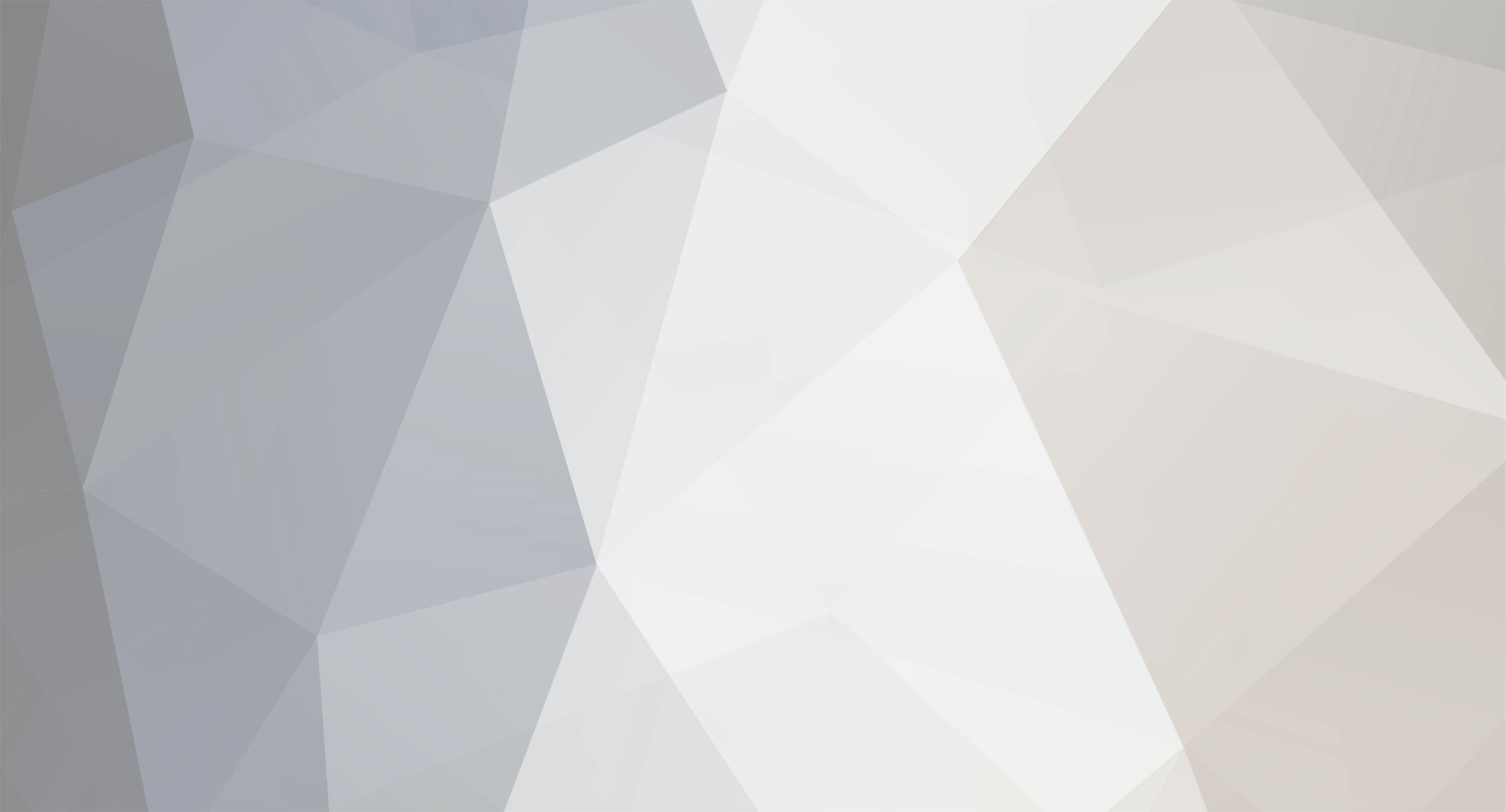
Dan F
Members-
Posts
1422 -
Joined
-
Last visited
-
Days Won
2
Dan F last won the day on September 16 2024
Dan F had the most liked content!
Personal Information
-
Location
Berkshire
Recent Profile Visitors
5433 profile views
Dan F's Achievements

Advanced Member (5/5)
386
Reputation
-
We used a designer. Yes, there were fees involved, but not very high vs other professional, and was money well-spent I think. Depends what you want to do though, only makes sense to invest in a designer if you want something more than standard and are happy to pay for the fittings. We also used Loxone. Went with DALi for all fittings, so have full control over mood creation with no limitations based on how circuit were run. Not a must I know, but satisifies my desire for programmable flexibiliy, and have used in on a couple of occasions to: - seperate downloads into different zones (center downlights vs wall-washers) - disable downlights near TV in tv-viewing mood, while leaving those above table on.
-
That is a solid choice for indoors if you not deperate to get on the wifi 7 bandwagon. Outside the U6 Mesh is a significantly better option in terms of wifi standard and coverage, but it depends on your requirements. If you just needs a basic AP wifi-5 AP without too much coverage UK-Ultra would work.
-
Thoughts on commissioning a Vaillant Arotherm Plus 12kW
Dan F replied to sharpener's topic in Air Source Heat Pumps (ASHP)
What information specifically? I have a 7kW which is quite a bit oversized. Yes it cycles, but having adjusted the integral settings I have minimized this. Also, 7kW heats DHW faster than 5kW would. Cycling is to be expected and not something you should try to avoid at all costs, that said you clearly don't want to significantly oversize and you want to ensure you have enough system volume to minimize frequency of cycles. -
Thoughts on commissioning a Vaillant Arotherm Plus 12kW
Dan F replied to sharpener's topic in Air Source Heat Pumps (ASHP)
This is nonsense. All the aroTherm+ models modulate down. 10/12kW models don't modulate down as much as 7kW though, and 7kW doesn't modulate down as much as 5kW can. There isn't a single value for miniumum kW output as this depends on flow/external temperature, but you can find this info in the data tables. You don't need an additional circulation pump(s) unless you have hydraulic seperation (buffer, HEX etc.). There is a preference to avoid hydraulic seperation in most install currently as an "open loop" approach is simpler, cheaper and generally gives best efficiency also. That said, there are cases where a buffer may make sense, this depends on how many circuits you have, what they are used for etc. -
Carpet cleaner might have worked, but it would need to be one with fairly strong water jets to list the fines out of the tarmac pores before sucking them up, rather than just brushes which wouldn't reach the fines. In the end we had our window cleaner have a go at it with a pressure washer and gutter vacumn (two guys, one on each). Took a while, and didn't give a perfect result, but I think we probably got 80% back to as new cleaniness/permeability. Enough to lay resin without being concerned about pooling anyway. That said, we did go for a thicker 30mm resin system on a plastic grid, vs. the intial plan which ws 18mm bonded directly to the tarmac, to mitigate risk further.
-
Control cable is often used to connect a CT clamp of some kind and allow the EV charger to do load management. Some EV chargers also have ethernet connection. Don't think load management is required, but depending on your main fuse size and expected load may be a good idea to have in place. This can be a seperate cable, as @Alan Ambrose said, doesn't have to be special all-on-one EV cable. 25mm2? Is this 50m+? Seems overkill otherwise..
-
We had 70mm open-graded tarmac laid on our drive just before we moved in 3 year ago. Since then, we've completed landscaping works and one of the few remaining things to complete things is to lay some resin. The result needs to be permeable and shouldn't pool. Permability after it was installed was great, with only a very small amount of surface water for a short period of time if there was heavy rain non-stop for a week. However, duing landscaping work, getting MOT and topsoil on the drive was pretty much unavoidable, and while it is still somewhat permeable we do have significant pooling in a number of areas. I haven't wanted to rush into getting resin put down as we don't want to proceed with resin only to find that the resin doesn't drain. The resin supplier has suggested a few things to mitigate this: - Drill holes in the tarmac, especially in areas we see pooling currently. - Use 10mm vs 6mm aggregate to increase permeability of resin. - Use 35mm resin on a grid, rather han 18mm directly on the tarmac as orginally planned (so resin layer can hold more water and water can distribute within resin layer). There are all great suggestions, and probably ones that we should follow, however I'd feel more confident if we could restore the permeability of the tarmac first. Pressure washing just move the fines around and doesn't improve things, so we need a different approach. According to Tarmac: However, the only versions of this that I have found online as large road-sweeper machine and charge £1000's day rate. Given drive is only 120m2 or so this does't make sense, yet I can't find anything smaller/cheaper or any self-hire options. I may well be looking in the wrong places though. I've wondered about hiring a higher power/capacity wet vaccum and then trying to do this myself and have also seen a product call "rotaryvac" [1] which I thought about trying to hire somewhere, but thought I'd see if anyone here has any experience of advice before I start experimenting..? [1] https://equip2clean.co.uk/products/kiam-rotaryvac-21-rotary-floor-cleaning-tool-with-fluid-recovery-vacuum-system
-
As I said, mine may have stopped at 80rps because it had already drosted enough, hard to tell, but even when mine is running flat out at 100%, defrost only reaches 80rps. I graphed this via ebusd/emon: I also experimented by setting NR mode to -50% (limiting compressor to 60rps), and defrost compressor still rose to 80rps. I'm can't say for certain that NR doesn't impact anything related to defrost, but it certainly doesn't constraint compressor to NR setting on mine. IGNORE THIS. FORUM WON'T LET ME DELETE IT FOR SOME REASON..
-
On my system, compressor speed on defrost only seems to reach 80prm (67%). It may go higher if needed, I'm unsure, but I haven't seen it go higher recently. Defrost compressor speed appears to ignore any noise reduction or eco modes, so AFAIK there is no way to limit defrost compressor speed or noise. My 7kW allow for -30%, does yours not? (I know the manual only says 40-60%).
-
80% was DALI or LED, and it was easier for electricians to use same cable everywhere and avoid any mix-ups. If you drivers are local to fitting you going to need more than twin-earth anyway, unless control is wireless or you have a seperate dali/dmx/tree/control cable. One example of where having this 5-core in place was handy was bedside lamps. We ended up choosing some wall lamps that have a wall light an a reading light, by using 4 cores were were able to give it a permannt live for the reading light (locally switched) and have the wall light on a loxone-controlled dimmer. We couldn't have done this otherwise once everything was boarded. It also meants that, when we finally source and install pendants we have option to use mains dimmed or DALI etc. You're right re: tree via 5-core. The scenario I was thinking about was a pendant in the hall, where we only decided later to use the Loxone pendant. What we did in this case was use the 2 cores (of the pre-wired 5-core) to supply 24v to the pendant, and then brought tree from the closest light switch.
-
We used 5-core in most places for lighting unless we knew that the lighting circuit was definitely going to be i) single-color ii) use a cabinet-based dimmer. Wtih 5-cores we could then: - power RGBW or tunable strips from with central LED driver, - send 230v + DALI to remote drivers (all our downlights and some other fittings are DALI) - send dimmed 230v - could even send 24v + loxone tree if needed. (albeit overkill core area)
-
Victron does too, and I'm sure others do too, includig Sonnen. Just need to check datasheets .
-
We had a consultant do our initial version, but i actually spent a lot of time learning it (bought the printed manual) and I used this knowledge to update and improve a few things that weren't quite right too. It's doable, but I know from experiencia how much time investment is required to even try to get it right. Also, how much of an impact things like exact glass specifciation, ventliation and how tress are modelled have have massive impact and change results fundamentally.
-
Thoughts on commissioning a Vaillant Arotherm Plus 12kW
Dan F replied to sharpener's topic in Air Source Heat Pumps (ASHP)
Start with inactive and try to find your correct heat curve, you can then switch to active which is more forgiving and adjusts better to solar gain etc. Expanded has its uses, but it's typically not a good idea. Adaptive WC is not really recommened either. Don't touch integral or hysterisis configuration until you've done the above, only then are you really in a position to understand if either of these need tweaking. -
Thoughts on commissioning a Vaillant Arotherm Plus 12kW
Dan F replied to sharpener's topic in Air Source Heat Pumps (ASHP)
Expanded doesn't ignore energy integral. Adapative WC is typically not used or recommended. Energy integral is -60 by default, not -90. Don't think pressure should be varying like that, mine doesn't.