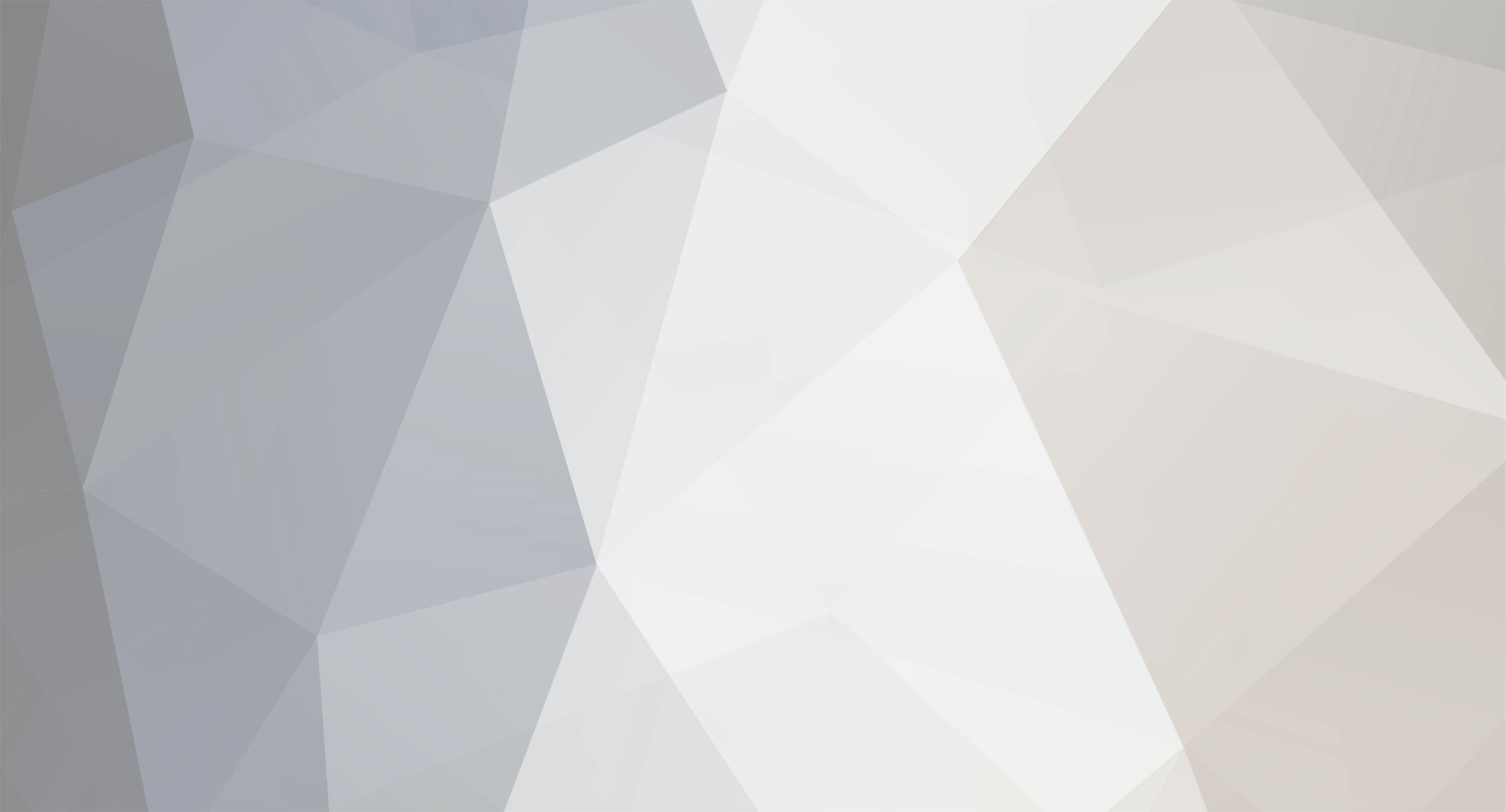
LA3222
Members-
Posts
1185 -
Joined
-
Last visited
-
Days Won
11
Everything posted by LA3222
-
It may well be small beer but that is one project. The true cost of net zero will not be known until decades after the fact when people start to dig into the weeds. When has a government project ever come in on time or within budget. There is also the cost to industry, knock effect to jobs and so on. There are too many second, third and fourth order effects to this net zero drive to quantify the true cost. At the minute the zealots are in charge and driving the car so no one is looking closely and joining dots. Someone said leading by example. Yep. That works. When cash money is involved those taking a moral stance can sit there and pat themselves on the back whilst doing so all the while those making money are happy to let you do so. Carbon taxes. Another way to cripple UK industry when we already have amongst the highest energy prices in the world. The country is a mess and putting net zero on a pedestal is making it worse. Fix the foundations and then do what you can. There is little point in watching the house burn down whilst pontificating on the global stage about how morally superior you are to the rest of the world because we are saving the environment. NHS is fundamentally broken. Criminal and Justice system likewise. Education. Roads. Social Care. I'm not sure I can point to any successes within the UK at the minute.
-
And how much carbon are we going to capture, how much will that cost the UK taxpayer and how much will that reduce the amount of carbon in the atmosphere given that the biggest polluters in the world don't care. The West is on a crusade to hoover the atmosphere whilst our neighbours keep spewing ever more crap into. Absolutely pointless and crippling to the country. Population of UK is about 1% of the world, our carbon emissions are also about 1%. They are spanking 20 billion on carbon capture to remove 'wet finger in air' between 20 to 30 million tonnes by 2030. In that time we will have emitted 1.7billion tonnes and globally the figure will be around 187 billion tonnes. So we are removing at best 0.01% of the CO2 generated. If anyone can educate a retard like me as to why it makes sense to spank 20billion quid removing 0.01% of global carbon emissions across 5 years then by all means, I'm all ears. Don't suggest it's worth it to develop new technology as even if we can somehow advance the technology by a magnitude of ten it still makes no sense. To advance it by 100 is fantasy land and absolutely none of the country's actually making big carbon emissions will be interested in wasting the kind of cash we are on this rubbish. The big polluters like China are laughing at us. We cripple ourselves pursuing a net zero fantasy all while their emissions shoot up to offset our drop all whilst making an industry and getting rich by suppling all the net zero equipment to us. This whole net zero fantasy will come home to roost in the next five to ten years and then we're snookered.
-
Yeah I heard the sun dimming one, shill PV then turn the lights off with cloud seeding. Absolute jokers.
-
Carbon capture. Now there's a turd if ever I've seen one. How many billions of UK taxpayers money is being pumped into that particular snake oil. When the UK contributes so little to global emissions and we are spending billions on this nonsense whilst education goes down the pan, dentists are rarer than hens teeth, getting a GP appointment is a lottery and don't even bother going to A&E. There are so many more pressing issues in this country affecting our day to day lives which can be improved rather than zealously pursuing a net zero agenda that is financially crippling and makes little difference when the big polluters don't give two sh*ts. I despair for the UK. Not to mention the fact that offshoring all of our industry and importing everything we need seems counter intuitive in the drive to reduce fossil fuel use. Its the same as this 'I've flown on an international flight so I'll pay to plant a couple of trees to offset my emissions"....yeah brill.
-
Not gonna lie, when I saw what had happened in Europe my first thought was the drive to net zero is behind it. Think it was Spain which only a day or so ago had a days power entirely driven by renewable and then this happens. They are blaming the weather....really. 22 degrees in Spain. Sounds like bullshido to me. To be clear, I believe the whole net zero drive to be the biggest con of our lifetime. I do believe in building houses to high standards and the like, but the rest of it..nah and it's too long and complicated to go into the weeds on this. The world is very polarised nowadays and I don't think people really budge from whatever camp they are in, they just get angry instead if their camp is the one not being listened to/making the decision.
-
No, it's a seperate room at the far end of the house. It gets used all the time, even just for normal TV shows - sure I saw the missus watching the apprentice in there the other day!
-
Can only answer Q1, we use our cinema room all the time - it's the main screen, we hardly ever use the lounge.
-
Do you have any y line strainers installed? Xouple of years back I noticed flow was really low, eventually thought to check tge strainer to find it was gunked up - flow improved a lot once I'd cleaned it.
-
messed up a kitchen wall (metro tiles)
LA3222 replied to johnhenstock83's topic in Wall Tiles & Tiling
Pretty sure that powder is for walls and floors. I used powder for all my walls - the difference between the two is how they cure. The powder is by chemical reaction, the paste by drying out. If the tiles are slipping it sounds like the mix is sloppy. I've tiled the ceiling of my steamroom using a powdered adhesive with no issues. -
Ha, I did the exact same this time last year....cost me £1200 (formaplus) to get one of the panes replaced in a four pane window. Luckily, with insurance it only cost me £250. Bloody expensive and I'm paranoid everything I cut the grass now!
-
Can you build a quality home for £1500 per sq M in 2024?
LA3222 replied to ScottishPete's topic in Costing & Estimating
This is pretty much the point I was making. I've been on the forum since pretty much the beginning, I know what Nods background is and his business etc. I saw all the in and outs of his first build and the costs and I have seen this self same question crop up so many times and I think it is really unhelpful when folks just sling a magic number of £850/m2 or whatever out there. Casual new members looking for answers will have no idea what the context of that number is and may naively think they can use that for their cost assumptions. This is a terrible question with lots of variables hidden under the surface and if people want to chick numbers out there, they really should give full disclosure to how that was achieved because not wveryone will be aware of folks background, experience and personal circumstances which feed into how those numbers are achieved. I'm six years in and sitting at around £1250/m2....meaningless to a casual observer as my circumstances, location, Labour effort are not contextualised to allow an understanding of how I am at that figure. -
Can you build a quality home for £1500 per sq M in 2024?
LA3222 replied to ScottishPete's topic in Costing & Estimating
I hate these types of threads.....there is absolutely zero standardised way of quantifying this question. There are far too many variables in how folks achieve a self build and what they include in their costs to enable a like for like comparison. @nod is an absolute outlier and every time this question is raised pipes up about how little he has spent per m2 with no context to how that was achieved. Is land included in your cost there, i expect not, how much have you spent on labour throughout vs how much have you done yourself? There is not much to be saved on materials...shopping around and economies of scale will help but the margains for material cost savings are small compared to the savings which can be made if you eliminate external labour costs and are able to do the work yourself. Labour costs are the killer and individual self build costs per m2 are primarily determined by how much work they can actually do themselves. But it comes at a cost of time. -
Dunno, I didn't ask tbh...they sent me the fixing pullout data sheets which I weren't particularly interested in! Just told what the use was and asked for a recommendation 🤷♂️
-
They need to be screwed, I have a SIP house and I spoke to technical department at Kingspan Tek - they said screw and directed me to ejot for Screws. Spoke to ejot tech department and they sent me tge pullout tests they'd done fir a couple of screw options...think I went with their stainless steel ones in then end - the screws have to be long enough to for the tip to penetrate at least 20mm beyond the back face of the osb iirc.
-
Don't they dry assemble at factory to check everything fits before dispatch? I thought that was standard practice🤷♂️
-
Mortar on indian sandstone slabs
LA3222 replied to xtianaudio's topic in Landscaping, Decking & Patios
In all honesty, it looks a right mess IMHO. I would suggest the slabs will have to be replaced, I can't see how those Mortar stains are going to come off sandstone - not what you want to hear I expect and I may well be wrong. Hopefully some with more experience of sandstone slabs will be along to give their thoughts. -
Get one off FB marketplace...always loads of paslodes on there, no point buying brand new.
-
Fan Coil Units for use with a (cooling) ASHP
LA3222 replied to ProDave's topic in Air Source Heat Pumps (ASHP)
This looks exactly what I need, it will be interesting to see how you get on. I haven't the time to tackle this issue yet, hopefully by next summer! -
I had to get G3 for Build control but to be honest as @TerryE said, these things can explode under certain conditions so I would have had it looked at anyway. Plumber spent 20mins checking it over and charged me £300 for the pleasure - still a big saving overall by doing it all myself. As far as servicing goes, its the PRVs and expansion vessels which need checking - easy enough to do DIY so no need to pay a plumber.
-
Agreed. My ASHP which I installed myself along with the UVC had two bits of 'plumbing' - Flow and Return. That's it, not sure why an MCS bod would need to do that?
-
I installed all mine myself then got spark to wire up. Had to pay a plumber £300 just for the G3 sign off for BC - was at my house all of 30mins checking it over. The beauty if pre plumbed is its a piece of cake...just dot to dot.
-
The sauna has a vent that extracts into the bathroom pretty much next to the mvhr extract, nothing in the steam room - just leave the door open once done and the moisture dissappears in short order with the MVHR on boost. There is a floor drain in there too.
-
I've put both a steam room and sauna into my Build- did them myself and they are easy enough. Steam room is just tanked and tiled all around, sauna is foil lined all around and then clad. They both quite big, I have 3ph so used 3ph 9kW heaters for both - sauna one sits in the sauna, steam one in the loft. Both take about 20mns to get to temp - all in they generally run for about an hour a time and use about 5kW.