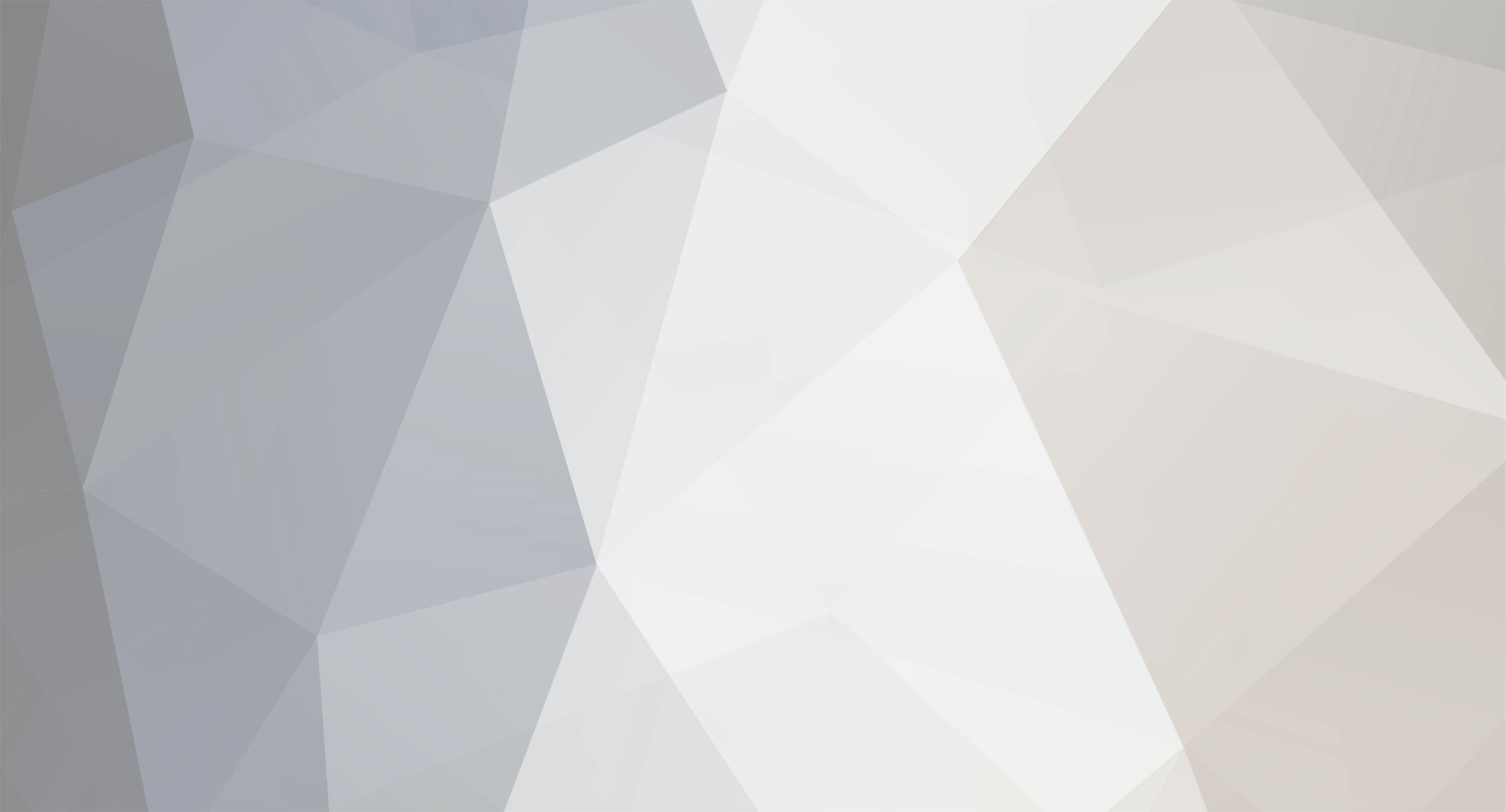
SuperPav
Members-
Posts
222 -
Joined
-
Last visited
Personal Information
-
Location
Cotswolds
Recent Profile Visitors
The recent visitors block is disabled and is not being shown to other users.
SuperPav's Achievements

Regular Member (4/5)
57
Reputation
-
MVHR and log burner
SuperPav replied to Tetrarch's topic in Mechanical Ventilation with Heat Recovery (MVHR)
As a counter to this discussion, and from someone in a very not-passivhaus house (but OK insulation!), we have MVHR, and a log burner. The log burner is in a room with a supply vent. I agree with all the above points about it defeating the purposes of an MVHR in a airtight house, but for us the MVHR is more than about heat recovery. It runs on the lowest setting, so is quiet, but it provides good background ventilation to closed habitable rooms, which (at least subjectively) means the air doesn't seem stale in any room (which can't be said for previous houses we've had) and even the completely enclosed tiny wetroom bathroom we've got dries out wonderfully. We also didn't want window trickle vents and lots of bathroom/kitchen extracts, so I'm still happy with the MVHR, even if it costs us money to run. Arguably we could've fitted a positive ventilation system for some of the above benefits but there really isn't that much in it in terms of cost (all was DIY'd, the MVHR unit was a good deal.) Probably further offset by the fact we have free wood to burn! Having said all that, if you're after optimal thermal performance, then lose the WBS. -
We've had a bit of a change of mind for the upstairs from carpet (original plan) to continuing the same engineered wood flooring as we have downstairs (14/3mm 600x600 versaille parquet panels with ~150mm borders). Downstairs these are getting glued onto concrete which is simple enough. Upstairs we have 22mm Egger Protect subfloors, which I'm pretty sure won't hold nails properly so I can't secret nail the engineered wood panels - can anybody confirm a suitable glue that would work directly onto Egger Protect? Unfortunately as the stairs and a few other thresholds are already in place, overboarding with ply would be a bit of a headache height wise so I'm trying to find a solution which works with the Egger Board. If absolutely not, I could overboard with 4mm ply and alter the thresholds and top stair nosing if that's the only way that would work.
-
So I've got a twintec water softener, bought it in great anticipation of finally not having to deal with hard water issues. Planned a place for it in the utility cupboard. Happy days. Completely missed the fact that it needs a waste/overflow/discharge! (DOH). Our water main comes into the utility cupboard downstairs, where the UVC, and all the manifolds for the whole house will be. It is in the centre of the ground floor, with no waste. The only "waste" pipe is a 28mm D2 copper pipe running along a wall to the outside to a gravel trap, put in place for the UVC. Is there any way I can utilise this 28mm pipe for the overflow and discharge of the twintec, while also using it downstream of the tundish/D2 for the UVC?
-
Got a picture?
-
We (well I say we, I mean she) decided that a Samsung Frame TV flush mounted on the wall is a better look than a "recessed" TV with a gap all around. Might be one to check with the boss before building walls?
-
PV plan and in-frame mounting options - am I going crazy?
SuperPav replied to SuperPav's topic in Photovoltaics (PV)
I have no existing inverter, it's a "ground up" install. Plan to stay within G98 regs using enphase microinverters via their Envoy controller to keep it at sub 3.68kW total. Looks like I'll need to go for the IQ7A's or IQ8's to avoid clipping, the price difference vs the IQ7 doesn't seem massive to be fair. -
PV plan and in-frame mounting options - am I going crazy?
SuperPav replied to SuperPav's topic in Photovoltaics (PV)
My garage feed is on a 50A MCB at the moment which having just had a look is indeed on a RCD on the main CU, which is indeed unnecessary I suppose as it could be rewired just straight off the main switch. Garage is fed by 16mm cable as it was sized to be big enough to feed a heat pump, two EV chargers (+ usual garage circuits), and be big enough to reverse-feed the house if we ever upgrade the supply to 3phase - the easiest way would be to run 3 phase to the garage and then split one phase off back to the main house for the domestic loads, as all the big stuff is in the garage. As I'll only ever be able to get an absolute max of approx 4kwp on the roof (to , I'd try and use as much as possible of it via immersion dumping or dumping into one of our two EV's if we ever have a surplus, just seems crazy to lose 30% of the capacity of the cells, maybe I'm overthinking it... I'll be honest I also don't quite understand how they can be rated to 400W DC and only 300kVA AC - what's the point of the 400W DC rating in that case? -
Should I be filling this before tiling?
SuperPav replied to Tom's topic in General Self Build & DIY Discussion
Are you tiling directly onto the concrete block? without backerboard or anything? Wish my newly built walls were straight enough for that!! If the tile edge doesn't meet over the chase, you can probably just bridge it (depending on the tile!), I'd personally probably fill it in (even if just squirty foam and then trim it flush), but I'd be putting backerboard over my walls anyway so that would hide any chases. -
Welcome Carl! I'm about to almost exactly the same thing project from a planning and design point of view for a friend, so look forward to seeing your plans. Thankfully I won't be involved in any of the actual building work on this one!
-
So looking to get some PV onto the roof as we hopefully complete the never-ending project this year. I have a sloped roof (35 deg, south-ish) on the garage which is approx 4.2x3.6m of surface, and next to it a flat roof about 7.5m long, so I was planning on getting 10 panels up there, to give me around 4kw of peak theoretical generation, capped at whatever the G98 limit is.. I was planning on the following layout: 6 in landscape 3 rows x 2 columns on the pitched roof in in-roof frames (roof isn't slated yet) 4 in landscape along the flat roof in renusol ballast buckets (world's biggest rip-off from what I can tell given they cost as much as the panels!) However, all the reasonably priced panels I can find (£80 or so for 405-410Wp) are like 1700x1130 size, and I cannot for hte life of me find any compatible landscape GSE in-frame options! Do I just need to get smaller/more expensive panels to fit with their tiny frames (1600x1000 ish). What am I doing wrong? If I can't get them in 3x2 landscape on that roof, I'll need to reduce the number of panels to 4 in line, as I can't quite get 2 in portrait to fit along the roof slope on top of one another. I was also planning on going for micro-inverters as we might have some partial shading due to neighbours trees during some parts of the year, but the enphase IQ7+ ones I look at have a peak output of 295kVA - does that mean I'm losing up to 30% of the panels output by going for microinverters? if that's the case, am I not better off just getting a string inverter and taking the 30% hit on partial shading? All will be DIY'd with the sparky hooking everything up, I will stick a junction box on the flat roof for everything to run into which will then run back to the garage CU.
-
Probably not depending on which flashing you have (the flexi-bendy ones with straight sides are a bit more flexible in terms of installation), but you can usually adapt virtually any velux flashing kit by making your own flashings/soakers out of lead as required. What I will say though, is that's unlikely to be much (or at all) cheaper than just getting a replacement correct flashing kit from Velux...
-
Mainly because if I got a 12kW heat pump with cylinder for £6k, even with the £1.5k paperwork fee, I'd get it all covered with £7500 BUS monies. If I buy it myself, without it, it would cost me £5k net of VAT, which I cannot reclaim. Re requirement to be fully built, I was under the impression having read the requirements is that the system would need to be commissioned before the grant is paid, but I don't know how you commission it when the upstairs hasn't got any rooms/rads yet?
-
If you've not done it yet (we're in the same boat as you, holding out till the house is built enough to be able to go through BUS, while shivering with a 3kW willis and a 12kW shower), we're considering using these guys as they'll do the sign off and MCS paperwork for the BUS. I've been in touch and essentially they want £1.5k for the privilege, but if that gets you £7.5k it's still not a bad deal if you can DIY it. I've also got the advantage of being able to buy/supply the ASHP and install it via my ltd co (i'd still be doing it!) thereby getting the VAT back, which in itself is worth £1k or so.. https://www.unitherm.co.uk/pages/mcs-design
-
Daikin Alitherm hybrid without the boiler?
SuperPav replied to SuperPav's topic in Air Source Heat Pumps (ASHP)
Thanks everyone for the opinions and suggestions. Following the (fairly obvious) mention of having a look through the technical docs, I've gone through the installation manual for the Altherm hybrid ASP, and it can be configured to block the boiler and exclusively use the ASHP down to -14 with a bottom plate heater (£40 on ebay), or -5 without the bottom plate heater. I think based on that I might try and give it a go if the unit is still available for £500... I've got a circ pump that came with my UFH manifold (which would be ~1m from where the ASHP is going, so should be fine), so that's not a problem. Re: A2A ASHP, yes if I hadn't already put the loops in the slab that's what I'd be doing, but as the UFH is in and a garage will always have fairly rubbish airtightness due to the main door, I figured putting the heat into the concrete slab is better than A2A. but A2A would be a better fallback than a new £2k unit. The dream units look interesting but for the price still a expensive especially given I can't see any proper way to control them using a thermostat to call for heat without starting to rig 3rd party control systems etc. -
Daikin Alitherm hybrid without the boiler?
SuperPav replied to SuperPav's topic in Air Source Heat Pumps (ASHP)
I don't - it's on FB marketplace I think so will need to dig it out on my phone, but it was this unit (with this model code) - EJHA04AAV3, along with some flexi hoses and the controller/thermostat unit, https://www.cityplumbing.co.uk/p/daikin-altherma-hybrid-hydrosplit-4kw-heat-pump-outdoor-unit-ejha04aav3/p/478567 and this is the Daikin manual for the hybrid system: https://www.daikin.eu/content/dam/document-library/catalogues/heat/hybrid-heat-pump/ejha-av3/Daikin Altherma H Hybrid_Product catalogue_ECPEN20-731_English.pdf: