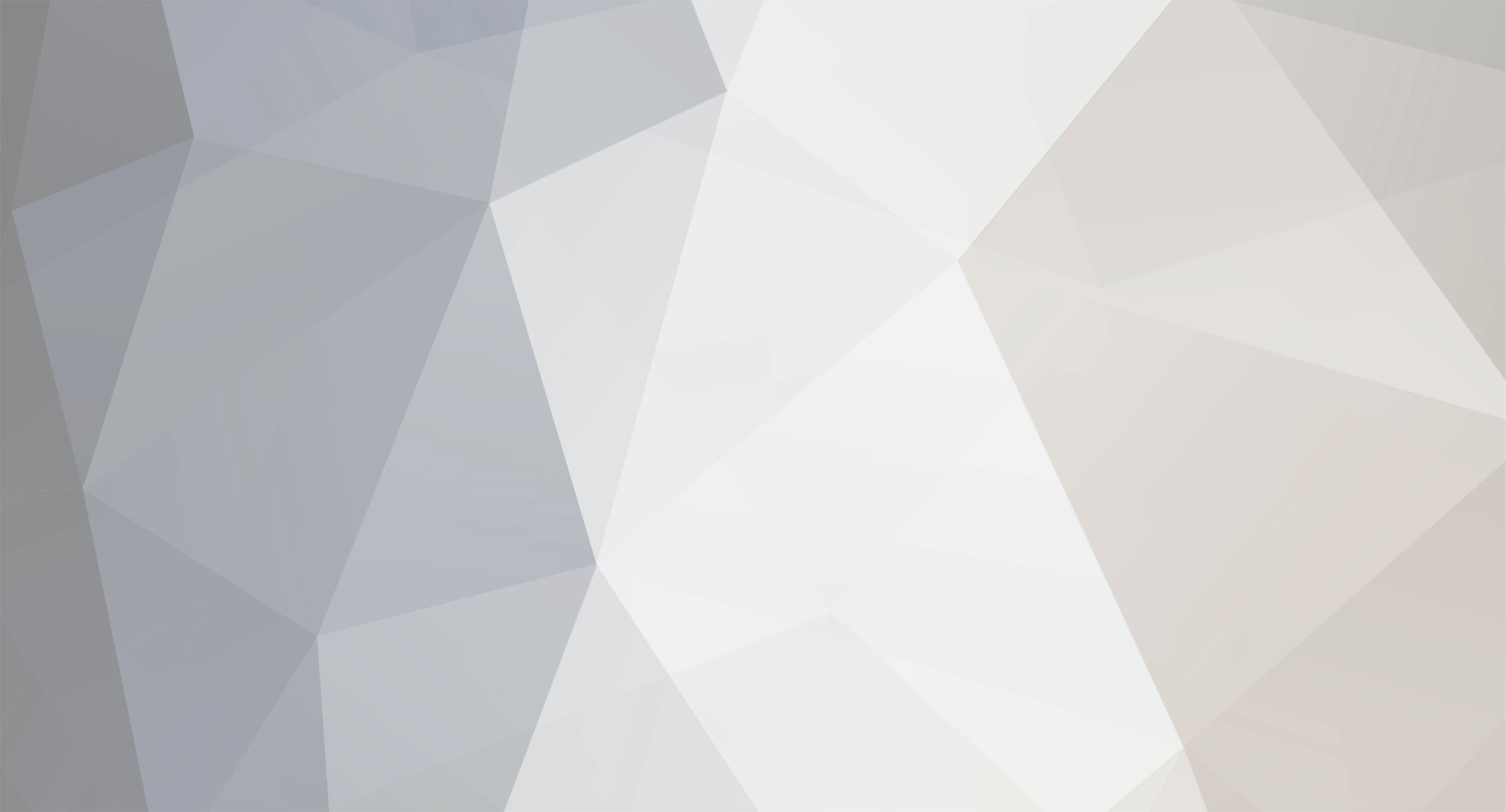
eandg
Members-
Posts
757 -
Joined
-
Last visited
Everything posted by eandg
-
2700 is far superior to 2400 and extra costs are pretty negligible. As said about also let's you drop a ceiling if need be (we actually went 2750 then used resilience bars).
-
Be an absolute waste if you don't do it right then... In the scheme of things a bit of extra cash on insulation and airtightness is pennies. We were probably another 10k on getting above building regs minimum and it'll pay itself back in 5 or 6 years.
-
We covered pipework with pea gravel and then backfilled with what had been dug out.
-
We went with Ecology, who accepted a spreadsheet setting out a breakdown of quantities and costs for materials, with a separate column for labour costs for each element (some was nil cost as DIY, some costs for trades).
-
I thought our joiners did very well and they were on a bit less than a quarter of the £48k you're allowing for erection... Plus if you go supply and fit then you aren't out the VAT which helps your cashflow, and you pass much of the risk onto the supplier. I've no idea how you think you can handball sips panels into place, particularly at height and on the roof. It's not necessarily complicated but if you've anything a bit unusual, steels/glulam then you really want someone that's got a bit of experience erecting for you.
-
SIP wall thickness vs u value
eandg replied to Bournbrook 's topic in Structural Insulated Panels (SIPs)
65mm facing brick 50mm cavity 142mm sips kit 60mm PIR 25mm typical service void 12.5mm plasterboard 355mm total -
SIP wall thickness vs u value
eandg replied to Bournbrook 's topic in Structural Insulated Panels (SIPs)
We looked at various sips kits but found going with 142mm Kingspan and augmenting it with our own led to best u-values. (We put 60mm in walls and 100mm in roof). Obviously not the only part of the story but our as built SAP rating is 101 and it's a very warm house. Do the additional insulation and the airtightness yourself to make sure there's no shortcuts and voids. -
No - decided against it on durability (and cost) concerns and went with LVT, which we are happy with instead.
-
Same approach here and sound only tends to transfer up the hall and come in via any open doorways than through walls. We did have 9mm OSB for racking on most walls though.
-
You get 0% loans and 75% cashback up to £7.5k for an ASHP, 25% for solar PV and different rates for other renewables. Cashback on a max of two technologies and a loan for anything else (but MCS requirements mean any additional technology will be dearer than you could get buying yourself and paying for installation).
-
Lessons learned from last ready - getting ready for cold snap
eandg replied to Conor's topic in Air Source Heat Pumps (ASHP)
Thanks - will do. -
Lessons learned from last ready - getting ready for cold snap
eandg replied to Conor's topic in Air Source Heat Pumps (ASHP)
We've just left it as the installer set up. 7kW system, 50° water temperature. UFH on ground floor only set at 21°. -
Lessons learned from last ready - getting ready for cold snap
eandg replied to Conor's topic in Air Source Heat Pumps (ASHP)
So using that metric our COP is 3.16 which doesn't seem great. Will that improve in the better weather when the temperature differential is less? Anything we can do to improve it? -
I'm planning for something similar next year but will be looking to get the found done in the next month or so while I've machines/groundworkers in. Ideally looking for something well insulated - plan is for 89mm CLS studded timber frame with mineral wool fill, then 50mm PIR the other side so decent enough u-value. Wood burner inside. Was thinking we'd want maybe 150mm PIR/200mm EPS floor insulation but not sure what build up should be and I'll need to decide for getting levels done.
-
Looks nice and tidy. Await the jumble of copper pipes when your tank gets fitted!
-
I'd get a commitment from them that they'd do that for your build in that case - huge difference in being a client with a regular stream of work (like a big contractor/developer) and a one-off house builder with little prospect of repeat work. Chances are you'll be very much viewed as the latter and you'll need to accept that in most cases subbies will go where the money is and you'll not always be at the front of the queue. Do that, keep healthy communications with your trades with a bit of come and go, and have a ready supply of caffeine and some decent biscuits and you'll generally be fine - but you'll never complete in two months. Or get a main contractor in and have penalty clauses in your contract if you're wedded to that timetable.
-
Same - was only an extra £40 or so. Through Protek. Cover not enough for a crane but okay for telehandlers and smaller machines.
-
I think you'd be doing exceptionally well to go from weather tight to complete in two months max unless you have access to a large supply of subbies like your developer clients do - particularly if you are reliant on finance and getting staged payments following valuation to allow you to progress. I'd recommend being prudent and budgeting for 6-9 months; also note that most self build lenders lock you in for two years so factor that into your budgeting - even if you think you'll be complete in a matter of months you're on the hook for the extra cost of financing through a self build lender.
-
Same. It didn't look too hard but that's the fitter's skills and experience and the finish was spot on. Wish I had him on a day rate as he did very well and rattled through it - but it'd easily have taken me three times as long and with a lot more waste.
-
Lessons learned from last ready - getting ready for cold snap
eandg replied to Conor's topic in Air Source Heat Pumps (ASHP)
We'll have the same unit and have the same set up with heating only downstairs, though the house is about a quarter smaller than yours (208m2). UFH set for 21 between 7am and 10pm and yesterday was our highest use yet, using 34kWh of electricity all told (which includes for the usual dishwasher, oven, showers, washing machines on etc). I'm not sure how we find out about defrost settings, heat demand and calculate if our flows are right etc. but does that sound reasonable enough (or not excessive enough to spend my weekend working out how to make the set up more efficient)? -
I'm about 95% happy and not one for sweating the small stuff too much. Unlike the general experience I was by and large very happy with the work done by trades but most we used were either pals/folk I knew (and had confirmed by others their work was good) or recommendations, which will help reduce the risk of having a cowboy on site. The only exception I'd make is for groundworkers, and I also wouldn't let anyone near airtightness or insulation - do that yourself as there's no understanding at all among trades and not enough care for the things you won't see.
-
I didn't find painting vaulted ceilings with a roller too onerous. A coat of plasterboard primer had dried more or less in time to start again with the emulsion - used slightly dearer (Valspar) stuff and it only needed one coat. My neck was glad when it was done though.
-
I'd check that out as our supplier told us ventilation was definitely required. There's also been some complaints on here about SIPS not being great with noise and while that has not been an issue for us I would think decoupling the metal roof from the structural one by way of a battened out void would be a good idea (we also had a noise dampening/anti-condensation layer fitted below the standing seam panels).
-
Do you not require some ventilation? We used standing seam but it went into 22mm sarking board on battens creating a ventilation gap to our sips roof.
-
Missing insulation in vaulted ceiling
eandg replied to d87francis's topic in Lofts, Dormers & Loft Conversions
I don't understand the English system at all but can't see why the LA would have an interest when they've not been paid to. From an enforcement perspective, if it's like Scotland then they'll only get involved if there is any imminent threat to public safety. I personally wouldn't waste my time with it all and would do as suggested above - line up local media and use it as leverage to get some cash from the developer and then do it properly yourself.