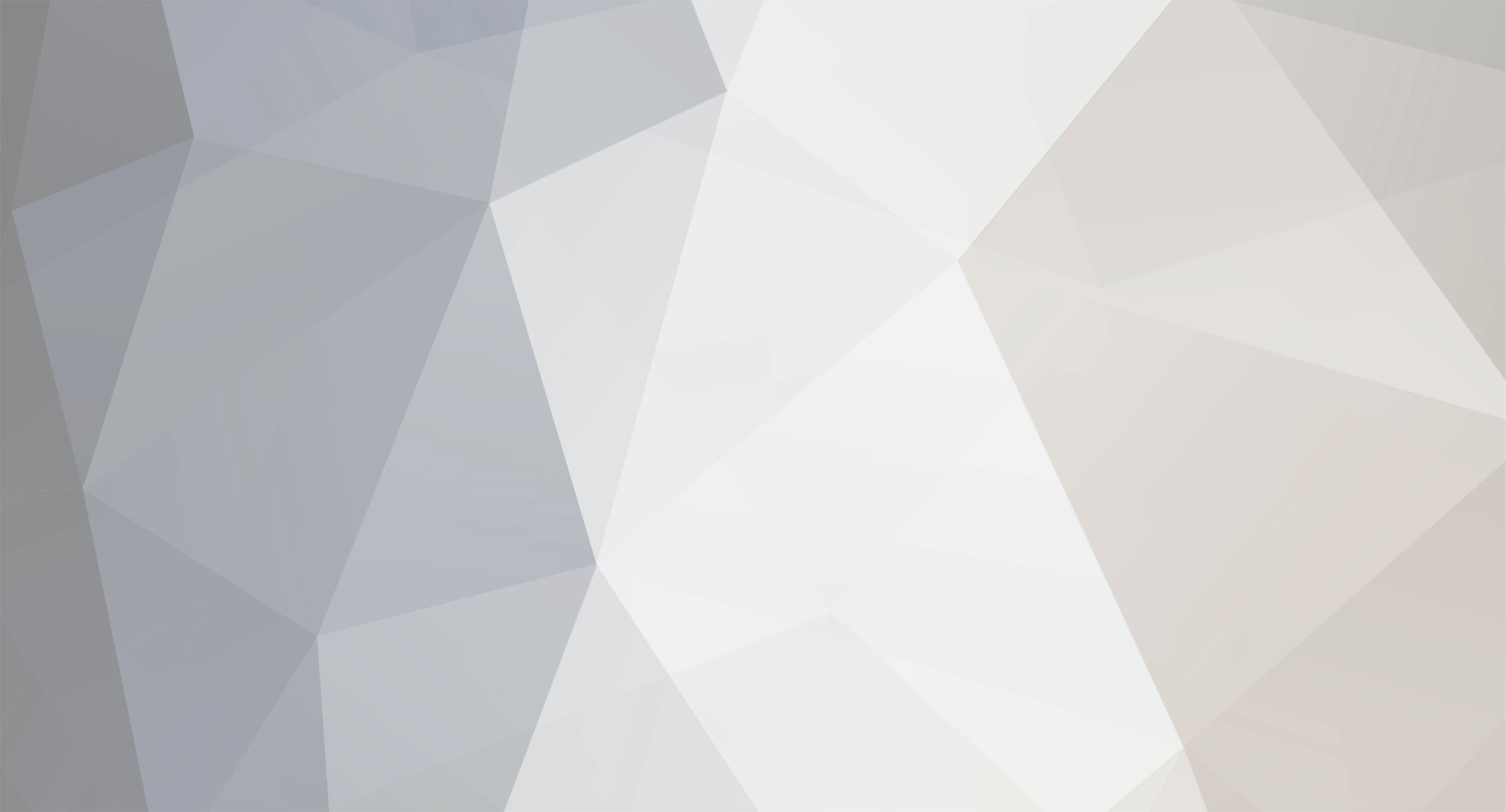
scottishjohn
Members-
Posts
4222 -
Joined
-
Last visited
-
Days Won
21
scottishjohn last won the day on June 16
scottishjohn had the most liked content!
About scottishjohn
- Birthday 09/11/1951
Personal Information
-
Location
south west scotland
Recent Profile Visitors
5994 profile views
scottishjohn's Achievements

Advanced Member (5/5)
1.2k
Reputation
-
as title going to plumb up the sewage for next phase rebuilding of old stable to be 2 holiday rentals so even though not doing it now I already have water +elec in there --so sewage connection would be good to put in before surfacing the large area in front of building and fire pond even if just the manhole outside to connect to - and connect to rest of septic system then I can continue making the rest of the areas around the house and compound complete and finished do not want to have to dig up later bit of an old picture bshows how far we have come
-
wallpaper is a good way to hide the crappy plastering my dad was master painter and decorator and specialised in anaglypta and his biggest job ,so he told me, was the free trade hall in manchester in the 30,s took months to do and he was not happy with the hieght of the saffolding !!! maybe he was the only one mug enough to do it thats when it was made from rags not just paper and would last for ever and could have just large embossing , if done right you can still find it in victorian houses sometimes
-
I would think its very hard to do a dry mix and get it perfectly level --thats why proper screed is very sloppy --so it self levels to an extent I would consider how you going to get it smooth and flat enough for your floor I know my floor men --would not even consider using stick down lvt without using self levelling on top of the screed and then grinding it before laying the floors If your going to use cermaic tiles =--then not so much of a problem but your screed still needs to be as perfect as possible
-
where is your planning officer based?
scottishjohn replied to scottishjohn's topic in Planning Permission
and where they work from-all by email and google earth and no site visits -
Iwas speaking to 2 people in my area and to my suprise the first one told me his planning officer was in belfast the second one even better his officer is in ATHENS greece just shows howeverything id odne by email adn how short of planning officers some areas are
-
and of course in my area where planning are toal power freaks --its 6m for planning
-
Advice on Solar and whether to go 3 phase
scottishjohn replied to d438a1's topic in Electrics - Other
-
What next for heat pumps after BUS and MCS?
scottishjohn replied to joth's topic in Environmental Building Politics
what makes you think I,m a tory itar them all with the same brush -
What next for heat pumps after BUS and MCS?
scottishjohn replied to joth's topic in Environmental Building Politics
Idon,t know what you are all worring about we have all the politicians telling us electricity is going to be cheaper with building more wind and solar farms and if you believe that you will also belive labour are going to "smash the gangs" and stop the boats -
that will be correct and if you want to sort it out you will have to spend some money if it goes to court they will only look at written documents # sowhat he says to you is not worth the paper its wrtieen on its the same with every legal thing -- inwriting is what counts thats whay isaid before just build your own fence on the boundary so he cannot over hang it after that its proper survey aand drawings bsck of fag packet will not work in court and any drawing you do with no letters after your name is worthless
-
Timber Cladding in the Scottish Highlands
scottishjohn replied to North80's topic in General Construction Issues
yes not just fit and forget like stone or brick -
found a screen shot octopus sent me a month ago for both flux and flux intelligent first one is flux lower one is flux intelligent
-
just go on octopus site and look for flux intelligent you have to enter youtr postcode so it might be different where you are just looked and i,m telling you lies import+export normal hours is same at 21.88 import+export atpeak times 4-7at night 29.18 for my postcode
-
yes but balancing them -so water does not just take easiest route eg going round the rads --will be the main problem and it sounds like you do not want to have zone controls and individual stats . both my UFH systems have each room on its own control and is the right way to do it no good UFH system will just have thermostatic valves they will have individual room stat and programmers
-
my thoughts based on having UFH runing from lpg and then ASHP in same house the main difference was that the ASHP -cost alot less to run than the LPG your first and critical job is the insulation --what ever system you go for I can also confrim that from experince with my new house --nearly moved in --next week is permanent move in it is a1730 granite house with a TF built inside it 150mm pir insulation concrete sub floor then insulation and UFH pipes -then screed stuck down LVT flooring although i have been running both houses at same base internal temp the new refurbed/ old house feels much warmer cos there are NO DRAFTS so what i am advising with which ever way you go is concentrate and spend most attention on insulation and draft prevention my new/rebuilt old house is 400sqms of floor space and is same or cheaper to heat then the old one which is less than half that size I have had ashp running on this house since november last year while the builders were doing things and the temp was raised somewhat to dry out the floor for the stuck down flooring as for running ASHP and rads it should not be more expensive to run than gas and all you need is to make rads larger basically twice the size as water temp will be nearly half of boiler temp -- and run them at alow tempwith moore surface area if size of house precludes that then stay with boiler My feelings are that you cannot over stress tthe importance of the air loss and insulation