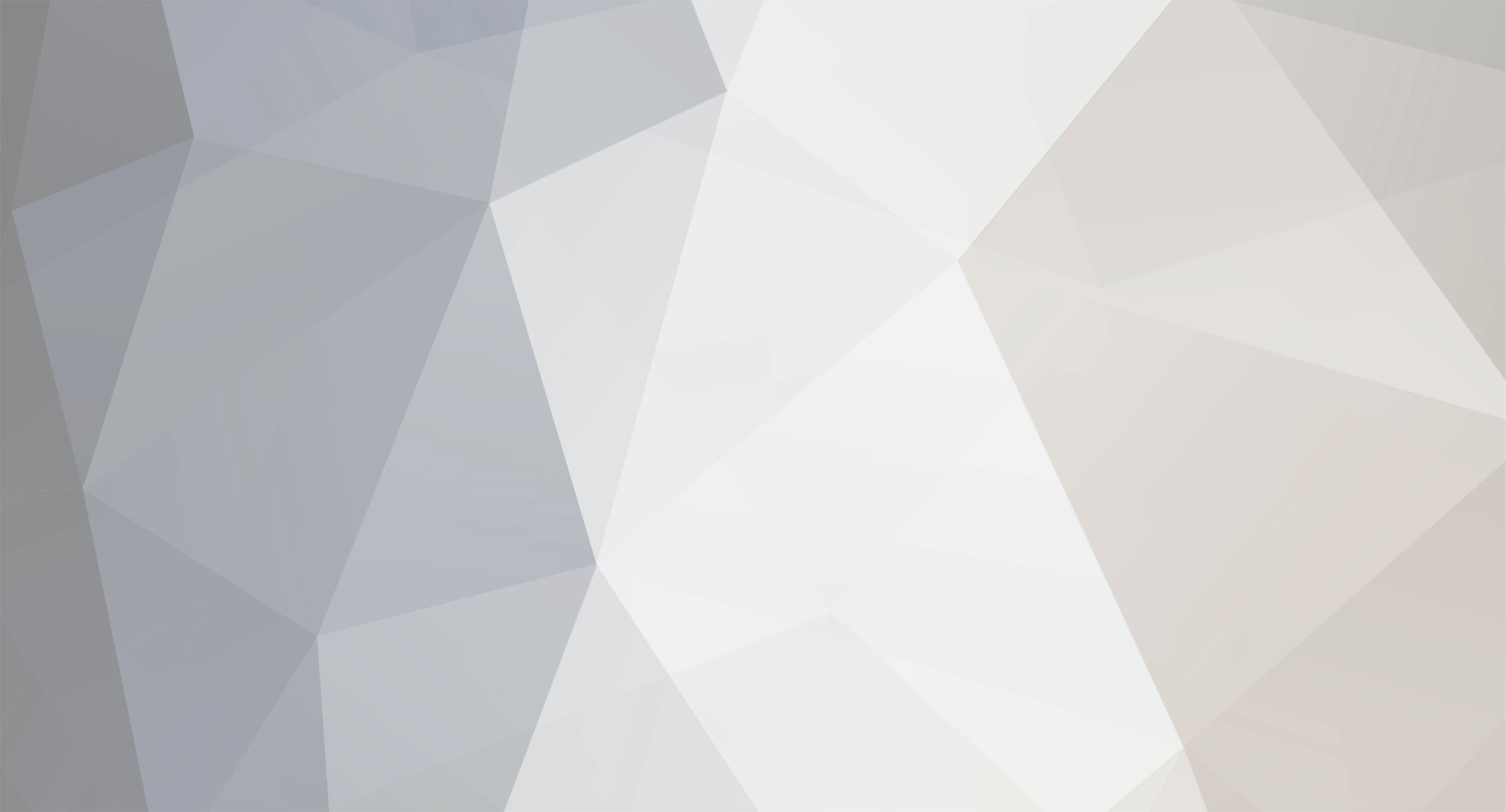
mvincentd
Members-
Posts
495 -
Joined
-
Last visited
-
Days Won
1
mvincentd last won the day on December 10 2019
mvincentd had the most liked content!
Personal Information
-
Location
North Dorset
Recent Profile Visitors
The recent visitors block is disabled and is not being shown to other users.
mvincentd's Achievements

Regular Member (4/5)
154
Reputation
-
http://2gomadindorset.blogspot.com/
-
Scroll to july 21 and 22 entries when floor is being poured. It worked, the pipes are ok, the system works well.........but make a point of being 'away' the day they pour yours if you go this route as the stress of watching them trample all over it is awful....they cannot with the best will in the world tread carefully while laying the slab. Despite success I would not reccomend this route unless like me circumstances forced it.
-
roofchart.pdf
-
Insulated Raft Slab Foundations - Finished Flooring
mvincentd replied to TBlew's topic in General Self Build & DIY Discussion
My power floated raft is my finished floor throughout my ground floor. The concerns being raised are all valid and it's good to be aware of them and know what you're getting into, but I believe they are all merely aesthetic. There's no reason why it won't work, but you need a shift in aesthetic sensibilities, and a pretty open mind to your precise outcome. The visual outcome of a powerfloat is a pretty individual thing dependent on numerous uncontrollable variables. Protecting that surface for the remainder of your build can have implications. Sealing powerfloat has problems associated with it, but (limited) solutions exist (look at Watco). I have one crack in 160sqm after 3.5 years, maybe 0.3mm at widest, I like it , whats the problem. I like the rust I sealed in from nails hanging around on the surface during the build, and the footprint. I'm ok with the steel baseplates and the protruding bolts on show, but it could have been avoided using the same principle as for a wetroom. I have 52 holes in the floor that have been grouted....from the bolts that supported soldiers holding wall shuttering up...there's no hiding them...so what. I appreciate 98% of people dont want a floor like this...but i didnt want to create a floor like 98% of peoples. -
Late reply, but for completeness of info....I sanded edges then overboarded with 9mm ply which then took a levelling compound, onto which Forbo Marmoleum (old fashioned lino) was glued. So, no comment re self levelling onto egger protect, sorry.
-
Brokers Adrian Flux found me some with Midas Crown.
-
I would choose to interpret that as meaning a road regardless of whether the road has a footpath alongside......so not pertaining to a path that hasn't got a road alongside....like yours. It's probably with drivers line of sight in mind. If you're lacking confidence to forge ahead then perhaps query it with your local highways officer rather than alert planning.
- 128 replies
-
- planning permission
- fence
-
(and 2 more)
Tagged with:
-
Manifold system versus hot return system
mvincentd replied to Russell griffiths's topic in General Plumbing
My supplier sold me this one, saying they'd had them apart and believed them to be rebadged but the same as the Grundfoss. https://www.bes.co.uk/dab-vs65-150b-bronze-hot-water-circulator-pump-21452/?ref=gs&gclid=Cj0KCQiAj9iBBhCJARIsAE9qRtD6d1psWN6bBJn8ra0KPJPrBvUf4JRHn2MjCK1I4kRZCa_UC_lYoEAaAjlnEALw_wcB -
Manifold system versus hot return system
mvincentd replied to Russell griffiths's topic in General Plumbing
I dont recall the rationale now but I was also lead to believe it needs to be a bronze and a rationale was given.... -
Phew, was hoping nod was taking the P... , didn't want to have to question his standards! I know nothing except what mine was like, I didnt have one square inch that rough.
-
The mortar between your blocks can suck water through like a sponge, as can the blocks to a lesser extent. This is the easy obvious explanation. For zero cosmetic change externally try a masonry cream, a step up in price from screw fix/everbuild/thompsons waterseal but you get what you pay for. http://www.stormdry.com If you can stand a cosmetic change externally http://www.renotex.co.uk/renotex_rollercoat.php I used this over failing render 4 years ago in economic preference at the time to replacing the render and it's still good.....quite a sticky mess to work with though.
-
What window style....velux and ideal combi for example which use compriband wouldn't want the compriband to bridge from frame to cavity closer, they'd want it to seal against outer leaf. Also what's your detail at the base....... I'd start by asking him to expand on this explanation, it might be that in your scenario he has a good point you should take on board. Do you currently understand the challenge of setting them back 100mm from the front leaf which is itself 100mm. I know in my scenario I definitely wouldn't want that....80mm fine. You've another window problem currently where you say "I can't work out if it is the architects plans which are wrong or it has been build incorrectly." I'd suggest adequate drawings would make this easy to establish....do bear in mind though the actual illustrated window section will likely be a generic representation so taking a ruler to your drawing to scale off it may be unsound.
-
Supporting stone above opening (parapet)
mvincentd replied to SuperPav's topic in General Construction Issues
-
Supporting stone above opening (parapet)
mvincentd replied to SuperPav's topic in General Construction Issues
Whats your wall construction....is the line drawing right? I'm thinking you've drawn the steel in line with the cavity, but wouldn't it be in line with the inner leaf blockwork? Whats the cavity tray arrangement above the window? So your 7m span is the window width anyway...or is it coincidentally 7m the other way too. Wouldn't you fit the window into a steel goalpost arrangement and run the joists the other way. The top post would have an additional plate welded to underside supporting the 'outer leaf' which in fact is just circa 400mm as you say. I dont know anything about how stone like that pictured is laid but if it was brick/block you'd surely just look to how it was done lower down...ie tying the 2 leafs with wire ties....so i'd imagine Hilti fixing some steel strap into the I-beam. I have broadly this scenario over a 6m wide window but with flint blocks circa 400 high rather than your stone. I imagine (slightly simplified description) the top capping in the photo being a continuation of the box gutter and so acting a bit like a horizontal hook to hold the top of the stone too. On pozis' i have some 6895's that are 147 x 279 @ 400 ctr's but they're supporting a green roof so i'd think you'd be ok finding a 7m pozi.