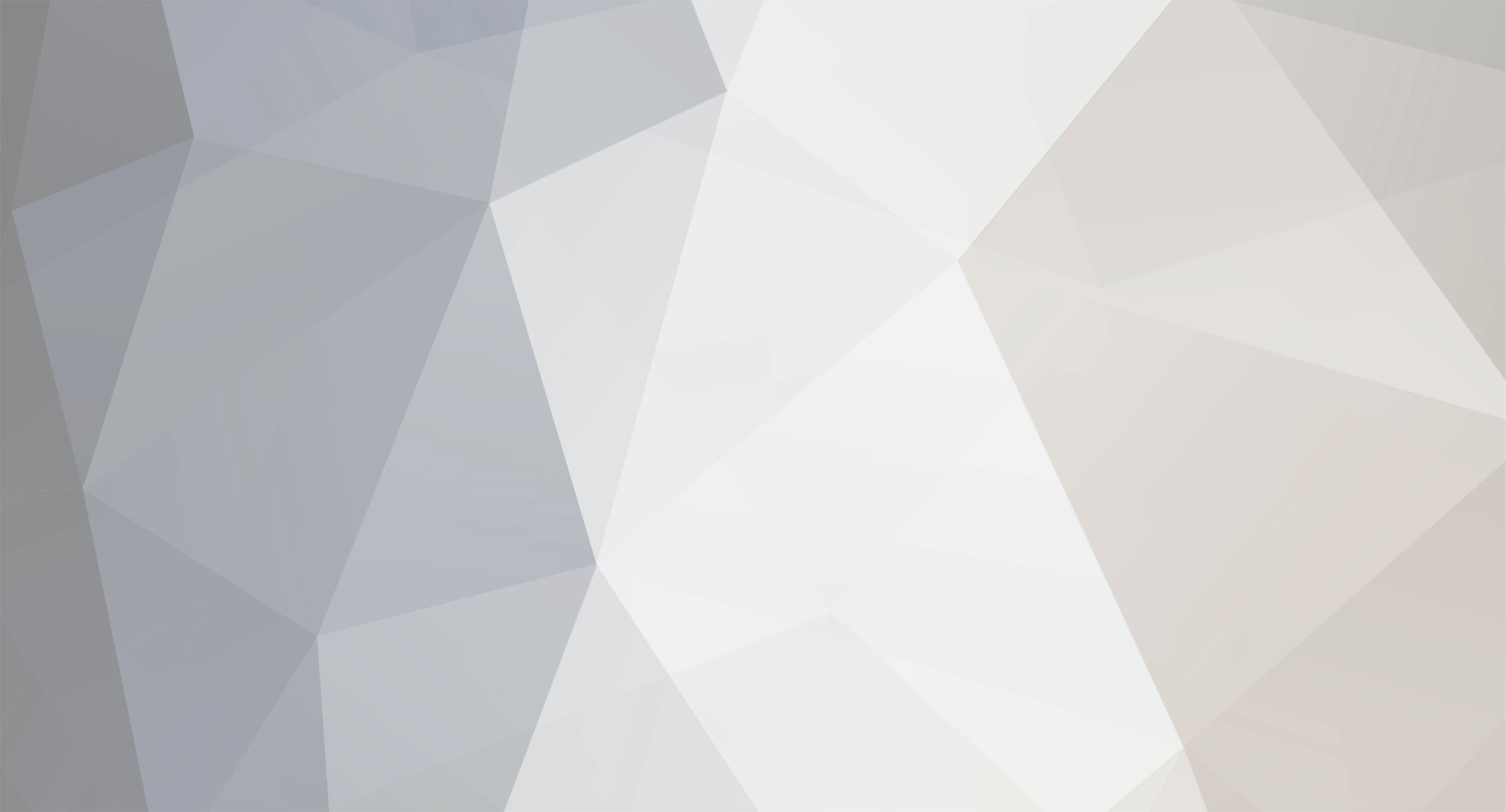
ChrisJ
Members-
Posts
46 -
Joined
-
Last visited
Recent Profile Visitors
ChrisJ's Achievements

Member (3/5)
18
Reputation
-
ICF Pricing and ease of use questions
ChrisJ replied to IATM's topic in Insulated Concrete Formwork (ICF)
Check your pricing, some appear to be block prices (more then a square meter) also look at each blocks features to understand the price difference as well as support from distributor/manufacturer for details available -
ICF Pricing and ease of use questions
ChrisJ replied to IATM's topic in Insulated Concrete Formwork (ICF)
Just to update, have found a new supplier with XR35 for £65 per m2 -
Internal wall connection to ICF
ChrisJ replied to metalgear2k2's topic in Insulated Concrete Formwork (ICF)
Awesome, sometimes you get lucky with the correct moisture content in the wood and never get a crack -
Internal wall connection to ICF
ChrisJ replied to metalgear2k2's topic in Insulated Concrete Formwork (ICF)
It’s needed for sheer purposes, plus to prevent cracking in the corner of the plasterboard -
Internal wall connection to ICF
ChrisJ replied to metalgear2k2's topic in Insulated Concrete Formwork (ICF)
Using Nicks comment for wood, Use an SDS drill, drill thru the stud, foam and into the concrete, epoxy/resin threaded rod in, every 600-750 starting just above the floor will be fine, once cured, square washer and a nut, snug it up add 11mm OSB typically one side is enough nail every 50-75mm on the perimeter of the sheet and 150 in the field -
ICF How much more expensive ?
ChrisJ replied to Dave Jones's topic in Insulated Concrete Formwork (ICF)
@Nick Laslett Your drawing makes sense to me, couldn't tell from your photo I don't agree with the DPM between the top of the slab and the wall, may as well just slather some butter on there as the bond will be the same @SteamyTea Yes rebar can help during catastrophic failure, I've seen it and allows time to safely secure and repair rather then no notice and someone die -
ICF How much more expensive ?
ChrisJ replied to Dave Jones's topic in Insulated Concrete Formwork (ICF)
Is that DPM on top of the concrete slab separating the wall concrete from the slab, or placed prior to the slab concrete and just run over the top edge of the KORE? -
ICF How much more expensive ?
ChrisJ replied to Dave Jones's topic in Insulated Concrete Formwork (ICF)
Sure we do, rebar on the perimeter where the structure sits and then typically mesh across the top of everything -
ICF How much more expensive ?
ChrisJ replied to Dave Jones's topic in Insulated Concrete Formwork (ICF)
How we get away without rebar throughout amazes me actually Understanding what the rebar does would make you question - does the engineer understand it The theory of we don't use it in block walls why would we put it in concrete walls then - is like comparing an engine on a 1992 Ford Escort and a 2025 BMW X5 Concrete shrinks as it cures, the larger the concrete mass the more its pulling on itself and more chance of cracking. now granted its within the ICF form, the perfect cure environment as moisture is trapped, a typical concrete test is done at 28 days to ensure design strength has been achieved, in ICF I have had it fail many times at 28 days as the cure is so slow based on moisture being trapped, however at 56 days not only met the design strength but exceeded by 50% or more Back to the rebar, the horizontal bar is to help with cracking, that's it, nothing more, nothing less, I'm referring to the horizontal in the main open part of the walls, above lintels is different. vertical rebar deals with loading, not just wind or backfill loads, but also point loads from above. how we set a steel beam into a pocket of the wall without vertical bar directly below amazes me as well Does no one question why we do slabs and have mass amounts of rebar cages throughout and then the walls above have no rebar? This post is to make you think and question nothing more -
I don't know the product you are using but any that I have used all requiring rasping The block maybe clean but its also got too smooth a surface so the base coat will not adhere and be loose and potentially fall off And even tho only 6 months old I can assure you there is some UV damage and a light film on it, rub your hand across it and you will see it on your hand but maybe not visible to see
-
There is a product called Insuldeck it is from America, but I understand there is also a manufacturer in Italy and can arrive in the UK in about a 2 week turnaround. I have used the product in Canada and if you are after a concrete decking system I would recommend it. It is similar to Amdeck, however it is one piece length rather then small panels as Amdeck is. Amdeck is not available here, shipping from Canada is possible but costly unless you require an entire container
-
Is your balcony proposed to be concrete or wood? Both are possible, personally I’d do concrete for long term. Based on your picture with columns from foundation to underside of roof this will all be quite simple for the engineer to design connection and support details price - you’ll need design first and then go for pricing
-
https://www.framemax.com Not part of the UK, but a company I have dealt with during my time in the US a long time ago, they have done well with pre fab walls for steel frame construction
-
Can you post some pics of these corner blocks failing?
-
Natural Stone for an ICF house is no different then conventional masonry, you can use a Brick Ledge (4.5" sculpted ICF form) form at the bottom to carry the stone, usually placed 150mm above finish grade or use an ICF form 4" wider (i.e. 10" below grade to 150mm above then switch to 6" ICF) the Brick Ledge form with proper rebar stirrups is designed to carry 27' (roughly 8.5m) of standard masonry bricks, I don't know that weight value but if you get that and your stone weight you can sort how high the stone can go There are ways to allow you to go higher, I've done 6 storey buildings all masonry and we used an angle iron every 2nd floor to help break the weight load to the brick ledge form at the bottom Brick Ties can be screwed directly into the ICF webs, most are rated for 450lb pull out depending on the screw fastener used (Sorry don't know the metric conversion for that). There is a 2 part brick tie that you embed part of it prior to placing concrete, it goes thru the polystyrene into the concrete void, probably have to import from North America and if I recall fairly expensive and not sure how well it would work since natural stone is various sizes. I did do a project in Los Gatos, California almost 20 years ago and the owner had very thick tie wire (think what was used for T-bar ceilings) cut in 800mm lengths, folded in half and then pushed though the foam into the cavity prior to concrete placement, this was engineer designed for the stone facade which exceeded 30' (9m+) in many areas