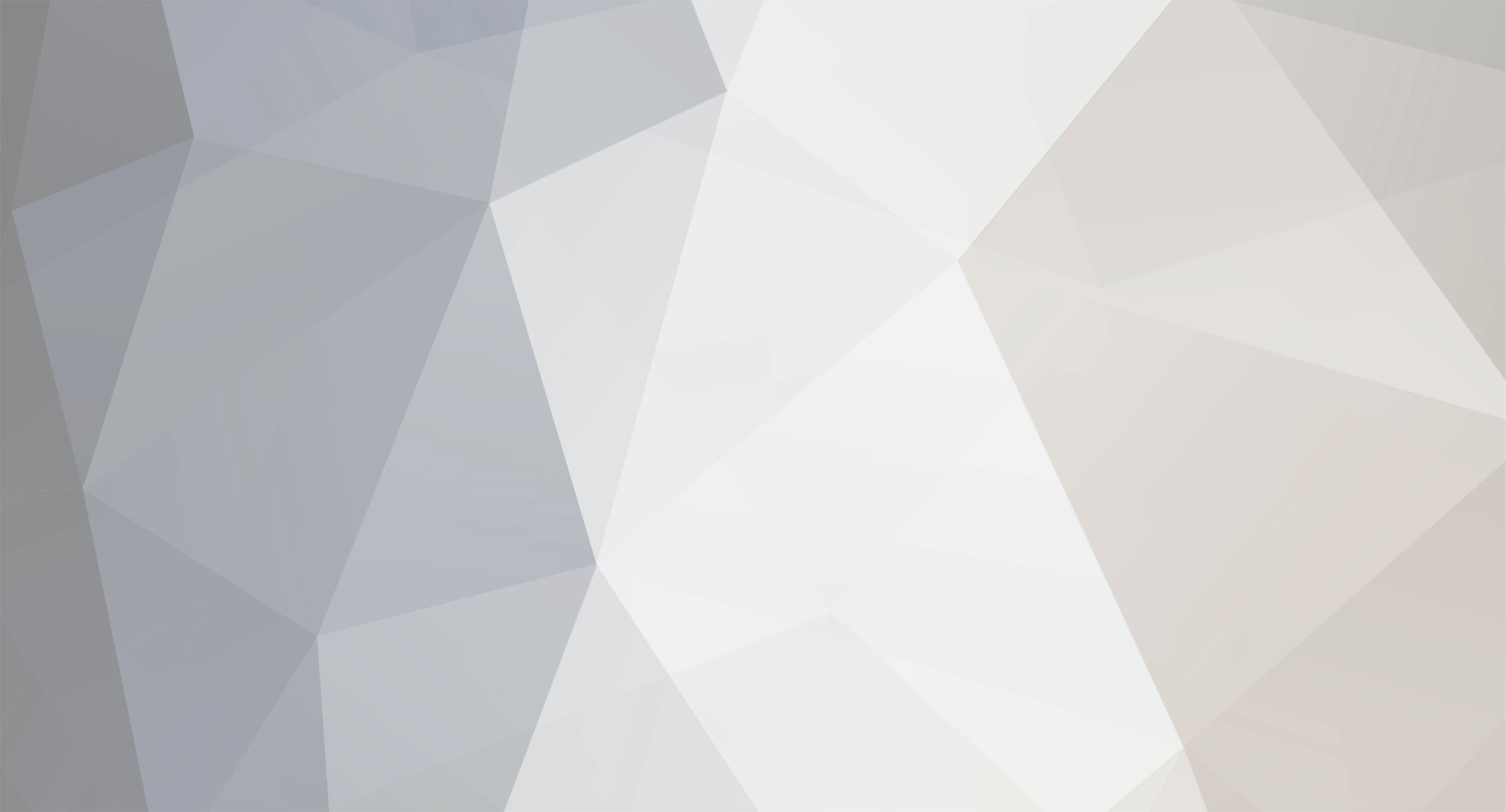
simon45089
Members-
Posts
31 -
Joined
-
Last visited
Recent Profile Visitors
The recent visitors block is disabled and is not being shown to other users.
simon45089's Achievements

Member (3/5)
20
Reputation
-
I was planning to install ASHP on my Barn conversion in rural Northumberland. (250 sqm) I put in lots of PIR insulation, and have a South facing gable end which is all glass. Underfloor heating downstairs, no heating upstairs. Its certainly not passive house standard, but I put a bit of effort in taping gaps and joints etc. I sought advice all over and did loads of real world research. I eventually came to the same conclusion. I bought a small cheap oil boiler and have no regrets. I spaced the UFH pipes so I could always retrofit ASHP if I have to. I have found the oil boiler cheap to install, cheap to run, and more than efficient for heating.- I have some big double height rooms and its always warm. My oil costs are just a few hundred pounds a year, and often I dont need the boiler on much. Also the floor heats up really quickly, despite what many say, it is almost as quick as a radiator to heat up. (I have a 50mm thick liquid screed over the pipework). We dont need to heat upstairs.
-
I got planning permission for conversion of three barns into a home in 2007. I converted a small byre, part of that project, in 2010 to comply with the condition to start work within 3 years. Building control signed the building off, which in hindsight was a mistake as It should have been part of the whole project and signed off when the rest was finished. Fast forward to 2022 and the entire project was nearly finished ( I was forced to get my Architects Certificate signed prematurely as the Architect was retiring at 88 !) I didnt know if I could make a successful VAT claim because the project had essentially started in 2010, been signed off, and no claim with the required 3 months made. I came across Andrew after some online searching. Andrew McDonald MAAT FCCA SELF BUILD VAT 33 Ocean Way, Pennar, Pembroke Dock, Pembrokeshire SA72 6RA Tel: 01646 687599 He is a self builder, and an accountant. He talked me through the rules and advised that I had a good chance of a claim, on all the building work EXCEPT the small byre completed in 2010. He was clearly used to challenging the revenue- in court if necessary, if he felt they were not applying the rules correctly. I sent him all my invoices, and he prepared the spread sheets and made the claim, with appropriate covering letter. As my build wasnt finished entirely due to my elderly Architect forcing my hand, I continued to rack up bills after the claim was made, which had significant VAT attached. After about six months of waiting for my VAT refund- to no avail, I contacted Andrew and mentioned I had more bills. He argued that the claim process was a two way street, and it was unreasonable for the revenue to refuse to add these claims to the original claim, as they had been keeping me waiting so long. A further collection of invoices was submitted, the VAT element of which, came to over 3K. Twelve months after Andrew lodged my claim with HMRC, I received a full payout of 16K, with no queries or rejections. I am of course delighted, and felt I should share the details of this superb professional contact. Andrews fee was a very modest £500.00. This account is entirely my own personal experience and I have no other relationship with Andrew other than as client. In fact I have never even met him in person ! I hope my experience is of interest to other self builders. Simon.
-
I am building a 7m x 7 m garage and am using Steadmans AS35 insulated panels. The sheets are 1 metre wide and any length, with different insulation thickness available- up to 120mm. I have done a previous roof with them and they were easy to fit and have worked well. You can fix them direct to timber joists, all the fixings are included. All in they cost about £2700. Simon/
-
Training recommendations to become a builder.
simon45089 replied to Claire B's topic in General Self Build & DIY Discussion
As Ronan1 says above, I would urge you to buy a a small dilapidated fixer upper and do it up and sell it on. The risk to your investment is relatively low, and the learning curve for your son will be huge. He will learn the process of building- the order that things need to be done. He will learn to organise trades to fit in with this schedule, and learn how to adapt when he is let down by some of those trades in the process. He will learn about budgeting, and shopping around securing the best deals fo materials as well as learning when cost cutting is a good idea, and when it isnt. Knowing how to speak to building control and get the best out of that relationship is also invaluable. If he is interested in the practical/creative side of things then by watching trades at work he may find he wants to learn more and get hands on- or know where to leave well alone. When he finishes the job, and sells the property on and covers his costs or makes a profit, then he will know if development on a grander scale is right for him. He will have learnt much more than any formal courses in my opinion, and at a much quicker pace. All of this I did myself at 26, having realised my very different chosen career was not for me. That was nearly 30 years ago and I have not looked back (much!) My projects are slower than they probably should be if I was just chasing the money, but I like doing a lot of the work myself as I have picked up a lot of practical skills and really enjoy the creative process. I have made a little money, enjoyed the projects, am apparently the envy of friends trapped in well paid London careers that they dont enjoy, and have lived in some lovely houses ! Good luck . Simon. -
Green system was sold to me as it would be "future proof" should I later decide to go for a low temperature heat source ( I currently dont). I also bought a pipe stapler which I will happily sell on at a greatly reduced price. Used once, one careful owner !
-
I feel the need, the need for screed
simon45089 replied to MortarThePoint's topic in Floor Structures
I used Express Screed, based in Ripon. They will travel all over though I was told. Kingspan upstand as I am overlaying the studwork with 50mm more kingspan and that will tie in nicely. A useful tip is that when securing the plastic that goes under your pipes, and also comes up the wall above screed level, it is possible to simply use a few spare pipe staples and poke them through the plastic and into the kingspan upstand to stop it flapping down. Holds much better than tape- my tape anyway ! Simon. -
I feel the need, the need for screed
simon45089 replied to MortarThePoint's topic in Floor Structures
I had 50mm of Ahydrite screed poured last Thursday. 120 sq metres. It was fine to walk on after 24 hours although I waited 48 as per advice of very experienced screed chap. It was a joy to see it being laid, so quick, he took longer to clean up than pour and level the screed. It is dead flat according to my level. I did all stud partitions first, fitted kingspan upstands 50mm higher than the expected finished screed level, and then attached the foam expansion upstand tapes to these as advised. Worked a treat. Simon. -
Sovereign Hey’di K11 really needed?
simon45089 replied to NWGEAR's topic in Waterproofing & Sealants
I have now converted 4 barns at the same site, as well as reformed the original farmhouse. I used K11 on all of the properties and I am a fan. None of the buildings had a damp proof course, so Heydi K11 to a metre and a half from the floor stopped any rising damp.(Good to have the guarantee for resale, and you can register yourself as an installer so you can issue the certificate if you are so inclined). I have some west facing elevations which are seriously exposed to the Northumbrian weather, and powerfully wind driven rain on occasion. One year after a storm the rain came through into the farmhouse right through the 500mm walls. (This wall had no stud wall on the internal face so I could see what was going on) There was a distinct line showing the penetration was all above the tanking and that the K11 had prevented all penetrating damp. As a result I tanked the wall full height. In the whole scheme of things its not that expensive a product and is defiantly a DIY job if you strictly follow the instructions. When I first used it 15 years ago following recommendation from a surveyor, the rep told me to do it myself as it was not difficult. He had just sold a batch to a lady who was using it on the inside of her swimming pool ! It works. -
Gabion Basket Recommendation
simon45089 replied to Triassic's topic in Landscaping, Decking & Patios
I have just had three retaining walls erected at 2.4 metres high using concrete lego blocks. 64 blocks went in in 5 hours. Its fantastic stuff. Not sure of your location but I am very close to the Cumbrian border in Northumberland. The Lego is made nearby. Its obviously not pretty, but can be disguised. A 1200 x 600 x 600 block is £75.00. I got free delivery as local. Simon. -
Box Gutter Construction Options?
simon45089 replied to ashthekid's topic in Roofing, Tiling & Slating
I recently made and installed two box gutters of 7 metres each. I made the box section in ply then lined it a full length aluminium square gutter. The aluminium has no joints, and was formed on site by a man in a van with the necessary folding machine. You can go as long as you like with no joints as the aluminium is on a roll. if it ever leaked- which is not expected, I could in theory draw it out of the ply boxing, and slide in a new one. The only limitation is the size of gutter required in width and height. The former makes them a standard size, around 140mm x 100mm , but as stated length is only limited by the roll of aluminium in the van ! -
Excellent advice, just what I am looking for. many thanks. Simon.
-
Hello, I am at the stage on my Barn Conversion project where I am about to install the underfloor heating pipework which will cover 120 Square metres of the ground floor. I have been advised to use two separate manifolds to cover the different zones required. I have chosen the best locations for the manifolds in terms of distance to their relevant zones, one being in Utility/plant room, along with the boiler and cylinder, but the second being in a dedicated kitchen cupboard. I would like advice re whether this will be suitable as I am unsure if there is likely to be any noise from the Manifold as it does its thing. I do not want a noisy manifold in the kitchen area my bedroom is above the kitchen, and living area is next to it, with an open plan aspect. I am likely heating via oil boiler so am aware there will be a necessary heat reduction of the water to get the correct temp for the UFH. Sorry for the waffle, are manifolds noisy ? Many thanks, Simon.
-
I am so pleased to have found this topic today because I too have been struggling with this issue. I am converting a barn, and have been prepping it having anticipated I will need an ASHP as no gas here. I have 175mm pir in vaulted ceilings, 150mm on the slab and 150mm on the inside face 450mm thick stone walls. I have used what seems like miles of aluminium tape on all joints and I am having underfloor heating pipework going down stairs at 150mm spacings imminently. Today I woke up and wondered if am I making my life overcomplicated by going ASHP, when a simple oil system- which I am familiar with, may well be cheaper to install, easier to find people to fix, and may not even cost much to run as I will be so well insulated I may not need to burn much oil anyway. The work I have done so far would appear to have future proofed the building, so if in 10 or 20 years time ASHP becomes mainstream, cheaper and obviously better all round, then I can just switch my oil boiler( which would fit nicely in my plant room), for an ASHP then. I may just be bottling it as I still dont really understand how an ASHP is going to cheaply warm my big open plan barn on a freezing night when its minus 10 outside in not so sunny Northumberland, but the problem continues that most of the advice given is not impartial when it comes to the merits of ASHP (not on this forum of course). Its a relief that others have the same dilemma, and that I am not just some luddite afraid of this technology ! Any advice gratefully received. Simon.