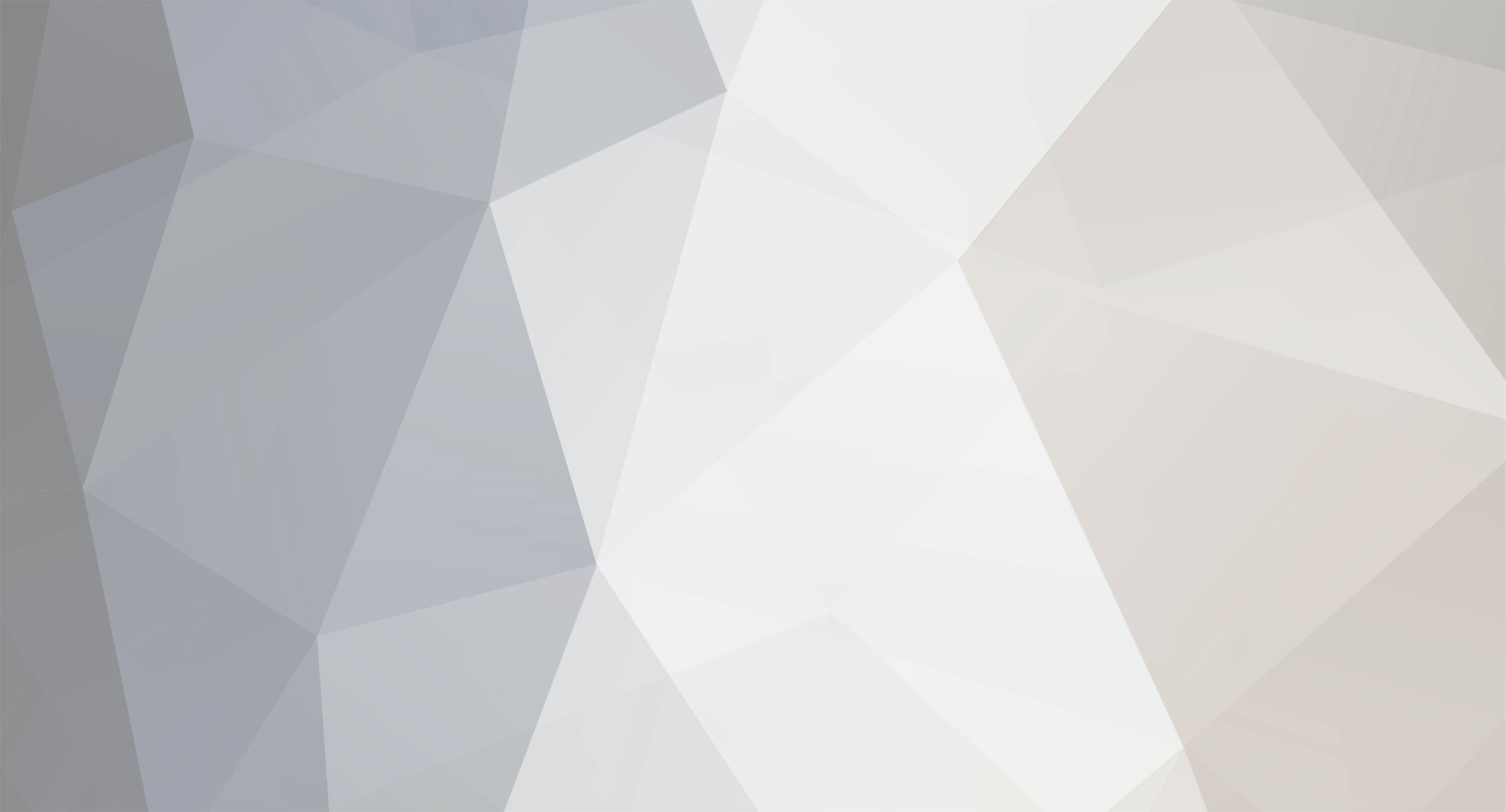
PeterTweeter
Members-
Posts
30 -
Joined
-
Last visited
Everything posted by PeterTweeter
-
@MikeSharp01 Hi, I'm responding to your post because I think I'll be facing the same issue - having fallen down on the side of an external layer of insulation. I'm not sure I'm any the wiser regarding the solution @markocosic showed. However, I came across this document - published by Rockwool North America, that may be of some help. Search for "Rockwool cladding & support details". I haven't read it in detail, but it might be useful. A crucial problem for you is the loading - Rockwool would, I'm sure, regard tile hanging as "heavy". One route to support are "big buggerrr" lag screws ie mushroom head bolts like these https://www.toolstation.com/forgefast-construction-screw/p55793?searchstr=construction%20screw. Hope this helps P
-
BTW - which forest is going to yield an 8m+ lump of straight oak? Unless, of course there is a join!! Even more of a deep intake of breath. Go for the DF - just saying.
-
That's not a house truss - more like a bridge truss!! Seriously, the pitch is c30deg, quite shallow for a king post truss. Typically, I have built redwood trusses like these, but the pitch is 9/10, ie 42deg. Your SE is having a laugh, the deflection would be something else. I would go with PeterW's suggestion & go for douggie fir & something like a Howe truss - much more like a bridge truss, cos 8m is a stretch! The truss builders quoted will have a much better handle on the shape/material - trust them. Cheers
-
Cheaper options for bespoke Crittall-style interior doors?
PeterTweeter replied to jack's topic in Doors & Door Frames
Jack The good news is that Crittal themselves developed the steel sections & these are available commercially. Enterprising artisans are now offering bespoke units using these very sections. The sections are W20; W30 & W40. You can actually get them from China via Aliexpress - just saying. -
Joe This is why old-school septic tanks work well (if they're not cracked). The one we replaced by modern techology had NEVER been emptied!
-
BTW The compressors used usually aerate fish ponds - they don't shift the liquor, merely make the bubbles (just like the Aero advert!). The movement between chambers is effected by the incoming effluent.
-
Hi In our last house we installed a Platinum Mini - an early type of treatment plant. The 3 stages were: solid separation - literally the heavy stuff dropping to the bottom; aeration - where the liquor is encouraged to further refine & the last stage did something else (not entirely sure what, now); the overflow then trickling over to the porous drainage set-up. In all our time, the tank was desludged maybe twice; it was never an issue (yes, you can dip for the sludge level). The secret is the nose test - if it smells sweet, then everything is Ok. Any "off smell" is a problem. The aerator can, at a pinch, be offline for a week or more. Our usual tanker driver used to travel all over the country - can't think why - but was a good source of advice. So, bottom line is/was - desludging was an "as required" job.
-
-
Kevin Thanks for the info. As a matter of fact, it was @ the NSBRC Swindon that we saw the Tata product. We also made contact with Fleming & found out that our 1st build was supplied by Celtic Homes - an early incarnation of Fleming. Simon I've just fallen off my chair - Festool, indeed! Maybe I could slip that past my paymaster! Curious about the "cross cut rail" - must investigate. I'm glad it's not just me with an Erbauer impact driver. Sadly, mine has just died on me - not the batteries, but the switch. Haven't bothered to search for a new one - just replaced it with an Einfell. Right, just a brand tart! Tho I have decided to go down the multi tool/single battery route & added a combi drill & a multitool. TS were doing a cracking deal - now I've got spare chargers coming out of everywhere. I have to say that a multitool is one of the best tools I've ever owned. It makes short work of the job of cutting out a hole in old lath & plaster, for a new socket box. Buzzing away with two of the blades to ease away the plaster & then the underlying laths; slip in a deep drylining box & we're done! Cheers
-
Joining timber framed extension to existing brickwork
PeterTweeter replied to SeanDean's topic in Timber Frame
Sean My mistake - I see this IS that earlier post. Duh!- 4 replies
-
- timber frame
- brickwork
-
(and 4 more)
Tagged with:
-
Joining timber framed extension to existing brickwork
PeterTweeter replied to SeanDean's topic in Timber Frame
Sean I believe you posted this same question some time ago & got no takers then. Since we 're all in the same boat, I'll add my tuppence worth! I will be having the same issue, connecting my TF extension to a 120 year old Victorian brick corner. As I see it, there are 2 issues: 1) movement - the masonry is not going anywhere ( the Germans had a go when they bombed the factory across the road & slightly cracked some lintels & moved an older add-on, but I digress) & 2) weather tightness. In a conversation i had once with a builder of oak framed buildings, he alluded to a system he'd developed but wouldn't divulge - for obvious reasons. So, my inner-engineer got to thinking that it's a bit more than bolts, resin & great wodges of butyl filler. Tho I havent firmed up on this, my approach would be: resin anchors; slotted holes in the timber; something like comprimat in 2 strips @ the outer edges of the stud; all made weathertight by liberal application of a butyl-type filler. So, the join will be watertight & shrinkage will be accomodated. Hope that helps & after you!!- 4 replies
-
- timber frame
- brickwork
-
(and 4 more)
Tagged with:
-
Simon. If you're happy to share - I'd appreciate a steer to the local timber suppliers. James. Also kudos! I shall frame those images because the look youv'e achieved is exactly what is in my mind (& on scraps of paper!) When my wife asks "why are you/we doing this?" - I'll point to your example! On a serious note - glazing is on my mind, at the minute - yours look the business, can I ask the manufacturer/supplier/fitter? WRT roofing - not that I've delved too deep, but when we were first talking about this project we came across Colorcoat Urban. It seemed the dogs danglies but I've gotten the impression from other buildhubbers ( is that the collective noun?) - that Tata are/were none too reliable. At the moment, I'm leaning towards these candidates - FalZip; VieoZinc & Greencoat (as Simon has used). WRT boys toys - James, I note your 'workshop space' - I need to review my kit in order to proceed. I have an older 10in Axminster compound saw (w. dodgy detents, so accurate crosscuts are an issue); a Makita track saw; a 10in Dewalt radial arm saw & a very old 8in B&D circular saw. You may mock, but she has served me very well since 1969 & many house builds/refurbs/roof framing projects, so she won't be retired - merely supplemented with something, maybe. The Dewalt compound saw in the photo - any thoughts? Also the chunky table saw - I've never been able to justify the need (mainly space). So, my thoughts are: a better/bigger compound saw - deeper cuts? & a 12in circular saw - also deeper cuts. Any other thoughts/suggestions? Many thanks.
-
Glass gable ends. Looking for examples..
PeterTweeter replied to Olly P's topic in General Self Build & DIY Discussion
My apologies for butting into this thread - but gable end glazing is very much on my mind & this thread popped up. Olly P Kudos - a bloody great hole without, apparently, knowing quite how to fill it! I'm sure you had a cunning plan. I have a hole (on paper) that I'm trying to get a handle on how/who to glaze it. I'm in the early research stages & these system suppliers surface: AluK; Origin & Sieger. I note that BMBifoldingdoors has been referenced in the thread - so worth a punt. So, could you share any thoughts on who supplied your glazing & maybe any pointers to alternatives? The same question is directed towards other contributors - I need all the advice I can get! Cheers -
Simon - thanks for that, you make some good points. I'm doing the design myself so I'm beginning to get to grips with the issues of adequate support. Interesting point about window fixing, we shall see! I am in awe of you, having seen shots of your roof & your videos! I'm fully expecting to have to go down the DIY route for our roof - I note your choice of Greencoat. Ideally, we would like zinc but will probably go down the "look-a-like" route for cost/contractor reasons. Re. your comments about 140cls - I was speaking to Griggs Timber yesterday & was told that the US are hoovering up European supplies, at over the odds, cos Canada can't meet demand. Your point re sheathing - always a bugger when you're doing a bit of work & realised that it's an imperial sheet - had that trouble with the buffalo board to my workshop!
-
Reinforced joists for cast iron bath weight?
PeterTweeter replied to ashthekid's topic in Timber Frame
At least these strengthen the single bolt. From the underside, I can see the 2x's are forming a support platform - not very elegant but ok. BTW are you paying your chippies/SE by the cube of timber used? FTW I would still look to further reinforcing the O/B ends of the joists. -
Reinforced joists for cast iron bath weight?
PeterTweeter replied to ashthekid's topic in Timber Frame
If this is a cantileverd structure then the bolts would be redundant surely - nails would be sufficient. The OP needs to better describe the stucture. -
Reinforced joists for cast iron bath weight?
PeterTweeter replied to ashthekid's topic in Timber Frame
Well, I don't think much of your SE - IMHO. Those joists are pretty meaty, so there's a lot going on out of shot. This is a scenario seen with old school ballon framing, in which studs rose from sole plate to roof plate. For intermediate joists, a bearing support is housed into the studs to take the floor load. No way should those joists be relying on a single bolt into a stud that is not braced. Whilst not up to speed on bolting schedules - my inner engineer would use a pair of bolts spaced thirds across the stud & 50mm from top/bottom face. Those infill pieces look to be lumps of joist toe-nailed into the principal joists. All these will do is brace the joists & not add any dead/live load capability. To remedy your dilemma, I would rip them out & turn them vertical & attach with joist hangers. As to better support of the joists, if you are able, look to install a bearer below them & use something like simpson structural screws to attach to the studs. Then reinforce the studs with noggins between screwed to this bearer. As a young engineer, I was counselled by our structual tutor "If it looks right, it probably is right". In your case, you need to see that those joists are well supported; the studs braced & this extra load supported. I know, "much better informed - still none the wiser!" Hope this helps. -
Gus Make no mistake, for all the reasons you make, I will be building this myself, tho 'her indoors' keeps saying I/we are not 20 somethings anymore! I'm well aware of the long standing scottish association with TH - the house we built in the mid70's was a package supplied by Celtic Homes, based in Duns. You, and others, may know their current incarnation - Fleming Homes. My real interest is taking up some /all of these new ideas in reducing timber usage & boosting insulation
-
The alternative is a dedicated metal connector nailer @ 5-10x the cost - you choose, tho I take the point re H&S. That said, I may rethink my plan depending on how I will be supporting the I beam roof. Current thoughts eliminate hangers.
-
There you go - as long as you've got enough oomph in your compressor, they take a lot of air.
-
Russell I'm afraid I can't agree with your assessment - just a walk away from us, a developer is throwing up an estate - part bricks & mortar & some TF. From what I can see the framing is just like we erected in the mid 70's. The only difference I can see are the more sophisticated membranes & sealing tapes, which is what you'd expect on the science front. As for double stud walls - wasn't John Larsen advocating a similar approach in Ontario in the 80's. MBC were a bit late in the game. That said, I notice you're based in Gloucestershire, so maybe you could direct me to a reliable source of timber in our area. In addition, I've also noticed your input in regard to metal roofing. This is the route I'm taking but finding an installer hard to locate - let alone deciding on the system. How did you find this & making the decisions? Peter
-
We have some TF buidings going up just a short walk from us. These are for social housing by a developer. You can see the poor quality & shoddy workmanship here just like in the US. That said, the TF house my wife & I built in the mid 70's is still standing!!
-
When I get going, I will be stick building with air power - to my mind it's the only way to go - more reliable &cheaper. I shall be beefing up my nailing effort with a Makita 924 & said palm nailer. Normally, I would look to the US to get this kind of kit (Hitachi/Hikoki & Milwaukee) but the Makit comes close & would be UK sourced.
-
Hi, there I've been spending a while getting myself up to speed on framing techniques for the 21st century. My previous experience was based on publications from the British Columbria Timber Frame Housing Group, dated mid 70's! Clearly, a lot has changed & I've been reading up on the moves to AFT in North America. I see the a basic item (2x6 stud @600crs) has been adopted here as a standard, but I'm wondering if any of the other items have made an appearance over here? These include: the elimination of jack studs & cripples; 2 stud (California) corners; single top plate; rim joists doubling for headers; etc. All of this is in order to reduce cald bridging & increase insulation. Has anyone out there come across these? Either from experience or knowledge. Cheers, Peter