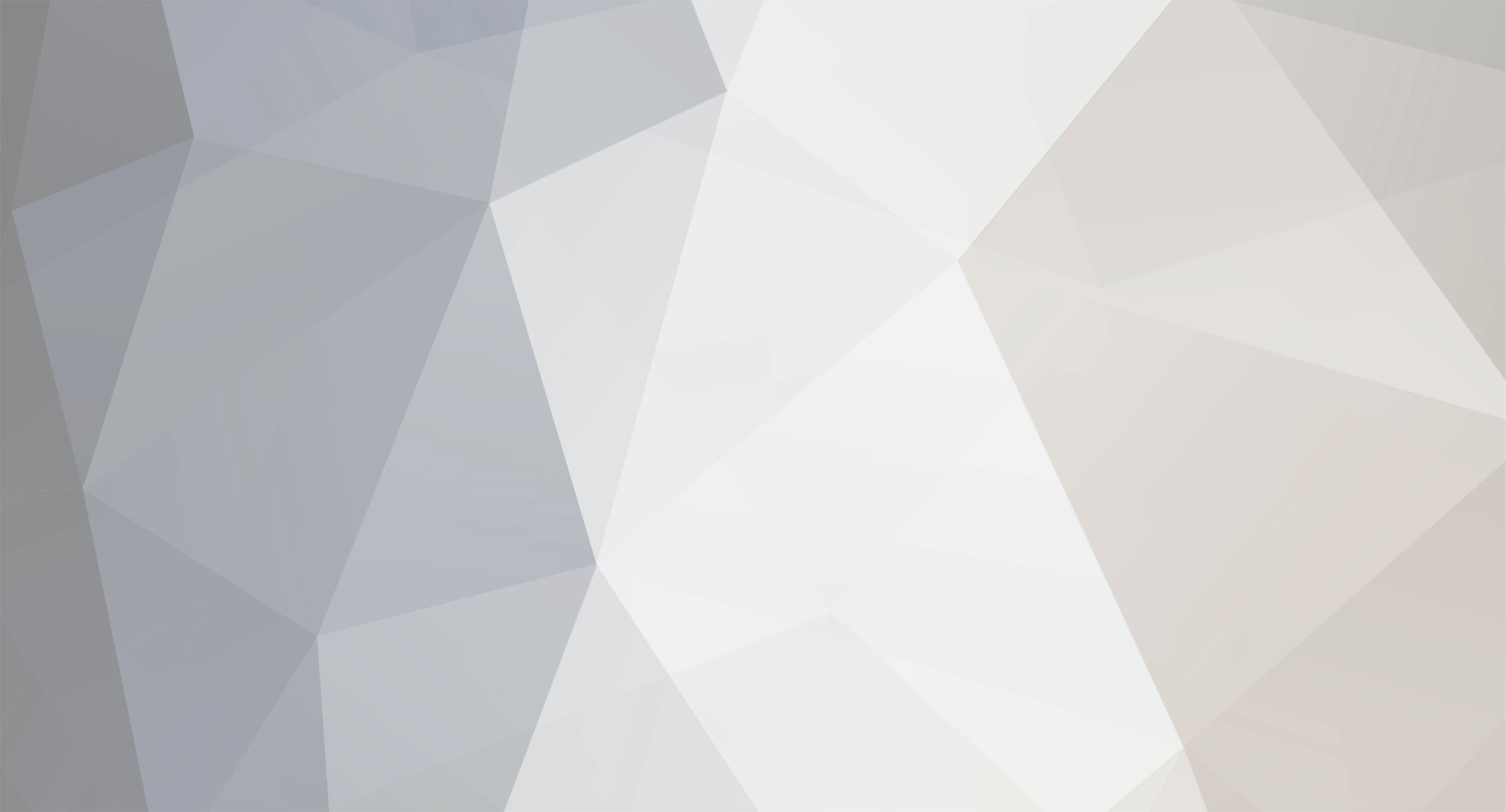
gavztheouch
Members-
Posts
239 -
Joined
-
Last visited
-
Days Won
2
Everything posted by gavztheouch
-
Hi I’m thinking about buying a roof rack to carry 4.8m timber on my van roof. It’s a standard van length (Peugeot expert) i think I need a full rack as the mounting points on my van are quite close together so a full rack will give extra support in the length. I think the rack is 2.6m long so I will have 2.2m of overhang to split between front and back somehow. The first job is to pickup some cladding battens which are 42mm by 42mm, they are 100 miles away and I will need to go on the motorway/dual carriage. Is it a bad idea to carry loads like 20 or 30 battons on a roof rack long distance. I have tried searching for pictures or folk discussing this online but I don’t seem to see anything. If they came off during transport it would be extremely dangerous
-
Hi I have some external doors to fit. My frame is 245mm studs with 60mm external wood fibre and then rainscreen cladding. My foundation is insulated raft and the concrete in the raft is the finished floor. I’m going to use flashing tape, it’s pro clima extoseal to flash the threshold. The door will sit on top of this flashing on packers. There will be a gap I was planning to fill. The architect suggested packing with structural grout but I was thinking something like sikaflex structural glue/silcone would be better. Lay it down on a bed of the stuff, and hope once it’s sets it should be solid underfoot. How do you seal your external doors to the weather under the door frame?
-
Cladding battens, Pressure treated or not
gavztheouch replied to gavztheouch's topic in General Joinery
Thanks everyone a few good options here. Looks like it’s a sensible option to use stainless steel. just need to decide if I stick with the pressure treated spruce or ‘upgrade’ to thermopine. In theory the thermopine might be longer lasting but I guess it’s hard to prove without testing it myself for 50 years, which I can’t. My biggest worry was the screws rusting, I guess stainless helps there. @Duncan62 did you have any issues with the stainless screws snapping. im hoping for 50 years out of the larch cladding which I think is possible. Some of our shed doors at the farm are wood and still in good condition. Need to decide if pressure treated spruce can match the 50 year lifespan -
Anyone else get nervous when it’s windy like this. My house is not up to full strength and every time the wind blows like today i think of all the things getting stressed by the force of the wind. I have a very exposed site and a lightweight construction which doesn’t help to calm the nerves.
-
Fire barriers required behind cladding.
gavztheouch replied to Big Jimbo's topic in General Construction Issues
Thanks Mark, I spoke to my warrant officer and he said I wouldn’t need fire battens as just like you said he would not consider it a cavity. My architect is arguing that he is wrong and I will need them. -
Cladding battens, Pressure treated or not
gavztheouch replied to gavztheouch's topic in General Joinery
Thanks @Duncan62 Can I ask what brand/ type you went for. -
Hi I have some 47x50mm pressure treated battens (The green coated ones) My screws to attach the battens are 180mm heco-topix that hold on 60mm insulation too. They have a standard galvanised finish. Im worried that they won't last the hopefully life of the cladding about 50 years. apparently the copper in the pressure treatment will cause the screw to rust fast. A solution would be to use stainless screws (very expensive @ 180mm) or change to a non copper based treatment. batten. I have struggled to find decent battens at 50x50mm, most batten are made from crap wood. I guess I could have them milled from something naturally durable like larch but I assume there is a solution already out there or I am overthinking things again
-
Battening for Vertical Timber Cladding - Tips, Hints and FAQs
gavztheouch replied to Thorfun's topic in General Joinery
Were they the green pressure treated variety? I have pressure treated but I noticed my screws are only mildly galvanised so they may not last with the copper in the treatment eating the zinc. Stainless screws would be good but I have external insulation so that would be a large expensive screw in stainless. Even the blue and red 25mm roofing battens are pressure treated with a copper based treatment which I think will shorten the life of the screws and nails. -
Fire barriers required behind cladding.
gavztheouch replied to Big Jimbo's topic in General Construction Issues
My thoughts were a cavity barrier won’t stop the supply of air but they might physically stop the movement of a flame progressing upwards. However as my boards are not very deep it would only be a 90mm jump for the fire to bypass the cavity barrier and jump into the next cavity. one positive I can think of with open rain screen is there is less of a chimney effect cause it’s not closed off like a chimney. Did they not try and make you use a closed cladding system? -
Fire barriers required behind cladding.
gavztheouch replied to Big Jimbo's topic in General Construction Issues
Hi I’m in Scotland and would love to not put horizontal cavity barriers behind my open rain screen. Mainly because wind driven rain will get past the cladding and then I have the worry of horizontal cavity barriers (held on with screws) blocking the water escaping easily and potentially seeping in behind the cavity barrier fixings. And then there is added cost and complexity. Probably 5k in materials and time. what was your main argument? -
Insulated threshold detail for insulated rafts
gavztheouch replied to WannabeBob's topic in General Construction Issues
Hi nick, my door is also set back like yours. The sill does not cover the remaining part of the isoquick upstand. In a bit worried about people standing on the edge of the polystyrene. How did you finish you sill detail at the doors? -
Anyone else have a similar wall build up to me and how did you weather proof your windows before cladding. Here is a mock up of one of my windows. I have insulation pushed into the reveals, the outer aluminium face is cut back to allow 35mm of external wood fibre to fit in there against the wood portion of the window. On the sill I have made a tapered wood fibre fillet. This will be primed so I can cover the still with flashing tape and also stick to the bottom edge of the window creating a pan in front of the window to shed water. The metal sill is meant to then fit into a grove under the window. All wood fibre will covered in membrane of some sort my walls are made from 45x245 timbers and I have 60mm external wood fibre. There is a black membrane on the outside and then I have 50mm battens to which I will clad with an open rain screen.
-
Got the big ones in a few weeks ago. 3 guys and a robot for £1k plus me. The glazing robot was great. A reckon the big unit was 500kg.
-
Spray foam gun cleaner works for me. I think it’s acetone
-
Il don’t know off hand but my slider is smaller than yours Russel. Prob closer to 3m but it is quite tall at about 2.6m which makes it more intimidating from a tipping over perspective. I also think 5 people could lift all my windows in. I have an insulated raft base which makes the finished floor 500mm higher than the current outside ground level. I think it might be worth my time trying to prep the site to take the robot in any weather. I was trying to avoid putting any sub base down that will need to be dug out again to fit the drains. If I put the drains in first it will delay getting the windows in.
-
Hi I have some large triple glazed units to fit. The biggest is around 2.6 by 3m. The company that sold the units have a glazing robot which they can supply with labour at £1000 per day. This could work well if the ground around the house is hard, it was last week but the rain this week has turned it soft again. Another option is renting or buying from AliExpress a glazing cup vacuum pad that I can sling from our digger or forklift. These can lift over 500kg which is well within the weight. The biggest problem I can see with these is drawing the window into the rough opening. The rope it is dangling from can only get so close to the house so it’s not as handy as moving it into place with a glazing robot. The robot has a much more positive placement. How are large units normally fitted without the use of loads of people . Even people might be tricky as only so many hand can get a good position to lift. If I had to do it myself. I think I would prob use the forklift or digger with a vacuum pad. Maybe a chain hoist between the digger and pad to give some height adjustment. I would hold the window away from the house to avoid damage from the digger getting too close. Prob put a hand sucker pad to each bottom corner of the window and attach a ratchet strap to each hand sucker pad to draw the window inside the house. As the window swings in lower it down with the chain hoist. ??
-
@JamesP oh yes I forgot I have an external membrane and internal vapour barrier. Do you have a closed cladding or is it open rain screen?
-
@JamesP yes it’s 60mm wood fiber 12 mm Elka board 245mm stud filled with wood fiber, 12mm osb then 45mm service cavity and plasterboard
-
Roof complete! Major relief. Third baby is due on the 16th of March. Scaffold came down yesterday. Next job is to finish building the porch, install the rest of the windows and complete the outer membrane. we have been lucky with the weather low wind and not much rain. Need to wind proof the membrane in case we get another storm soon.
-
Built a rough staircase today. I needed a better way of getting materials upstairs. Next step is to take the windows upstairs ready for fitting.
-
Still up at roof level but I see light at the end of the tunnel with the roof. A couple of weeks and I should be able to get rid of the hire scaffold and then switch over to my own. last week I installed my first window, 1 down 23 to go.. What this project needs is a one man band joiner. I need someone I can work with together. What I find is most companies work as a pair which leaves me redundant and paying twice as much. I would rather employ one person for a long time rather than multiple people for a short time. This is especially true with theses passive house style builds as a lot of time can be lost scratching heads with unfamiliar details.
-
Is it normal for roof membrane to leak like a sieve?
gavztheouch replied to Tom's topic in Roofing, Tiling & Slating
I found it really hard to secure the membrane without making holes which leak. The biggest leaker on mine was the screws holding down the battens and there is not much you can do about that. In general though it kept most water out. If you do not secure it down well and use less fixings to avoid hole if the wind picks up it will tear and oil on the membrane making much bigger holes. -
Hi im thinking about a temp install of my heat pump to put some heat into the slab. My timber frame is sitting on an insulated slab and water is pooling under the sole plate. In winter it prob is not drying out under there. Going to start to seal the house up to limit water ingress. I though it might be worth hooking the heatpump up to the ufh to try and dry the soleplate. My system has about 70 litres of water in the pipes. Im looking at connecting the arotherm straight to the ufh manifold, from the diagram the only thing extra I think i need is an expansion vessel. Does that sound right. I was hoping the Vaillant heat pump would be able to pump the water round the circuit using its internal pump. It might be worth adding insolation valves both ends of my temp pipe so I can try and save some of the expensive antifreeze/inhibitor
-
Hi everyone, Im looking for some ideas and opinions on my flat roof design by my architect. I am a bit worried about the use of sealant as a primary waterproofing layer on my new build roof. Here is a walkthrough of the design and how to build/sequence the detail. Step one: The green coloured roof in the image is a layer of osb attached to the rafters, it is covered in a breather membrane. The purple part is firestone epdm formed inside the parapet, up the walls and down the other side of the parapet to form a little triangle web. Step two: A ventilated deck is formed above the original osb roof and epdm. This layer is covered in another breather membrane. There is a plywood upstand running up the cheeks to form the standing seam upstand against. Step Three: Standing seam Greencoat metal roofing material is added, note the upstand against the dormer cheeks. Step four: A flash band tape is added to seal the standing seam metal roof against the dormer cheek membrane. The tape is called extoseal by proclima. Step five: Cladding battens are added. Step Six: Add wooden cladding Step Seven: Adding metal capping piece over parapet walls tight against metal roof Step eight: Add sealant where the capping piece meets the roof. My issue with the design is the reliance on sealant to waterproof the junction between the capping piece and metal roof. This will have the roof above pouring water onto this area and also wind driven rain will be blown back against it. I have 4 dormer windows so there will be 8 of these junctions. The architect did mention I could slip the capping piece under the standing seam. I think for that to be better it would need to be running up the roof with a suitable overlap to stop wind driven rain and capillary action. I think it would also need to flair out and become flat to be able to go under the roof which will be difficult with a steel capping piece. Also unless you lap the metal roof like slates in this area you will always need to seal certain edges with sealant. I have a few ideas on how to better the design but I wanted to get some opinions on the design as it stands today. Would you do this detail on your new roof? Cheers Gavin
-
https://youtu.be/uZf9aAsytm4?si=TO_7B4VJdSwwK2bB I have a question about my parapet walls and thermal bridges I think as a compromise I might just use one 245mm by 45mm for the upstand and cover it with 60mm insulation on the outside to keep it warmer