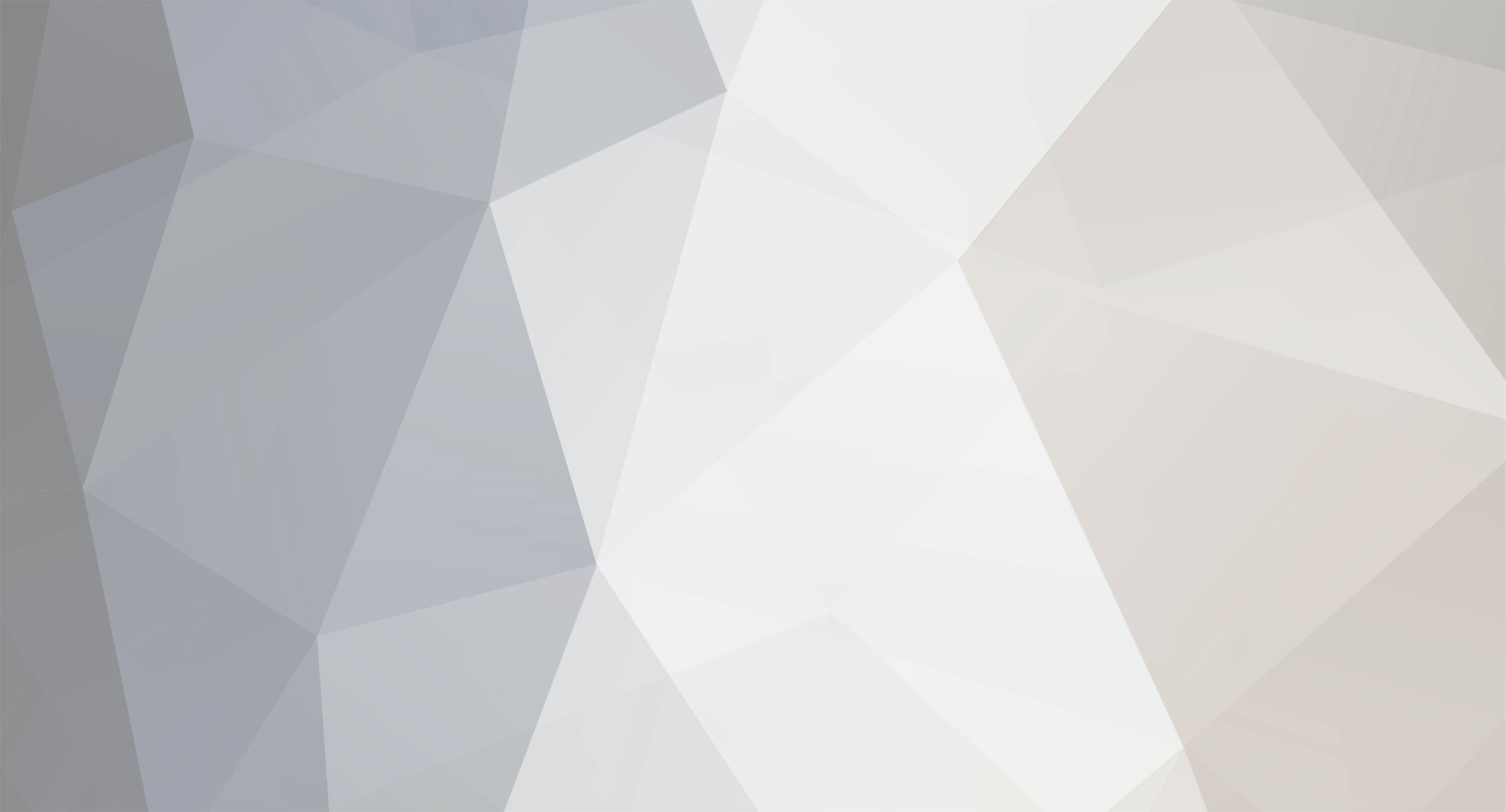
AdamSee
Members-
Posts
155 -
Joined
-
Last visited
Recent Profile Visitors
5091 profile views
AdamSee's Achievements

Regular Member (4/5)
62
Reputation
-
Can't connect the SWA cable. Practical help please.
AdamSee replied to saveasteading's topic in Power Circuits
You need a Wiska box, these are IP 66 rated so suitable for outdoor use. But they have M20 holes on the side so the SWA gland can screw straight onto the box. https://www.tlc-direct.co.uk/Products/WK108B.html I find the best way to get a decent earth connection is to use the spring rings rather than the bulky earth bar clamp. -
Was your son a climber by any chance? I had a wooden pull-up board above my bedroom door just after uni. It had big grips at the top to jump and grab (I'm short) and a crimping pockets below. Or in your case, a crimping rail. Essentially allows you to do pullup using fingertips only. Thing was called a Beastmaker. So that I didn't f-up the wall, I mounted a piece of 18mm ply to the wall first. This spread the load further out to the left and right. Then mounted the pullup board to it. Painted to match the wall when done. Looked "ok". A bevel on the sides would have improved its look.
-
Nice work with the adhesive, it uses alot, but thats the proper way to do it. I see you've also used soundcoat as a parge coating by the looks of things. Another proper job there. To get a long run of boards in line. My method is to put a chalk line on the floor, roughly 25 or 30mm away from the wall. When standing in front of the board, look down and that line should be parallel to the board face. Don't worry if it's ahead of behind the board line. Just ensure it parallel. Check for high / low spots and general plumb of the walls to avoid any nasty surprises. Particular in the top corners. For the gap in-between the boards, I would chuck some bonding coat in there, rather than leaving it for the plasters to deal with. Takes seconds to do, and makes for a more consistent plaster finish.
-
I play around with recycled plastics quite a bit and I've yet to find a glue that sticks to it. Use lost head screw for best finish. Depending on the decking type a bit of WD40 on the screw before driving it in helps buy displacing the plastic instead of cutting it away. The head becomes more "lost" in the plastic. Make sure to use stainless screws. Nothings worse than a fancy, permanent, rot proof, ever lasting decking structure.........with some rusty ass screws stuck in it. Btw, What decking did you go for?
-
Connecting toilet pan to broken clay pipe
AdamSee replied to Del-inquent's topic in Waste & Sewerage
As you said. Cut off the clay pipe below the crack. Use one of these to convert to a PVC pipe. Adaptors can be found from screwfix / toolstation. Link here: https://www.screwfix.com/p/mcalpine-push-fit-single-socket-drain-connector-black-110mm/4255V?kpid=4255V&cm_mmc=Google-_-Datafeed-_-Heating and Plumbing?kpid=KINASEKPID&cm_mmc=Google-_-TOKEN1-_-TOKEN2&gad_source=1&gclid=EAIaIQobChMI6-vH9J37gwMVf49QBh1wcAAyEAQYAyABEgLBHPD_BwE&gclsrc=aw.ds You could use a compression style rubber adaptor. They work fine and don't restrict the internal bore. If the pipe was horizontal I would recommend that option. Alternatives could be fiberglass lining it if you think its cracked under the house. Quite pricey to do. -
I've put UFH pipes through walls. Drill a hole large enough for some flexible conduit, make good with some motar....expanding foam.
-
Gap for washing machine, is 600mm ok
AdamSee replied to cwr's topic in Kitchen & Household Appliances
I would leave more than 600. Eg. 620 for the first machine, the 600 for the next. Learnt this from a recent annoying mistake. Left 1200mm for the two machines under a utility counter (my utility is essentially a hallway with a door either end). But once I had fitted the architrave on the door in front of the washing machine you could no longer open the detergent drawer. Certainly couldn't get any skirting down the side. -
Sweet looking bathroom pocster. Hopefully it remains leek free. Funny story relating to my post about my shower build....it eventually leaked. Not from a fitting, but from the diverter valve. Getting the faceplate off was a pain in the ass due to vast quantity of silicone use. Tried dental floss, rubbish. Got it off using two wall paper scrapers in the end. Had to replace the diverter in the end, and resealed it using minimal silicone this time. Best of luck!
-
Cheap sturdy vacuum cleaner for DIY cleanup
AdamSee replied to Gill's topic in General Self Build & DIY Discussion
I have the bosch gas 35 m class extraction. You can use it with it without the bag depending on how problematic the dust is. The extra long hose is very useful and it has an alarm when it's full or blocked. Overall it's a brilliant machine which is well suit for professional use, but it had a shitty flaw built in to it. After using it for a few weeks its pitch sounded off and it lost suction. Turns out that the internal soft foam sound insulation had come loose and blocked the exhaust. Had to opening it up and fix it once and eventually I removed it all together. It's overly complicated in there too. 4 out of 5 I guess. -
I've found a lot of the gu10 holders to be like this now, rather than the old type where you had to try and get the bulb in from below and twist them by applying pressure to the bulb. I assume it's the only way to maintain a ceilings fire resistance. The detachable connection block is good for the old style gu10 Philips hue bulbs, which were very tall. And didn't fit in much.
-
That wishbone looking bit of spring steel near the top of the black part of the fitting would usually hold the gu10 bulb. Remove the bulb from the fitting nad slide it in from above and in a sideways motion. Looks like the bulb will sit approx 50mm back from the base of the fitting.
-
Remembered to check today. The tracks I have are 1400mm long. Explains my issue with them.
-
Easier option, use the supplied tails and replace the (assumed) brass olive supplied with a copper one. That can be compressed directly on to the plastic pipe. Remember to still use a pipe insert.