
Existing run is at some fancy angle, adjustable would give freedom to match it. But that made me think and I should go for round gully, then I can align is as I wish and even 1 fixed bend will do! Unless the top on square one spins?
-
As preparation for EWI I need to move existing gully by about 25 cm off the wall (roughly marked by red square on the photo) My current plan is to go with + + Is there any easier way? Here is the current state: I've already found detailed answer to my question 'how to cut the pipe' https://forum.buildhub.org.uk/topic/24060-how-to-cut-this-clay-soil-pipe/
-
Not really, going under the foundations would be harder... By the way, as you already dug for the extension, BC should have very good idea about ground conditions, so you test hole in the floor will not need to go too deep: just enough to asses existing floor buildup. Something like this: UFH pipes tied (with cable ties, easier than rebar wire) to the mesh that is sitting on 'chairs' (but other options of keeping the rebar elevated are possible)
-
Very doable, but watch for: - what is your current floor construction? Make a test dig in a place you can easily fill in if you decide not to progress. I made 20x20cm hole under fireplace hearth and got good idea of the scale of a challenge - BC: agree what floor buildup is acceptable so you know exactly how deep you have to dig. I ended up with 150mm hardcore+50mm lean concrete blinding (what BC reqested and pi$$ed me off)+150mm PIR+100mm slab with rebar and UFH: total of 450mm meaning digging 350mm below existing slab. Don't think about reducing insulation thickness to save digging: it is not a passivhouse, your floor temperature will be at least 30°C and the last thing you want to do is to send too much heat into the ground. - test hole should also give you idea about soil condition: some are easier to excavate, some (clay...) are proper pain. - it can be done by hand, great exercise for back muscles - plan timing: do it after the extension is done and the area leading to entrance should be the last and done like F1 pitstop, otherwise life is challenging for few days
-
Foam Gun Cleaner - am I doing something dumb??
Olf replied to jayc89's topic in General Self Build & DIY Discussion
Soudal cleaner uses an oring on the tip, it is ether missing or stuck in the hand spraying nozzle attachment, so when the can is mounted there is no push against the gun. If that is the case and you can fix it, you are also likely to find that the oring stays in the gun. If not removed, when you load foam can it sprays BEFORE tightened... -
Questions on underfloor heating in a flat and insulation required
Olf replied to Honza's topic in Underfloor Heating
What is your current peak energy use for heating, what is total and available (not permanently covered by furniture) floor area? I assume you have already radiators, so no need for a new boiler? Are you planning any energy efficiency improvement jobs during renovation? If you define 'better' as 'longer and more disruptive installation but 1/3 of heating cost long term' then wet is better How long are you planning to stay in that place (what is you return on investment period)? You never mentioned funky stuff like wall/ceiling electric radiant panels - some people like it, even for the art some of them offer Cause on the ground floor even with 30cm EPS one loses 10% of heat as sacrifice to Mother Earth, and that at very low floor temperatures. Search here for horror stories of people who were conned into installing UFH without insulating and burn money yet freeze. Even with flat below, if you have to have high floor temperature (because of losses elswhere, hence do your homework in figuring them out) you may end charitably reducing bills of your neighbour. Tiles are always a winner for UFH, with vinyls do check spec of what max temperatures they like. With the bathroom be especially careful about calculating losses through walls, window and ventilation and all the holes through the wall vs available floor area (as bath, toilet etc take relatively large proportion). You'll likely end up with need for heated towel rail (which is helpful anyway). -
So it is actually a proper air conditioning system (cooling + heating), air-to-air, and unlikely to have heatpump - which is a bummer, as makes it less efficient than modern solutions. Keep it, it will still be useful especially for cooling in the summer. As for the main problem: If you want to keep existing water tanks (assumed immersion heated) as is, then indeed system boiler is the way to go. Not combi, as you have no use for DHW part of it, and so installation gets cheaper. Do consider using new system gas boiler for heating tank(s) too, even with investment in coil you may end up saving long term. Installing boiler and rads is costly and disruptive, do calculations if fitting modern (higher output, heat pump based) AC unit may not be a better option after all. Whatever you do, think about how you could insulate the building (internal walls, loft, doors/windows, reducing draughts etc) as whatever heat source you want to use, the less losses to fight, the cheaper it will be to install and run.
-
The right way to fill a gap between the window frame and the surround
Olf replied to bigandyt's topic in Windows & Glazing
Soudal Window System -
With extra detail in the original thread I now don't think it will be beneficial, but for reference: Foil face is radiant heat reflector, airtight barrier and (marginally) they equalise surface temperature. Radiant heat transfer between the floors is not going to be big (low surface temperatures and small temperature difference between them), so the extra cost of foil facing may not pay back. Airtigtness internally does not matter. So all in all not worth it internally, unless difference in price negligible (or other factors in place, eg supply of non-faced, having leftovers etc) For the reflection to work you need an air gap (but that will be the case anyway, explained below) and point it to the underneath of the floor. All the wools are intended to be supported from the bottom: even if you pack it between the joists, the panels can sag anyway as you already noticed. Addidng noggings wil reduce sagging, but not eliminate it - and that at a lot of expense in time and materials. Glueing is pointless, as the boards themselves have poor structure and can leave just the very top layer attached, with the rest going loose. I think it is safe to asume that ultimately the insulation may shift all the way down until it sits on the ceiling board, if not - that's a bonus.
-
OK, that is a whole different problem then! Adding insulation under the boards = it limits heat flow downwards = more heat stays in floor structure to flow upwards = reaching surface temperature quicker (=using less energy to achieve sufrace temeprature in that room, though kitchen will use more to maintaing temperature there). The same with changing flow temperature, fixing potential air blockages etc - they won't increase floor temperature, as it is capped by the protection. Once you start with floor temperature of 27'C (regardless how achieved) and the room gets only to 18'C, that means energy emission from the floor at 27'C balances all the losses through walls and ceiling, with 18'C being equilibrium achieved. From here I'm afraid there are only bad and worse choices: - increase emission by increasing floor temperature (adjusting cut off threshold) - risky - find and fix paths of heat escaping through the walls and ceiling - tricky and potentially costly. You did mention celotex in the loft, but how well laid? UPVC window, but how well fitted? What is the wall structure, if filled cavity then how well? Thermal camera would be your friend here. - if none of above then sit and wait for warmer weather, as then with the same floor output the losses will reduce and so equilibrium temperature increase. Addidtional heat source in the room necessary for cold periods like now.
-
This system seem to rely on good contact of spreader plate with the top of the pipe, if air gap is present you'll have only half of the pipe surface transferring heat, and that into the chipboard - not the best heat conductor. Anyway, it is what it is now. Definitely! The boards seem to receive heat from the pipes, by adding extra insulation you limit the flow downwards - so the only way is going to be up, where you want it. As a bonus improvement of acoustic properties. Of course that will reduce what the kitchen receives, will that be a problem? What is the temperature limit for the surface, are you able to increase flow temperature in that room?
-
If the condition of old wool is ok, you'll save time money and itching if keeping it. There is something off with method you measure temperature, but the fact stays that you loose heat way to quick to maintain the temperature economically. How did you check? I think you should search for a free thermal camera rental/check (google spits plenty of charities doing that, you may be lucky to be close to one), that will give quick and definite answer.
-
Cost of airtightness retrofit?
Olf replied to anonymous's topic in Energy Efficient & Sustainable Design Concepts
Might as well be, but the question is if this is money well spent: completely sealed building will still loose energy if the walls conduct. Passivehouse will loose energy if you open all the windows. The most economical option is when conductive (through floor, walls, ceiling) and convective (draughts) losses are similar - so if you have budget of 1k, it may be that you attack the biggest holes, but spend the rest on loft or other areas. Not to mention that even if your own labour rate is nil, getting extra detail sorted out takes exponentially longer. Also some of the jobs have cost of disruption or require redecoration afterwards. And to finish, if you're too well sealed and do not have precautions (ventilation, preferably with heat recovery, but that is another cost), moisture and CO2 levels will climb up, and that can cause new problems... -
Cost of airtightness retrofit?
Olf replied to anonymous's topic in Energy Efficient & Sustainable Design Concepts
There is your answer: if the airtight tests (very good idea, will allow to make informed decisions! ) finds only specific holes/gaps/cracks, you may end up with spending 2 hours with £10 can of Illbruck. Or if the whole structure is one big sieve, multiple of £60 cans of blowerproof and goth decor 🤪 -
So after adding insulation you would be crawling... Would what you can reach from the hatch be enough? Rigid boards are ok to transfer load (compressive strength), but too fragile to support. You'd need to board under (over the joists, filling between the joists), so the boards are what holds you standing on PIR. Wool (Knauf) is going to be cheaper to buy and easier to lay (PIR is messy to cut), but in your case all begins with storage, so you need to sort that. Here I'd put PIR instead of Rocksilk: twice teh performance at the same thickness and zero risk of compressing when pushed. Check if the spotlights are fire rated, what type of bulb is installed (halogen or LED)? When wrapped in insulation they'll heat more. Also when refitting think about how to seal gaps around, as you've just mentioned that your ceiling is a sieve leaking warm air..
-
Yes, both those foams produce airtight barrier and stay flexible. You pay more than the usual do-it-all foam, but it is worth it, and the gaps do not take a lot to fill, so one can gets you far. Q is not stupid, some materials do react. PVC is what cables are wrapped in and what most windows are made of, and those foams are intended to be used there, so you should be safe. In any case, do double check your chosen product safety note. Gas pipe being steel will be fine.
-
Sorry about posting yourself @JohnMo, but this picture says it all!
-
IF the window is well fitted (big IF), then that would be cosmetic only and any strip the look you like will do it. But likely this is where spiders get inside (no joking, I had it) and you either foam it or fill with appropriate sealant. Illbruck and Soudal make dedicated products, Soudal SWS actually suggests foam, internal and extrenal sealant. If you go for foam, mask the area around as it likes to splash, expands, and then is b!tch to remove. Cover with strip (or at least filler or lick of paint) to protect foam from UV degradation. With sealant alone you can possibly get away with extra strip, though lose thermal insulating properties of foam.
-
That's the whole point: with large heat capacity of screed, there is a delay between floor surface getting to temperature and air above heating up. I for example have timer set to start heating at 4 am, at 7 it is ok, but peaks midday. Repeated daily. Boiler set to lower flow temperature will be more efficient, and even more so when runnning for longer periods. In other words your £200 will give you more heat than last month. What is your floor finish? You mentioned that the house keeps temperature once heated, so I'm worried that you're blocking the screed from releasing upwards and end up with heating soil below. Oh, that makes it for a prestige piece of paper to wipe whatever needs to be wiped. May or may not relate to actual thermal performance of the building
-
Search for 'stairs drawers', 27million hits, very popular way of using that space. I'll be doing this too at some stage.
-
No, the diameters are just dictated by the flow from each of the utilities and coincidentally in this case match the level of challenge to run them through the structure. But as belt and braces you could add AAV at the sink, that way the pipework can equalise pressure if necessary
-
If you mean ambient as room temperature, then if the walls are warmer, they actually are trying to heat the room. Though your 'heat gun' (or ratehr IR thermnometer) is fixed at specific emissivity, so may give wrong reading on some surfaces. Skeilings. Only plasterboard separates you precious (at current energy prices) heat inside and cold sky outside. And if eaves ventilation is done properly, then even better at sucking that warmth out. The most pragmatic solution is to measure how big gap between the board and felt is, subtract 20mm (ventilation gap), find suitable rigid insulation board and slide in. But that is a tricky attic exercise. Proper solution requires insulating also from inside. Saying that, skeiling area is not large in respect to the overall room surface, and if only 3'C lower that the rest, it should not be enough to make the house freezing. What is the readout on the ceiling? The problem is that some materials are permeable, also some services are not obvious routes of cold air ingress (I had conduits running from switches to the attic as well as massive holes above ceiling roses) Over last few weeks the air outside was regularly over 90% @ around 10'C, so baseline inside RH is stupidly high and on top of that we all breath, cook and shower.