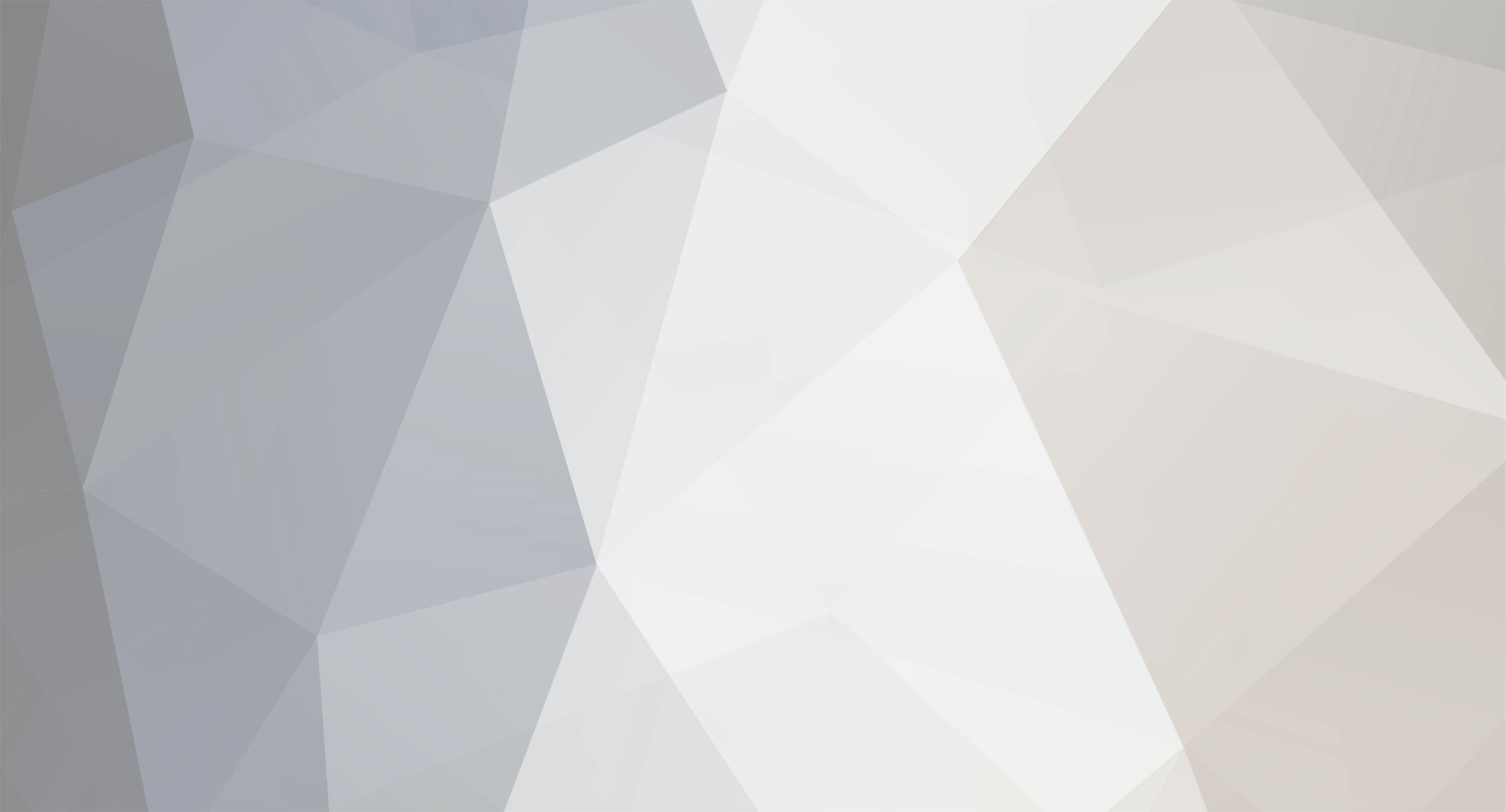
najem-icf
Members-
Posts
20 -
Joined
-
Last visited
Everything posted by najem-icf
-
pro's & cons of different ICF systems
najem-icf replied to mvincentd's topic in Insulated Concrete Formwork (ICF)
I doubt the risk of concrete burning off the foil is something that will happen in the short term - so I guess we will just have to "watch this space" - I have asked the a colleague who works in the Built Environment section of a University here to see if he can assist me with determining the longer term effects of this kind of scenario. If nothing else, it is an interesting topic. Oh gosh - I strongly disagree with you here. EPS with FRA has an ignition point of 360°C. Prior to this EPS will melt at source but will not spread flame. There are numerous tests that have been conducted that have confirmed this. If the EPS perishes, you have a monolithic wall of concrete with no breaks in it to facilitate the spread of flame. The foam products of yesteryear (mainly ceiling tiles in kitchens) have long since ceased existence. All ICF EPS/XPS now use Polymeric Fire Retardants as it became illegal in North America to use HBCD. As we know, North America is the worlds biggest ICF market. EPS is 98% air. PUR on the other hand is a known flammable product, decomposition from fire can produce significant amounts of carbon monoxide and hydrogen cyanide.(<- straight out of wikipedia!) Grenfell is a prime example of what PUR/PIR insulation can do. The internet is littered with examples of PUR/PIR fires. Have a look at this: and this: -
Creating a fall on a flat roof: and attaching the wall plate for it
najem-icf replied to ToughButterCup's topic in Flat Roofs
Why not use tilt firrings? Most timber merchants do them - they will give you the fall you are looking for without the need to install your posi's at an angle. Water will run no problem at a gradient shallower than 1:40. There doesn't seem to be a large span there so you could achieve this without great difficulty. Alternatively, ask the posijoist manufacturer what angle you can go to (that's if you have already had them made) - they are engineered joists and the webs are calculated according to the stresses based on their proposed installation. As such, if they are installed at an angle, they could cause stresses not factored and the webs could potentially fail. Not saying that *will* happen - but the potential worst case scenario. For the roof covering, I would recommend using Firestone Rubbercover - I have used it several times now and never had any issues with it. It is a single ply membrane and is flexible enough to accommodate expansion and contraction without compromising the integrity of the membrane. I have attached a photograph of one I did some years ago for my brother. Hope this helps. -
pro's & cons of different ICF systems
najem-icf replied to mvincentd's topic in Insulated Concrete Formwork (ICF)
I had a look at some of the old Ballytherm, Kingspan and Celotex stuff we had laying around and they all seem to have an aluminium coating of sorts. Some are admittedly thinner than others - Celotex especially seems to have a very very thin veil of foil on a backing product - it does look like paper to be fair. @JSHarris have you managed to do some conclusive testing yet? I am now wondering if the reason not to have the concrete come into contact with foil faced insulation is more to do with its reaction with the dummy foil. I still maintain that it is not a good idea to have concrete come into contact with the board at all due to the uncertainties. I prefer to play it safe than to take the risk - a roll of polythene will set you back around £20 for 100m² - hardly breaking the bank and would at least give peace of mind in case the scaremongering is true. The Celotex announcement came as no surprise - people in the industry have been saying it for years. In North America, they refer to PIR/PUR insulation as pure gasoline. Fire crews are told that if a building they are attending an incident at contains PIR/PUR insulation, get everyone out and just wait until it finishes. Almost on a daily basis there is a stick frame building on fire in the US. Also heard that PIR/PUR insulation is going up again in price in October... -
pro's & cons of different ICF systems
najem-icf replied to mvincentd's topic in Insulated Concrete Formwork (ICF)
That's fair enough. I must admit I have taken the BBA and the manufacturers word on the composition of the products. Hopefully your testing can confirm otherwise and give us all invaluable knowledge. I do appreciate you guidance. I guess when you believe your views to be well informed and without doubt correct, there is a tendency to become a little too passionate and precious about things. You are right - stuff just got real! Looking forward to @JSHarris findings... -
pro's & cons of different ICF systems
najem-icf replied to mvincentd's topic in Insulated Concrete Formwork (ICF)
*sigh* See attached BBA for Cavity Wall Full Fill. Technical Specification 1 Description Celotex CF5000 PIR Insulation for Full Fill Cavity Walls comprises foil-faced rigid polyisocyanurate (PIR) foam board with aluminium foil-facings with the nominal characteristics given in Table 1 of this Certificate. cavity-wall-full-fill_bba-certificate_mar17.pdf -
pro's & cons of different ICF systems
najem-icf replied to mvincentd's topic in Insulated Concrete Formwork (ICF)
@Russell griffiths a friend of mine is a carpet fitter - yet has no carpets in his own house - so I totally get that... When I was in IT, last thing I wanted to do was fix my own computer issues... -
pro's & cons of different ICF systems
najem-icf replied to mvincentd's topic in Insulated Concrete Formwork (ICF)
@Russell griffithsNajem is my first name and my preferred method of construction is ICF. It's what I have the most knowledge about. -
pro's & cons of different ICF systems
najem-icf replied to mvincentd's topic in Insulated Concrete Formwork (ICF)
Sorry @jamiehamy - Durisol was named by a previous poster and they asked about pros and cons of different ICF systems. The detailed discussion on Durisol has been carried by various replies, not just myself. I don't have an agenda other than to inform people of my own experiences and knowledge. Inevitably each of us has likes, dislikes and extreme opinions about every aspect of life. -
That blog is awesome! Wish more people did that... Are you doing a regular blower test @JSHarris? I would be curious to see the results - it would be a good advert for MBC if they have solved the issues most stick builds face.
-
pro's & cons of different ICF systems
najem-icf replied to mvincentd's topic in Insulated Concrete Formwork (ICF)
Awesome :-) A guy I know who was at the coalface told me differently. Are you saying you experienced zero crumbling of the block in the rain? When I first looked at ICF, I looked at their biggest market in the world - North America - and I saw what they use there. Went to the World of Concrete Conference in Las Vegas. Lots of ICFs there, predominantly EPS based ones. Durisol wasn't there. It isn't very widely used in North America at all. -
pro's & cons of different ICF systems
najem-icf replied to mvincentd's topic in Insulated Concrete Formwork (ICF)
From what I read in the article, that stuff was treated. I was a treehugger - but given that we are consuming more lumber than we are planting (http://www.globalforestwatch.org/) and the harm we are doing as we prepare timber for use in construction, as well as the damage to the environment caused by producing additional material sued in wood construction. I'm confuddled now... Are you saying your statement that it is irrelevant if foil is intact or not is correct despite what BBA certs and manufacturers say about the importance of keeping the foil intact? Well here's the actual answer: The reaction of Aluminum with fresh concrete 3 parts Calcium Hydroxide + 2 parts Aluminum 3 Ca(OH)2 + 2 Al -> 3 Ca3Al2O6 + 3 H2 3 parts TriCalcium Aluminate + 3 parts Hydrogen 3Ca+ 6OH- + 2 Al -> 3 Ca3Al2O6 + 3 H2 Within the first 24 hours In a flooring scenario, it would only be a concern where there are loads coming down on the areas affected - generally unlikely. However, in a vertical application, like Durisol, it is impacting on the walls where you are transferring significant loads. you are right that you would need the bubbles to move horizontally, however that is relying on reactions to be uniform across the board. Not to mention that the insulation itself is not doing what it is supposed to. Oh - and you have an air permeable product that links the outside world to in... My test is always - leave the product you want to build with out in the rain for a few weeks - if it is still as new, then use it. If not, then why would you want to put your loved ones into an envelope structure made of something that can't even sustain a few weeks of our wonderful weather? -
pro's & cons of different ICF systems
najem-icf replied to mvincentd's topic in Insulated Concrete Formwork (ICF)
Correct re edges not being sealed - precisely why the BBA Cert and manufacturers installation instructions state that foil tale must be used where two boards join. Ask any builders merchant if they (a) stock it and/or (b) have sold any. The answer is usually no to both. Hence the poor quality of UK housing stock. -
pro's & cons of different ICF systems
najem-icf replied to mvincentd's topic in Insulated Concrete Formwork (ICF)
Point I was trying to make is that regardless of how you treat an organic product, it will still eventually attract vermin... Ah - no - that's not quite right sir. The foil on the PUR/PIR boards is aluminium based, and it will burn off if in direct contact with concrete. Fresh concrete corrodes aluminum with subsequent release of hydrogen. After the chemical reaction, the concrete loses its properties and deteriorates. The concrete is no longer homogenous. Significant testing has been done Stateside that confirms this. This is before we even consider the reaction between concrete and PUR/PIR as well as Hydrogen - usually results in air bubbles in the concrete. If those air bubbles form near rebar, you end up with corrosion. There is a reason every single BBA for PUR/PIR foil faced boards say the same thing - cement must never come into contact with the foil - a polythene sheet must be placed between the foil and the concrete. I have an e-mail from Celotex and Kingspan that differ with your view that "there isn't an issue with pouring concrete on foil faced insulation." I would much rather follow the BBA certificate and the manufacturers installation instructions sir. True - you are correct in the handling and reflection aspect, however it is also to keep gasses from escaping. PUR/PIR off-gas. You could potentially face the same issue with any other method of construction - stick build - you could catch the end of the timber *only just* - or with masonry - you could be drilling into weak mortar. IMHO - yup Usually you will be able to feel or detect screws fixing the plasterboard back to the strips - use this as your datum... Hope this helps - absolutely enjoying discussion like this - is that sad on my part? -
I had a very detailed discussion with Kingspan guys some time ago at a show. I put a challenge to them to air test one of their best builds over a period of five years - if there was a degradation in performance between year 1's test and year 5's test, would they give the home owner their money back? They categorically said absolutely not - it is an organic product and over time it will open up and adhesive sticking plasters will eventually fall off. They declined, however I would have loved to have that kind of data just for sake of education and improvement of housing stock. Innovate UK, a government agency, published a report back in February 2016 that stated there was no relationship between design and deployment - ie whatever is specified and expected in a design is seldom what appears in the finished product. A summary of that report is here: https://www.gov.uk/government/uploads/system/uploads/attachment_data/file/497757/Domestic_Building_Performance_Summary_2016.pdf Note recommendation on page 3 to "Designers/homeowners/policymakers" that states: I understand what you were trying to achieve with your detail - what did you end up doing given the contractor could not give you a quote for what you wanted? If you have achieved the uValues stated - you will be running your home on pocket change!!
-
pro's & cons of different ICF systems
najem-icf replied to mvincentd's topic in Insulated Concrete Formwork (ICF)
Up until recently, Durisol refused to be classified as an ICF and have only now jumped on the bandwagon by calling themselves the "first ICF" on the market. They are right in what they claim, however the application at inception was for use in non-habitable spaces like garden retaining walls etc. Personally, I have a number of issues with Durisol - firstly, they are not members of the ICFA, which means they are not accountable to anyone but themselves - that is evident from the posts you have read on here. My second issue is that you have a continuous material that features from the outside world to the inside world - in other words - a cold bridge. Third, they use foil faced PIR/PUR boards to "beef up" the uValue of the wall - however they pay no attention to the fact that every single PUR/PIR manufacturers BBA (or ETA) cert states that there must be a barrier between the concrete and the foil face. I have yet to see a Durisol build where the foil is actively protected. In essence, the concrete burns the foil and renders the board much less effective. Fourth, it is marketed as the only "permeable ICF block on the market" - in a day and age where air tightness is the aim, that should not be a selling point. Reminds me of an article I read when I was Stateside some years ago about a Durisol build 22 storey hotel in Canada - built back in the early 1980's - guests complained of "ghosts" in the rooms - later realised it was curtains moving due to air penetration through the structure. Then there was this article that summed it up for me - http://www.telegraph.co.uk/news/2017/09/01/grand-designs-dream-home-ruined-biblical-plague-moths - anything organic will eventually attract vermin. EPS based ICF's will either have a plastic or metal strip that serves two purposes - one is to provide EPS something to adhere to during the manufacturing process, second is to provide a fixing point for the next phase of construction. I know one manufacturer in particular has done extensive testing on pull out strengths of various screws into the ABS plastic strips - a standard drywall screw has a pullout strength of 95kg and a permissible load of 24kg per screw - the highest proportions were 130kg pull out and 41kg permissible. If you are still concerned, you are only 70mm or so away from concrete - in one case I recall using Simpson ICF-LC brackets cast into the ICF wall and attaching a timber runner to which you can fix anything heavy. These webs are factory manufactured, so will feature in regular intervals. If, for example, they are at 200mm c/c, you can measure from any corner and know you will hit a web consistently at 200mm c/c's. Most (if not all) EPS based ICF's have markings on them to indicate where the webs are. I have attached photographs of various EPS ICF's to demonstrate this. I do agree with your architect - while ETA's should be accepted Europewide, there is always a comfort and preference of Building Control to accept BBA/BRE/LABC etc as they are familiar with the formats. ETA's are also somewhat deceptive - I came across an ETA for an ICF that simply confirmed its use as a permanent shutter - no testing done on its thermal properties or fire resistance etc - not to mention that the product has a completely different name in the UK to what the ETA is for. Something else to consider would be the ease of getting mortgages - I often hear people saying they don't need a mortgage and are building using their savings - these are forever homes that they intend to grow old in. Nice thought - however - what happens when eventually the property is left to children/ next of kin? They are unable to sell it because people cannot get a mortgage (or the Loan to value is miniscule) and they will end up with a massive inheritance tax headache. So whatever you chose - make sure there is plenty of faith and support behind the block. ICFA membership is a good start (www.icfa.org.uk) and secondly, ask the suppliers what the highest building they have built in the last 12 months was - seems silly - but the reasoning behind it is simple. Whoever decided to take the risk and build a tall building will have done so after seeking assurances from engineers, architects, insurers, lenders, QS's etc - it would not have been a decision taken lightly on the flip of a coin. Hope this helps -
SIPs are a great product for their thermal efficiency. Using them on a roof is perfect. The issue with SIPs usually is the lack of sound attenuation that ICF can give you. SIPs is a timber product so will react to our forever changing seasons. As a result the airtightness blower test will always deteriorate as time goes on. ICF is a monolithic build - the concrete is poured in one go per storey (or higher if you are brave enough or have a competent, experienced contractor) so essentially goes off in one go and is, for all intents and purposes, one piece of concrete per storey and usually with reinforcement in there. Recently, PIR/PUR prices have shot through the roof and this has had a direct impact on the price of SIPs. The Grenfell disaster is also making people take notice of what they are putting in their walls, many are now insulating with EPS instead of PIR/PUR. My views have changed over the years - from being a complete tree hugger, I now firmly believe that concrete is the answer. We have been building with it for years, the Romans, Greeks, Egyptians all built with the stuff - and its all still there. Hope this helps - athough with this post being so old I am curious to know what you decided on.
-
Lenders will lend varying degrees on any method of construction. What differs is the Loan To Value (LTV) - so for example, some ICF's will attract the usual 95% LTV while others may attract a 45% LTV - its all risk related and each Lender decides on how much they want to expose themselves. Using two different construction methods will probably complicate things with some lenders, while others may not be phased by it at all. The ICFA has a letter on their homepage from the Council of Mortgage Lenders that you may find interesting - http://www.icfa.org.uk Hope this helps.
-
Hello everyone! My name is Najem (Naj for short) and I am new around these parts. I was asked by a client of mine to join the forum as he felt it would benefit the community here. First, a little intro: Started out life in Telecoms sales while studying when Orange first surfaced, sold my small company to a bigger fish that went on to sell to Carphonewarehouse. From there I worked in IT in London and Edinburgh - decided to retrain in architecture and ran my own practice for a while. Got into construction and that's where I got into ICF... Assisted a friend of mine who needed his home extended but could not afford the kind of prices builders were quoting. That was back in 2007 - and I have been involved in ICF builds ever since. I have used various products and know the ups and downs of them all. I settled on one in particular and my day to day business now distributes that particular product. I am very well versed in ICF construction, as well as SIPs, Timber Frame and Masonry. I have travelled the world to see how building structures is evolving due to our need to become more environmentally efficient, reduce build costs, increase building strength and life expectancy, not to forget creating the "dreams do come true" environment. Looking forward to engaging in discussions - please note I will do my utmost to be generic - my apologies in advance if I sway one way or the other. I am only human! Naj
-
I'm afraid I would have to disagree with your comment "it's the joins between blocks where you'd have issues" - almost all ICF blocks available in the UK are installed break-bond - meaning the joins are held together very comfortably. I have installed a few photos to demonstrate this. At most you will get water seepage but concrete pours will not cause any issues. Where you have vertical stack joints (ie a vertical line of joins) you would ply this up as shown on the photo (right hand side) using the grey block - this will keep everything together during the pour. While the ICF itself will not allow moisture to travel through it, we still have to comply with BS8102. BS 8102 defines 3 ways of water-resistant construction: A Barrier (Membrane) protection B Structurally integral protection C Drained protection Two are recommended at minimum - three is best case if possible. We normally use the A and B to comply. The remainder of your post is absolutely bang on the money. Just one small thing to note - I always recommend the use of a waterstop at the junction where the wall meets the foundation/slab. The best products I have seen for this are from Kryton. Waterproof concrete that is ordered from the plant are guaranteed so long as no water is added on site - leaks will become apparent very quickly after the concrete has cured. We have not had any issues with water ingress in ICF so long as a waterstop is used. This is my first post here - apologies if I have not followed etiquette - we all gotta start somewhere