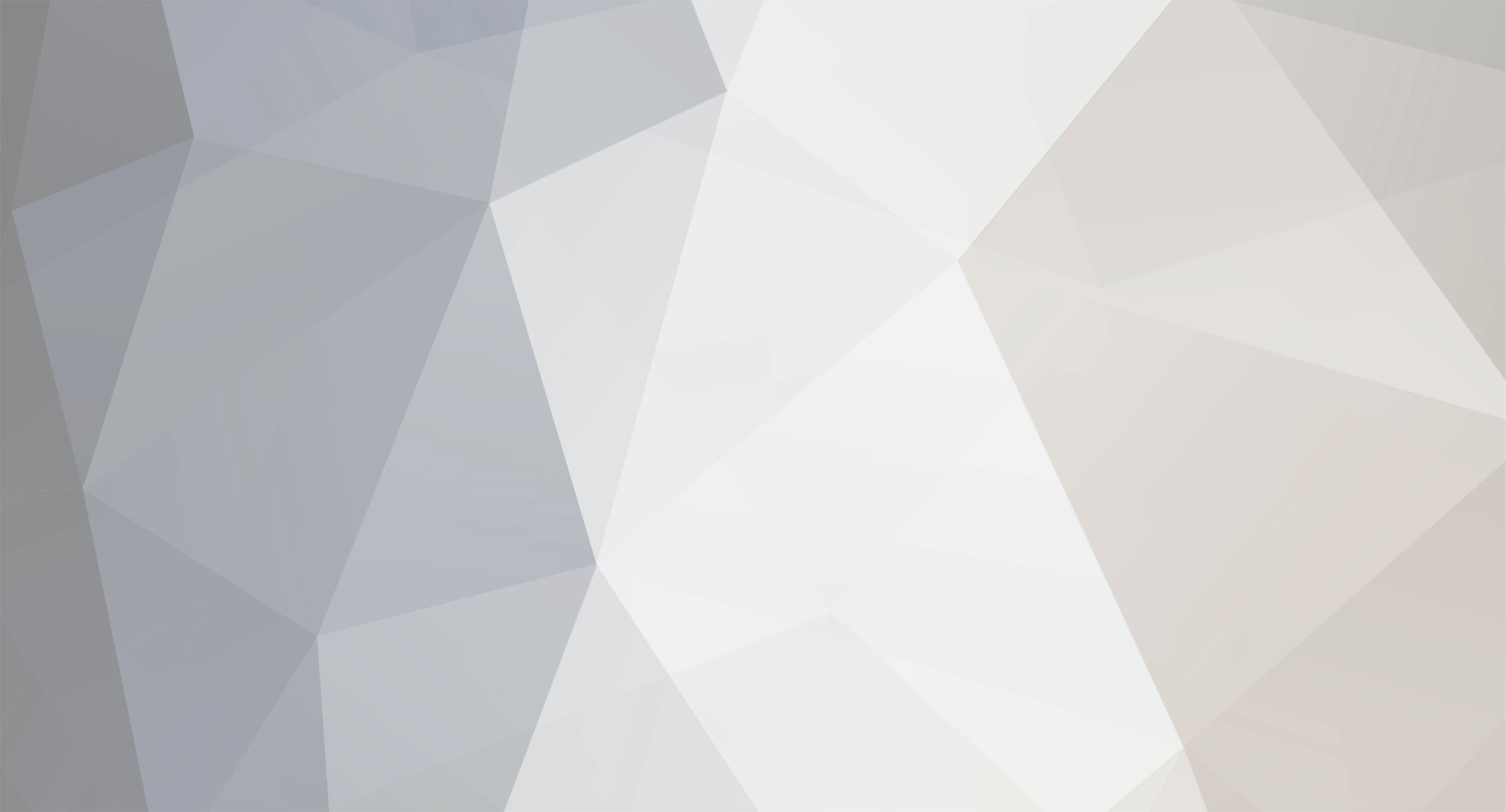
Nick
Members-
Posts
121 -
Joined
-
Last visited
Everything posted by Nick
-
I get that the tape & fill between boards and the band of compound behind them is supposed to be airtight, but what about all the other details that aren't just one board next to the other? Like when a board finishes up against an existing stud wall, or a ceiling, or a window, or a doorway, e.t.c. The way all the IWI guidelines tell it, air / vapour is just going to take that route to get to the masonry and create air leakage & condensation. The only solution I can think of (the one we use in the glazing industry) is to run a membrane to continue the layer and overlap it onto the next airtight element and terminate it mechanically or with adhesive. I can see a way to do that with separate PIR boards as there is an nice foil face to stick things to, but how are you supposed to do it with insulated plasterboard where you can't access the VCL?
-
By using separate boards? I originally planned it with insulated plasterboards and would make life easier to use them, but there were just too many places that I couldn't find a way to seal properly. It's an old building where there needs to be a continuous VCL to protect the brickwork. With a pre-made board where the VCL is glued between the insulation and the plasterboard, I have nothing to run airtight membranes from windows or perimeter details into - no way to overlap them / glue them / clamp them, e.t.c. How do you go about detailing these sorts of areas if using insulated plasterboard?
-
I've read of a few people using separate PIR boards and plasterboard sheets for internal wall insulation instead of buying the pre-bonded stuff. That's exactly what I'm planning to do for my retrofit as it will make the airtightness detailing a lot more solid. I'm not clear on what to use to stick the plasterboard to the foil-face of the PIR though. I'm planning to use adhesive foam to stick the insulation boards to the masonry so using it again to stick the plasterboard on would make sense, but I'm not sure how much of a gap it will leave - I have a fiddly detail to line the plasterboard edges up with the windows and anything more than a couple of mm gap will be an issue. Alternatively, acrylic adhesive will stick to both materials according to literature, so I'm wondering if a grid of small blobs on the plasterboard be a workable idea? The only thing thinner would be contact adhesive (or nothing and just bang a load of mechanical fixings in), but I have my doubts the insulation boards will be flat enough for either of those to work. Can anyone who's done it before advise what worked for them?
-
Sounds like the seal in the unit has broken down. Yes I would say this is a valid reason to ask for a replacement and you should be covered as long as the glass is under warranty. Would expect this to be at least a few years but all depends on the supplier you used and their Ts & Cs
-
Cheers. The funny thing is the inner wall really doesn't seem that bad. Will have a much more detailed look next time I'm there, but my main concern at the moment is that the brickwork will stay soaked on the outside with all the earth against it and develop more issues over time.
-
Thanks, looks good! Will it actually keep the external wall dry in any way though, or just remove the water once it's already ingressed into the basement?
-
Modern thermal breaks are mostly polyamide. In high spec windows they are supplemented with lots of additional foam insulation stuck to / around them to improve u-values and minimise room for convection currents. The depth of the polyamide section definitely does matter. To get better results from aluminium windows you need to increase the polyamide depth. You can get aluminium frames that give you far superior u-values to Rationel, but they will be 100mm+ depth (most of which is thermal break) and therefore cost a lot more. Nothing wrong with the windows in the OP. Good system but they are 58mm depth and mainly designed for replacement of existing windows so not high-spec. Your window sizes are probably on the small side if you're getting those u-values. The psi value shown on the calculation also indicates that the supplier is using solid aluminium spacer bars in the glazed units (or doesn't know how to programme their software). In 2020 you should be getting a warm / thermally improved spacer bar in everything.
-
Thanks for the replies and resources. Next time I'm there I'll take some more detailed photos and scrape at a few bits to see what exactly we're dealing with. Have been reading up on solutions and in this case there's no real access to most of the basement walls from outside. Seems pointless tanking from inside - would still leave the brickwork wet and it's not habitable space. No real damp showing through inside anyway. Anything else that can be done given the lack of access or is this just something you have to live with and hope it doesn't become a serious problem?
-
Thanks both. Couple of photos that I happened to grab below. The run marks where the paint has washed off show the difference between sheltered and exposed areas I was talking about. Hard to tell under the paint but pointing condition looks reasonable-ish to me? No similar buildings nearby unfortunately - all newer construction. Thinking about it now and looking back at photos, the window openings are keeping the brickwork directly above them isolated from the ground so as well as rain, it makes sense that they'd also be better protected from damp as you've suggested. Assuming it is damp (or damp but with rainwater making it worse), is there anything that can be done? Main concern is obviously if we have to insulate the walls internally, it will only make moisture issues with the brickwork worse. Can get spalled bricks changed and the wall repointed if need be, but would I be looking at improving the drainage away from the building and/or tanking the basement walls to sort it out longer term?
-
I know little to nothing about brickwork so would appreciate if someone could tell me if I'm miles off with this thinking. Currently looking at a 225mm solid brick built (uninsulated) building with three floors plus basement. Would need to insulate it down the line so wanting to make sure the construction is sound. The original brickwork has been painted over - overall the condition doesn't look too bad considering the age. At basement level there are a few spalled bricks and a lot of efflorescence, but this is only in the vertical runs of brick where there are no windows or stone cills (i.e. the sections where rainwater is running down all four floors uninterrupted and soaking the basement brick from the outside). The areas of brick under the stone cills at basement level look lovely and dry in all cases, so my thinking is that if I were to get some kind of drip edge profile installed in the mortar bed on every floor at cill level and screw it to the underside of the stone cills for support , it would shed rainwater away from the brickwork on the floor below and stop it running down onto the basement where it is creating issues. Other than the fact it probably won't look the best, is this a done thing / practical in any way? If not, are there better solutions out there? Am wary of trying to waterproof the brick from the outside without first doing everything I can to keep water away from it.
-
Sorry, you're a bit far outside the area I work in so can't really recommend local suppliers, but generally I would say that even in non post-lockdown madness times it would be a struggle getting an aluminium panel door in 4 weeks - they are literally made to measure. Composite door should be do-able if you call around suppliers as they make them from standard-sized slabs and just rip them down to suit before edging & finishing. Can still get them in 2 weeks down in the South-East.
-
What exactly do you need - type of product, size of opening, where in the country, e.t.c ?
-
Tony, When you say nylon ties, are you talking about a manufactured product with test data? Any chance you could post the name as searches so far aren't coming up with much.
-
Perfectionism, finishing quality and builders
Nick replied to ReX's topic in General Self Build & DIY Discussion
Possibly I'm younger than you so my memory doesn't go back as far but when I first started in my industry, it felt like the majority of tradesmen were getting by with few/no qualifications, some surface-level knowledge and were just about able to do a good enough job to get paid. A small percentage were utter chancers and did terrible work, declared bankruptcy and resurfaced with a new company name every couple of years. An even smaller percentage really knew their stuff and were always in demand although weren't necessarily more expensive than the rest. Haven't really seen those proportions change to be honest. Marketing yourself online has definitely become a big thing. The best chaps don't seem to need it and are kept busy by existing contacts and referrals only. That's why the only way to get a good person seems to be to find someone in the trade who you trust and ask them. Sadly the internet is probably the worst place to look. -
Self-Build first steps – advice sought
Nick replied to bpk101's topic in General Self Build & DIY Discussion
I've asked and can't get anything less than 4% with a 50% LTV ratio and a literal 100% perfect credit rating. That's why I'm querying it... -
Self-Build first steps – advice sought
Nick replied to bpk101's topic in General Self Build & DIY Discussion
Would that apply to something like a self-build mortgage though? -
Perfectionism, finishing quality and builders
Nick replied to ReX's topic in General Self Build & DIY Discussion
I see your point, but all that "professional" really means is that someone is getting paid to do it. Doesn't necessarily mean they're any good at it or that they will be better than you doing it yourself, you're just paying for the convenience of someone else taking care of it. I can make a nicer omelette than the cafe round the corner or a nicer burger than McDonalds but I wouldn't necessarily do it if I worked there myself. -
Perfectionism, finishing quality and builders
Nick replied to ReX's topic in General Self Build & DIY Discussion
It's definitely tricky... When it comes to what's acceptable, that varies from person-to-person but as a minimum you can expect them to work to the relevant British standard and the manufacturer's guidelines. For tiling a floor for example, there will be a BS specifying the tolerances they should be fitted to, and the tile manufacturer will have their own on top of that. If the tiler has met both of those, I would say they're within their rights to consider their job done and expect payment. If not, then unfortunately it's you as the buyer who's stuck with the job of checking it and pulling them up on it and getting it resolved. I'm with you in the sense that there is pretty much no amount of money you can spend that will guarantee you a result that would please a perfectionist. Everything is manufactured to tolerances and built to tolerances. My company makes aluminium glazing products on a large scale and there are rules about what size scratches in the powder coating are acceptable and how far away you have to stand from the glass to identify a defect. When you buy a chocolate bar, there are rules about how many insect parts can be inside it before it is rejected. Making things with absolutely no defects is just not viable. -
Perfectionism, finishing quality and builders
Nick replied to ReX's topic in General Self Build & DIY Discussion
True. The other side of that coin though is that people generally go for the lowest price bid and THEN start talking about quality as an afterthought. Certainly like that in the trade. When I do painting, plumbing or whatever, I do it to my standard but I'm sure it takes me 2-3x longer than a professional. I wouldn't consider it reasonable to expect a total stranger to work to that level unless I've specifically asked them to and they understand that is what they're being hired for. Unless you've discussed with the builder exactly what you want from the get-go, all you can really expect is that they will do a standard, acceptable job. -
Perfectionism, finishing quality and builders
Nick replied to ReX's topic in General Self Build & DIY Discussion
Well "perfectly" level is open to interpretation unless you take it literally in which case it is impossible. Level to +/- 5mm (for example) can at least be measured. Chipping existing tiles I'd expect to be taken care of by you having taken photos of the starting condition. Unless a builder had specifically said "we can't guarantee we won't damage "X" while doing these works", they should take responsibility for rectifying that. When it comes to doing things fundamentally wrong , accidents, mistakes - you're right. Nothing you can do about this other than make sure they are spotted and rectified. That's why there are project managers, defects periods, retention and the like. On multi-million pound building sites there are whole departments and huge amounts of money dedicated to sorting out mistakes and sub-standard workmanship because they fundamentally can't be avoided. The safest way is to do it yourself. The next safest is to watch the person doing it like a hawk. The next safest is to hire someone you trust to watch the person doing it like a hawk. And so on it goes until you have the structure of a large main contractor. Half the people are there to check the work of the other half. -
Perfectionism, finishing quality and builders
Nick replied to ReX's topic in General Self Build & DIY Discussion
Show them samples or give them an exact specification of what you want before they start the job including reference photos. Agree it in writing. At that point they will either decide the job isn't worth it and back out or, agree they can deliver what you want (and possibly increase their charge accordingly). If you haven't agreed what you want in advance, there is no reason to expect they will work to your standards. They will work to a combination of what the market expects and what they are required to do by building regs, British standards, regulatory bodies, e.t.c. Getting a personal recommendation where you can see their previous work is always a good start but definitely not a guarantee - busy tradespeople hire new labourers fairly often and they get busy spells where they overcommit and have to rush through jobs or subcontract them out. People who you can trust to do a job well unattended are very rare in this life... -
Any Low Modulus Neutral-Cure (LMN) silicone will do. We use Silirub 2, it sticketh closer than a brother.
-
Stuff we use grabs within a few minutes. I would say 24h to cure to the point where it won't move under a gentle bit of local pressure like floor movement. If you have access, just throw a few self tapping screws in after the silicone. Try to get them to only pierce the first wall of the door profile so they don't stick out visibly into the threshold.
-
LMN Silicone will do the job just fine as long as you run a bead across the whole length. Also has some flexibility so won't break away easily when the two aluminium sections expand/contract at different rates.
-
https://www.billbutterswindows.co.uk/images/downloads/Members_Glazing_Manual_March_2015.pdf GGF Glazing Manual - 1.1.3 In case you / anyone is interested.