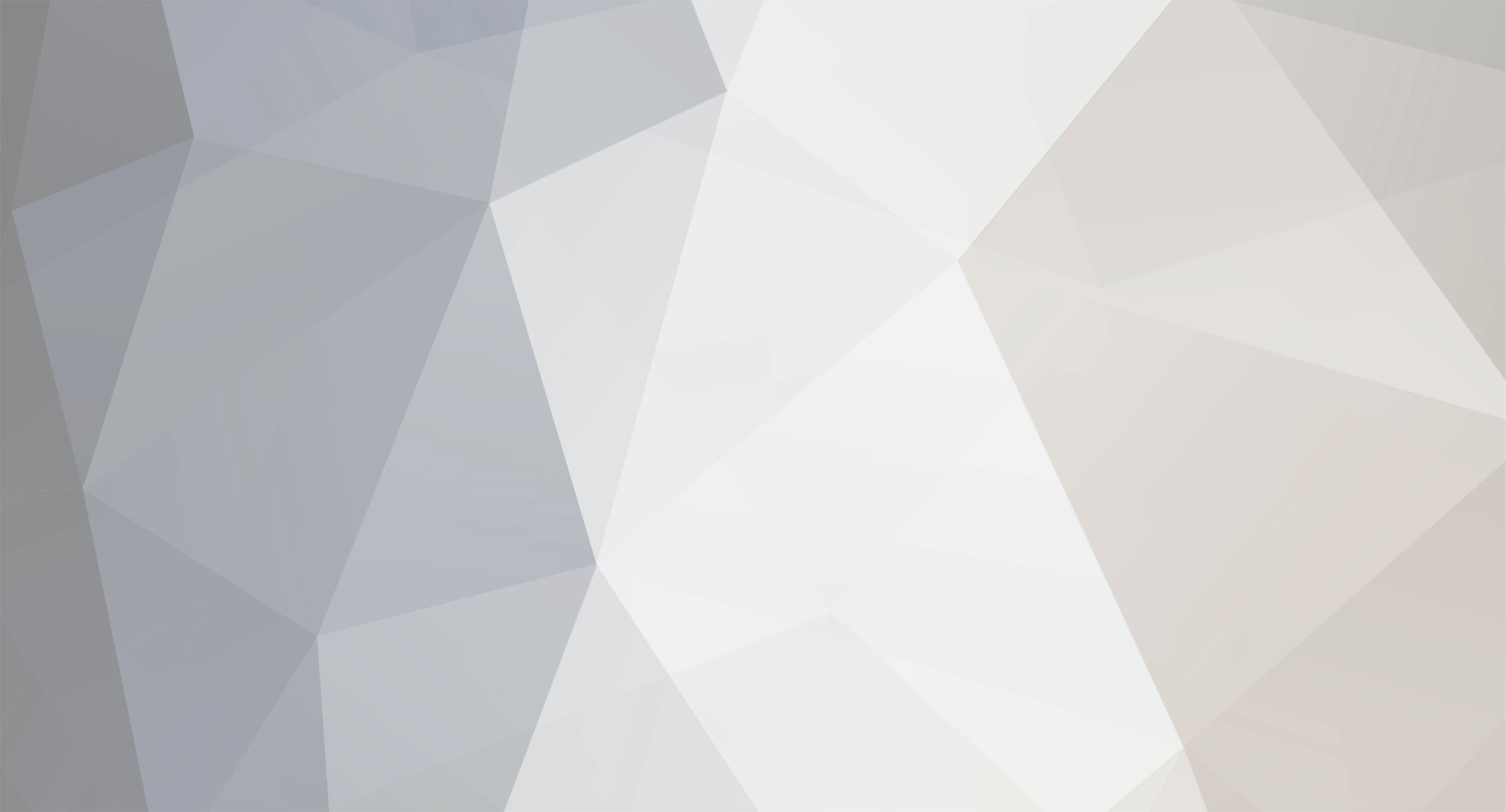
ReX
Members-
Posts
27 -
Joined
-
Last visited
Personal Information
-
Location
London
Recent Profile Visitors
The recent visitors block is disabled and is not being shown to other users.
ReX's Achievements

Member (3/5)
3
Reputation
-
Perfectionism, finishing quality and builders
ReX replied to ReX's topic in General Self Build & DIY Discussion
That's exactly what I thought when I did some projects on my own. But it is not always the case: in many occasions I have seen them not using the right technique, the right tool or even basic common sense. For repetitive builds (e.g. equally spaced wooden battens wall cladding, drawers, stair treads, risers, stringers) I always make templates. It takes a little bit of time but then you proceed fast and have exact consistent measurements. In another case a bricklayer was raising a party wall in the garden. The drawings stated the wall was supposed to be 180m high, resulting in 100cm lower than the existing kitchen extension roof level (I don't remember the exact measures TBH). Well, the guy used as reference the indoor floor level, so the wall built was 20cm lower than the kitchen extension, 80cm higher than it should have been. And the 100cm drop from kitchen extension level was on the drawings. His justification was that he couldn't use the garden grass level as reference, so he assumed the best way was to use the kitchen floor level. He didn't think about using the other measure. I have almost never found a professional (that does this for living) that can do a better job than I could do on my own. Even if I go for "premium" recommended people. Of course there were few exclusion of very good, exceptional people. If you think about it, it is depressing: it is like going to a restaurant (not a fast food) knowing you could have a better meal at home, so only for the convenience of not cooking. Surely it is my luck plus the fact I actually enjoy doing stuff on my own. It seems that the builders I've used and seen in action (also the recommended and friendly ones) were doing their jobs just because they didn't find anything better. I do the same but unfortunately they don't always listen or have even the knowledge to amend (see comment from Visti below). The thing about the instruction manual & talking them through the process makes me smile: I did exactly the same with a carpenter and he was clearly annoyed and surprised a DIYer would attempt to explain him things about his trade. At the end of the first day I noticed he completely ignored what I told him. This was the end of it, I decided to let him go and had to redo the whole thing my own. It is difficult to generalise from a personal experience, but I have seen the same. Also because the local building standards are higher than here, so they are used to more demanding customers. -
Perfectionism, finishing quality and builders
ReX replied to ReX's topic in General Self Build & DIY Discussion
I am in a similar situation, I have had a very positive experience in the past, but recently (in the new house) I was really disappointed with few builders. I try to do everything on my own but there are some large jobs I can't do and the time is also the other issue. Thankfully really few things are left do be done now. I have learnt few things from this guy: https://www.youtube.com/channel/UCzqh_8hImIc9fhvUu0oVC8w In my opinion, the quality of his jobs and the passion in doing them (including explaining mistakes, etc.) is impressive. I would love to hire him but he is based in the US :). He doesn't cut any corner and he takes the time necessary to do things properly. -
Perfectionism, finishing quality and builders
ReX replied to ReX's topic in General Self Build & DIY Discussion
I think this is one of the main problems. But actually Nick is right, with very few exceptions I have always struggled to find professionals that could do better than my DIY attempts. Surely faster but almost never better. I reached the conclusion I am just unlucky in researches. -
Perfectionism, finishing quality and builders
ReX replied to ReX's topic in General Self Build & DIY Discussion
Fully agreed. I have seen many expensive houses with incredibly cheap finishes, but apparently many people don't care. This is true, but I didn't hire cheap labour, but people that work also on multi-milion houses. Good point but it shouldn't be a justification, especially in a sector that lives also of recommendations and reviews. -
Perfectionism, finishing quality and builders
ReX replied to ReX's topic in General Self Build & DIY Discussion
You are right - I rushed my reply. Indeed the contract stated that the tiles would hav been installed with the same tolerance, accuracy and gaps of the existing floor (that was perfect, the only tile slightly not leveled is not even 1 mm above the next one). We are talking about joining the floors of two rooms, they had to remove the tiles that were cut (next to the wall that was removed). In doing so (using the wrong technique) they chipped existing tiles that were not supposed to be removed. This tiling drama was sorted by another tiler that had to remove everything (new tiles and existing chipped tiles) and redo the job. I am not familiar with all this, so very interesting - thanks for sharing. I have to say that when I saw a friend of mine house being built in Switzerland, the building approach was very different. Everything moved slowly compared to here but each trader was responsible for the build and quality of their own part. The only person with an oversight of the site (coming from time to time) was the architect that did the drawings. Indeed I feel like a hawk and I don't like it (it is annoying for me and the person that is doing the job). I try to do as much as I can, but in some cases you need manpower and time. Makes sense, but in my case I am talking about stuff that can be done properly with some common sense (no external dependency). I was thinking about this when I did the staircase, experimenting my own design. It took me so much time (including building a prototype) that it wouldn't be sustainable (or economically viable) to for a client. But the issues I am talking about in this post are way more basic, hence the frustration. -
Perfectionism, finishing quality and builders
ReX replied to ReX's topic in General Self Build & DIY Discussion
Fair suggestion, but - to give you an example - I wouldn't expect to write on a contract: "the floor tiles should be perfectly leveled, the 3mm gap should be consistent (not only when you feel it) and you shouldn't chip the existing tiles". I would expect this to be by default the normal outcome of extending an existing tiled floor. Or to give another example, during the installation of a steel frame box (to replace a load bering wall) I found by chance that the builders had inverted the lower beam and the upper beam. This happened just because the beams drawings were left on the floor and looking at it for a second it was clear that the lower beam had additional steel to sustain the weight of the side posts. Thankfully they hadn't yet removed yet the acros and reinstalling it properly was quick. How can you possibly prevent these issues with a contract? This was the root cause for at least two jobs, in one extreme case every day new people were sent to do the job and they had no idea about what we had discussed earlier. In another case I hired main contractor / PM (not sure how to call it) to look after the job and the builders but he was on the site 20% of the time, so he wasn't really checking anything (he had 3 jobs in parallel). It seems then that I am not alone. -
How do you deal with builders and specialists that don't deliver the quality you expect? I have always used recommended builders and contractors, that have worked on projects and houses much larger (and more expensive) than mine, but unfortunately I have never been happy with their work. Most of the times I had to step in during the job and ask, suggest (or even do myself to show how it should be done) what I was expecting from them. I am conscious that I am very demanding and perfectionist, but it is disappointing to see how little care and precision is delivered if the customer is not there to chase them. Eventually I reached the conclusion that it is better for me to do stuff on my own (tiling, plastering but also plumbing, electricity, bespoke staircase, bespoke furniture - these are few of the examples) than let someone else do the job, keep an eye on the job and then end up fixing or correcting the errors (if possible). Unfortunately I don't have the time neither the energy to do large jobs on my own, so I am now back again with a builder that is doing stuff more poorly than I could do on my own. Is there an etiquette to deal with these situations? I don't want to be rude toward the builder (that is very nice and friendly) but knowing myself I will be bothered to see a finished product not as good as I would like.
-
Very interested in looking at the result. Is it doable also with redwood? By the way, between redwood and cedar, which one would last longer for fencing?
-
So, the timber included in the quote is this redwood. I have seen it installed at our neighbors and it looks quite nice. But after 6 months it is difficult to judge how long it will last. So far the color is still as new. Not sure if it has to be stained to avoid color fading or the pressure treatment makes it unnecessary. An alternative that will cost about 4.9 per meter is this one with composite battens. Has anyone experience with composite fences?
-
Was the cedar untreated? Did it stabilise as in this picture or it changed? By the way I really enjoyed your blog - very informative and cool house! How often does it need to be stained? Okay, so it seem oak is more durable. Where is redwood in the chart? Which wood would be classified as very durable?
-
Hi, For the new bespoke fences, the landscaper I want to use suggests to use oak but many websites talk about Siberian larch What are the main differences? I am looking for a long lasting solution, requiring reduced maintenance and that doesn't fade or become grey / silver. Thanks
-
Digging and swapping soil for sand - work estimate
ReX replied to ReX's topic in Landscaping, Decking & Patios
Thanks, very informative and you make it seems so simple :). Unfortunately it seems to me that it requires to carry trough the house a lot of heavy material, that I would like to avoid. An alternative I was considering is self install ground screws: https://www.groundscrewcentre.co.uk/products.asp?page=calculator&structuretype=Garden Office https://www.ukhelix.com/product/eco-diy-manual-install-screw-piles/ And then fix the timber base or the SIPs panels on top. I don't have any experience with these screws so I wonder if they are really so easy to install and if they last as long as a classic concrete base. I guess the gap issue will be also with the ground screws solution above. I'll have to look carefully if we have any perennials (not an expert). Would it be okay to do another round of weedkiller and then after 2 weeks roll the turf? Do I need to prepare the soil for the turf? I have started removing the last layer of slabs, there is still some more sand (see picture). A very thin layer that is mixed with the soil (it is almost impossible to remove the sand without digging out also some soil). Do I need to remove it before installing the turf? -
Digging and swapping soil for sand - work estimate
ReX replied to ReX's topic in Landscaping, Decking & Patios
Resolva 24h. They die but then then come back. -
Digging and swapping soil for sand - work estimate
ReX replied to ReX's topic in Landscaping, Decking & Patios
I plan to have a more modern look :). To add more colour: my original plan (now under discussion because it will take to much effort) was to buy cladding panels from Rockpanel (2440 * 1220) and cut them in stripes of variable height (between 5-10 cm), in the shape of "waves" that I would then fix against the old post, creating a sort of horizontal random stripes look. The space between each stripe should be about 2cm. The wave look and the random finish was intended also to hide the fact that the original fences are not exactly in line. To cut so many panels in some many pieces I intended to buy this CNC machine and do the design of the stripes in CAD: https://www.maslowcnc.com/ -
Digging and swapping soil for sand - work estimate
ReX replied to ReX's topic in Landscaping, Decking & Patios
To my surprise, we managed to lift and move all the sand from the green area to the pink area, in about 4 hours. It wasn't just sand but also some solid concrete, but while it took time to break it, it was also easier to pick those large pieces (compared to the other find sand). The old tiles that were buried under the sand are now exposed, I need to lift them and fill with the soil from the former flowerbed in the blue area. I lifted some of them and this time underneath the tiles there should be just soil, no more sand or concrete. I'll leave the path as it is and lay on top the new tiles. I have two options on the table now: SIP kit or "lightweight metal C stud" kit. With SIPs the floor panels could sit directly on top of ground screws or concrete. If I get the lightweight metal frame, I will need to build my own base (it is not provided). Any suggestion? Quadrabase is ultraexpensive and I would like to avoid concrete. I am not sure I understand: could you explain it once again? Any suggestion on how to get rid of the weed? I keep killing it with weedkiller but it comes back after heavy rain. Once killed (again), if I roll the turf over, will the weed continue to grow trough the grass? If so, how do I kill it without killing the grass as well?