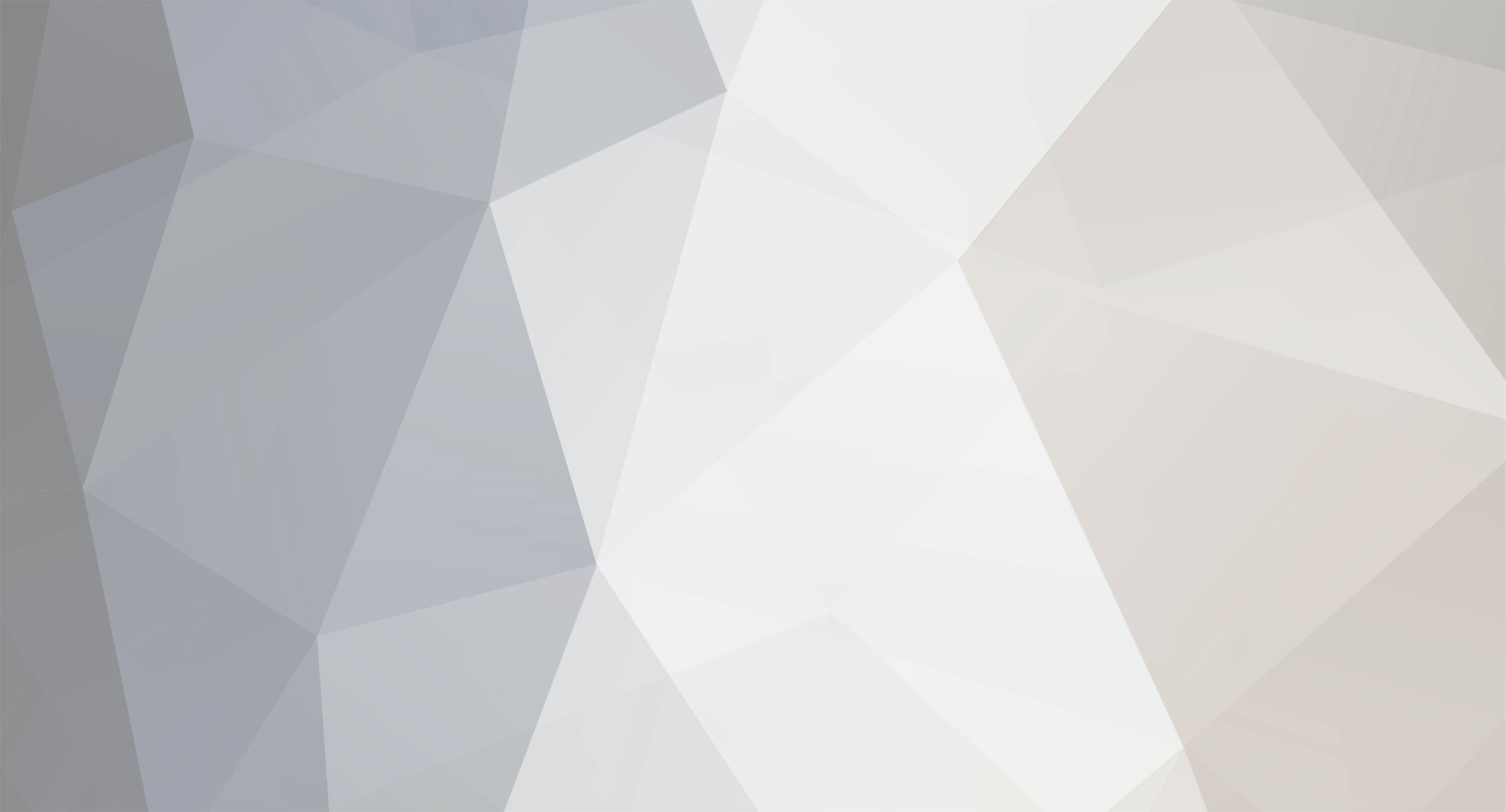
ADLIan
Members-
Posts
667 -
Joined
-
Last visited
Everything posted by ADLIan
-
Anyone got a WUFI Pro licence?
ADLIan replied to Drellingore's topic in General Self Build & DIY Discussion
Also is there an option to use SI units? Written around ASTM Standards rather than British Standards so not applicable to UK Building Regs. -
The section on cavities and cavity barriers in dwellings in Approved Doc B is relatively short and straightforward. Follow this and if BCO raises an objection ask exactly what their issue. Rockwool will insist that you use their insulation with their cavity barriers - if so try another manufacturer such as Promat FSI or Siderise. The type of 'cavity' insulation is not relevant.
-
The cavity barrier would normally be from the main stud (structural) wall through the 'external' woodfibre insulation to the back of the cladding - in this respect I would imagine there are quite a few manufacturers. There are some cavity barriers that can sit external to a non-combustible 'cavity' insulation but in this instance the cavity barrier must be tested in conjunction with the cavity insulation. I note the ply/OSB sheathing is internal in this instance, perhaps this is where some of the problem lies. In dwellings the cavity barriers are normally around openings and at each storey height and at the top of the cavity. I doubt the company linked to above will have the technical resource to comment and advise on something as specific as the English Regs & Approved Docs. NHBC and/or LABC technical manuals may help. Perhaps ask your BCO for guidance, citing specific requirement and sections in Appr Doc B.
-
Hi Nick - I doubt this will happen. Again post Grenfell manufacturers are very careful on what they claims. There is a big difference between reaction to fire (above discussion) and resistance to fire.
-
Post Grenfell the Building Regs were updated and walls of high rise buildings had to use non-combustible materials, Euroclass A1 or A2. There is a list of exclusions for items such as gaskets, brackets and membranes. ‘A2’ rated breather and AVC membranes are now available giving enhanced safety. Bearing in mind their position within the construction not sure there’s any real benefit of the non-combustible version in normal low rise dwellings but at least there is a choice.
-
Appears there is some dumping of commodity building products on the UK market by Turkish manufacturers - seen similar with insulation. Provided the product is manufactured to and complies with the British or European Standard and carries the correct CE label then it is deemed fit for use. Not sure what would happen if you needed sales or technical support from these companies. Pay your money and make your choice. Caveat emptor!
-
Cavity tray at abutment missing?
-
No need for insulated cavity closer or similar measure as garage is unheated (normally).
-
Closing cavity at the top for blown beads
ADLIan replied to MortarThePoint's topic in Heat Insulation
Any clear cavity in the cavity wall should closed at the top to stop fire/smoke being able to spread into the roof void. -
Builder put 'rockwool' below DPC, I am in flood zone. Fixes or thoughts?
ADLIan replied to boxrick's topic in Heat Insulation
If it’s superglass insulation phone their technical department and get their advice -
What is the span of the roof? More than 5m creates a problem. Do the proposed vents allow cross ventilation to each roof joist void? They appear to comply with the British Standard and Building Regs for open area. Can the vent manufacturer help? On a general note cold flat roofs should not be used with current levels of insulation. Relying on unknown and unquantifiable ventilation levels leaves a big question mark over the long term performance. Perhaps what the BCO is alluding to.
-
As the name suggests Koolduct is for insulation of A/C ducts and not for use in floors, walls or roofs. Not sure who would risk that in a floor under the slab or screed!
-
If you are just completing now you may only have the 'as designed' SAP. On completion this is updated to the 'as built' to include the air test result, actual insulation/thickness installed, make and model of heating system, solar PV etc, etc. At this point the EPC can be lodged too. If you can get the 'as designed' SAP file from the original assessor you may be able to pass this to a new assessor to do the 'as built' assessment. Check the EPC register as you first port of call.
-
They're 'seconds' for a reason - they've failed quality control procedures. May not have correct compressive strength or thermal performance as well as dimension problems. May not comply with relevant manufacturing Standards. With no label you don't know what you're buying.
-
Cables above or below acoustic insulation
ADLIan replied to tommyleestaples's topic in Electrics - Other
100mm mineral wool insulation is often used between joist for acoustic insulation in intermediate floors within dwellings - see Appr Doc E. Some plasterboard & I-joist manufacturers have systems that comply with the Regs without the need for this insulation. The insulation will also have thermal properties but this is irrelevant here. An electrician will be able to advise but I believe good practice is to clip the cable to the sides of the joist above the insulation. Cables under the insulation may need de-rating but this may not be too much of an issue with lightly loaded lighting circuit cables. -
Impact of broken gas boiler on EPC
ADLIan replied to Michael_S's topic in Environmental Building Politics
SAP assumes the main heating system, gas boiler in your case, works and supplies the heating and hot water even if broken. If you choose alternative space/water heating that’s your call and not SAP. -
Here are 3 examples one from the now out of date Accredited Construction Details (so been good practice for some time) and one from URSA and Knauf current publication. There are many more.
-
With insulation at horizontal ceiling level the gable cavity insulation should extend something like 300mm above the top level of the loft insulation. Should also use a cavity tray to protect the top edge of the cavity insulation and change of construction (in practice I’m sure this is rarely done!) Alternatively insulate all of gable.
-
And not choice of insulation type! Can we put 'sweating' in the same bin as 'thermal mass'?
-
Rash statement as you know nothing about me, my background, knowledge or experience.
-
Not to the Psi-value (the heat loss at a junction) which is all the RCDs are looking at. They cannot cover every scenario of floor level, external levels, DPM/DPC positions etc
-
If by 'sweating' you mean prone to condensation this statement is rubbish. Bad roof design causes condensation problems not the type of insulation.
-
I wouldn't get too hung up on the position of DPC/DPM in these details. Their primary function is to show the geometry of junctions (with all adjacent materials and physical properties) in order to arrive at the Psi-value - the DPM/DPC has no effect here.
-
U value Calculations for timber frame wall construction.
ADLIan replied to Croccy's topic in Heat Insulation
The 15% thermal bridging with timber frame means you don't get the benefit of a 32 product between the studs but there is a big cost associated with it. A 35 product will give basically the same U-value and is more cost effective. -
Roof insulation / air gap design
ADLIan replied to Pappa's topic in Lofts, Dormers & Loft Conversions
If you fully fill the rafter with insulation you then need to counter-batten and batten for the tiles/slates.