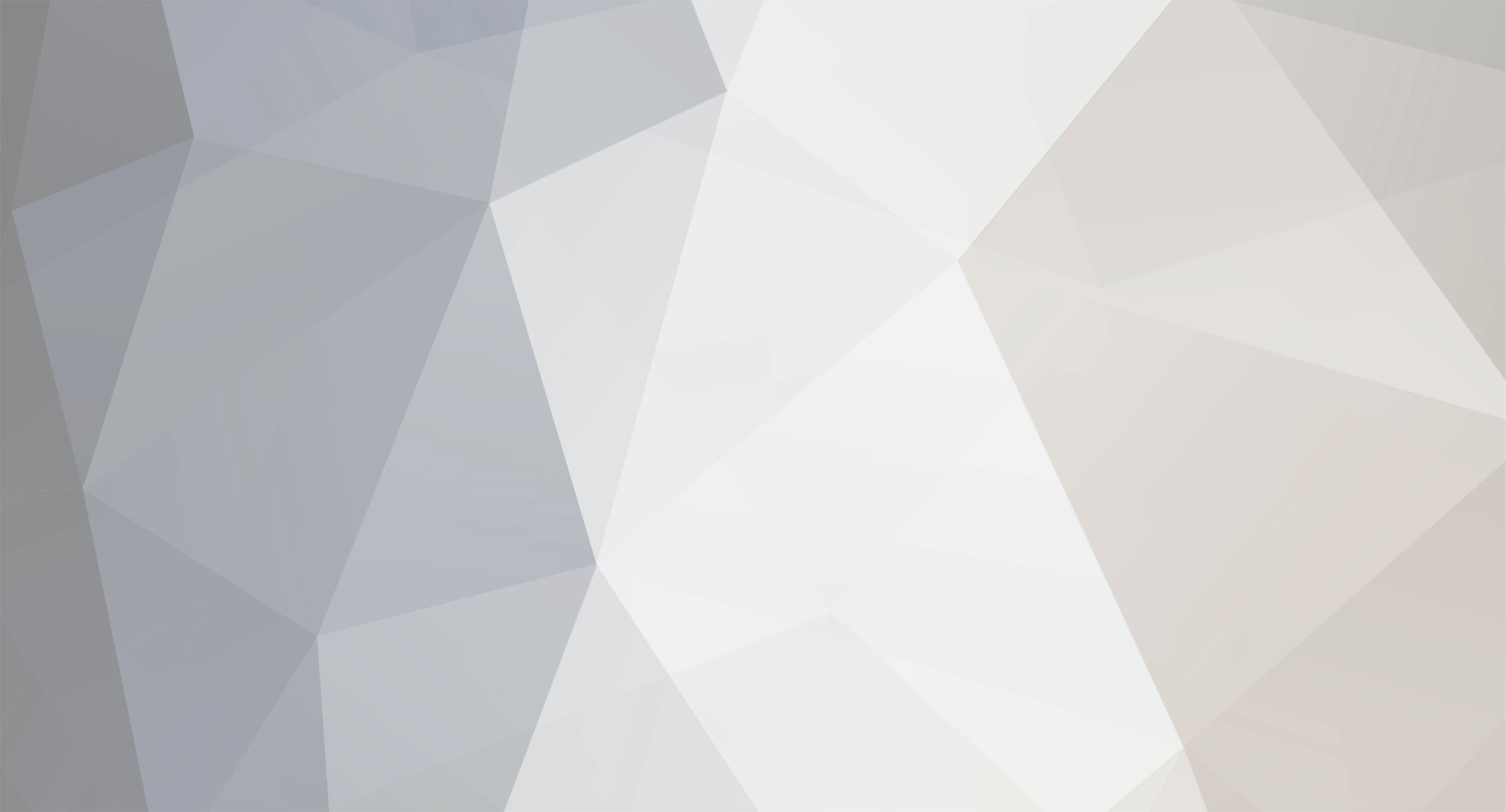
Thorfun
Members-
Posts
4698 -
Joined
-
Last visited
-
Days Won
35
Everything posted by Thorfun
-
Can you contact LuxPower to ask them if their BMS can handle different manufacturers of batteries?
-
AC can be for downstairs too! Many times this year while working from home have I used the AC in my study.
-
We missed with screws through battens and 80mm PIR in to 38mm wide studs often. Just slapped some airtight tape over the hole and move on! I also told every trade who came on site about our airtightness requirements and said if you make a hole to let me know and we’ll seal it. In the end had to do that pretty infrequently as they all seemed to get what we were trying to do.
-
Why don’t you just use optimisers to get over the shading issue?
-
i had a countersink bit with the drill bit in it already so did both in one go. 😉
-
don't know. i've not tried since as i'm happy with single phase for now. if i ever need to start using 3-phases i'll look in to it then! hopefully the OP has considered this though.
-
this is the key point! how many suppliers offer a modern smart 3-phase meter that actually does net metering? when i had my meter installed a couple of years ago getting a 3-phase smart meter was next to impossible.
-
Out of interest, are you going to run the house on 3-phase? We have a 3p supply but run the whole house on a single phase and so our PV inverter is also single phase and can power the whole house. If splitting over 3-phases you will have to balance what appliances use each phase PV production so, afaik, you’re more likely to “waste” generated electricity if nothing on a phase is running. It just all complicated the house electrics for me and I’m happy we kept it simple! I have run a 3p cable from the cabinet to the house so I can install a 3p EV charger at a later date if required.
-
Like Nick said I think you’re over complicating things just put a board up and chalk line where the cross battens are and you can’t miss! (Unless they’re screwing at a strange angle) and we pre drilled and countersunk all our service cavity battens. Got a cheap table drill and eventually got it down to a short overhead of time. But we were doing it ourselves so weren’t paying someone the extra time it took.
-
i hope no one gets burned financially by this. our TF company Flight Timber went out of business and i remember at least one member on here lost money because of it. i think if i were to ever do this again i would seriously consider a stick built house. could then buy materials as required through a local BM and substantially reduce risk
-
you da man!
-
only 9/10? you need to up your game mister
-
You sound like that CEO who lost his job and family coz he got caught on camera with his head of HR. He blames Coldplay.
-
Battening for Vertical Timber Cladding - Tips, Hints and FAQs
Thorfun replied to Thorfun's topic in General Joinery
i can only presume so but tbh i didn't even remember asking. i just asked my BM for 2x2 and they sent stuff over. 🤣 we used 90mm nails to fix the battens. they're also mildly galvanised afaik. but our cladding is tongue and groove and so very little water should get behind it so i wasn't worried at all. -
Openreach taking the proverbial for tree lopping
Thorfun replied to BotusBuild's topic in Electrics - Other
@BotusBuild our copper broadband is finally installed and running. In the end I raised a complaint with EE and our order was escalated on openreach and, despite this we got loads of “update by next week” type messages until the message was “Openreach need to cancel your order and then you’ll need to raise a new order which will be escalated and expedited“! once that was done we got an appointment for OR to attend a couple of days later to connect the cable and got it working. it’s taken about 8 months, although only about 5 months of that was with EE who have been very communicative throughout and it was obvious all the delays were on the OR side. I’m looking forward to seeing what the compensation I’m due will be. so if it drags on some more ask EE if you can lodge a formal complaint as to how long it’s taken and ask to have your order escalated.- 16 replies
-
- 1
-
-
- tree lopping
- openreach
-
(and 2 more)
Tagged with:
-
If your inverter of choice already has certification then it should be pretty straightforward. Ours was solaredge so it was easy. but I went through this quite a while ago so can’t really remember! I think I posted about my G99 application on here though so might be some information in there if you can find it.
-
Drain/gulley in patio......recessed or flush?
Thorfun replied to Thorfun's topic in Landscaping, Decking & Patios
Thanks @nod out of interest is it normal to keep the square surround or ditch it and just keep the round drain top? -
got a last minute question! the groundworkers are pouring our patio slab tomorrow and we have a drain/gulley from the flat roof above that will eventually have a rain-chain on it going in to a plant pot that will sit on top of the drain. they're saying that they've set the level of the drain cover to be about 5mm below the concrete slab which means it'll be about 30mm recessed from the top of the porcelain tiles. I'm thinking it should be flush with the patio tiles. what does the forum say?
-
-
and don't forget acoustic sealant to fill all the small gaps!
-
I think it’s 12kW
-
Battening for Vertical Timber Cladding - Tips, Hints and FAQs
Thorfun replied to Thorfun's topic in General Joinery
Just standard 2”x2” for us (ends up about 45mm/47mm). No angling at all, figured that as the cladding was tongue and groove very little (if any) water would get behind. -
We used these https://www.impeyshowers.com/Wetroom-floor-formers/Aqua-Dec-EasyFit-Wetroom-Floor-Former/ made things easier to fit!
-
With a ducted system there is minimal drafts that we can feel. but I agree with the wall units. Careful placement is required so you’re not sitting in the draft. one regret I have is not having the money for ducted system downstairs and having to have wall units instead. But something had to give as money runs out quickly!