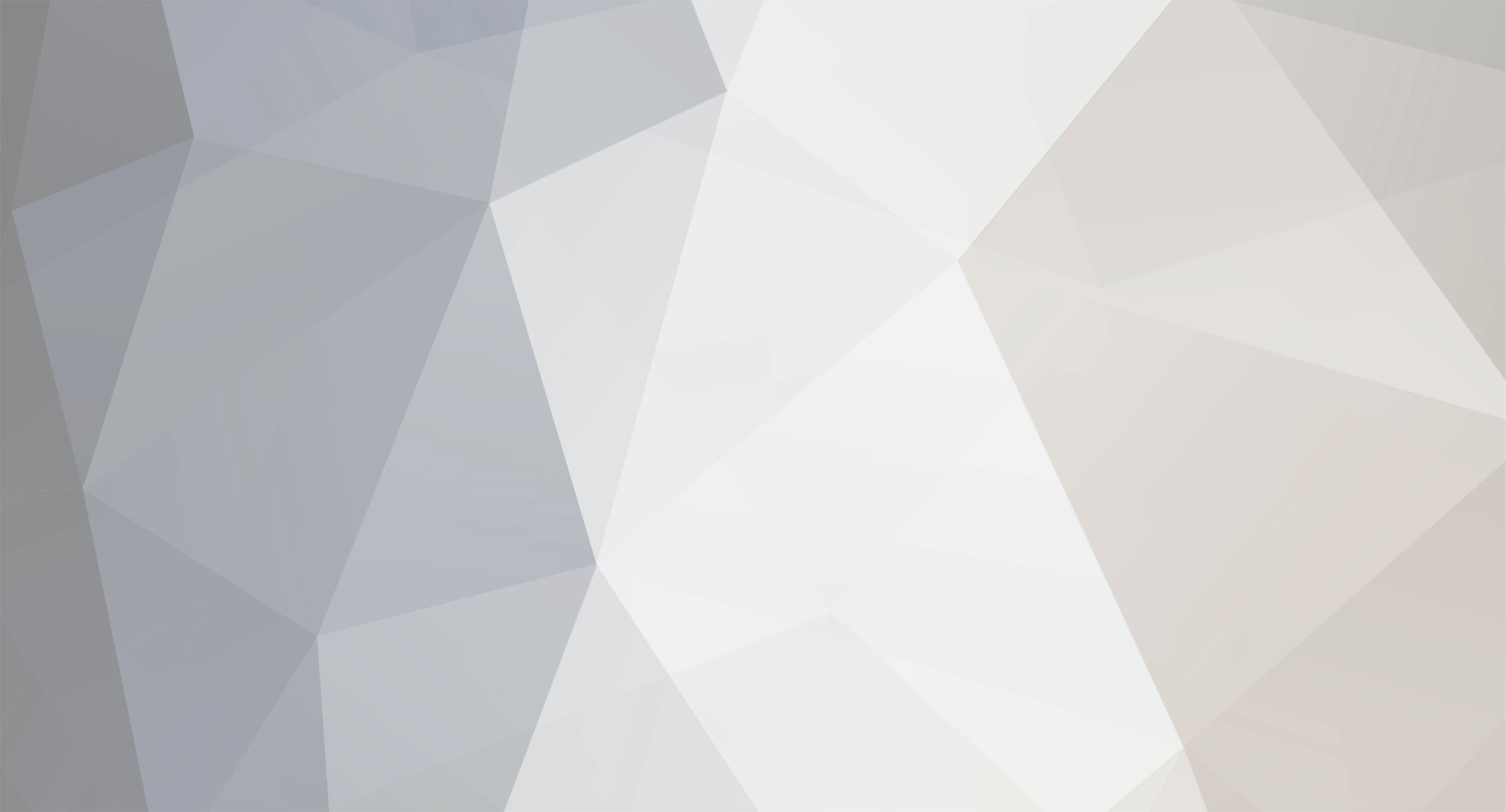
MarkA
Members-
Posts
22 -
Joined
-
Last visited
-
Days Won
1
MarkA last won the day on April 7 2019
MarkA had the most liked content!
Personal Information
-
Location
North Essex
Recent Profile Visitors
The recent visitors block is disabled and is not being shown to other users.
MarkA's Achievements

Member (3/5)
21
Reputation
-
Exciting weekend for us, the scaffolders dismantled all of the scaffolding on the house and garage, finishing at lunchtime yesterday. Our first view of the house as it is (mostly) supposed to look. Interesting downpipe detail at the moment... The groundworkers were back on site yesterday reviewing the long list of external work still to do, including another retaining wall to keep the drive away from the house.
-
Following the example of @Weebles last year who we visited, we would like to invite fellow Buildhubbers who would like to come and see our MBC 140mm frame to get in touch and make arrangements to visit. We are located in North Essex about 8 miles west of Colchester. We briefly met @Dreadnaught and @vivienz when visiting @Weebles and we all agreed that seeing a real project was extremely useful. See photos below of the house from the rear + central section - taken just after MBC had completed frame erection and gone home for Christmas (the rooflight is 2m x 1m, triple glazed and weighs just over 180kg - we had fun getting that in place ?). The photo is a bit deceptive in that the ground does not slope as steeply as it seems, the house is set down in the ground - we had to dig out over 1,500 tonnes of soil due to the constraints those nice planners put on us ? - and there is more to come out once we start landscaping: At the moment we are reaching major milestones every month or so. November 2018 saw the slab poured, December 2018 the frame was erected and (most) windows/doors installed and PV array on roof, January 2019 the slate roof was nearly completed (slating should be finished this week). About half the house has a brick skin and brickwork starts tomorrow (weather permitting) and they are expecting to take about 5/6 weeks (weather permitting – I think I shall be saying that a lot in the coming weeks). The other half is rendered and the rendering team should start preparations within the next couple of weeks. We also have a couple of areas with brick slips, just to keep us on our toes (but that's another story for another day). MBC are due back during the second half of February to install the insulation in the roof and then make the building airtight. All the above means that there is plenty to see in terms of how the house is constructed. We have lots of lessons to share as well. We have contracted with MBC for them to deliver wall & roof u-values of 0.14 W/m2.K (achieved using Knauf Earthwool + PIR for the walls and similar for the roof) and the slab of 0.105 W/m2.K. I also have a belated apology to make to @Dreadnaught for not responding on his previous thread about the 140mm system – we have been distracted by non-build related issues in recent weeks as well as having plenty of build related issues to deal with. @Dreadnaught - see the photo below of the panels in situ (struggled a bit with the light I am afraid)
- 1 reply
-
- 7
-
-
@MikeSharp01, when we looked into it, it seemed that the fan coil units would deliver greater cooling capacity. We have a lot of south facing glazing so are concerned about overheating potential. Planners have been extremely unhelpful to the point of being obstructive when it comes to practical shading solutions.
-
@pdf27We are intending using small fan coil units for cooling upstairs (driven by ASHP in cooling mode). Then have option of doing heating as a backup as well.
-
I demolished your house, but I'm not moving the debris!
MarkA replied to laurenco's topic in Demolition
Should have also said the slab was already broken up and he used the mini digger to load the crusher. It was a small barn that we demolished so probably smaller than your bungalow.- 192 replies
-
- demolition
- cowboys
-
(and 2 more)
Tagged with:
-
I demolished your house, but I'm not moving the debris!
MarkA replied to laurenco's topic in Demolition
We paid £500 for a man, mini digger, mini crusher (and big sledge hammer to break up bigger bits) for 1 days work. We are near the Essex/Suffolk border. He worked solidly all day and created about 30 tonnes of hardcore (which is actually a fairly small pile really). Bit dusty but we are on the edge of a small village so not too problematic. Nowhere near as noisy as I expected, even the neighbours who don't like noise were not bothered (but we are on a main road so people are used to a reasonable amount of traffic noise).- 192 replies
-
- 1
-
-
- demolition
- cowboys
-
(and 2 more)
Tagged with:
-
Site visit? (MBC frame now up)
MarkA replied to Weebles's topic in General Self Build & DIY Discussion
We visited @Weebles yesterday and I wanted to say a big 'thank you' to them for being brave enough to make the offer and give up their valuable time to show various Buildhubbers their MBC frame when they clearly had plenty to do without nosy visitors asking lots of questions. With luck and a fair wind we will be able to do the same soon (but still not sure exactly when - the joys of self building...) We briefly crossed paths with @vivienz and @Dreadnaught and it was good to put faces to their Buildhub names. The amount of help/info (directly and indirectly) that we have gleaned and the sense of community from people on this forum is amazing. Thanks to all. Mark -
Crikey, that sounds like an intense day all round. Our MBC slab pour is not many weeks away and we have been following your journey as though it is our own. I shall add to the 'to do' list sourcing a defibrillator for that day to deal with heart-stopping moments.
-
@PeterW - very good point - I shall add it to the list of variations we are talking to the planners about at the moment.
-
That's all reassuring as this is most likely to be on the neighbours boundary
-
Yes, that all makes sense. I have not been near to either of these pieces of kit while they are in action, so thank you @JSHarris for the feedback. With your point about the ASHP blowing a small gale - does that actually mean it is relatively noisy due to the airflow (versus the motor noise)?
-
I have been reading posts about ASHP issues and the thread below has provoked some thought: Since we at still at the stage where we still have lot of options over where to locate an ASHP plus MVHR system I am wondering if there was any value in positioning the MVHR exhaust duct so that it could blow over the ASHP? From what I have read there may only be a few degrees C above the external temperature in the exhaust stream during the cooler months, but would that be of any value in helping reduce the frequency of defrost cycles that the ASHP goes through? I am assuming that it would be relatively simple to direct the MVHR exhaust away from the ASHP once the ambient temperatures rise, should the ASHP be used for cooling in the summer months (this could be manually done). The energy (combined with the flow rate) from the MVHR exhaust may be insufficient to make any real difference but it seemed worth asking the question since it will be running continuously anyway.
-
Another question. What have other people done when it comes to providing for routes through the fabric of the building to future proof the insertion of additional cabling/pipes etc without compromising the airtightness (or make it tricky to sort out) when the future change takes place? I suppose this is a bit of a chicken and egg question since you don't really know where these future cables/pipes are going to go?
-
All sorts of useful observations here which are already triggering lots more thought on my part, so thank you. @Bitpipe's response is a good reminder that several of these points are dependant on the context you are building in. In our case one side of the building will be next to where the neighbour will be parking their cars, so a low level duct for MVHR in this position will almost definitely suck in exhaust fumes. We also have the benefit of living next door to the site and already know that we are going see large volumes of silver birch and willow seeds and pollen (at certain times of the year we seem to be blanketed in the cotton wool parachutes of willow seeds) and this seems to deliberately target the Velux windows to get into the house. We are pretty confident that our external filters are going to need clearing at least once per year, possibly more. @TerryE - I am particularly keen on avoiding hidden joins. Our existing house is a nightmare when it comes to maintenance, nothing seems to be easily reachable and maintenance tends to involve destruction of some sort to get access. We plan on having a dropped ceiling in one section (ground floor) to give plenty of space for pipe, cables, ducts to run between two gable end sections of the new house. Unfortunately the plant room (well large cupboard really) location is going to mean some bends are likely (so may be joins) so I am thinking of having an access hatch in the ceiling where the bends may be. @SteamyTea - hadn't even considered your points about how to access certain areas on the outside. We have no flexibility on changing the approved design so I will be adding this to my checklist for sure. Standard sizes are important, especially with the passage of time. We currently have a non-standard undersized toilet due to space constraints in the existing house - it was a real pain when the seat needed replacing due to a broken hinge type connector (limited options and expensive and never did quite match). @PeterStarck - flooding... yes, good point (both external and internal flooding). We theoretically don't have a flood risk at all... but... our neighbours had a serious flood through their house about 10 years ago and guess where the water came from? It was run-off from the field opposite which slopes gently down towards our row of houses and the farmer had plowed the field the field in such a way that such a large volume of water was directed into a ditch along the road during a downpour that the ditch was overwhelmed, it then ran across the road and straight through the neighbour's house, leaving them knee deep in water. We were very, very lucky not to be impacted. We have friends whose houses have flood protection by a river and it is very unpleasant when they get flooded - so I will add @PeterStarck's point about the wetroom to my checklist. so at least it is considered. Self cleaning glass on difficult to reach roof lights etc also seems worth considering. I also fall into the school of thought that whatever home automation is felt is necessary needs to be carefully considered (as per another topic I saw recently). This probably falls into the 'designing for inevitable change' topic, but the key is that you need to get access to change things as per @ProDave's point.
-
(Or should that be 'if only I knew then what I know now...'?) One topic that I am keen on is thinking in advance is how elements of the house will be maintained once the build is complete (we only just have planning permission so are early in the process). I am sure lots of people have lessons that we could learn from based on mistakes they have made as well as the thought process that they went through in drawing up their detailed plans. I get the impression that there are some well explored areas and one would hope that architects/technicians will have the experience and/or checklists to methodically work through so that maintenance is considered. However, as a self builder I am sure there are lots of traps we can walk into. Does anyone have any checklists or could they point me at this sort of info if it has been discussed before? As a starter for ten I am thinking about MVHR units and their filters (both within the unit and on the external ducts into the building). Lots of these units seem to be in the roof so the ducts are high up, yet surely the filters are going to need cleaning at least once per year. Where we live we get loads of tree seeds and pollen which will clog up external filters in no time at all. I am not looking forward to the prospects of climbing up tall ladders in increasing old age (or paying someone) just to clean a filter. We are thinking that it makes more sense to have these lower down (but then not too low due to a host of other potential issues this could lead to). What have the rest of you considered (or just got wrong )?