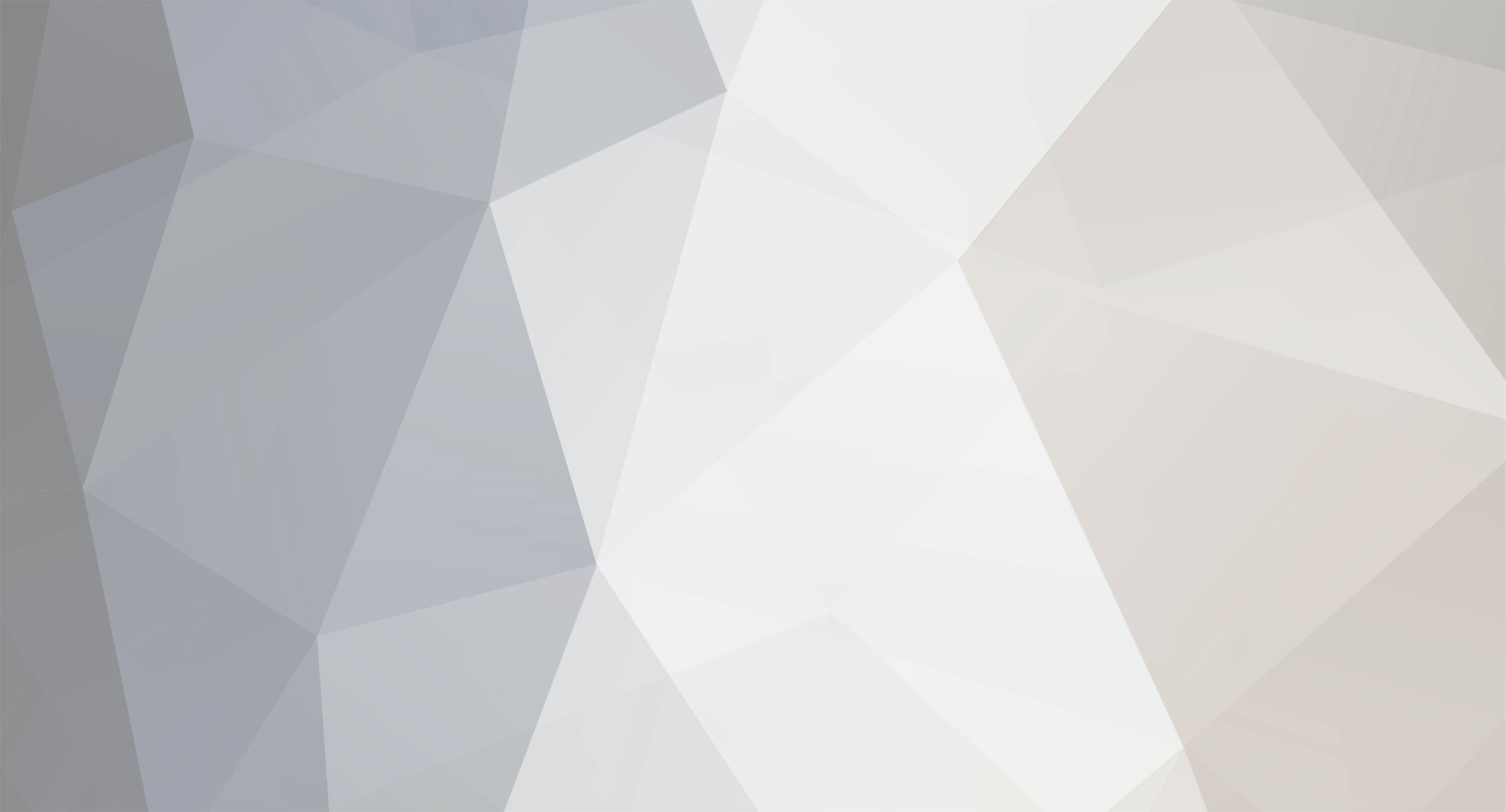
Olly P
Members-
Posts
117 -
Joined
-
Last visited
Recent Profile Visitors
1879 profile views
Olly P's Achievements

Regular Member (4/5)
44
Reputation
-
We've just moved in our 450sqm dormer bungalow which has cost us £325k with the VAT to be reclaimed on the materials ( we think around £30-£40k to come back). We did get the bulk materials before the price increases and I did loads of the work myself, foundations, laboured on brickys, fitted all insulation, wired and plumbed and plasterboarded most of it, fitted mvhr, decorated, fitted the kitchens and bathrooms etc etc etc. I went part time at work to do this. Its still possible to build under £1k per sqm but you've gotta out the graft in!
-
We have 2 Vent axia MVHR units, one GF one 1st floor. I have installed the systems myself and it is up and running however it has not been balanced. I would prefer to do this myself as then, if any changes need to be made in the future then it's easy for me to do and not have to get someone out to it. Has anyone done this and also where do you get a suitable anemometer from?
-
For that size of paddock a westwood or countax would do the job well. Mine has cut very long grass you just need to go slow then cut every week or two to keep it tidy. I would recommend getting a newish one with hydrostatic drive.
-
Thanks for the advise so far. Yes it could be the case I'm maybe expecting too much and the steam did clear in the end. I will order an anemometer tonight and see what's actually happening. It's just strange that the supplying terminals are supplying lots of air yet the extracting ones arent performing the same.
-
Hi all We have installed vent axia sentinel kinetic plus MVHR. 2 units, 1 upstairs, 1 downstairs. Circa 450 Sqm dormer bungalow. The systems were designed and supplied by BPC and I installed them myself. We are nearing completion on the build and I have had the ground floor MVHR running for a few weeks. I have not commissioned the system yet as I'm yet to get hold of an anemometer but i have set all terminals at 2 turns out. My issue is that when I run a hot shower or create steam in the kitchen by boiling some water the extraction is very poor, even on boost . But the supply to the rooms is very good and you can hear/feel the air being supplied into the rooms. I've altered the boost extract setting to 100% and its still not great. I've cleaned the filters and checked all the ducting all seems good and airtight. Any ideas? I was expecting the same performance as a conventional extractor fan but this is nowhere near that. I am expecting too much?? I have the ducting set up as per the vent axia installation manual but I would like to see if anyone could upload a picture of there vent axia system to confirm I have the ducting correct
-
What glue did you use to fix the decoupler mat to the screed? I have about 200sqm to do. And also, the boiler is installed but not fired yet as there is no rads coupled up yet, the screed is call retinol and went down semi dry (it is sand and cement with an additive and fibres). I've sheeted the screed from day one so as no plaster or drywall paint etc would contaminate it, hopefully making my job slightly easier. Do I need to prep the floor in any other way before I start?
-
Glass gable ends. Looking for examples..
Olly P replied to Olly P's topic in General Self Build & DIY Discussion
-
Glass gable ends. Looking for examples..
Olly P replied to Olly P's topic in General Self Build & DIY Discussion
See below. I used a local upvc trade supplier who I bought the alu doors and glazing off. The 2x sliding doors and glazing cost around £8k in total. -
Glass gable ends. Looking for examples..
Olly P replied to Olly P's topic in General Self Build & DIY Discussion
That looks really good. The horizontal beam at 1st floor level, the top of the steel needs to sit flush with the 1st floor so you can sit the glazing or door frame etc onto it. As the steel beam was smaller than the floor joists I built stud work underneath with insulation and a membrane to fix the top rail of the downstairs sliding doors to ( the downstairs doors are 2.4m high). Then I finished the outside with a 400mm fascia board that tucked behind the upstairs doors cill and used some soffit board between the fascia bottom and the downstairs doors. Hope that makes sense! I got all the Ali trims from factory that made the doors and glazing so they were all the same RAL. -
Glass gable ends. Looking for examples..
Olly P replied to Olly P's topic in General Self Build & DIY Discussion
Hi all sorry for the late reply. I fabricated the steelwork on site myself as I found it too difficult to get the frame measurements mm perfect. All steel work is 152 152 I beams and I insulated them with PIR on the inside. Essentially it is 2 sets of sliding doors with two triangular pieces of glazing above. I fitted a 70mm box section between the upper sliding doors and the triangular glazing ( filled the box section with PIR) to stop any wind deflection- works well. When designing the steelwork frames the best advise I can give is to think about every stage. Think about the timber rafter sizes, where the steel ridge will land and the connection specified, what size insulated plasterboard will be fitted and where the soffit will finish on the outside. I couldn't be 100% sure of all of this so I built the frame onsite in stages I.e posts out of the ground then horizontal in at 1st floor level then when blockwork complete the apex above. -
Glass gable ends. Looking for examples..
Olly P replied to Olly P's topic in General Self Build & DIY Discussion