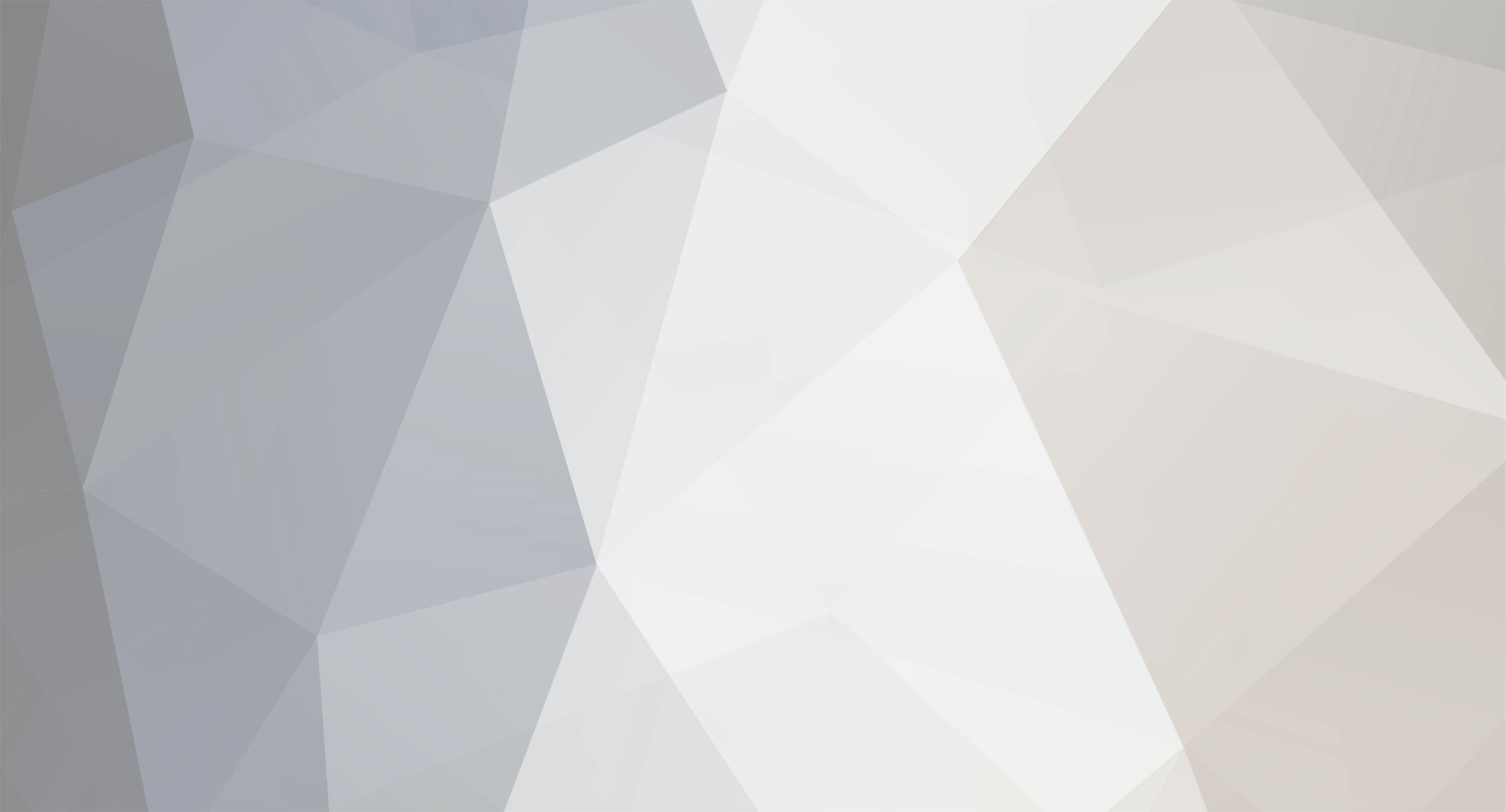
Redbeard
Members-
Posts
1206 -
Joined
-
Last visited
Everything posted by Redbeard
-
I would probably not be remotely bothered about the chimney - there's not much of it and you might not keep it anyway. But 'nothing wrong...'.?.. till it droops?
-
Note there is a difference between an RICS 'Full Structural Survey' (or whatever it is now called - I cannot remember) and a Structural Engineer's Report. The latter will, if you so instruct, report simply on the issue in question.
-
Is this a single-storey property, or 2-storey? Can you post some general pics of that elevation externally? Those bricks look weirdly long, unless the internal pic is somehow distorted.
-
How about: Take the gutter off, fix notched uprights to the existing uprights, the notches allowing them to protrude up above roof level, and fix a horizontal bearer across. This stops your scaff planks falling off the roof. In fact if you take some timbers from there up the line of the roof to where you want to stand, you can them use those timbers to hold your 'stand-on' timbers. I take your point re installing 'cross-noggins', but are you not still standing on the polycarb even with those underneath, with point-loads of feet, instead of spread loads in my 'model'? See my suggestions above.
-
Stroma private building control. Any experience?
Redbeard replied to flanagaj's topic in General Self Build & DIY Discussion
I'd go with your gut feeling, then, and go for LA. -
Stroma private building control. Any experience?
Redbeard replied to flanagaj's topic in General Self Build & DIY Discussion
No, but my general experience of LA vs private BC has been that LABC are more thorough, though to be fair, see-very-little 'fly-bys' can be common to both, and the use of photographic evidence is, in my view, at very least a mixed 'blessing'. -
If the flashing remains intact then it seems to me the top (although not where it should be) will not leak. Do you think I am correct in this? If so... cut pieces of 45x45 PSE to fit in each 'bay', fixed to the ledger-plate at the top to prevent 'droop', then make 'tingles' (glorified 'slate straps') to hold the bottom of thhe sheets to stop them falling further. So, 'downstand' down the face of the wall-plate, horizontally across the wall-plate towards the lower end of the poly sheets, then an upstand holding the sheet in place, with a drip-end on it (a little - 15mm? - 'turn-down). Or maybe I haven't read the OP well enough... Yes, I hadn't read the OP well enough!! I see the flashing tape is damaged. Scaffold planks across the lot to support you and spread the (otherwise) 'point-loads'. I would suggest do this *after* you have put the restraint straps on the bottom. Then repair the flashing. (Assuming it is 'flashband' perhaps take the opportunity to do in lead - don't forget the patination oil. Unless you feel you have to I don't think there is any need to hammer the sheets back up as you suggest. I think my 'remedials' suggestion sorts that.
-
I suspect the more important Q is how far down will his wall start? If it is genuinely 3m tall it will have to start in a trench probably 900 (all right, maybe only 600, but I am Not A Structural Engineer) deeper even than that. If he does not start below the level of your land then, as far as I can see, it may be able to behave like a snowplough over the years, slowly moving his garden towards yours! But I may be wrong!...
-
I have had many more problems with nuisance tripping with my 3 linked mains-fed alarms than with any battery alarm over 30+ years. I now use the 10-year sealed ones. Mains-fed was a stipulation of BCO but they did not have to live with the jolly things going off at random times. We have not-linked but functional alarms in the relevant areas which do not nuisance-trip.
-
That's incredibly well camouflaged!
-
I wondered if maybe you'd got too much caulk. That won't rough up without looking like it's been attacked by a magpie. I cannot explain why the top and sides peeled. You mention plasterboard. Was it joint-filled and then paint straight on the plasterboard? That should adhere OK, but if it was skimmed it could have been over -'polished' - again, potential poor adhesion. Come to think of it, if it is just joint-filled, that may account for your top and sides if the joint filler was over-trowelled. Have to say I have never had adhesion probs on tape and fill pl'bd. I have no idea bout the colours of masking tape I'm afraid - all a bit hi-tech for me! It was (and is) all buff for me!
-
It looks like just inadequate adhesion/'keying' of the pink paint to the white under-layer (what is it?). Can I guess that you have maybe run the skirting paint (a top-coat) onto the wall? If this is the case then it's your reason; gloss (or satin or whatever) is a top coat and not designed to 'hold' another coat on top. Fine sandpaper, rough it up, preferably use an undercoat, then gloss/satin on top. (Alternatively I may have misunderstood the issue, in which case please tell me where I have 'mis-assumed' and correct me).
-
+1 to @Iceverge's a/t tape. Unless there is a solid layer behind the membrane I do not see how a squirt of sealant can be relied on to actually seal the hole. (And, come to think about it, if there is a solid layer you can't get to the hole itself anyway (to tape or to 'squirt' - You'd just have to squirt sealant down the batten-hole and hope. All a bit 'loose', perhaps.
-
Is this habitable space or a garage/outbuilding? And I assume the membrane is a breathable membrane to go under tiles or slates, not a 'flat roof' membrane such as EPDM or felt. Can you confirm? If it is to be battened and tiled or slated I'd say get the joiner to staple the membrane, unless you know the roofer is coming before it rains! On a related note (I am not a roofer) are you/is the roofer using counter-battens?
-
Where does your rainwater go?
-
It does but how would you detail the 'raw' PIR perimeter on the outside - just a timber (or Alu?) fillet?
-
Yes, FM330 is air-tight foam.
-
Strictly it does not help the paint adhere to the building; it (and a bit of scrubbing) takes off any algae to which the paint would otherwise adhere, rather than to the brick. If you paint over the algae - algae falls off; paint falls off. After application of the algaecide you once more have propitious conditions for the paint to stick to the wall.
-
Sorry, what is the 'it' in your Q ? The algaecide?
-
Help! How can we avoid trickle vents on a Jacobean cottage reno?
Redbeard replied to Amberella's topic in Windows & Glazing
Yes, in the wall, and no, not in every room. The idea is you put them in the wet rooms, so that the 'pull' extracting moist air from the wet rooms *pulls in* dry air via the other rooms, so yes, trickle (window or, as preferred, wall) vents in all or most 'dry' rooms. -
Help! How can we avoid trickle vents on a Jacobean cottage reno?
Redbeard replied to Amberella's topic in Windows & Glazing
Agreed 'get vents' but if the OP does not want them in the windows they can be elsewhere. (and see my point above). -
Help! How can we avoid trickle vents on a Jacobean cottage reno?
Redbeard replied to Amberella's topic in Windows & Glazing
I do fully understand that, but have spent years advising clients to design *out* the unintentional ventilation (draughts) and design *in* the intentional. Once you have vents and a couple of dMEV fans you can go mad stuffing draughts. Have a look at the Bldg Regs for the relevant cross-sectional area of ventilation you'll need. Goood luck! -
Potton Homes(Kingspan) out of business
Redbeard replied to Post and beam's topic in General Self Build & DIY Discussion
See also -
Strictly no, but I can give a good guess. Apply expanding form tape such as Compriband in the expansion gap. I have not come across the term 'penny-rolled' before, but assuming they use a 'standard EPDM 'detail' roller (which seems to have a min 40mm diameter) I would suggest just roll first across then up to the abutment.
- 1 reply
-
- 1
-
-
Is it compliant with the Code for Sustainable Hens?