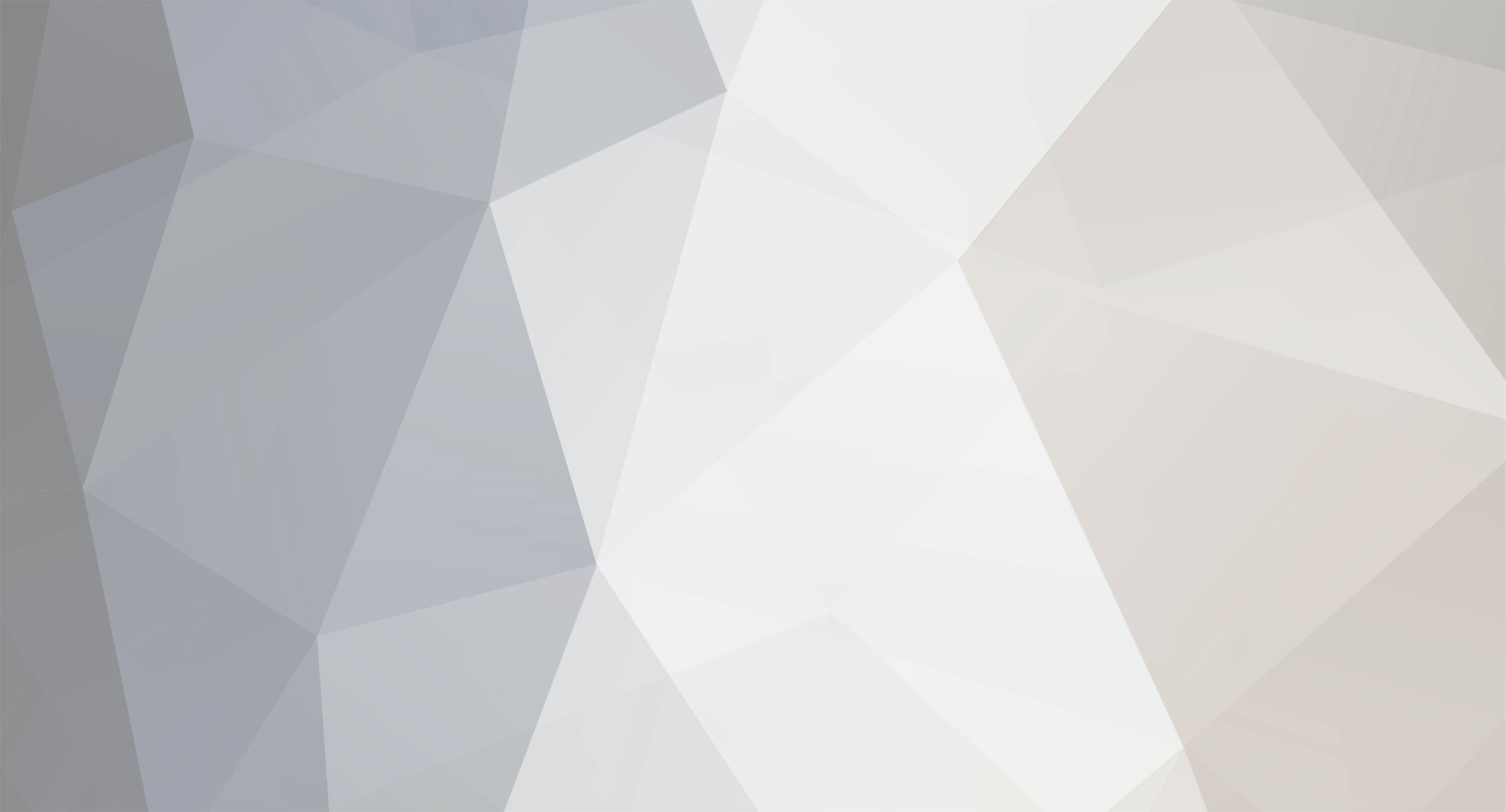
akjos
Members-
Posts
34 -
Joined
-
Last visited
Personal Information
-
Location
London
Recent Profile Visitors
528 profile views
akjos's Achievements

Member (3/5)
7
Reputation
-
Of course it would. But usually it’s hard to find smaller units. 2.5 or 3 are very common and might have a good deal, so instead of chasing every W sometimes it’s better to just install something which is practically available.
-
A 2.5kw or 3.5kw unit would be more than enough for your room and would work great.
-
I have a similar setup, two UFH manifolds, on on ground and one on first, same piping as you but without any mixing valves and pumps on the manifolds. The ASHP flow and return are directly piped into the manifold as the internal ASHP pump has enough power in my case to push flow through everything. If you remove the mixing valves and still don't have flow in the ground floor manifold, try closing of the first floor one and check again. Water will take the flow of least resistance, so it might be the case that your first floor manifold just passes the whole flow through, so you'll need to add resistance so water reaches the second one. This should have been calculated as design though, and if all flow rates for each loop are correct this shouldn't be a problem. Worth checking though.
-
Your heatpump needs around 2-2.5x the capacity in flow rate in l/min. So 9kw unit you’ll need 18-22l/min for the unit to work. Otherwise you’ll get flow rate errors. Not the individual rooms or UFH loops you can calculate by the heat output formulas gives above. But you heatpump overall needs the high flow rate to function.
-
As JohnMo said, many variables to take into account, which means nobody will be able to tell you what to set your heat curve to without knowing the details. The simple answer is: Don’t fix it if it ain’t broken. The more complex approach, if it isn’t working properly right now or you want a better performing system: 1. Figure out your heat loss. Preferably room by room at certain outside design temp. (Example: -3C). 2. Get the data sheets for your radiators and calculate what temperature needs to flow through them with a delta T of 5C to achieve the heat loss from 1. 3. Look at the Grant manual and see the heat curve lines. Find the one which gives you the needed flow temp at the design temp. 4. That’s the curve which will work best for you.
-
What you're describing is exactly what is being used in commercial settings for many years: VRF Systems, i.e variable refrigerant systems. You'd have experience them most probably in hotels and similar. Essentially there are big condenser units and then there is a main trunk with both hot and cold refrigeration lines branching to each unit. The cool thing is they can even balance themselves out, i.e if one unit needs cooling, and another heating, they can work between each other as condenser and evaporator and not use the big outside unit. Really cool stuff, but overkill for residential for sure.
-
L9 Error - Flow rate - Ecodan 8.5kW ASHP
akjos replied to athlonoc's topic in Air Source Heat Pumps (ASHP)
When you re-pressurised it, did you bleed all air out? Make sure all air valves are open as trapped air can also cause flow rate issues. -
Combining radiators with UFH - some surprising conclusions
akjos replied to sharpener's topic in Air Source Heat Pumps (ASHP)
From a theory and calculation perspective I think your conclusions make sense. But in reality this setup would be unpractical. If I understand correctly, based on your following statement: you have modelled the system to receive 45'C flow on both Rads and UFH. Your UFH return is 20'C because the flow rate needs to be very low to only output 2.5kW. UFH has a huge surface area, and feeding it 45'C it makes sense to only require a tiny portion of the overall flow rate. But in reality, you don't want to feed 45'C to UFH and have a 20'C return. There will be big fluctuations across the floor, cold spots, hot spots and flooring most probably wouldn't support it. UFH should be at 5-7'C delta T to be comfortable, that's why the 'more conventional' setup has a separate pump and mixes the flow. Ideally we'd run the whole system on a lower temp, oversize rads and have everything running on a lower flow temp with both rads and UFH giving an acceptable delta T. -
From what I’ve read online, Hitachi are one of the best. I was considering them but found a really good price on a Midea unit and got that one instead. If price is good, I’d definitely go for the Hitachi, they’ve been around forever..
-
Mitsubishi Ecodan immersion heater
akjos replied to NightMail's topic in Air Source Heat Pumps (ASHP)
@NightMail are you still seeing high usage of the immersion heater even with warmer outdoor temperatures? It's absolutely normal for your COP to fall in the colder months. -
Mitsubishi Ecodan immersion heater
akjos replied to NightMail's topic in Air Source Heat Pumps (ASHP)
There is usually a setting in the ASHP unit where you can specify under which temperature conditions the booster heater should be used for DHW. This is usually meant for very low outside temperatures, where you don’t want the ASHP stopping your central heating in order to heat DHW. So the unit can use the booster heater in those situations and not have any down-time in your central heating. My Midea unit has these setting in the controller, though I’m not sure how the Mitsubishi is configured, or if it is configurable at all. -
From what I’ve seen they’re really good units for a good price. Pretty much all in one nice compact package on the monobloc artic series. Contains also an expansion and pump inside the unit. I’ll be getting an 8kw mono for my house deep retrofit soon. Check this out as well: Also here are some technical specs: https://www.microwell.sk/assets/uploads/matrix/files/downloader/TM_Midea_A_series_Mono_M-Thermal_Heat_Pump_R32_2020513_V1_7.pdf
-
ASHP size (don’t sigh I’ve done the calcs)
akjos replied to Kelvin's topic in Air Source Heat Pumps (ASHP)
How are you going to distribute the heat? UFH, rads something else? What flow temperature was it designed at? also how big is your property? If your heat loss is 3.6kw, a 11kw unit seems unnecessarily big. Anyway it’s worth knowing your whole design. -
Samsung 8kw R32 Monobloc Air Source Heat Pump
akjos replied to Ceridunn's topic in Air Source Heat Pumps (ASHP)
Water expands as it heats up, so you definitely need an expansion vessel both on your heating circuit and your DHW. Just search for Robokit online. -
In the summer, can a heat pump do cooling *and* hot water?
akjos replied to Garald's topic in Air Source Heat Pumps (ASHP)
For the heat pump itself it’s no issue at all to switch between heating and cooling as much as you like. That’s exactly what it does during defrost in winter constantly. It switches to cooling and runs hot gas outside to melt frost on the coils, then back to heating. As @jack mentioned, you have to pay attention inside where you might have condensation. But if you use fan coil units for cooling, those usually have their own condensate drain.