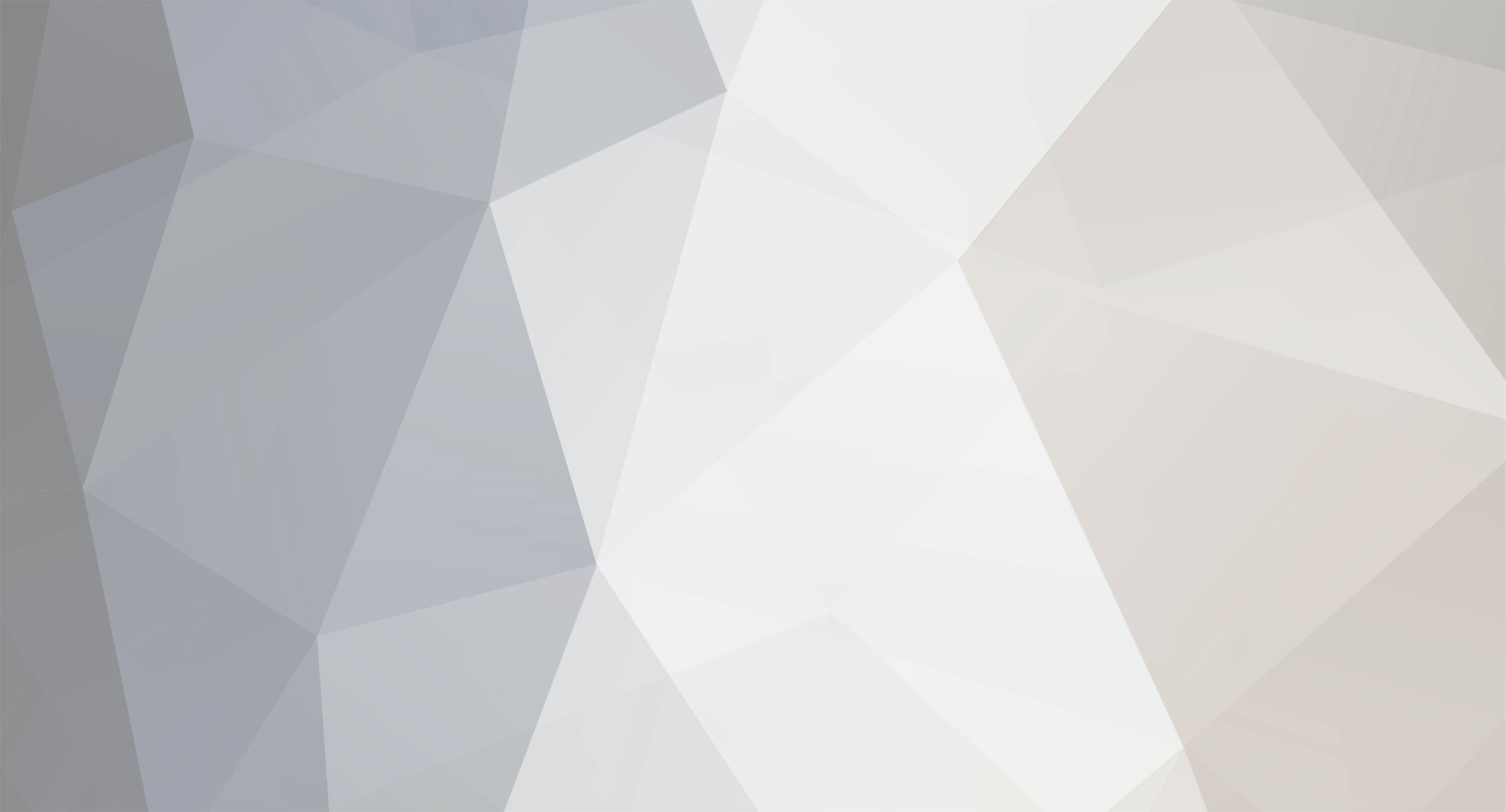
BadgerBodger
Members-
Posts
131 -
Joined
-
Last visited
-
Days Won
1
BadgerBodger last won the day on September 14 2024
BadgerBodger had the most liked content!
Personal Information
-
Location
North Lincolnshire
Recent Profile Visitors
2178 profile views
BadgerBodger's Achievements

Regular Member (4/5)
58
Reputation
-
Lincolnshire. Day rate - labour only. From found to wall plate inc two external gables and one internal. 101m2 external 150mm cavity wall. Brick/block with English garden wall bond externally. 45m2 internal block some 140mm and some 100mm. All “technicians” work I.e tray, taped insulation, stays etc. insulated block and beam with reinforced slab atop. couple of days left but currently sitting at 13k and forecasting to finish under 18k
-
Running MDPE pipe through drainage field
BadgerBodger replied to flanagaj's topic in Waste & Sewerage
IMHO you should definately have used barrier pipe. -
Public liability insurance - nothing else (yet)
BadgerBodger replied to Drellingore's topic in Self Build Insurance
Howdens brokers I had a reasonable quote from them for various individual aspects -
Crane pad thickness
BadgerBodger replied to Lincolnshire Ian's topic in General Self Build & DIY Discussion
Have you considered a designed solution, technically this is temporary works and should be considered by an appropriately qualified engineer based on ground residual ground bearing pressure of the outriggers and the bearing capacity of the substrate… if not at the very least, go with the crane suppliers advice. And, if you know you have „bad ground”, throw some geo grid and terram down under the stone for good measure, it will help act a a separation membrane when you’re digging it back up later. the last thing you want is a crane going over! -
5.95 offer received in last fortnight. Took roughly 6 months to pull together doing my own BOQ and pricing.
- 1 reply
-
- 1
-
-
This puts my quote for 2500 from Yorkshire water into perspective. They only lay 2m onto the property though. Annoying considering I put 575m pipe down the lane for less than 1800
-
Also I see a shed load of “computer says” with engineers on site… a misinterpreted point or an incorrect layer on a complex drawing can be an extremely costly mistake… It’s like using Chat GPT, the technology is great so long as you A. Know how to use it and B know enough about it/what you are doing to interrogate the output. Amazingly, many lack skills in A, B or both!
-
I’m reading your other thread and thought I’d throw my two cents in… Perhaps I’m a little more prone to taking risks but if the overall upstand size still fits (I.e the rooflight can still be installed over it), the upstand is at least 150mm on all sides from top of the flat area of zinc and the workmanship of the weld detailing is acceptable (you’d have to make the call on that or get a consultant to comment) and velux haven’t explicitly stated that it can’t be installed over multiple layers of zinc, I’d be inclined to install anyway… If you are still unhappy, the zinc layering means the rooflight doesn’t fit or the upstand is too short, have you considered extending the upstand with solid timber and/or cutting back the zinc in the bracketed areas using a colour match GRP to dress in the detailing. Yes it might not quite give the aesthetic you want but many GRP specialists warrant their work for 20+ years. In industrial roofing with Kalzip (a similar albeit not the same product) this is a typical detailing solution for unplanned or overlooked penetrations. I’m sure if you spoke with the roofing manufacturer and velux technical teams a simple enough solution is in front of you. As much as we would all like it to be, building on site is not always a precise science and one has to be dynamic and pragmatic about things like residual risk in situations such as this. The main problem is that for the most part, most people only think about THEIR job and not how it interlinks, impacts or even obstructs a subsequent task. In fairness I am often frustrated by this but I have to remind myself that it is not their role. Adding to this frustration, the architect does not include explicit instruction and provides “typical” details which overlook the most complicated scenarios (in your case, where the materials overlap). There are many reasons for this which often includes an inability to half the issue in their minds eye and permissible dimensional and installation tolerance in accordance with the British Standards. Adding to this confusion are the manufacturers guidance notes which in many cases are only available by request and are more restrictive than the British Standards which architects specify to. As others have said, don’t beat yourself up about this, it’s a typical conundrum, but it’s also a situation which would be “overcome” by a site or project manager by opening dialogue with all the relevant parties albeit sometimes circumventing a difficult contractor and just telling them what the solution was.
-
What to do with bare earth garden during build?
BadgerBodger replied to Ed_'s topic in Landscaping, Decking & Patios
Glysophate sounds like the solution here. Maintain that scorched earth look like a champ. -
For building regs you normally need ties 225mm from wall opening jambs at 450mm vertical centres (I think). More than likely an issue…
-
I found that once I got most of the bigger players discussed here down to the same spec and scope there were much of a muchness for the material cost +\- 10% or so. It was the fitting that varied the most and I just want entirely sure with some that I wouldn’t get more costs down the line. In some cases fitting wasn’t offered. Installation, surveying and delivery varied the most being between 40 and 60% of the material cost. We went to VELFAC, Nordan, Norrsken, Rational, internorm & 21 degrees. Or relevant rep installers. Some were just plain difficult to deal with and went off the list. We’ve needed up with Norrsken based upon reading here and elsewhere. Would have like Nordan (used before) but they didn’t offer fitting. Being honest the Norrsken windows are the only ones we haven’t seen but in reality IMHO they were very similar with the main leading difference being the larger the frame size, the more “solid” they felt. I wasn’t so keen on the Belgae ironmongery (too spindly) and it was the flimsier feeling of them all. The only exception being the internorm lift and slide which was truly magnificent!
-
-
Yes, it’s the upper floor UFH i am most concerned about as opposed to the flow/return to the manifolds. I know everyone says that UFH likely isn’t needed upstairs but because of the high ceilings and general area I’d rather have it and not use it that not have it and want for it! So here if the surface temp of the floor was say 30 degrees and the RH within the house was 50% the dew point would be around 18.5 degrees meaning the flow temp of the water in the upper floor area would need to be above that because the UFH pipework isn’t insulated. Or am I missing something?
-
My worry is in the upper floors where pipework runs in a joisted floor. I’m not sure what the air temp might reach because of the larger space, air tightness and increased insulation but unless I’ve misunderstood, the table below indicates that my current room in roof dew point in summer at 40 % rh and reaches 35 degrees quite regularly, the dew point is just above 19 degrees. How would I manage the flow temp to ensure it runs above the dew point for the relative RH? I could probably tolerate a wet floor in the tiled hall. I wouldn’t want soggy ground floor ceilings.